Технологічні основи виробництва паркетних щитів Технологічний процес виготовлення щитового паркету має багато спільного з виготовленням паркетної дошки. Він займає як би проміжкові положення між технологією паркетної дошки, оскільки може будуватися на використанні некондиційних заготовок паркетної дошки і технологією художнього паркету, як більш складного за конструкцією. Паркетні щити виготовляють на таких технологічних дільницях: виготовлення планок лицьового покриття із твердих листяних та цінних  
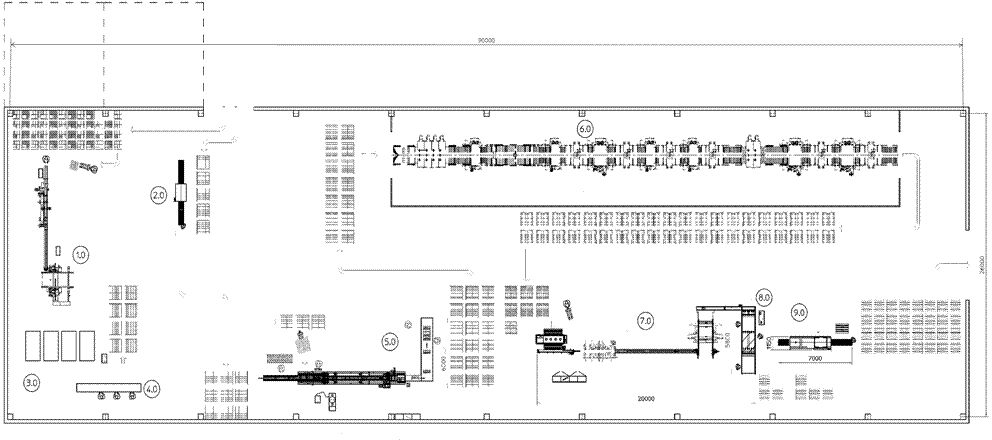 Рис.5.19. Технологічна схема виготовлення двошарової паркетної дошки на обладнанні фірми A. Costa : 1 – лінія МОД обрізних дощок; 2 – верстат форматного розкрою матеріалу для нижнього шару; 3 – верстат поздовжнього розкрою дощок на заготовки ламелі; 4 – робоче місце сортування ламелі; 5 – лінія склеювання односмугових паркетних дощок; 6 – лінія опорядження; 7 – лінія профілювання; 8 – контроль якості, формування пакетів; 9 – обгортання пакету плівкою. порід деревини; виготовлення планок (рейок) основи з хвойних порід деревини; складання та склеювання паркетних щитів; механічного оброблення щитів; нанесення захисно-декоративних покриттів. Виготовлення планок лицьового покриття для щитового паркету практично не відрізняється від описаного раніше процесу для паркетної дошки. Для отримання планок (рейок) основи для паркетних щитів типу ПЩ4 (середній і нижній шари наклеюють у взаємно перпендикулярному напрямках) використовують операції аналогічні, як для паркетної дошки. Середній і нижній шари формуються з планок, що випиляні з обрізних сухих пиломатеріалів на прирізному верстаті та оброблені за довжиною на оптимізаторі (торцювальному верстаті) з метою вирізання вад та формування довжини. Для щитів типу ПЩ1 рейки проходять операцію фрезерування шипів і провушин для рамкової основи або пазів для складання основи на нескрізний шип. Особливістю цих конструкцій щитів основи є необхідність вторинного механічного оброблення для зняття звисів після складання рамок. Операцію пресувавання і склеювання щитового паркету можна виконувати як на пресах і лініях для прискореного склеювання, так і на простих однопролітних пресах для холодного склеювання. Варто зазначити, що операції транспортування і подачі пакетів у прес істотно спрощуються, якщо щит основи є досить жорсткою конструкцією. Цього можна досягнути внаслідок попереднього склеювання щита основи, використання рамкової обв’язки, виготовлення основи з використанням лущеного шпону тощо. Жорстка конструкція щита основи дає змогу також якісно виконувати операцію нанесення клею для з’єднання з ламелями на клеєних вальцях і отримати паркетні щити з високими фізико-механічними властивостями. Жорсткість конструкції щита може бути досягнута внаслідок попереднього склеювання планок лицьового покриття за поздовжніми крайками, за аналогією виготовлення верхнього шару паркетної дошки. Технологічну витримку щитового паркету після склеювання виконують на підстопних місцях і секціях рольгангів. Остаточне оброблення щитового паркету передбачає шліфування-калібрування лицьового та нижнього шарів, обрізування за периметром, фрезерування паза і гребня. Після завершення механічного оброблення і здійснення контролю якості передбачається етап опорядження, за аналогією опорядження паркетних дощок. Розглянемо технологію виробництва паркетних щитів (ПЩ1) для умов базового підприємства. Основною особливістю технологічного процесу, схема якого наведена на рис.5.20, є необмежені розміри паркетних щитів. Планки лицьового покриття товщиною до 6 мм виготовляються шести типорозмірів за довжиною в межах від 90 до 250мм і більше 20 розмірів за шириною – від 19 до 75мм. Ширина планок визначається в залежності від їх довжини і кількості в квадраті. Така технологічна схема дозволяє зменшити відходи і збільшити корисний вихід деревини. Рейкова основа виготовляється у вигляді рамкової обв’язки з кутовими з'єднаннями на відкритий нарізний одинарний шип і брусками заповнення, закріплених у пазах брусків обв’язки на прямий нескрізний шип Технологічний процес виготовлення лицьових планок включає наступні операції: чотиристороннє стругання (2) з наступним діленням заготовки за товщиною (3); сортування за орієнтацією річних шарів і сортування за якістю (4); повторне стругання сортованих заготовок (7); торцювання на кратні за довжиною відрізки (5) і штабелювання (6); вирізка дефектних ділянок (8); торцювання в розмір (9). Бруски рамкової обв’язки і рейки заповнення виготовляються в наступній послідовності: заготовки довжиною до 3500мм і товщиною 32 мм торцюються за довжиною (12), розкроюються на необхідну ширину (13); стругають з чотирьох сторін з вибирання паза для обв’язки (15); заключним є торцюванням (16) за довжиною та вибирання паза (17) з формуванням гребня (22). Процес складання та склеювання щитів виконується з наступних операцій: попередньо складена рейкова основа вкладається на стіл, на якому набирається шар (килим) лицьового покриття, зверху накладається піддон; щит з піддоном кантується на 180° та знімається основа; наноситься клей на лицьове покриття і основу, які знову вкладаються в піддон, кантують на 180°, покриття розрівнюється і зібраний щит вкладається в прес. Операція пресування та склеювання щитового паркету може виконуватися в персах та лініях з прискореним склеюванням і простих одно чи багато проміжних пресах для холодного склеювання. Для запобігання і недопущення зсуву заготовок у сформованих пакетах часто використовується піддони, та фіксація шарів ламелі виконується з приклеюванням паперу. Технологічна витримка щитового паркету після склеювання виконується на підстопних місцях і настільних рольгангах. Заключне оброблення щитового паркет, в більшості випадках, передбачається стругання для вирівнювання верхнього шару, обрізання за периметром, фрезерування паза і гребня, шліфування зовнішньої пласті щита. Використання сучасних калібрувально-шліфувальних верстатів дозволяє замінити операцію стругання верхнього шару та підготувати його до опорядження. По завершені механічного оброблення та контролю якості окремі щити піддаються ремонтним роботам: заміна планок лицьового покриття, ліквідація тріщин, сколів, шпаклювання зазорів (люзів).  Рис. 5.20. Технологічна схема дільниці виготовлення лицьових планок, брусків рамкової обв’язки та рейок заповнення: 1-штабель заготовок для лицьових планок; 2-чотирибічне стругання; 3-поздовжній розкрій на дві планки; 4-сортування за породами і бракування за якістю; 5-торцювання за довжиною; 6- штабелювання; 7-вторинне стругання бракованих брусків; 8-вирізка дефектних місць; 9-торцювання за довжиною на більш короткі планки; 10-штабелювання; 11-штабель для брусків рамної обв’язки; 12-торцювання заготовок на потрібний розмір; 13-поздовжній розкрій за довжиною; 14-чотирибічне стругання; 15-вибір поздовжнього пазу; 16-чистове торцювання за довжиною.17- профілювання шипа і паза; 18-штабелювання; 19-штабель для брусків заповнення; 20-калібрування за товщиною; 21-торцювання за довжиною; 22-профілювання гребеня; 23-штабелювання. Сучасні проектні розробки передбачають організацію технологічного виготовлення щитового паркету, аналогічно як, і паркетної дошки, з використанням дільниць опорядження. Такі дільниці можуть включати опоряджувальні лінії з нанесенням захисно-декоративних покриттів вальцями або методом наливу. Характерним для опоряджувальних ліній є наявність поряд з обладнанням для нанесення лаку, щітково-шліфувальних верстатів, спеціальних методів для прискорення сушіння та затвердіння покрить за рахунок конвективного сушіння, інфрачервоного і ультрафіолетового опромінення, термоконтактного обігріву обертовими вальцями. Готовий щитовий паркет підлягає контролю якості, сортування, пакування і транспортування до складу готової продукції. Нижче наведені, як приклад структурна та технологічні схеми виготовлення паркетного щита на прикладі одного із передових підприємств західного регіону. Паркетні щити випускають розмірами 400х400 і 800х800 мм. Товщина паркетних щитів 30мм, притому товщина паркетних планок 6 мм, а основи 24 мм. Технологічний процес виготовлення паркетних щитів включає такі потоки (рис. 5.21) виготовлення рамкової основи, виготовлення паркетних планок, складання і склеювання щитів, оброблення паркетних щитів. Планування технологічного обладнання цеху з виробництва паркетних щитів наведено на рис. 5.22. Штабелі висушених заготовок і паркетних планок траверзним візком подають на відповідний потік для переробки. Деталі основи виготовляють на двох потоках. Заготовки основи роликовим конвеєром, подаються до торцювального верстату для формування довжини. Отримані відрізки передаються до рейсмусового верстата для калібрування рейок заповнення за товщиною. Стрічковий конвеєр передає калібровані рейки до паркетного кінцевирівнювача (7) для формування шипів на торцях. Готові рейки заповнення подають на дільницю складання основи щита. Бруски рамки обв’язки основи виготовляються на сусідньому потоці. Заготовки конвеєром подають до торцювального верстату для формування довжини. Отримані відрізки передаються до паркетно-стругального верстата (11), де їх калібрують за товщиною та формують паз на поздовжній крайці. Оброблені бруски обв’язки потоком подаються до двостороннього шипорізного верстата для формування на торцях шипів та провушин.  Рис. 5.21. Структурна схема технологічного процесу виготовлення щитового паркету: 1-торцювання рейки заповнення: 2-калібрування рейки заповнення; 3-чистове торцювання рейки заповнення із фрезерууванням шипа; 4-торцювання брусків обв’язки; 5-калібрування брусків обв’язки з одночасним фрезеруванням шипа; 6-чистове торцювання бруска обвя’зки з фрезеруваням шипа; 7-складання щита основи; 8-місце технологічної витримки; 9-калібрування щита за товщиною; 10- чотиристороннє стругання; 11-ділення заготовок на планки по пласті; 12- чистове торцювання планки лицьового покриття із трьох сторін; 13- торцювання фризи; 14-стругання фризи з трьох сторін; 15-чистове торцювання; 16-ділення заготовок на планки «по крайці»; 17-укладання планок лицьового покриття на піддони; 18-нанесення клею на основу щита; 19-укладання щита онови на планки покриття; 20-склеювання щита в гідравлічному пресі; 21-місце технологічної витримки; 22-зачищення лицьового покриття; 23-обрізування щита із чотирьох сторін з прорізуванням паза і компенсаційним прорізуванням; 24-шліфування лицьового покриття; 25-шліфування лицьового покриття (виправлення дефектів). Рис.5.23. Технологічна схема розміщення обладнання цеху з виготовлення паркетних щитів: 1-траверзний візок; 2,8-столи-роликові; 3-торцювальний верстат ЦКБ-40; 4,10-столи; 5-рейсмусовий верстат СР6-7; 6-стрічковий конвеєр; 7-паркетний кінцевирівнювач ПАРК-8; 9- торцювальний верстат ЦПА-40; 11,18,25-паркетно-стругальний верстат ПАРК-7; 12,26-лотки; 13-шипорізний верстат ШД; 14-гідравлічні вайми; 15-рейсмусовий верстат С2Р12-2; 16,22-столи; 17.-живильник; 19-круглопилкова приставка; 20-лоток;21- торцювальний верстат барабанного типу; 23-барабанний верстат торцювальний; 24- стрічковий конвеєр; 27-паркетний кінцевирівнювач; 28-конвеєр. 29- модернізований багатопилковий верстат ЦДК-5; 30-торцювальний верстат; 31-клеєві вальці КВ-9; 32-лінія формування і складання щитового паркету; 33-надпідлоговий траверзний візок; 34,36,38- надпідлогові роликові конвеєри; 35-рейсмусовий верстат; 37- форматний кінцевирівнювач ЦФ-2; 39-шліфувальний верстат ШлПС-2; 40-шліфувальний верстат ШлПС-2; 41,42-робочі місця для ремонту паркетних щитів. Основу складають в гідравлічній ваймі (14). Перед складанням на шипи брусків обв’язки і рейок заповнення наносять клей. Отримані щити основи викладаються на столи для технологічної витримки, для полімеризації клею, а потім калібрують з двох сторін на рейсмусовому верстаті. Паркетні планки теж виготовляються на двох потоках: на першому переробляють вузькі заготовки, на другому широкі. Штабелі вузьких заготовок шириною, що рівна ширині паркетних планок з припусками для механічної обробки, розбирається та викладається на стіл. Верстатник подає їх в магазин паркетно-стругального верстата (18), де заготовки обробляються в розмір за перерізом із допомогою пильного вузла розпилюються за товщиною. Отримані рейки сортують і потоком подають в магазин трьохпильного торцювального верстата (21). Отримані паркетні планки сортують, викладають в пакети і подають до лінії складання та склеювання паркетних щитів (32). На наступному потоці виготовляють паркетні планки із заготовок великої ширини, товщина яких рівна ширині паркетних планок з припусками на механічну обробку. Здають їх в магазин торцювального верстата з роторним механізмом подачі та вертикального розміщення. При обертання ротора від нижньої заготовки віднімається брусок. Бруски стрічковим конвеєром подаються до паркетно-стругального верстата (25) для оброблення пласті і однієї крайки. Оброблені бруски потоком поступають в магазин паркетного кінцевирівнювача (27) для замикаючого торцювання з двох сторін в розмір за довжиною паркетної планки. При виході із кінцевирівнювача бруски конвеєром подаються в магазин багатопилкового верстата (29) і розпилюються на паркетні планки методом ділення "по крайці". Отримані паркетні планки сортують, викладають в пакети і передають до лінії складання та склеювання паркетних щитів. Браковані паркетні планки переробляються на торцювальному верстаті. Складання паркетного щита зводиться до набирання лицьового покриття із паркетних планок і викладання на нього щита основи. Лицьове покриття збирають вручну на піддонах, що переміщаються по конвеєру завдяки біляпресової механізації. Піддони із набраним у виді малюнком лицьовим покриттям подають до місця викладання щита основи. Щит основи пропускають через клеєві вальці і вкладають на лицеве покриття, що набране в піддоні. Піддони зі щитами на завантажувальній етажерці подаються в прес. По завершені циклу пресування щитів піддони вивантажуються на розвантажувальну етажерку, а далі поштучно на конвеєр, з якого паркетні щити знімаються з піддонів і викладаються в пакети на траверзний візок (33). А з його допомогою пакети передаються на підлогові роликові конвеєри для технологічної витримки (34). Дані щити калібрують за товщиною зі сторони лицьової поверхні на рейсмусовому верстаті. Оброблені щити сортують, вкладають на підлоговий роликовий конвеєр, передають до форматного кінцевирівнювача, де обрізають щит за периметром з одночасним вибором паза. Щити вкладають в стопи і підлоговим роликовим конвеєром подають до шліфувального верстата для шліфування лицьової сторони. Якісні щити пакуються і відправляються на склад. Для ремонту дефектних паркетних щитів в цеху передбачені робочі місця. Сучасні та нові конструкції паркетних щитів розроблені зарубіжними виробниками. Заслуговують уваги перспективні технології та обладнання німецьких, італійських, австрійських та інших фірм. Австрійська фірма "Латнер" розробила конструкцію двошарового паркетного щита. Верхній шар складається із паралельно розміщених планок довжиною 280 мм, товщиною 5-7 мм, шириною 22 мм. Планки основи вкладені із проміжками. Паркетні планки розміщені перпендикулярно до планок основи. Розміри щитів 280х280 мм, товщина 15 або 22мм. На крайках щита сформовані паз і гребінь для з'єднання між собою при вкладанні. Рис. 5.23. Планування обладнання цеху з виробництва паркетних щитів Фірми Латнер: 1-штабеля заготовок для основи щита; 2-штабеля заготовок для паркетних планок; 3-верстат торцювальний; 4-верстат чотирибічний поздовжньо-фрезерний; 5-верстат багатопилковий; 6-контейнери з рейками основи; 7-контейнери з паркетними планками. 8-конвеєр сортування паркетних планок; 9-установки для укладання паркетних планок в касети; 10-установка для складання квадратів з паркетних планок; 11-верстат для нанесення клею; 12-автомат для складання щитів; 13-прес; 14-траверзний візок; 15-прес високого тиску; 16- проміжкове зберігання щитів після склеювання; 17-верстат калібрувально-шліфувальний; 18-верстат шліфувальний; 19-верстат для обробки щитів за периметром; 20-ілянка для контролю якості щитів; 21-проміжкове зберігання щитів; 22-шліфувальний верстат; 23- щітковий верстат; 24-лаконаливний верстат; 25-камера відсмоктування парів розчинника; 26-сушильна камера; 27-камера охолодження; 28-конвеєр; 29-столи готових щитів; 30-пакувальна машина; 31-столи упакованих щитів; 32-склад готової продукції. Технологія виготовлення паркетних щитів "Лакет" повної заводської готовності передбачає виконання наступних операцій: виготовлення лицьових паркетних планок і планок основи; складання та склеювання щитів у піддонах; шліфування лицьової сторони і оброблення щитів за периметром, опорядження , контроль якості, пакування. Планування обладнання цеху з виробництва паркетних щитів "Лакет" наведено на рис. 5.23. Паркетна планка та планки основи виготовляються на однотипних напівавтоматичних лініях. Висушені заготовки подають на багатопилкові торцювальні верстати з роторним механізмом подачі для формування довжини планки. Отримані бруски конвеєром подаються до поздовжньо-стругальних верстатів для розкрою на планки. Отримані планки сортуються, вкладаються в конвеєри, а планки верхнього шару на установці вкладаються в палети. На складальній установці із паркетних планок набирають лицевий шар у вигляді щитів квадратної форми. Сформовані стопи із щитів лицьованого шару роликовим конвеєром подаються на дільницю складання щитів. Попередньо наноситься клей на нижню сторону щитів. На автоматичній установці для складання паркетних щитів лицьовий шар складається нас піддони і переміщається на позицію викладання планок основ, які автоматично подаються із магазинних пристроїв. Пакети сформованих щитів ущільнюються в пресі і подаються візками у прес високого тиску. Після пресування візки із пакетами щитів викочують із преса та перекладають на підстопні місця для витримки і зберігання. Після витримки склеєні щити калібрують, шліфують лицьову сторону та обробляють за периметром з формуванням на крайках пазів і гребенів. Оброблені щити перевіряють за якістю, викладають в стопи та транспортують на проміжкове зберігання перед опорядженням. |