ПОЗНАВАТЕЛЬНОЕ Сила воли ведет к действию, а позитивные действия формируют позитивное отношение Как определить диапазон голоса - ваш вокал
Игровые автоматы с быстрым выводом Как цель узнает о ваших желаниях прежде, чем вы начнете действовать. Как компании прогнозируют привычки и манипулируют ими Целительная привычка Как самому избавиться от обидчивости Противоречивые взгляды на качества, присущие мужчинам Тренинг уверенности в себе Вкуснейший "Салат из свеклы с чесноком" Натюрморт и его изобразительные возможности Применение, как принимать мумие? Мумие для волос, лица, при переломах, при кровотечении и т.д. Как научиться брать на себя ответственность Зачем нужны границы в отношениях с детьми? Световозвращающие элементы на детской одежде Как победить свой возраст? Восемь уникальных способов, которые помогут достичь долголетия Как слышать голос Бога Классификация ожирения по ИМТ (ВОЗ) Глава 3. Завет мужчины с женщиной 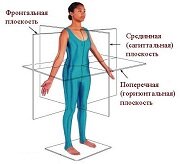
Оси и плоскости тела человека - Тело человека состоит из определенных топографических частей и участков, в которых расположены органы, мышцы, сосуды, нервы и т.д. Отёска стен и прирубка косяков - Когда на доме не достаёт окон и дверей, красивое высокое крыльцо ещё только в воображении, приходится подниматься с улицы в дом по трапу. Дифференциальные уравнения второго порядка (модель рынка с прогнозируемыми ценами) - В простых моделях рынка спрос и предложение обычно полагают зависящими только от текущей цены на товар. | Часть 1. Основы управления качеством. 5 страница 3. Вовлечение работников.Люди на всех уровнях составляют основу компании. Их полное вовлечение дает возможность использовать их способности для достижения организацией максимальной эффективности. Персонал рассматривается как самое большое богатство организации. Поэтому создаются необходимые условия для того, чтобы максимально раскрыть и использовать его творческий потенциал. Руководство организации должно стремиться к тому, чтобы цели отдельных сотрудников были максимально приближены к целям организации. Огромную роль здесь играет материальное и моральное поощрение. В TQM предполагается делегировать больше ответственности на нижние уровни управления. При этом не следует забывать, что сотрудники должны быть специально подготовлены для принятия новой ответственности. При увеличении ответственности рядовых сотрудников возрастает роль обратной связи, которая становится основной составляющей информационной системы предприятия. Естественно, такой подход не предполагает отсутствие управления, но оставляет для высших уровней управления больше возможности сосредоточиться на решении стратегических задач. Кроме этого, важную роль играют социальные и психологические факторы. Самоконтроль (должным образом подготовленный) и контроль со стороны коллег работает эффективнее, чем формальный контроль сверху. Персонал организации должен владеть методами работы в команде. Работы по постоянному улучшению преимущественно организуются и проводятся группами. При этом достигается синергический эффект, при котором совокупный результат работы команды существенно превосходит сумму результатов отдельных исполнителей. 4. Подход к системе как к процессу.Основополагающим принципом ТОМ является концентрация всех усилий по совершенствованию деятельности предприятия на конкретных процессах, и в особенности на процессах, непосредственно влияющих на качество конечной продукции фирмы. Доказано, что желаемый результат легче достичь, если соответствующими ресурсами и деятельностью управляют как процессом. Процессная модель предприятия состоит из множества бизнес-процессов, участниками которых являются структурные подразделения и должностные лица организационной структуры предприятия. 5. Взаимовыгодные отношения с поставщиками.Требования к качеству продукции поставщиков предъявляются практически такие же, что и к своей собственной. Для мониторинга поставщиков следует оперативно отслеживать качество их продукции и своевременно отказываться от услуг ненадежных (если это возможно). Целесообразно также налаживать с ними взаимовыгодные отношения, в том числе направленные на определенную регламентацию их действий. На этом этапе устанавливаются документированные процедуры, обязательные для соблюдения поставщиком на всех этапах сотрудничества. 6. Системный подход к управлению.Выявление, понимание и управление системой взаимосвязанных процессов, направленных на достижение поставленной цели, повышает результативность и эффективность организации. Это означает, что организация должна стремиться к объединению процессов создания продукции или услуг с процессами, позволяющими отследить соответствие продукции или услуг потребностям заказчика. Только при системном подходе к управлению станет возможным полное использование обратной связи с заказчиком для выработки стратегических планов и интегрированных в них планов по качеству. 7. Постоянное улучшение. В этой области организация должна не только отслеживать возникающие проблемы, но и после тщательного анализа со стороны руководства предпринимать необходимые корректирующие и предупреждающие действия для предотвращения таких проблем в дальнейшем. Цели и задачи основываются на результатах оценки степени удовлетворенности заказчика (полученной в ходе обратной связи) и на показателях деятельности самой организации. Улучшение должно сопровождаться участием руководства в этом процессе, а также обеспечением всеми ресурсами, необходимыми для реализации поставленных целей. 8. Принятие решений, основанных на фактах.Для оценки необходимо разработать систему критериев и порядок проведения такой оценки. Полученные и проанализированные результаты должны быть использованы для дальнейшего совершенствования деятельности предприятия. Система TQM предназначена для обеспечения соответствия качества продукции предприятия или проекта требованиям норм, заданий потребителей и действует на всех фазах проектного цикла. В менеджменте качества участвуют все организации, службы и подразделения предприятия. При этом выполняются следующие функции: • планирование качества продукции предприятия/проекта и его отдельных элементов; • создание команды проекта, включая подготовку кадров и организацию трудовой деятельности; • подготовка производства, т.е. обеспечение необходимой для заданного уровня качества квалификации исполнителей и их технического оснащения; • разработка системы материально-технического обеспечения; • контроль и текущая оценка достигнутого уровня качества, включая входной, операционный и приемочный контроль технологических процессов и производственных операций, а также проведение инспекционного контроля; • информационное обеспечение, включая систему сбора, обработки и передачи информации между уровнями управления; • лабораторное, метрологическое и геодезическое обеспечение технологических процессов; • правовое обеспечение менеджмента качества. 3.3 Внедрение ТQМ на российских предприятиях Еще рано говорить о том, что экономические реформы повернули российских производителей к качеству. Однако все большее их число, предчувствуя будущее, осознают эту проблему и изучают опыт зарубежных фирм. Сильное влияние на россиян оказывают контракты с зарубежными предприятиями, в которых основной упор делается на качество. Однако, прежде всего нужно выявить проблемы, которые встретятся на пути к всеобщему качеству. Главная (первая) методическая проблема,чаще всего не осознаваемая руководством российских компаний, состоит в том, что единственное ясное предложение, которое они имеют, — это стандарты ИСО семейства 9000, а данные стандарты неадекватны российской текущей ситуации. В настоящее время почти все внешние, да и некоторые отечественные потребители требуют от российских компаний сертификаты на системы качества по ИСО 9000. Это хороший толчок к началу работ по качеству. Но безоглядное внедрение стандартов на системы качества может привести к бесполезным затратам и необоснованному разочарованию в стандартах ИСО серии 9000. Суть проблемы заключается в том, что, с одной стороны, российским компаниям необходимы серьезные изменения в организационной структуре, общей корпоративной культуре, стиле и методах менеджмента, зачастую в смене номенклатуры создаваемой и производимой продукции. С другой стороны, стандарты ИСО семейства 9001 весьма консервативны. Использование указанных стандартов для целей обеспечения качества опирается на принцип: «Документируй то, что делаешь, делай то, что задокументировано». Если нарушить данный принцип, то система качества теряет свою приспособленность к аудиту (проверкам), ибо аудиторы могут фактически проверять лишь документы и соответствие реальных процедур документированным. Если же документировать существующую систему, то документированная и реальная системы совпадут, но мало кого может устроить их уровень эффективности. Более того, документирование системы качества в том виде, в котором последняя существует, приведет к стагнации уровней качества продукции и процессов на низких уровнях. Второй проблемойна пути внедрения стандартов ИСО 9000 является невыполнение в России правил Джурана: 85% — 15% и Деминга: 96% — 4%. Напомним, что это такое. Дж. Джуран утверждал, что за 85% проблем качества отвечает система менеджмента, а за остальные 15% — исполнители. Э. Деминг усилил это правило. Он подчеркивал, что 96% проблем качества — это ответственность системы, на долю исполнителей приходится лишь 4%. В последние годы своей жизни он еще более ужесточил цифры: 98% — 2%. Эти цифры возлагают основную, доминирующую ответственность за качество на систему менеджмента и ее создателей. В России ситуация почти обратная — основная доля несоответствий падает на исполнителей. Третья проблема— неадекватность культурных основ российской промышленности и сферы услуг и принципов, заложенных в стандарты ИСО семейства 9000. Главный принцип, составляющий основу стандартов ИСО 9000 это «жить по правилам, которые помогают жить лучше». В России люди ориентируются не на правила и законы, а на авторитеты и на силу власти. Культурный базис российских систем менеджмента качества — это репрессивный менеджмент, основанный на поиске виновных. Необходимо переходить от менеджмента, основанного на праве силы, к менеджменту, основанному на силе правил. Четвертая проблемароссийских компаний — пропущенные этапы развития менеджмента качества и, прежде всего статистических методов управления качеством. Мы не поняли в свое время, что статистическое управление качеством это новый подход, направленный на устранение недостатков системы Тейлора. Пятая проблема (обобщающая) – лечение без диагноза. Предприятие легкомысленно относятся к внедрению стандартов ИСО 9001. Многие руководители поручают подготовку документов по системе качества рядовым сотрудникам, при этом надеются, что в результате внедрения стандартов все болезни менеджмента предприятия пройдут сами собой. Они не проводят диагностику менеджмента, не выявляют болезни и не определяют методики лечения. Как построить систему статистического управления качеством и вписать ее в общую систему менеджмента качества? Это один из серьезнейших вопросов для российских компаний. Успех массового распространения концепции Всеобщего качества и тем более придание ему характера национальной идеи во многом определяются тем, как поведут себя лидеры российской экономики. К сожалению, сырьевые отрасли менее чувствительны к требованиям по качеству, в связи, с чем на первые позиции должны выйти крупные машиностроительные компании. Во-первых, это — крупнейшие компании России, успешно работающие в последние годы, во-вторых, они имеют армию поставщиков не менее 400—500 предприятий каждый и могут оказать на них прямое влияние в освоении стандартов ИСО 9000. Стартовые условия на большинстве российских предприятий очень сложные, им, прежде всего, необходима программа оздоровления систем менеджмента качества. Приведем семь шагов, направленных на развитие ТQМ. Первый шаг: организация процедуры измерений и анализа уровней дефектности, или уровней несоответствий в производстве. Прежде всего нужно понять стартовые условия, оценить, где находится предприятие в отношении качества продукции и процессов. Второй шаг: анализ и классификация несоответствий и их причин. Несоответствия необходимо разделить по степени важности. Рекомендуется следующая классификация несоответствий: критические, значительные, малозначительные. Причины несоответствий могут носить различный характер: технический, исполнительский, организационный и др. Причины могут быть на уровне исполнителя и рабочего места, на уровне бригады, цеха, на заводском уровне или на уровне взаимоотношений с поставщиками. Для каждого из этих уровней применяют свои методы и средства анализа. На внешнем уровне используют специальные приемы работы с поставщиками. Третий шаг: введение мотивации за снижение несоответствий. Нужно стимулировать персонал к снижению уровня несоответствий, даже если они в начальный момент составили десятые доли процентов. Однако мотивация к снижению уровней несоответствий через материальное стимулирование должна изменяться с развитием системы менеджмента в направлении TQM. Совершенно очевидно, что после того, как рабочие и ИТР исчерпали свои внутренние возможности, мотивация в виде премий за снижение уровней несоответствий теряет смысл. Их премия будет колебаться случайным образом в соответствии с вариациями, обусловленными уже системой. Здесь следует изменить тактику. Усредненную за несколько последних месяцев премию следует превратить в надбавку к зарплате. Далее нужно начать использовать другой метод вовлечения работников в процессы непрерывного улучшения качества. Необходимо объяснить и показать на примерах, что дальнейшее улучшение возможно лишь путем коллективной, групповой работы. Тем самым начинается подготовительный период создания кружков и групп качества. К этому моменту предприятие должно иметь ясную миссию, политику качества, руководящие принципы и ценности. Четвертый шаг:согласование возможностей производства с требованиями конструкторской и технологической документации. Пятый шаг:разработка централизованной программы поэтапного снижения уровня несоответствий на заводском уровне, внедрение системы статистического управления качеством — системы Шухарта. На этом этапе разрабатывается программа инженерных и технико-экономических мероприятий по снижению уровней несоответствий в масштабах предприятия. В ней устанавливаются задания производствам, цехам по проведению конкретных мероприятий. Контроль за реализацией программы осуществляется на основе календарного графика снижения уровней несоответствий. Шестой шаг:построение производственных отношений между бригадами, цехами, производствами на основе цепочки «изготовитель (поставщик) — потребитель», создание документированной системы качества, соответствующей стандартам ИСО 9001(2). Практически все производственные отношения на предприятиях можно разделить на цепочки «изготовитель — потребитель». Например, цех, который делает детали для более сложного изделия, является изготовителем (поставщиком) для сборочного цеха-потребителя. Целесообразно эти отношения формализовать, установив определенные права и обязанности сторон. Как правило, в общем случае потребитель признается слабой стороной, и его права защищаются. Одним из важнейших моментов этих отношений является приемка продукции от поставщика на основе статистического приемочного контроля. Рекомендуется начинать внедрение стандартов ИСО 9001(2) только на шестом этапе, когда проделана большая внутренняя работа по снижению уровней несоответствий, получены практические навыки в непрерывном снижении уровней несоответствий. Система обеспечения качества в этой ситуации не должна привести к стагнации уровней несоответствий, а должна стать только частью общей системы менеджмента качества, предусматривающей непрерывное улучшение. Седьмой шаг:создание системы работы с внешними поставщиками на основе стандартов на статистический приемочный контроль на базе принципа распределения приоритетов (ПРП) и внедрения систем качества, соответствующих стандартам ИСО 9001(2), QS-9000, ИСО/ТУ 16949. Стандарты, реализующие ПРП, фактически предлагают систему конкретных взаимоотношений между поставщиками и потребителями, а также процедуру управления качеством поставок со стороны потребителя. В них заложены все основы, которые позволяют потребителю последовательно добиться от поставщика нужного уровня качества. Стандарты предполагают активное сотрудничество между партнерами, учитывая при установлении объемов контроля информацию о внедрении систем качества, результатах аттестации производственных процессов, внедрении статистических методов у поставщиков. Это позволяет начать с жестких схем входного и выходного контроля, затем по мере улучшения качества уменьшать объемы входного контроля, перенося акцент на контроль процессов поставщика и оценку систем качества. В целом система работы с поставщиком включает: • выходной контроль продукции поставщиком в соответствии с требованиями потребителя; • входной контроль потребителя и обратную связь по результатам контроля; • инспекции и аудиты со стороны потребителя (аудит второй стороной продукции, процессов, систем качества); • аудит третьей стороной (сертификация) системы качества поставщика; • оценка качества поставок; • оценка (рейтинг) поставщиков, кроме того, потребитель и поставщик могут создавать совместные команды по улучшению качества поставок и решать многие вопросы, вплоть до инвестиций. 3.4.Современные методы управления качеством Метод «шесть сигм» Метод «шесть сигм» представляет собой хорошо структурированную методологию, направленную на устранение дефектов, снижение отходов и решение проблем контроля качества для различных промышленных производств, компаний, предоставляющих услуги, и других сфер бизнеса. Методология «шесть сигм» опирается на сочетание статистических методов контроля качества, различных методов анализа данных и системы постоянного повышения квалификации специалистов, так или иначе вовлеченных в процессы, организованные с учетом «шесть сигм». Основу системы качества «шесть сигма» составляет оценка отклонений фактических показателей процесса от кривой нормального распределения отклонений. Если те или иные показатели процесса находятся в определенных пределах отклонений, качество результатов процесса также остается высоким. Единицу измерения отклонений в статистике принято называть «сигмой». Заметный эффект наблюдается при отклонении не более 4,5 сигма; в этом случае показатель числа дефектов на миллион единиц продукции составляет 3,4. Но это условие выполняется для стабильных процессов. Производственные процессы не отличаются стабильностью. Изобретатели методологии пришли к выводу, что отклонения процесса, вызванные его естественной нестабильностью, дают отклонения качества на уровне 1,5 сигма. Таким образом, если целевой уровень качества составляет 4,5 сигма, то с учетом 1,5 сигма на отклонения необходимо обеспечивать уровень качества в 6 сигма. В большинстве компаний обеспечивается уровень качества 3 или 3,5 сигма. Уровень 3 сигма соответствует 93-процентному уровню качества, то есть 66800 дефектов на миллион единиц продукции. Методология «шесть сигма» была разработана в 1986 году в компании Motorola. Концепцию предложил старший инженер подразделения средств связи Билл Смит. Его побудили к этому жалобы торговых агентов на местах, сообщавших об участившихся случаях предъявления претензий по гарантийным обязательствам. Смит создал новый подход к стандартизации методов учета дефектов. В идеале производство, организованное с учетом методологии «шесть сигма», должно было выпускать продукты, практически не имеющие изъянов. Смит разработал необходимый статистический аппарат и представил его руководству компании. Идея была принята на «ура», и в Motorola развернулась работа по документированию основных процессов, их согласованию с критически важными требованиями пользователей и установке систем измерения и аналитических систем, позволявших постоянно вносить усовершенствования в процессы. В результате компания в 1988 году стала первым лауреатом премии за качество продукции Malcolm Baldridge National Quality Award. Компания за четыре года добилась экономии в 2 млрд. долл. Подобная сумма не могла не привлечь внимание отрасли, и у методологии Six Sigma начали появляться адепты, например компании General Electric и AlliedSignal (теперь Honeywell International). Сила «шесть сигма» заключена в «эмпирическом», управляемом данными подходе и в использовании количественных показателей. Цель «шесть сигма» — сокращение отклонений в ходе производственного процесса и его совершенствование путем реализации так называемого «проекта совершенствования «шесть сигма», который распадается на последовательность шагов DMAIC (define, measure, analyze, improve, control): определение, измерение, анализ, совершенствование и контроль. На первом этапе, «определения» (define), ставятся цели и рамки проекта, выявляются проблемы, которые должны быть решены для достижения определенного уровня отклонений. Цели могут различаться на разных уровнях организации — так, например, на уровне высшего руководства это может быть большая отдача от инвестиций или завоевание большей доли рынка. На уровне операций целью может быть увеличение объемов выпуска какого-либо цеха. На проектном уровне — снижение количества брака или увеличение эффективности отдельного процесса. Для выявления потенциальных возможностей для улучшений используются методы добычи данных. На втором этапе, «измерения» (measure), происходит сбор информации о текущем состоянии дел для получения данных, характеризующих базовый уровень показателей работы, и выявления участков, требующих наибольшего внимания. На этом этапе также определяются метрики, позволяющие оценить степень приближения к намеченным целям. На третьем этапе, «анализа» (analyze), выявляются основные причины проблем в обеспечении качества, после чего правильность выбора этих причин проверяется при помощи специальных инструментов анализа данных. На четвертом этапе, «совершенствования» (improve), внедряются решения, ориентированные на устранение проблем (основных причин), определенных на этапе анализа. В числе таких решений могут быть средства управления проектами и другие инструменты управления и планирования. Цель пятого этапа, «контроля» (control), — оценка и мониторинг результатов предшествующих этапов. На этом этапе улучшения подкрепляются модификацией системы стимулов и поощрений, наборов правил, процедур, систем MRP, бюджетов, инструкций персоналу и других рычагов управления. Для гарантии корректности документации можно обеспечить, например, ее соответствие спецификации ISO 9000. Как возник термин «Шесть сигм»? В статистике знаком «сигма» обозначают среднеквадратическое отклонение. Данный показатель позволяет понять, насколько производство определенной детали отклоняется от нормы. Из заданных таблиц по стандартным отклонениям можно сделать заключение о вероятности производства детали в границах определенного отклонения. «Шесть сигм» – такой уровень эффективности процесса, при котором на каждый миллион возможностей или операций приходится всего 3,4 дефекта. Враг совершенства любых процессов – их вариативность (они стремятся протекать несколько иначе, чем предусмотрено технологической схемой производства). На протекание процессов влияет все: негодный материал, заглохший станок, природный катаклизм или человеческий фактор. В идеальном случае, когда процессы протекают с минимальным разбросом, на выходе получается продукция заданного качества. К тому же такой подход позволяет сделать эту систему применимой ко всем товарам, услугам и процессам – от выпечки хлеба до системы пейджинговой связи. Для любой операции или на любом шаге процесса можно определять количество дефектов: например, отсутствие реакции на запрос заказчика, ошибка в заказе на покупку, неправильный счет и т.д. Можно также обнаруживать дефекты в цепи процессов, связанных с внутренними и внешними заказчиками. Установление этих мер в единицах дефектов на миллион событий усиливает их потенциальное влияние. «Шесть сигм» можно применять в организациях практически любого типа и размера. «Шесть сигм» – это процесс, философия, позиция, комплект инструментов и понимание высшим руководством высокого качества как вернейшего пути к рентабельности. Внедряться эта система может по-разному, в зависимости от объема и природы организации, типа ее продукции или сервиса. Работа по совершенствованию и преобразованию компании строится по плану маршрута (маршрутной карте) из пяти шагов: · идентификация ключевых процессов и потребителей; · определение потребительских запросов; · измерение текущих результатов; · расстановка приоритетов, анализ и внедрение усовершенствований; · расширение и интеграция системы «Шесть сигм». Необходимо также обеспечить, чтобы соответствующие меры измерения процесса идентифицировались заранее, а измерения отражали результаты бизнеса до и после изменений и вносили вклад в конечный результат. В ходе внедрения устанавливаются цели (задачи), ориентированные на величины улучшений на порядок (в 10 раз). Основное внимание при внедрении системы «Шесть сигм» должно уделяться совершенствованию процессов, а не работников, т.к. число проблем, зависящих непосредственно от персонала, составляет менее 20%. Это доказывается статистически. Исследования показали, что в большинстве технологических, производственных и многих других процессов возможности для брака и разного рода ошибок появляются на уровне 4 сигм. Производство товаров, процесс оформления бухгалтерских платежных документов, доставка и обработка багажа на авиалиниях, выписка медицинских рецептов, письменные заказы, заполнение ордеров на печатную продукцию (подписка), трансферты, ресторанные счета, покупки разного рода – все эти процессы имеют уровень 4 сигм по количеству моментов, допускающих ошибку или брак. То, что этот список включает в себя и процесс заполнения медицинских рецептов, говорит о том, что интеллект или уровень образованности никоим образом не влияет на количество брака. Скорее всего, брак – это следствие процесса. Следовательно, задача заключается именно в сокращении вариативности процесса. Следует также заметить, что каждая организация имеет специфическую культуру и способы ведения бизнеса. Культура организации – результат устоявшихся представлений ее работников. Если компания основана давно, может оказаться тяжело модифицировать ее культуру, особенно если сотрудники не привыкли к изменениям. В таком случае необходимо сосредоточиться на соответствии между культурой и качеством и, исходя из результатов такого анализа, определить, как лучше внедрить систему управления качеством в данной организации. Конечный результат этого этапа должен быть представлен в форме рекомендаций, пошаговой инструкции и долгосрочных планов по внедрению. Кроме того, учитывая, что нескольких месяцев тренинга недостаточно, чтобы заложить в такой организации крепкий фундамент знаний и навыков, нужно направить усилия на создание постоянного процесса обучения. Система Шинго Система Шинго разрабатывалась параллельно и во многом в противовес контролю качества, основанному на статистических методах. Система Шинго, или, если быть точнее, — данная философия производственного менеджмента получила свое название в честь одного из разработчиков известной системы "точно в срок" фирмы Toyota Шигео Шинго (Shigeo Shingo). Этот ученый чрезвычайно популярен в своей родной стране, где он даже награжден титулом "Мистер Улучшение", но в последние годы его идеи широко распространились и на Западе. Больше всего внимания уделяется двум основным аспектам системы Шинго. Первый из них заключается в том, как можно добиться значительного сокращения времени наладки оборудования с помощью так называемых процедур одноминутной замены штампа (Single Minute Exchange of Die — SMED). Второй аспект состоит в контроле источника (или поставщика) и использовании системы poka-yoke для достижения уровня "нуль-дефектов". По мнению г-на Шинго, методы статистического контроля качества не предупреждают брака. Конечно, с их помощью можно получить информацию относительно степени вероятности появления очередного дефекта, однако это будет лишь констатацией факта. Для того чтобы предотвратить выпуск брака в конце технологического процесса, следует внедрять элементы управления в сам процесс. Центральным элементом метода Шинго является разграничение ошибок и дефектов. Брак появляется в результате ошибок людей. Конечно, ошибки неизбежны, однако появление дефектов можно предотвратить, если обратная реакция (т.е. действие, направленное на исправление ошибки) осуществляется сразу после того, как совершена ошибка. Для такой обратной связи и ответных мер необходим контроль 100% выпускаемой продукции. Такой контроль может быть трех типов: последовательная проверка, самопроверка и контроль источника. Контроль с помощью последовательной проверки выполняется следующим рабочим в технологическом процессе либо независимым беспристрастным экспертом, например лучшим рабочим бригады. Информация о дефектах немедленно передается рабочему, по вине которого появился брак, который и исправляет свою ошибку. Самопроверка проводится каждым рабочим и применима для контроля любых показателей качества за исключением тех, для которых требуется сенсорная оценка (например, наличие или глубина царапин или правильность сочетания оттенков краски). В таких случаях необходима последовательная проверка. Контроль источника также выполняется одним рабочим, только вместо обнаружения дефектов в продукции он проверяет компоненты на наличие в них дефектов, которые впоследствии могут привести к выпуску бракованной продукции. Это предотвращает появление дефектов, а, следовательно, и устраняет необходимость доработок и переделок. Все эти три типа контроля основаны на применении особых процедур или оборудования для обеспечения надежности, которые относят к методам poka-yoke. Понятие poka-yoke включает такие инструменты, как контрольные списки и специальный инструментарий, который препятствует совершению в начале процесса рабочим ошибок, впоследствии приводящих к браку, или быстро информирует рабочего о нарушении норм технологического процесса, в результате чего у него остается время исправить положение. Существует большое разнообразие методов poka-yoka, от укладывания комплектующих в специальные ящики с ячейками (что позволяет обеспечить использование правильного количества деталей при сборке) до сложнейших детекторных приборов и электронной сигнальной аппаратуры. На рис. 3.1 приведен пример использования приема poka-yoka, взятый из книги Шинго. Шинго резко отрицательно относится к чрезмерному увлечению производственных компаний контрольными картами, указывая на то, что они просто отображают текущую ситуацию. Когда менеджер по контролю качества одного химического завода с гордостью заявил в беседе с ученым, что при штате в 150 человек они используют 200 контрольных графиков, г-н Шинго спросил его, не построили ли они контрольного графика для контроля контрольных графиков? |