ПОЗНАВАТЕЛЬНОЕ Сила воли ведет к действию, а позитивные действия формируют позитивное отношение Как определить диапазон голоса - ваш вокал
Игровые автоматы с быстрым выводом Как цель узнает о ваших желаниях прежде, чем вы начнете действовать. Как компании прогнозируют привычки и манипулируют ими Целительная привычка Как самому избавиться от обидчивости Противоречивые взгляды на качества, присущие мужчинам Тренинг уверенности в себе Вкуснейший "Салат из свеклы с чесноком" Натюрморт и его изобразительные возможности Применение, как принимать мумие? Мумие для волос, лица, при переломах, при кровотечении и т.д. Как научиться брать на себя ответственность Зачем нужны границы в отношениях с детьми? Световозвращающие элементы на детской одежде Как победить свой возраст? Восемь уникальных способов, которые помогут достичь долголетия Как слышать голос Бога Классификация ожирения по ИМТ (ВОЗ) Глава 3. Завет мужчины с женщиной 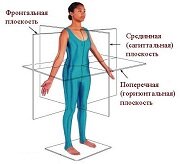
Оси и плоскости тела человека - Тело человека состоит из определенных топографических частей и участков, в которых расположены органы, мышцы, сосуды, нервы и т.д. Отёска стен и прирубка косяков - Когда на доме не достаёт окон и дверей, красивое высокое крыльцо ещё только в воображении, приходится подниматься с улицы в дом по трапу. Дифференциальные уравнения второго порядка (модель рынка с прогнозируемыми ценами) - В простых моделях рынка спрос и предложение обычно полагают зависящими только от текущей цены на товар. | Усадка и коробление изделий Практически все пластмассы при переработке проявляют достаточно высокую усадку. При этом она не всегда стабильна. Усадка и коробление, а соответственно и точность размеров пластиковых изделий (особенно важно при сборке пластмасс) зависят от ряда факторов. 1. Факторы, зависящие от материала: - тип материала – аморфные или частично кристаллические термопласты; - количество и состав наполнителей, в том числе армирующих волокон и т.д.; - степень абсорбции влаги. 2. Факторы, зависящие от конфигурации изделия: - номинальная толщина стенок; - разнотолщинность стенок; - габаритные размеры изделия; - конструктивные особенности элементов изделия, ограничивающие (затрудняющие) усадку; - технологические уклоны и конструктивные углы наклона. 3. Факторы, зависящие от конструктивной особенности литьевой формы: - расположение мест впуска; - тип и размеры впускных литников; - тип литниковых систем; - конфигурация и расположение системы охлаждения формы; - допуски на изготовление деталей литьевой формы; - тип систем выталкивания изделия; - упругая деформация нагруженных деталей литьевой формы. 4. Факторы, зависящие от технологического процесса: - температура расплава и равномерность её распределения; - температура формы и равномерность её распределения; - давление заполнения, подпитки, выдержки; - время заполнения, подпитки, выдержки; - температура изделия при выталкивании; - усилие смыкания и размыкания формы; Влияние толщины и разнотолщинности. Изделия с утолщёнными областями труднее охладить и сделать достаточно плотными. Эти области охлаждаются большее время и требуют дополнительного уплотнения. Когда изделия имеют как утолщённые, так и тонкие области, то места впуска предпочтительнее располагать в толстостенных областях, поскольку это позволяет уплотнять массу в них даже тогда, когда в тонкостенных уже произошло затвердевание. В переходных участках изделий между областями с различной толщиной возникает концентрация внутренних напряжений как следствие различно протекающих во времени процессов охлаждения и уплотнения. Внутренние напряжения могут приводить к краткосрочному (без остаточных деформаций) или долгосрочному короблению, ухудшению механических и других функциональных параметров изделия в процессе его эксплуатации. Следует, по возможности, избегать утолщения стенок в конструкции, поскольку они приводят к проблемам, связанным с усадкой, и вызывают необходимость более длительного охлаждения. Рационально при этом применять знаки и вставки – для формования поднутрений, или добавлять рёбра и элементы жёсткости на краях (торцах) изделия. Это позволяет компенсировать потерю прочности. Внутренние усадочные полости (вакуоли) формируются, когда толстая поверхность изделия, затвердевая в форме, становится достаточно прочной, чтобы выдерживать давление в формующей полости, возникающее в результате охлаждения расплава. И в это время в расплаве происходит образование усадочных полостей (зон разряжения). Усадочные полости представляют собой неоднородности, которые действуют как концентраторы напряжений, когда изделие при эксплуатации испытывает нагрузку. Усадочные утяжины часто образуются на противоположенной стороне стенки, на которой расположены усиливающие рёбра. Проблема усадочных полостей значительно упрощается при наличии больших закруглений в местах пересечения рёбер со стенками. Этот приём используется для уменьшения концентрации напряжений и улучшения движения потока расплава. Толщины рёбер обычно принимают равными 40 – 80% от толщины стенок, на которых они расположены, с радиусами закругления в основании, равными 25 – 40% от толщины стенок. Для маскировки таких дефектов как утяжины и линии спая используют текстурированную поверхность (использование специальной структуры поверхности или невысоких валиков). Также можно избавиться от утяжин – добавляя пенообразующие агенты в исходный термопласт. При этом при литье образуется пенистая структура по всему объёму отливки и утяжины пропадают. Факторы, влияющие на усадку. - Влияние различных условий охлаждения. Изменение усадки по толщине изделия может быть вызвано различными скоростями охлаждения поверхностных слоёв, соприкасающимися с формообразующими деталями формы – пуансоном и матрицей. Неравномерное охлаждение приводит к различному тепловому сжатию материала по толщине изделия, то есть к различной усадке. Горячие поверхности формуемого изделия будут подвергаться усадке большее время, чем холодные. Эти различия в усадке будут приводить к возникновению внутренних моментов сил, которые будут вызывать коробление изделия. Влияние на величину усадки при неравномерной скорости охлаждения может быть минимизировано за счёт правильного выбора системы охлаждения. - Влияние изменения давления в формующей полости. Давление уплотнения и выдержки, используемые во время переработки, оказывает значительное влияние на усадку отлитого изделия. Высокие давления уплотнения и выдержки приводят к снижению усадки материала, а меньшие значения к её увеличению. Давление в полости изменяется от максимального на впуске до минимального в конце пути потока расплава – из-за его сжимаемости. Перепад давлений по длине формующей полости может быть очень существенным, особенно при протяжённом пути потока и тонких стенках изделия. Это приводит к тому, что усадка увеличивается по мере приближения к зонам, удалённым от места впуска. А изменение усадки по длине изделия может привести к размерной деформации и короблению изделия. Одним из способов устранения такой проблемы является использование многовпусковой схемы заполнения. В этом случае путь течения отдельных потоков расплава уменьшается, а давление в формующей полости оказывается более равномерно распределённым, поскольку все области изделия будут находиться ближе к впуску. - Влияние радиального потока расплава. В изделиях с центрально расположенным впускным литником происходит заполнение формующей полости потоком расплава радиального (дискового) типа. В этом случае если изделие коробится в виде купола, то это происходит из-за того, что усадка поперёк окружности оказывается больше чем усадка вдоль радиуса. Если же изделие коробится в виде седла, это означает, что усадка во внутренних слоях изделия больше, чем в наружных слоях. В этом случае коробление изделия сводится к минимуму за счёт комбинированного воздействия разных способов – управлением давления в формующей полости, ориентацией расплава или разным по интенсивности охлаждением. - Факторы, связанные с особенностью термопластов. Различие в усадке, связанные с охлаждением, проявляются во всех термопластах, но наиболее они сильны в частично кристалличных материалах (часть объёма кристаллизуется, а остальная часть находится в аморфном состоянии). Способность такого термопласта образовывать зоны с чисто кристаллической решёткой усиливается, если охлаждение происходит с более низкой скоростью. Таким образом, скорость охлаждения будет в прямую влиять на степень кристаллизации полимера. Усадка отливки из аморфно-кристаллических полимеров будет идти гораздо сложнее, чем отливок из чисто аморфных пластмасс. Поэтому существенное значение здесь будет иметь толщина изделия. Толстостенные отливки, из-за увеличения времени охлаждения (времени кристаллизации), будут иметь высокую степень усадки. В целом усадка изделий из аморфно-кристаллических термопластов без наполнителей в несколько раз больше, чем из аморфных материалов. - Усадка в изделиях, отлитых из термопластов с наполнителем. Наполнитель (в виде волокон, чешуек, шариков) добавляют в термопласт для улучшения его механических свойств – жёсткости, сопротивления ползучести, прочности. Наполнители либо вообще не усаживаются, либо обладают крайне низкой усадкой, так как имеют очень низкий коэффициент термического расширения. Таким образом, мелкодисперсный наполнитель способствует снижению усадки отливок из термопластов. Другие дефекты связанные с конструкцией изделия и формы: - утяжки - струйный режим заполнения полости - недолив, перелив (балансировка литниковой системы, жесткость формы) - деформации при извлечении из формы (литейные уклоны, вакуумные зоны, повысить жесткость формы, изменить шероховатость поверхности, направление полировки, антиадгезив) - коробление (неравномерность усадки из-за разнотолщинности) - отклонение размеров, массы Проблемы литья под давлением изделий из ПМ: спаи Спаи являются характерным признаком многих изделий из термопластичных полимерных материалов (в дальнейшем – ПМ), изготавливаемых литьем под давлением, и в большей или меньшей степени служат причиной ухудшения внешнего вида изделий, их размерной точности, кратковременных и долговременных механических свойств, а также нежелательного изменения их теплофизических, электрических и других характеристик. Тем не менее, во многих случаях не удается избежать появления спаев в литьевых изделиях из ПМ. Однако более глубокое знание механизма и закономерностей образования спаев, влияния на их свойства технологических параметров литья, конструкции изделия и литьевой формы, а также других факторов помогает свести к минимуму негативное влияние спаев на качество литьевых изделий из ПМ. 1. Образование спая Под спаем понимают область в объеме литьевого изделия, соответствующую месту встречи потоков расплава ПМ при заполнении им литьевой формы. Традиционно рассматривают два типа спаев: спай «в касание» (melt line, meld line, streaming weld line) или, иначе, горячий спай (hot weld) и спай «встык» (weld line, butt weld) или холодный спай (cold weld). В обширной литературе, посвященной этим вопросам, применялись различные критерии определения типов спаев. В большинстве работ учитывалось, что важнейшим фактором, благоприятно влияющим на свойства спая, является течение расплава и связанное с ним диссипативное тепловыделение в окрестностях спая в процессе и после его формирования. Продолжающееся течение во внутренних слоях вблизи спая после встречи фронтов потоков расплава, как это происходит при образовании спая «в касание», приводит к более медленному охлаждению ПМ. Если же течение расплава и соответственно диссипация тепла в области спая прекращаются сразу после его образования, говорят о спае «встык». Ранее данная классификация использовалась по отношению к спаям в целом [1]. Позже эту терминологию стали применять к отдельным участкам спая, используя в качестве критерия угол схождения потоков [2]. В условиях устойчивого течения спай возникает при фронтальном соединении потоков расплава. Как известно, течение на фронте потоков расплава термопласта имеет особый характер и называется «фонтанным» течением [3]. Схема образования спая с учетом фонтанного течения при движении двух потоков и их встрече представлена на рис. 1 [4]. | | Рис.1. Схема (вид в сечении полости) последовательного (сверху вниз) образования спая [4] (стрелками показаны направления течения частиц расплава) |  | В реальном процессе образования спаев при встречном движении фронтов расплава реализуется более сложная картина движения расплава, и, наряду с фонтанным течением, происходит течение расплава вдоль спая (рис. 2). Причина этого явления – искривление фронтов расплава, которое связано с характером растекания расплава в полости и наблюдается практически во всех случаях. Изменение направления течения после начала образования спая происходит в локальной области за очень короткий промежуток времени. В такое течение вовлечены только области расплава, непосредственно примыкающие к спаю. По мере сближения периферийных участков фронтов в течение вдоль спая вовлекаются новые объемы расплава. Вблизи области начального контакта фронтов при достаточно большой длине спая (в случае, например, тонкостенных изделий с большой площадью поверхности) может возникать «мертвая» зона, в которой течение прекращается до окончания формирования периферийных участков спая и происходит быстрый рост толщины застывших пристенных слоев. Длина «мертвой» зоны вдоль спая зависит от формы фронтов расплава, которая в свою очередь связана с геометрией изделия, положением впусков и другими факторами. Таким образом, температурные условия и условия течения на различных участках спая неодинаковы, что служит причиной неоднородности структуры и свойств спая по его длине. | Рис. 2. Схема движения расплава при образовании спая (стрелками показаны направления течения расплава |  | Ориентация полимера вдоль спая при встречном движении потоков экспериментально подтверждается различными методами, в частности, с помощью лазерной рамановской спектроскопии (рис. 3). В готовой отливке сохраняется высокая ориентация поверхностных слоев вследствие их почти мгновенного застывания, тогда как во внутренних слоях происходит релаксация ориентационных напряжений. | Рис. 3. Схема ориентации макромолекул в области спая, построенная на основе результатов лазерной рамановской спектроскопии образца поликарбоната в форме лопатки (стрелками показаны направления движения фронтов расплава) | |  | | Похожий механизм реализуется и при образовании спая после знака (рис. 4 и 5), непосредственно за которым возникает «мертвая» зона, где течение быстро прекращается. Длина этой зоны вдоль спая зависит от формы и размеров знака и увеличивается при увеличении диаметра знака с круглым сечением или ширины знака с прямоугольным сечением. Вне этой зоны происходит течение расплава вдоль спая, причем «рост» поверхности контакта потоков происходит, судя по данным работы [5], по механизму фонтанного течения, так как слои расплава, контактирующие с оформляющими поверхностями формообразующих деталей (ФОД) остаются неподвижными. | Рис. 4. Схема последовательного (в направлении слева направо) образование спая после знака 4: 1 – точка начального контакта потоков; 2 – «мертвая» зона; 3 – зона течения вдоль спая |  | Рис. 5. Схема образования спая после знака 4 [10]: 1 – поверхностная канавка; 2 и 3 – соответственно области плохой и хорошей связанности потоков (показаны стрелками) |  | После застывания приповерхностных слоев полимера, прилегающих к спаю, внутренняя область спая все еще сохраняет подвижность, и ее пространственная конфигурация определяется градиентом давления в литьевой полости, который зависит от сбалансированности заполнения. При незначительной несбалансированности заполнения происходит очень быстрое (почти мгновенное) нарастание давления в той области изделия, которая заполняется в первую очередь, что приводит к искривлению поверхности контакта потоков. Свойства конкретной области спая определяются изменяющимися во времени локальными условиями ее формирования, такими как скорость течения, температура, давление и др. Характер изменения данных условий зависит не только от технологического режима литья, но и от геометрии изделия и литниковой системы, а также от расположения области спая в изделии. Из-за особого характера течения расплава в области спая его иногда рассматривают как одну из форм неустойчивого течения. Изделия из прозрачных аморфных полимеров демонстрируют в области спая повышенное двойное лучепреломление, что свидетельствует о высоких остаточных напряжениях. По этой причине на рабочих поверхностях изделий оптического назначения спаи не допускаются. Необходимо учитывать, что аномалия оптических свойств распространяется на всю область контакта потоков расплава, а не только на видимую линию спая. При охлаждении расплава кристаллизующихся полимеров в области спая формируется кристаллическая структура, которая имеет более или менее значительные отличия от структуры других областей литьевого изделия. При этом степень кристалличности и размеры надмолекулярных образований зависят от химической природы полимера, присутствующих добавок, условий течения и охлаждения в конкретной области спая. Известно, что у полимеров, образующих различные кристаллические модификации, например у изотактического полипропилена, в области спая наблюдается аномальное соотношение полиморфных модификаций, заметно различающихся по механическим и другим эксплуатационным характеристикам. Неоднородность процессов кристаллизации во многом определяет неравномерность усадки полимера и тем самым оказывает негативное влияние на свойства спая. Резкое изменение характера течения расплава в области спая приводит к ярко выраженной структурной неоднородности двухфазных полимерных систем и полимеров с волокнистыми и некоторыми типами дисперсных наполнителей. Ухудшение внешнего вида и снижение прочности спаев при литье двухфазных сополимеров и смесей полимеров в области спая связано, в том числе, с неоднородным распределением и ориентацией дисперсной полимерной фазы. Стеклянные и углеродные волокна, а также другие волокнистые наполнители могут ориентироваться при литье под давлением вдоль (в пристенных слоях) или поперек (при радиальном растекании, сходящемся течении, а также на фронте потока) направления растекания расплава. Их ориентация в отливке определяется направлением деформаций расплава. Фонтанное течение на фронте потока является причиной ориентации волокна в направлении толщины изделия. В области спая наблюдается резкое изменение ориентации волокна (рис. 6), что приводит к ухудшению внешнего вида и эксплуатационных характеристик изделия. | Рис. 6. Схема ориентации стеклянных волокон в области спая 1 в направлении, продольном (а) и поперечном (б) к направлению течения потоков расплава ПМ (места впуска показаны стрелками): 2 – ориентация волокон параллельно спаю; 3 – ориентация волокон перпендикулярно спаю; 4 – знак |  | Свойства спая чувствительны к ориентационным эффектам дисперсных наполнителей и пигментов в форме чешуек и коротких волокон [6]. Кроме того, на формирование спая негативное влияние может оказывать воздух, присутствующий в полости формы. В некоторых случаях сильное повышение температуры воздуха при сжатии под действием потоков расплава приводит к появлению подгаров в области спая. Во избежание подобных эффектов рекомендуется делать вентиляционные каналы в местах образования спаев. Вакуумирование полости перед впрыском создает хорошие условия для формирования спая, но данная технология имеет ограниченное применение из-за повышенной стоимости ее оснащения. Для толстостенных изделий, когда сопротивление течению расплава на стадии заполнения крайне мало, большую роль могут играть эффекты инерции течения. В результате может наблюдаться искажение фронта расплава с захватом воздуха и запиранием его на поверхности контакта потоков. 2. Внешний вид спая При формировании спая на поверхности изделия обычно остается след в виде V-образной канавки – «линии спая» (рис. 7). Визуальное восприятие спая зависит от глубины и ширины этой канавки, а также от оптических свойств поверхности литьевого изделия, которые во многом определяются шероховатостью оформляющей поверхности ФОД литьевой формы, типом и составом ПМ. Так, например, при одинаковой глубине канавки у изделия из одного материала спай может быть четким, а из другого – малозаметным. Текстура поверхности изделия оказывает большое влияние на внешний вид спая: наиболее четко выделяются спаи на глянцевой поверхности изделия. | | Рис. 7. Внешний вид поверхностной канавки в области спая на литьевом образце из ПА 6 (снимок получен с помощью сканирующего электронного микроскопа) | 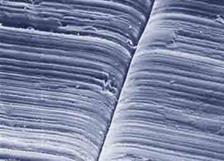 | Поверхностная канавка спая, образованного после знака, имеет наибольшую глубину вблизи знака. По мере удаления от него глубина канавки уменьшается (см. рис. 5). Поверхностная канавка возникает как обычный недолив, вызванный большим сопротивлением течению расплава, в то время как давление расплава на фронте потоков при нормальных условиях заполнения близко к нулевому. Начальная геометрия канавки определяется формой фронтов расплава, образующих спай. Дальнейшее изменение геометрии канавки во времени связано с деформированием застывшего поверхностного слоя полимера под действием давления расплава. При снижении скорости охлаждения уменьшается и скорость роста застывшего поверхностного слоя, он легче деформируется, уменьшая при этом глубину канавки. Изменение давления в области спая в ходе заполнения формы расплавом зависит от положения впуска и разницы времен заполнения областей изделия или, как говорят, несбалансированности заполнения. Быстрый рост давления наблюдается в наиболее удаленной от впуска части полости после того, как туда приходит расплав, в то время как вблизи впуска давление растет гораздо медленнее. Поэтому в конце потоков (при сравнительно небольшой длине затекания) могут создаваться более благоприятные условия для формирования спая, чем вблизи впуска. Таким образом, факторы, способствующие снижению скорости охлаждения поверхностного слоя полимера и повышению давления в области спая, улучшают его внешний вид. Во многих работах экспериментально подтверждается благоприятное влияние повышенной температуры формующей поверхности ФОД (для всех типов термопластичных ПМ) на внешний вид изделий со спаем. При очень низких температурах формы видимая линия спая может значительно удлиняться или даже проходить через все изделие [4]. Внешний вид спаев улучшается при изготовлении ФОД из сталей с уменьшенным коэффициентом теплопроводности, а также при использовании для формующих поверхностей покрытий с пониженной теплопроводностью. В некоторых случаях хороший эффект дает применение вставок из подобных сталей непосредственно в области спая, однако необходимо учитывать, что из-за различных условий охлаждения могут визуально проявляться неоднородность текстуры и неравномерность блеска поверхности изделия. Для изделий, формуемых в литьевых формах с ФОД из алюминиевых сплавов, обладающих повышенной теплопроводностью по сравнению, например, со сталями, характерно значительное ухудшение внешнего вида спаев. Следует заметить, однако, что мероприятия, направленные на снижение скорости охлаждения отливки и улучшение тем самым внешнего вида спая, вступают в противоречие со стремлением уменьшить время охлаждения отливки и соответственно время цикла. Окончательное формирование поверхностной канавки в области спая происходит во время усадочных процессов при полном застывании расплава во внутренних областях изделия (усадка по толщине) и в момент извлечения отливки из пресс-формы (продольная и поперечная усадка). Анизотропия усадки ПМ в области спая связана с молекулярной ориентацией полимера, ориентацией дисперсной полимерной фазы в блок-сополимерах и смесях полимеров, а также с ориентацией частиц наполнителя, что может оказывать большое влияние на внешний вид спая. Из-за влияния анизотропии усадки наряду с канавкой параллельно спаю могут образовываться бугорки, которые иногда могут возникать вместо канавки. Имеет значение даже направление механической обработки ФОД, что также может повлиять на характер усадочных процессов и соответственно внешний вид спаев. Для аморфных полимеров, характеризующихся повышенной вязкостью расплава, высокой жесткостью и малой усадкой, роль усадочных процессов в формировании поверхностной канавки невысока. Известно, что в области канавки при литье аморфных материалов нет следов механообработки формующей поверхности, в то время как эти следы хорошо видны при микроскопическом изучении в других областях отливки. Это доказывает, что канавка формируется уже на стадии заполнения. В то же время для кристаллизующихся материалов, которые имеют пониженную вязкость и высокую усадку, следы формующей поверхности наблюдаются и в области канавки (см. рис. 7). Следовательно, канавка в данном случае образовалась в процессе усадки полимера. Для материалов, содержащих, например, стеклянные волокна, характерны сильно выделяющиеся линии спая, что является следствием ориентации волокон. Локальное нарушение ориентации чешуек алюминия и слюды, применяемых в перламутровых пигментах и пигментах с металлическим блеском, приводит к нежелательным визуальным эффектам, связанным с ориентацией частиц наполнителя. Видимая линия спая в этом случае может тянуться через все изделие. Проблемы с такими пигментами могут возникать даже в том случае, если спай образуется в горячеканальном сопле до впуска в изделие. Улучшение внешнего вида спая достигается снижением содержания в пигменте крупных чешуек, а также при использовании комбинированных пигментов, которые помимо частиц плоской формы, содержат определенную долю частиц сферической формы [6]. Конструкция изделия и расположение впусков могут оказывать большое влияние на внешний вид спаев. Увеличение расстояния между впусками приводит к удлинению поверхностной линии спая. Повышение толщины изделия способствует улучшению внешнего вида спая. Иногда хороший результат может также давать локальное увеличение толщины в области спая. Этот метод лучше применять для спаев, образующихся в начале потоков, так как в этом случае легче обеспечиваются более благоприятные условия формирования спая. 3. Прочность спая Обычно спай является самым слабым местом литьевого изделия, что проявляется при различных механических испытаниях. Рассмотрим влияние спая на прочностные свойства отливок при растяжении. Прочность спая обычно характеризуют его относительной прочностью, которая представляет собой отношение прочности (или предела текучести) образца со спаем к прочности (или пределу текучести) образца без спая, выраженное в долях или процентах. Прочность спаев при растяжении изучают на образцах в виде лопаток, которые отливают в специальных формах соответственно с двумя или одним впуском или вырубают из реальных изделий. Вырубленные образцы позволяют учесть влияние геометрии изделия и расположения мест впуска, а также ориентационные эффекты. Внешний вид спая зависит главным образом от процессов, протекающих в поверхностном слое полимера, в то время как основные явления, влияющие на прочность спая, происходят во внутренней части литьевой полости. Поэтому иногда, даже при неудовлетворительном внешнем виде, спай может быть сравнительно прочным, и наоборот, спай с хорошим внешним видом может иметь низкую прочность. В реальных изделиях прочность спая зависит от площади поверхности контакта потоков, которая определяется пространственной конфигурацией внутренней области спая. Несбалансированное заполнение формы расплавом, нежелательное с точки зрения размерной точности, может, тем не менее, способствовать упрочнению спаев, так как вызывает искривление и соответственно увеличение площади поверхности контакта потоков расплава. Большинство исследователей рассматривают механизм образования спая с позиций теории молекулярной диффузии и обусловливают его прочность глубиной диффузии макромолекул через поверхность контакта потоков. Предполагается, что диффузия происходит только во внутренней части поверхности контакта, тогда как с наружной части существует область плохой связанности потоков расплава, что соответствует экспериментальным наблюдениям. Так, при микроскопическом исследовании спая на срезах и поверхностях разрушения было установлено, что с наружной части может существовать даже разрыв между потоками, иногда в виде явной трещины, продолжающейся от основания V-образной канавки в глубину спая (см. рис. 5 и 8). Глубина области плохой связанности увеличивается при повышении скорости охлаждения зоны спая. | Рис. 8. Схема внутренней части спая [7]: 1 – поверхностная канавка; 2 и 3 – области плохой и хорошей связанности потоков соответственно |  | Литературные данные указывают на большой разброс прочности спая практически для всех типов ПМ. Как правило, высокая прочность спаев (до 95 – 100 %) достигается у ненаполненных ПМ, кристаллизующихся в условиях литья под давлением: изотактического ПП, ПБТ, ПА 6 и ПА 66, полиформальдегида. Крайне низкой прочностью спаев (15 – 20 %) обладают термотропные жидкокристаллические полиэфиры, что объясняют очень медленными процессами диффузии в расплаве этих жесткоцепных полимеров. У ненаполненных аморфных материалов наблюдается корреляция между прочностью спая и разницей между температурами переработки (Тпер) и стеклования (Тс) ПМ [7], от которой зависит время охлаждения отливки до температуры стеклования. Увеличение времени охлаждения ПМ, находящегося еще в вязкотекучем состоянии, повышает прочность спая благодаря более глубокой диффузии макромолекул. Очевидно, этим фактором можно объяснить то, что высокая прочность спаев (до 95 – 100 %) характерна для ПМ, имеющих большую разницу между Тпер и Тс, таких как поликарбонат и полисульфон. У ПМ с небольшой разницей значений Тпер и Тс, например, у ПС общего назначения, прочность спаев существенно ниже. Очень непрочные спаи характерны для смесей несовместимых термопластов, у которых в области спая наблюдаются высокая неоднородность фазовой структуры и резкое изменение ориентации дисперсной фазы. Применение компатибилизаторов в этом случае уменьшает структурную неоднородность и способствует повышению механических характеристик спаев. Низкая прочность спая наблюдается и в смесях термопластов с каучуками, например, в смесях изотактического ПП и этиленпропиленового каучука. Это связано с негативным влиянием неоднородности фазовой структуры и ориентации дисперсной каучуковой фазы. Прочность спаев снижается при увеличении содержания наполнителей (рис. 9) [8]. Особенно сильно этот эффект проявляется для жестких волокнистых наполнителей (например, стеклянных или углеродных) и наполнителей с частицами в форме пластинок. Частицы наполнителей не пересекают границы контакта потоков, что отрицательно сказывается на прочности спая и соответственно литьевого изделия. Локальное изменение ориентации наполнителей приводит к высокой анизотропии усадки вблизи спая, что является другой важнейшей причиной уменьшения прочности спая у изделий из подобных материалов. Направленная химическая модификация поверхности частиц наполнителей с помощью аппретов позволяет повысить прочность не только основного материала, но и спаев. | Рис. 9. Прочность спая в образцах из ПА 66 с различными наполнителями и их массовым содержанием [8]: СШ – стеклянные шарики; СВ – стекловолокно; МН – минеральный наполнитель; АП – антипирен; ПТФЭ – политетрафторэтилен; УВ – углеродное волокно |  | Прочность спаев стала важной характеристикой ПМ, которая в настоящее время обязательно учитывается при создании новых полимеров и композиций. Характер влияния технологического режима литья и конструктивных особенностей изделия на прочность спаев зависит от многих факторов и не укладывается в простые схемы. Многие считают, что прочность спаев «в касание» выше, чем у спаев «встык». Однако, по данным экспериментальных исследований, в большинстве случаев различия между прочностью данных типов спаев незначительны [8], что объясняется, очевидно, сравнительно небольшими отличиями условий их формирования. Имеется множество примеров повышения прочности спая при увеличении толщины изделия, хотя, например, в работе [9] наблюдалось снижение абсолютной и относительной прочности спая для непластифицированного ПВХ при увеличении толщины детали от 2,5 до 4 мм. Известно, что прочность спая, образованного после знака, наиболее низкая в «мертвой» зоне и повышается по мере удаления от знака. В большинстве случаев повышение температуры расплава приводит к упрочнению спая, что можно объяснить, очевидно, увеличением подвижности макромолекул и времени нахождения полимера в вязкотекучем состоянии, что в целом способствует более глубокой диффузии макромолекул. Однако, для тонкостенных изделий в определенном температурном диапазоне может наблюдаться и понижение прочности спая с увеличением температуры расплава, что можно объяснить негативным влиянием повышенной молекулярной ориентации в области спая. Значение скорости впрыска неоднозначно: в некоторых случаях она оказывает очень сильное влияние на прочность спая, в других – практически не влияет, что можно объяснить действием двух конкурирующих факторов. С одной стороны, увеличение скорости впрыска способствует повышению уровня диссипативного тепловыделения в расплаве, что увеличивает температуру полимера в области спая и ведет к его упрочнению. С другой стороны, повышение скорости впрыска сопровождается увеличением молекулярной ориентации полимера, что может быть причиной снижения прочности спая. Характер изменения прочности спая при изменении давления в зоне спая также может быть различным. Например, у аморфных ПМ в некоторых случаях при увеличении давления выдержки прочность спая повышается, а в других – практически не изменяется. Есть примеры, когда прочность спая отливки из полистирола общего назначения в процессе ее охлаждения без выдержки под давлением оказывается большей, чем в нормальном процессе с выдержкой под давлением. В целом это, как и в случае скорости впрыска, также можно объяснить конкуренцией нескольких факторов. Так, при повышении давления уменьшается свободный объем полимера, что снижает подвижность сегментов макромолекул и, очевидно, затрудняет процесс диффузии. Кроме того, с увеличением давления должно увеличиваться время релаксации, что в условиях сравнительно быстрого охлаждения отливки повышает остаточную ориентацию полимера в области спая. С другой стороны, повышение давления до определенного уровня способствует большей плотности и меньшей усадке отливки, включая и зону спая, что должно благоприятно сказываться на его прочности. Для кристаллизующихся термопластов во многих случаях важнейшим фактором, определяющим прочность спая, является температура формующей поверхности ФОД. Повышение температуры формы приводит к снижению скорости охлаждения полимера, что, очевидно, способствует диффузии макромолекул и снижает влияние молекулярной ориентации. Поверхностная канавка уменьшает прочность спая, действуя в качестве концентратора напряжений, что проявляется больше всего для хрупких аморфных материалов, таких как полистирол общего назначения и сополимер стирола и акрилонитрила. Поэтому механическое удаление канавки при фрезеровании или полировке поверхности литьевого изделия ведет к повышению прочности спая. 3. Прогнозирование положения и свойств спая Прогнозирование положения спаев в изделиях со сложной геометрией стало возможным благодаря развитию численных методов моделирования процесса литья. Широкое распространение получили программные продукты на основе так называемой модели Хеле-Шоу, в которой рассматривается двухмерное течение расплава термопластов. В качестве критерия образования спаев различного типа используется угол j схождения потоков: предполагается, что при значении j < 135° возникает спай «встык», а при j > 135° – спай «в касание» (рис. 10). Считается, что при малых углах схождения реализуются наихудшие условия образования спая. Однако данный подход позволяет оценить спай только на качественном уровне. Длина видимой части спая может быть примерно определена по углу схождения потоков: экспериментальные данные свидетельствуют, что в нормальных условиях процесса поверхностная канавка заканчивается, когда угол схождения составляет около 120 – 150°. | | Рис. 10. Схема этапов образования (в направлении слева направо) за знаком 3 спаев «встык» (1) и «в касание» (2) и прогнозирования их положения по углу j схождения потоков [2] |  | Разработка методов моделирования трехмерного течения расплава при литье термопластов создает принципиально новые возможности для прогнозирования течения на фронте потока, положения и свойств спаев. Компьютерные программы для трехмерного моделирования позволяют более точно учесть влияние эффектов, связанных с охлаждением расплава и диссипацией тепла в расплаве вблизи знаков и кромок, определить положение линий спая на поверхности сложных по геометрии толстостенных изделий. В таких изделиях может происходить запирание воздуха на поверхности контакта потоков расплава. Моделирование трехмерного течения и принятые на этой основе решения позволяют предотвратить это нежелательное явление. Компьютерный анализ позволяет оценить влияние конструкции изделия и литниковой системы на положение спаев. Конечно, избавиться от спаев при наличии отверстий в изделии невозможно, но можно перенести спаи из проблемных мест в более выгодные с точки зрения прочности и (или) внешнего вида изделия. Для обеспечения более высокой прочности спаев необходимо избегать их местонахождения между крепежным отверстием и краем изделия или другим отверстием при малом расстоянии между ними, а также в областях, которые подвергаются многократным деформациям. Крайне нежелательны спаи в местах, где уже имеются другие источники повышенных остаточных напряжений или концентраторы напряжений, какими, например, являются острые внутренние углы. Изменение положения спаев достигается за счет локального изменения толщины изделия, количества и положения впусков, а для полости с несколькими впусками – также и при изменении сечения литниковых каналов. Для изделий переменной толщины на положение спая большое влияние может оказывать скорость впрыска. Точность расчетов определяется многими факторами и требует в каждом случае специальной оценки. Как и во всех сеточных методах численного анализа, сетка оказывает большое влияние на точность расчета, поэтому необходимо проводить оценку ее влияния на результаты. Сетки, имеющие слишком низкую и слишком высокую плотность узлов, а также сетки, содержащие излишне вытянутые элементы, вносят значительные искажения в прогнозирование растекания расплава, определения угла схождения потоков и положения спаев. Разработка инженерных методов количественного прогнозирования характеристик внешнего вида и прочности спаев остается актуальной задачей современной науки. | |