Ремонт маслоизготовителя емккостью 2000 л марки РЗ-ОБЭ 1. Отсоединить трубопроводы. Снять ограждения и крышки. Зафиксировать и закрепить положение бочки. Снять клиновые ремни и шкивы. Демонтировать электродвигатель. 2. Разобрать коробку передач на узлы и детали, промыть их, определить износ и комплектовать для проведения ремонта. 3. Снять с корпуса бочки 2 клапана, защелку и рукоятку. Детали промыть и определить износ. 4. Изготовить для замены 4 пружины, 3 уплотнительных кольца, 2 винта, 2 втулки, 2 эксцентрика, 2 прокладки и 12 шпилек. 5. Перебрать 2 клапана с заменой 2 уплотнительных колец, барашка винта, прокладки и штифта. 6. Определить места износа рукоятки, восстановить их сваркой и зачистить сварные швы. 7. Калибровать резьбовые отверстия в крышке и корпусе коробк передач. Изготовить из картона З прокладки. 8. Изготовить для общей сборки коробки передач: палец, 9 прокладок 2 втулки, 4 крышки, 2 оси, 2 специальных болта, З штифта, 40 винтов и 10 шпонок. Шпонки подогнать по мест посадки. 9. Восстановить сваркой места износа З рычагов, З вилок и зачистить сварные швы. 10. Перебрать механизм сцепления с заменой крепежа, 8 шарикоподшипников З80200, 8 специальных шпилек, 8 пальцев и 12 пружин. 11. Подготовить к сборке: комплект звездочек, комплект шарикоподшипников и роликоподшипников, манжеты, крепеж и клиновые ремни. 12. Отремонтировать тележку: разобрать, промыть и определить износ деталей; изготовить б прокладок, восстановить сваркой места износа цапфы; заменить резину у колес и собрать тележку. 13. Из отремонтированных деталей и узлов, комплектующих изделий собрать коробку передач и смонтировать ее на станине. Установить электродвигатель, шкивы и одеть ремни. Закрепит все узлы на станине. Освободить бочку. Установить ограждения и смазать подшипники. Опробовать работу маслоизготовителя на холостом ходу и под нагрузкой с устранение выявленных дефектов. Билет Схема производства казеина на линии Я9-ОКЛ. Комплектность линии. Конструкция коагулятора непрерывного действия, уравнительного бачка и установки непрерывной промывки. Виды износа оборудования. Методы определения износа. Коагуляторы Коагуляторы могут быть емкостные, змеевиковые и коагуляторы ВНИМИ. Емкостные к о а г у л я т о р — емкость цилиндрической формы с коническим днищем, в который поступает молоко, подквашенное до кислотности 474°Т и смешанное с кислой сывороткой (1 80—220°Т). Образовавшийся в коагуляторе сгусток направляется в аппарат для самопрессования, где происходит его обезвоживание. 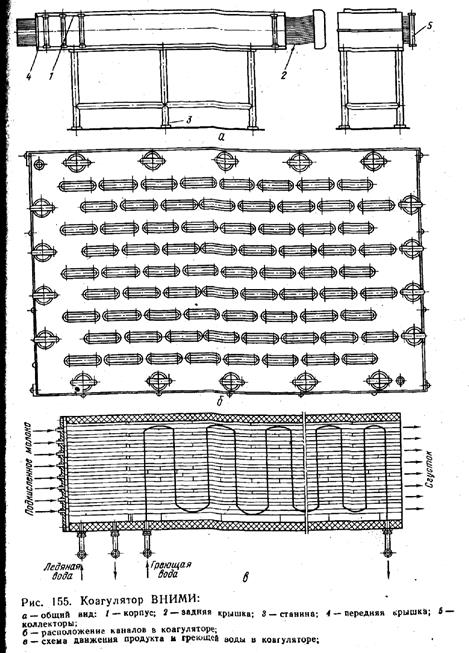 Змеевиковый коагулятор представляет собой трубу из нержавеющей стали, свитую в эмеевик. Сгусток образуется в потоке. Коагулятор В НИМИ (рис. 155, а)—это многотрубный одноходовой теплообменньтй аппарат, разделенный по длине каналов на два отделения: одно для гидродинамической стабилизации, другое для нагревания молока. Коагулятор включает в себя корпус 1, установленный на станине З, две трубные крышки — переднюю 4 и заднюю 2, коллекторы 5. Корпус коагулятора (рис. 155, 6) состоит из девяти секций, расположенных одна над другой. Каждая секция имеет восемь плоских труб из нержавеющей стали. Секции коагулятора сварные и отделены одна от другой герметичными перегородками. В каждой секции расположены патрубки для входа и выхода воды, соединенные коллекторами. По длине секций установлены перегородки, которые исключают прогиб труб и позволяют увеличить скорость движения греющей воды в межтрубном пространстве (рис. 155, в). Молоко с внесенными в него дестабилизаторами (Молочная кислота, сычужный фермент, хлористый кальций) по мере продвижения по трубам коагулятора нагревается горячей водой. В результате нагревания казеин молока коагулирует, образуя сгусток, который поступает на обезвоживание. Обезвоживание сгустка, полученного в коагуляторе, осуществляется в барабанном обезвоживателе. В качестве фильтровального материала в нем использована лавсановая ткань. Она натягивается на два обода, укрепленных на валу. Барабан приводится во вращение от привода со сменными шкивами. Сгусток перемещается от одного конца барабана к другому вследствие некоторого наклона барабана. Сыворотка собирается в поддоне, установленном под барабаном. Методы определения износа Основными методами определения характера и степени износа, а также дефектов деталей являются следующие: осмотр невооруженным глазом и с помощью лупы применяют для обнаружения поломок, трещин, выкрашивания, погнутости, задиров, течи; акустические методы: обстукивание и прослушивание без приборов; прослушивание с применением стетоскопа. Этими методами определяют наличие трещин и других скрытых дефектов; тепловой метод — определение температуры подшипника рукой (рука выдерживает температуру 60.. .70°С) или с помощью термоиндикаторных красок, которые изменяют свое первоначальное окрашивание; метод измерения — для определения отклонений размеров деталей от заданных в рабочем чертеже, зазоров между сопрягаемьими деталями, изменения формы, наличия изгибов и погнутостей; дефектоскопия (ультразвуковая, электромагнитная, рентгеноскопия), проводимая с помощью специальных приборов, — для выявления скрытых дефектов: трещин, раковин, неплотностей, посторонних включений в сварных швах и литых деталях; гидравлические и пневматические испытания — для определения прочности и плотности. При определении износа или дефекта сначала используют более простые (осмотр, измерение и т.д.), а затем более сложные методы (дефектоскопия, испытания и др.). При этом необходимо учитывать возможности ремонтно-механических мастерских предприятия. Износы деталей машин определяют микрометрированием, профилографированием, взвешиванием, выявлением количества железа в масле ванны, радиоактивными изотопами, по отпечаткам и вырезанньм лункам. Различают следующие виды физического износа: механический, химический (коррозионный) и тепловой, действие которых на снижение надежности оборудования может проявляться как отдельно (обособленно), так и в сочетании. Механический износ Механический износ выражается в поломке, поверхностном изнашивании (истирании) под действием сил трения и в результате эрозионного износа, появления усталостных трещин и снижения механических свойств деталей. Поломка детали или появление в ней трещин является результатом превышения допустимых нагрузок или низкого качества материала оборудования. Меры против поломок: предотвращение сверхдопустимых нагрузок при эксплуатации, профилактические осмотры и контроль с целью выявления трещин в начальной стадии. Поверхностный износ проявляется в истирании, смятии, задирании и выкрашивании поверхности под действием сил трения и деформаций, возникающих при локальных высоких удельных давлениях, а также в попадании в сопряженные детали абразивных материалов (песок, пыль, окалина, стружка). Одной из причин поверхностного износа может являться молекулярно-механических износ, возникающий при большом удельном давлении в условиях глубокого вакуума при недостаточной смазке, когда поверхности сближаются так плотно, что начинают действовать молекулярные силы, сваривающие трущиеся поверхности. Меры, принимаемые против поверхностного износа: смазка трущихся пар, чистота обработки поверхностей, правильный выбор антифрикционных материалов (антифрикционньие чугуньи, бронзы, баббиты, полимерные материалы — фторопласт, полиэтилен, винипласт и др.), конструктивные меры (повышение твердо- сти одного из элементов трущейся пары, нанесение на один из элементов тонкого слоя материала с малым коэффициентом тре- ния, применение гидростатических подшипников и т.д.). Меры, принимаемые против выкрашивания поверхностей: приработка узла, исключение превышения нагрузок. Усталостное выкрашивание усиливается при обильной смазке, так как она проникает в микроскопические поры и щели материала, нагревается и разрушает его поверхность. Эрозионный износ происходит под действием абразивных материалов при их движении и проявляется в абразивном истирании и стачивании металла под действием удара и трения твердых частиц. Наиболее характерно эрозионный износ проявляется в аппаратах для перемешивания сыпучих материалов, в шнеках для их транспортировки, в системах пневмотранспорта, сушилках. Меры, принимаемые против эрозии: протекторная защита установка легко сменяемых деталей); уменьшение крутых изгибов, резких поворотов в пневмотранспорте; нанесение покрытий; упрочнение поверхности; защита основного материала путем специальных устройств в системах пневмотранспорта. Усталостный износ возникает, когда деталь подвергается переменным нагрузкам в течение длительного времени (пружины, пальцы и др.). Усталостные напряжения носят местный характер, и предотвратить их можно исключением резких изменений формы детали, выбором правильного конструктивно- го ее оформления, исключением нарушения сплошности материала, профилактическим осмотром и контролем. |