Технологичность изделий из пластмасс Конфигурация изделия должна быть таковой, чтобы оно было простым в изготовлении, удобным в эксплуатации, чтобы оно легко оформлялось и извлекалось из формы (например, вместо 1 сложного изделия целесообразно изготовить несколько простых). Чем проще изделие, тем дешевле форма, выше производительность труда, выше точность и качество изделия, и ниже себестоимость проекта. С другой стороны (например, введение рёбер жёсткости) может привести к усложнению конструкции, однако это улучшит характеристики изделия (увеличение прочности при минимальной массе и избежание коробления для больших поверхностных изделий). Общая технологичность изделия направлена: - рациональные условия заполнения расплавом формующей полости; - повышение прочности; - уменьшение поверхностных напряжений в изделии; - повышение степени точности размеров и отклонений; - устранение необходимости механической обработки изделия. Общая конфигурация изделия – не должна препятствовать течению расплава при заполнении формующей полости, поэтому нужно стремиться к наибольшему упрощению конструкции наружных и внутренних поверхностей формы. Основными параметрами материала, влияющими на выбор формы изделия, являются текучесть, или вязкость пластмассы. Поэтому конфигурация изделия должна обеспечить наиболее короткий путь потоку полимера. Условия течения пластмассы влияют на характер и величину внутренних напряжений, усадку и ориентацию материала. Форма изделия должна обеспечивать возможность применения неразъёмных элементов, т.к. они резко повышают стоимость формующей оснастки и увеличивают трудоёмкость её изготовления. Также форма изделия будет напрямую влиять на количество плоскостей разъёма в форме, а, следовательно, на простоту извлечения изделия. Далее рассмотрим основные конструктивные элементы, которые имеются у всех изделий – стенка, дно, рёбра жёсткости, отверстия и углубления, радиусы округления, резьбовые отверстия и армированные элементы. 2.3.1 Выбор толщины стенок и дна. Литье изделия с тонкими стенками — более экономичное производство за счет использования меньшего количества сырья и сокращения длительности цикла. Стоимость материала и затрат, связанных со временем охлаждения, часто дает более 70% вклада в стоимость изделия. На рис. 9.19 можно видеть, что время охлаждения возрастает экспоненциально с увеличением толщины стенок. Удвоение толщины стенок для изделия из АБС с 1,0 до 2,0 мм будет приводить к увеличению времени охлаждения приблизительно в 2,6 раза. Удвоение толщины стенок — с 2,0 до 4,0 мм — будет приводить к увеличению времени охлаждения приблизительно в 3,8 раза. Толщина стенок изделия в общем случае определяется величиной и типом прилагаемой нагрузки, которую изделие должно выдерживать в условиях эксплуатации. К другим факторам, которые также зависят от назначения изделия, относятся электрическая, звуковая и термическая изоляция, а также способность сдерживать проникновение газа. Вне зависимости от конкретных требований целью конструктора должна быть минимизация толщины стенок при удовлетворении функциональных требований к изделию. Конструктор должен учитывать соотношение между толщиной стенок и давлением, которое необходимо для отливки изделия с такой толщиной. Уменьшение толщины стенок будет приводить к экспоненциальному увеличению давления заполнения (в некоторых случаях в 3 раза). Толщина стенок и дна оказывает существенное влияние на возникновение внутренних напряжений в пластиковом изделии, на время выдержки под давлением и на точность изготовления изделия. Разнотолщинность изделий вызывает неравномерную усадку, которая ведёт к образования коробления и трещин в изделии. Большая усадка объясняется неравномерностью протекания процесса застывания изделия в форме. Поэтому основным условием технологичности изделия является его равнотолщинность. Рекомендации по разнотолщинности следующие – 1:2 для изделий из термопластов и 1:3 для изделий из реактопластов. Толщину стенок назначают в зависимости от габаритов изделия, от необходимой прочности и текучести выбранного материала. Существуют следующие эмпирические формулы для определения толщины стенки термопластов и реактопластов: для термопластов для реактопластов где: Smin – наименьшая допускаемая толщина стенки, мм; h – предполагаемая высота стенки, мм; Lтек – текучесть материала по Рашигу, мм. Наиболее часто равнотолщинность нарушается в местах переходов от стенки ко дну изделия, при пересечении стенок друг с другом, при пересечении стенок с ребрами жёсткости, или при пересечении рёбер жёсткости между собой. Это объясняется увеличением массы материала в узлах, из-за чего увеличивается вероятность появления дефектов. Необходимо устранять подобные узлы, выполняя, например, скругление углов стенок и дна (рисунок 5), в местах пересечения рёбер жёсткости делают кольцевую перемычку и т.д.  а б в г д е ж а – L-образное (угловое), б – Т-образное (тавровое), в – К-образное, г – шахматное, д – V-образное, е – Х-образное, ж – крестообразное. Рисунок 5 – Типовые сопряжения стенок и дна Слишком тонкие стенки вызывают значительные трудности при изготовлении изделий. Необходимо предусматривать опасности незаполнения расплавом узких щелей в полости литьевой формы. Профиль стенки может влиять на прочность изделия и потенциальную возможность коробления. Выпуклый профиль имеет более стабильную структуру, чем плоское изделие. Профиль стенки будет также влиять на время охлаждения. Для сопротивления короблению изделие должно задерживаться в литьевой форме дольше, чтобы охладиться сильнее и стать более жестким. Чем холоднее, тем прочнее изделие и тем сильнее оно будет сопротивляться короблению, которое возникает из-за остаточных напряжений. Такие детали изделия, как фланцы, размещенные по его периметру, могут приводить к увеличению жесткости без увеличения толщины стенки. Они должны быть перпендикулярны стенке, на которой размещены, и иметь такую же или несколько меньшую толщину. Фланец с толстыми стенками, размещенный по периметру изделия, будет приводить к деформации изделия, придавая ему выгнутую, куполообразную форму. 2.3.2 Торцы изделий. Они не должны быть чрезмерно утолщёнными, чтобы облегчить формование и извлечение изделия. Особенно важным является оформление тех торцов изделия, по которым происходит выталкивание его из формы, т.к. при выталкивании может происходить изгиб или поломка дна изделий (в особенности тонкостенных). Поэтому в точках выталкивания следует упрочнять изделия. Торцы конструируют в виде буртиков разнообразной конструкции, выполненных, как правило, по периметру изделия и предохраняющих края его от поломок. При этом толщина торцев должна быть в пределах допустимой разнотолщинности, типичные примеры облегчения конструкции буртиков показана на рисунке 6.  а б в г а – неверная конструкция, б, в – достижение равностенности, г – повышение жёсткости, за счёт дополнительного ребра жёсткости. Рисунок 6 – Варианты усовершенствования торцев изделия Отклонения от правильной геометрической формы плоских поверхностей находится в прямой зависимости от величины стрелы прогиба изделия. Значение максимально величины стрелы прогиба определяется по следующей эмпирической формуле:  где: Lmax – наибольший диаметр, измеренный по данной плоскости (либо длина плоской стороны), мм; k – коэффициент, равный 0,016 – для термопластов и 0,01 для реактопластов. Конструкция, когда толщина стенок по периметру изделия толще, чем внутри него, называется «кадровой рамкой» (рис). Производитель такого изделия может столкнуться с большим количеством проблем: Расположение впускных литников по периметру с толстыми стенками будет приводить к эффекту образования «пояска», поскольку расплав переходит от быстрой скорости перемещения в местах с толстыми стенками к медленной в центральной области с тонкими стенками в процессе заполнения литьевой формы. Это может привести к вовлечению воздуха или видимым линиям спая в зонах с тонкими стенками. Расположение впускного литника в центральной зоне будет приводить к образованию пустот и утяжин по периметру. При любом расположении впускных литников зона периметра с толстыми стенками будет более подвержена усадке, чем центральная зона, где существует опасность коробления. 2.3.3 Радиусы закруглений. Радиусы закруглений, установленные на наружных и внутренних поверхностях изделий из пластмасс, позволяют облегчить течение массы в форме, упростить её изготовление, уменьшить износ, упростить извлечение изделия после формования и улучшить внешний вид изделия. За счёт плавных переходов между поверхностями снимаются лишние напряжения, уменьшается величина усадки и повышается точность изделия. Выбор величины радиусов закругления зависит от глубины детали, толщины стенки и марки материала (рисунок 7). Особенно важны радиусы закругления на поверхности изделий из термопластов, поскольку при их изготовлении напор расплава достаточно велик и между поверхностями необходимы плавные переходы, для качественного и быстрого заполнения формы. Рисунок 7 – Рекомендуемые радиусы закругления, в зависимости от глубины формуемой детали 2.3.4 Технологические уклоны. Они облегчают выталкивание изделий из формы после окончания цикла изготовления и используются практически на любой отливке, когда её протяжённость в направлении выталкивания из формы достаточно большая (также могут иметь чисто конструктивное значение). Уклоны не назначаются в следующих случаях: - если конфигурация изделия сама способствует простому извлечению его из формы (ведро, конусный стакан); - если внутренняя полость изделия имеет сложную форму, которая способствует тому, что при раскрытии оно останется на пуансоне - если высота буртов и углублений не превышает 1 – 5 мм; - если изделие тонкостенное и имеет высоту 10 – 15 мм. Технологические уклоны необходимо назначать на вертикальные поверхности, параллельные направлению усилия запирания формы, а также на поверхности изделий, которые параллельны направлению перемещения составных частей сложных форм. Величина технологического уклона определяется в зависимости от высоты пластикового изделия. При назначении угла уклона необходимо учитывать также способ выталкивания пластикового изделия, шероховатость поверхности детали, марку пластмассы. В большинстве случаев при размыкании формы изделие остаётся на пуансоне (при наиболее распространённой конструкции формы, когда матрица располагается в неподвижной полуформе, а пуансон в подвижной). Это связано с действием сил трения между изделием и пуансоном и из-за усадочных напряжений, которые стремятся оторвать изделие от стенок матрицы (рисунок 8). Углы уклона назначаются как на пуансоне (облегчают сталкивание изделия с пуансона), так и на матрице (облегчают выталкивание изделия из матрицы после размыкания формы – минимум 1º). Иногда применяют раздвижные полуматрицы или шибера и тогда изделия могут изготавливаться без углов уклона (рисунок 9).  Рисунок 8 – Углы уклона матрицы и пуансона  Рисунок 9 – Раздвижные полуматрицы После формования изделие плотно усаживается на пуансоне и необходимы значительные усилия, чтобы его столкнуть. Величина усилия сталкивания зависит от многих факторов, таких как усадка материала, его модуль упругости, коэффициент трения металл-термопласт, шероховатость поверхности пуансона и угол уклона поверхностей. Если изделие будет иметь нулевой угол выталкивания, то снять с пуансона его будет чрезвычайно трудно и это может привести к разрушению изделия. Большие углы уклона облегчают выталкивание, но существенно влияют на форму изделия (его конусообразность). При этом следует учитывать, что если изделие снимается легко, то нет опасности его деформации даже при извлечении в тёплом состоянии, чем можно значительно сократить цикл литья. Также нормальные углы уклона приводят к уменьшению величины контактной поверхности изделия с пуансоном и к быстрому уменьшению усилия выталкивания, что способствует быстрому проникновению воздуха и компенсирует влияние вакуумных эффектов в зоне контакта (рисунок 10). 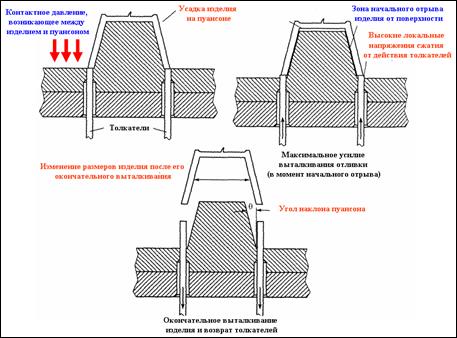 Рисунок 10 – Снятие изделия с пуансона Если изделие имеет большие габариты, то для его сталкивания применяют специальные воздушные клапаны, чтобы с их помощью устранить вакуум. При конструировании пластикового изделия углы наклона пуансона и матрицы целесообразно делать параллельными, чтобы соблюдать условия разнотолщинности. 2.3.5 Рёбра жёсткости. Рёбра жёсткости применяются для повышения жёсткости изделия, для усиления особо нагруженных и выступающих частей детали, для увеличения прочности изделия и для более равномерного распределения внутренних напряжений по объёму отливки (рисунок 11). В первую очередь они необходимы изделиям, подвергающимся изгибающим нагрузкам. На плоских поверхностях изделий они способствуют обеспечению требуемой прочности, предохраняют от коробления. Наиболее предпочтительным вариантом является проектирование тонкостенных изделий, но с рёбрами жёсткости, что способствует экономии материала и увеличивает поверхностную прочность отливки.  Рисунок 11 – Типичные конструкции рёбер жёсткости, имеющих форму пластин Рёбра жёсткости бывают усиливающие, разводящие, конструктивные, технологические, а также обеспечивающие равностенность отливки. Усиливающие рёбра жёсткости используют на поверхностях, не являющиеся лицевыми. Их проектируют в направлении максимального изгиба и повышенных напряжений. Они могут использоваться по всей длине изделия, или в определённых местах, где требуется повысить жёсткость. Рёбра жёсткости должны иметь равномерную толщину, конусность в направлении замыкания формы и закруглённые внутренние и наружные края. Оптимальная форма ребра жёсткости – в виде усечённого конуса с закруглённой вершиной и плавным переходом от стенки ребра к самому изделию. В результате этого уменьшается усилие съёма изделия, снимается концентрация локальных напряжений и обеспечивается постепенное изменение толщины. Закругление в основании ребра улучшает характеристики заполнения формы и демпфирует напряжения, возникающие в процессе усадки (рисунок 12). Если рёбра жёсткости имеют достаточно толстые стенки, то это может привести к образованию утяжин или формированию усадочных пустот. Использование больших закруглений, с одной стороны снижает концентрацию локальных напряжений, но с другой стороны может привести к возникновению усадочных напряжений и усадочных пустот, связанных с увеличением радиуса кривизны. Рисунок 12 – Оптимальная конструкция ребра жёсткости Высота рёбер определяется их числом и конструкцией изделия (у плоских изделий она обычно равна удвоенной ширине его у основания). Высота внутренних рёбер должна быть не менее чем на 0,5 мм меньше общей высоты изделия, для того чтобы упростить механическую обработку и облегчить монтаж и сборку изделий. Также высота рёбер определяется свойствами текучести расплава и технологическими характеристиками процесса извлечения изделий (свойства материала). Более высокие рёбра жёсткости – материалы с низкой вязкостью, низким коэффициентом трения и высокой степенью усадки. Если выталкивание изделия из формы осуществляется по ребрам жёсткости, то следует иметь в местах выталкивания небольшие утолщения с плоской вершиной. Рёбра должны быть отполированы в направлении извлечения для облегчения выталкивания изделия. Высокие рёбра увеличивают жёсткость конструкции, но создают опасные изгибающие напряжения на кромках рёбер (рисунок 13). При конструировании рёбер жёсткости следует соблюдать следующие правило - лучше использовать много тонких и невысоких рёбер, чем несколько широких и высоких. Рёбра должны располагаться вдоль направления течения расплава, чтобы улучшить условия заполнения формы. Также рёбра жёсткости могут быть использованы как внутренние ускорители для движения потока расплава, чтобы способствовать наилучшему заполнению полости формы.  Рисунок 13 – Различные конструкции рёбер жёсткости Также используют перпендикулярно направленные друг относительно друга рёбра жёсткости, в целях сопротивления изгибающим нагрузкам в разных плоскостях. Усиливающие рёбра жёсткости могут иметь простейшее прямоугольное сечение (рисунок 14), либо модифицированное сечение для более простого течения расплава и извлечения из литьевой формы (рисунок 15).  Рисунок 14 – Рёбра жёсткости без учёта специфики производства  Рисунок 15 – Рёбра жёсткости, модифицированные под производство Основная часть приведенных выше базовых принципов конструирования для ребер и косынок предназначена для обеспечения необходимых изменений в толщине стенок, которые часто приводят к короблению изделий. В частности, ребра позволяют увеличить длину или ширину изделия. Конструктор должен учитывать требования конкретного приложения и косметические требования, предъявляемые к изделию. Если косметические требования не являются главными, то уменьшение толщины ребра становится менее важным. В результате утяжина из-за толстого ребра, в сущности, не будет иметь негативных последствий для структуры. Это выглядит довольно правдоподобно при сравнении напряжений, которые могут развиться между основной стенкой и тонким ребром. Можно допускать образование пустот во многих изделиях на пересечениях ребра с основной стенкой. При приложении изгибных нагрузок максимальные усилия будут приложены к концу ребра. Следующей областью высоких нагрузок будет поверхность основной стенки напротив ребра. Наиболее вероятно, что разрушение изделия произойдет на кончике ребра, а не в месте образования утяжины, расположенной в зоне с относительно малыми напряжениями. Далее рассмотрим жесткость материала. Утяжина формируется, Когда отвердевший материал на поверхности изделия будет втягиваться внутрь из-за наличия усадки в материале, который находится под ним. Материал с низким модулем упругости будет легко втягиваться внутрь материалом, в котором происходит усадка. Материал с высоким модулем при охлаждении и наличии внешнего затвердевшего слоя будет сопротивляться втягиванию. В результате материалы с высоким модулем упругости будут с большей вероятностью образовывать пустоты и заметность утяжины будет сведена к минимуму. Базовые принципы конструирования высоты ребер и косынок каждый раз опровергаются успешно отлитыми изделиями. Однако конструктор должен быть осведомлен о потенциальных проблемах, которые создаются в случае отклонения от базовых принципов, и должен быть готовым реагировать на них. 2.3.6 Отверстия и углубления. Их расположение и число влияют на величину усадки и точность размеров. Могут быть разработаны отверстия любой конфигурации, но следует учитывать трудоёмкость изготовления знаков для форм, исходя из чего предпочтительнее более простые конфигурации отверстий. Отверстия делятся на сквозные, глухие и ступенчатые (рисунок 16). Они могут быть выполнены полностью во время формования, или с последующим предположительным сверлением после формования.  Рисунок 16 – Различные варианты оформления отверстий Расстояние между отверстиями и расстояния от краёв отверстия до края изделия должно быть такими, чтобы исключить вероятность поломки и растрескивания. Наиболее целесообразно располагать отверстия в направлении усилия смыкания формы. В отдельных случаях можно допустить расположение отверстий под углом или на разных осях, причём сами отверстия могут иметь разную конфигурацию. Наибольшую длину глухих отверстий, расположенных в направлении, перпендикулярном направлению формованию, можно определить по формуле:  , где: l – длина отверстия; d – диаметр отверстия; E – модуль упругости материала формующего знака; fmax – максимальная величина допускаемого прогиба; р0 – удельное давление на материал в процессе формования. Допускаемую длину сквозных отверстий, также расположенных перпендикулярно направлению формования, можно определить по формуле: 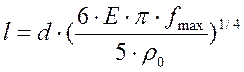 Изделия с отверстиями под крепёжные болты необходимо конструировать так, чтобы использовать прокладочные шайбы для увеличения опорной поверхности. При проектировании изделий различные углубления, пазы, канавки позволяют регулировать толщину стенок, массу изделия и снижать степень усадочных напряжений при литье. Но при этом следует учитывать, что это ведёт к осложнению формующей оснастки для данного изделия. Бобышки Бобышками обычно называют сплошные или полые цилиндрические детали проектируемого изделия, которые соединяются с основной стенкой. Они могут быть использованы для сборки с помощью самонарезающихся винтов, штифтов, запрессованных пробок, направляющих колонок и других аналогичных деталей. Бобышки часто усиливаются ребрами или косынками. Бобышки могут быть неприсоединенными или крепиться к боковым стенкам с помощью ребер. Бобышка может не быть прикрепленной прямо к боковой стенке, поскольку пересечение со стенкой будет приводить к образованию зоны большей толщины, что может стать причиной образования утяжин или пустот. Полая бобышка может привести к образованию линий спая на внешней, лицевой поверхности изделия, поскольку материал будет обтекать знак, формирующий ци-линдрическую полость в центре бобышки. Кроме того, линия спая обычно формируется как шов встык и обычно подвержена структурному разрушению, если кольцевые напряжения развиваются при установке в бобышку винта или шпильки в процессе сборки. Бобышка может быть размещена вблизи стенки и прикреплена к ней с помощью ребра, которое обеспечивает, с одной стороны, жесткость, а с другой — вентиляцию (воздух может проходить от бобышки вдоль ребра к боковой стороне стенки). Стандартная рекомендуемая конструкция бобышки показана на рис. 9.27. Внутренний диаметр бобышки обычно определяется функциональными требованиями, которые к ней предъявляются. При использовании самонарезающихся винтов внутренний диаметр обычно равен среднему диаметру винта. Внешний диаметр приблизительно в 2,5 раза больше внутреннего диаметра. Существует компромисс между необходимой прочностью и минимизацией толщины бобышки. Если бобышка слишком толстая, то в ней будут при отливке возникать пустоты. Если вкручивать самонарезающийся винт, то он может попасть в пустоту и таким образом уменьшить прочность на разрыв. Наружные диаметры могут варьироваться в зависимости от конструктивных особенностей винта и полимерного материала. В материалах со средней величиной модуля упругости или ниже могут использоваться самонарезающиеся винты. Существует набор специально сконструированных винтов, которые будут уменьшать кольцевые напряжения на бобышку. Материалы с высоким модулем требуют специальных винтов, поскольку напряжение, формируемое винтом, может стать причиной растрескивания бобышки. Высота бобышки должна быть не более чем в 2,5 раза больше внутреннего диаметра. Это необходимо, чтобы свести к минимуму потенциальные отклонения знака, формирующего внутреннюю полость бобышки, а также решить проблемы заполнения, уплотнения и извлечения. Поверхность пересечения бобышки с основной стенкой должна иметь радиус закругления минимум 0,25 мм. Пересечение внутренней поверхности бобышки и основания должно иметь радиус, который составляет 10% от толщины основной стенки. Толщина стенки внутреннего основания бобышки должна составлять 75% от толщины основной стенки. На внутреннем диаметре в верхней части бобышки фаска под углом 45 градусов должна быть предусмотрена. Сужение поперечного сечения наружных стенок бобышки должно составлять минимум 0,5 градуса. Уменьшение внутреннего диаметра бобышки также желательно, но его не делают, поскольку это может нарушить прочность сборки при использовании винта или шпильки. В результате возникает необходимость использования специальной втулки, чтобы гарантировать извлечение бобышки из литьевой формы. Следует ожидать, что относительно большие поперечные сечения в зоне пересечения бобышки и основной стенки будут, как правило, приводить к возникновению утяжин или изменению блеска поверхности в месте установки бобышки. Можно использовать альтернативную конструкцию для уменьшения объема материала в месте соединения бобышки с основной стенкой. Эта конструкция уменьшит потенциальную вероятность возникновения утяжин или пустот, но потребует дополнительных знаков. Отверстия должны обеспечивать пространство для минимизации проблем извлечения и возникновения зон с уменьшенной прочностью в местах образования линий спая. Если прочность линии спая является самым важным моментом, то отверстия могут быть намечены в процессе литья, а затем просверлены в ходе дополнительной обработки. Поднутрения могут существенно увеличить трудности, возникающие при извлечении изделия. Примером поднутрения с включением отверстия в боковую стенку изделия является внутреннее опорное кольцо, которое часто используется для крышек контейнеров, а также при изготовлении внутренних и наружных резьб. Это требует наличия специальных возможностей у литьевых форм, таких, как складывающиеся пуансоны, раздвижные полуматрицы и специальные плиты съема. Это увеличивает начальную стоимость литьевой формы, объем операций технического обслуживания и время цикла литья. Если возможно, следует избегать отверстий или поднутрений, которые формируют особые требования к литьевых формам. Если отверстие расположено в стенке, которая составляет прямой угол с направлением движения подвижной полуформы (пуансона) литьевой машины, то можно использовать обычный знак, который нужен для формирования центрального отверстия в бобышке и может быть легко извлечен в процессе нормального открывания литьевой формы; однако если отверстие сделано в боковой стенке изделия, которая не перпендикулярна направлению движения подвижной полуформы литьевой машины, то извлечение потребует использования специальных средств. Некоторые отверстия на боковых стенках могут быть сконструированы таким образом, что не потребуется смещения в сторону. Для этой цели может быть использована ступенчатая линия разъема литьевой формы. Минимальный угол отсечки 5° позволяет гарантировать приложение усилия смыкания литьевой формы к поверхностям соприкосновения полуформ, что предотвращает образование подгаров и гарантирует, что обе полуформы не будут царапать друг друга в процессе замыкания и размыкания. Эта технология упрощает процесс извлечения, устраняя необходимость применения специальных средств. Некоторые поднутрения, как, например, в разрезном кольце на большинстве крышек пластиковых бутылок, не могут быть отделены от знака, который их формирует. При проектировании таких разрезных колец конструктор должен учитывать прилегающую стенку и свойства материала. Разрезное кольцо должно быть сконструировано таким образом, чтобы изделие могло быть снято или сдвинуто со знака, который формирует его без повреждения самого разрезного кольца или всего изделия. Это требует, чтобы разрезное кольцо было сконструировано с уменьшенным направляющим углом. Предпочтительнее использовать угол в 45 градусов. Кроме того, боковая стенка должна быть в состоянии отклоняться во время извлечения кольца. Это требует учета глубины поднутрения, диаметра знака и предельных значений деформации и напряжения материала. Поскольку свойства материала при относительно высоких температурах, когда изделие должно быть извлечено из литьевой формы, как правило, неизвестны, то конструирование поднутрения максимальной величины, при котором изделие могло быть извлечено, часто базируется на основе предела динамической деформации, который получен при комнатной температуре. Это консервативный конструкторский подход, поскольку пределы деформации для большинства пластических материалов намного больше при температурах извлечения. Предел динамической деформации материала — наиболее информативный параметр его характеристики при быстрых деформациях, которые наблюдаются при посадке кольца. Например: Определить максимальную высоту опорного кольца, которое может быть использовано на изделии, которое имеет внутренний диаметр 70 мм. Динамическая деформация материала составляет 3%.  Следует ожидать, что для отделения изделия понадобится специальная плита съема. Приведенная выше информация представляет собой упрощенный подход к кон-струированию поднутрений. Для проверки конструкции часто требуется изготовление прототипа. Рифления Рифления — поверхностные мелкие выступы или канавки применяют в основном для увеличения контактной поверхности, т.е. предусматривают в основном на поверхности ручного инструмента. Иногда рифления выполняют с декоративной целью или для маскировки отдельных дефектов поверхности (утяжины, коробление). Рифления на цилиндрических поверхностях выполняют в виде ребер, расположенных в направлении извлечения изделия из формы. По геометрической форме они могут быть полукруглыми, трапецеидальными или треугольными с закруглением острых граней. Торец рифлений выполняют закругленной формы и он не должен доходить до края изделия на некоторую величину "а". 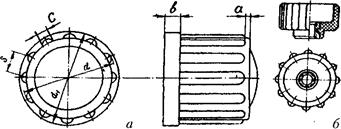 Рис. 2.29. Варианты выполнения рифлений: а — технологичный; б — нетехнологичный. Второй конец рифлений обычно упирается в выступающий цилиндрический поясок (буртик), чтобы в плоскости разъема формы была ровная геометрическая поверхность. Это необходимо для устранения острых кромок на торце изделия и легкости удаления облоя, который может образоваться в плоскости разъема формы. Диаметр буртика di должен быть несколько больше размера изделия с рифлениями "rf". Обычно рифления располагают в одной из формующих частей пресс- формы (матрице или пуансоне), т.к. при размещении их в двух частях, в месте смыкания пресс-формы будет образован облой, который на фигурной поверхности сложно удалить без повреждения поверхности изделия, см. рис. 2.296. При проектировании изделий необходимо предусматривать на рифлениях технологические уклоны. Расстояние между рифлениями (шаг S), см. Рис. 2.29, выбирается экспериментально, но наиболее часто оно равно 2 -j-2,5 с, (с —ширина рифления). Рифления на плоских поверхностях наносят в виде параллельных или сетчатых линий, как показано на Рис. 2.30. На прямоугольных участках можно применять рифления в виде параллельных линий или сеток с диагональным расположением линий. На участках треугольной формы лучше всего применять рифление, направление ребер которого должно совпадать с направлением каких-либо двух сторон контура. Высота ребер рифления, применяемого для плоских поверхностей, равна 0,5 —2 мм. Рифления выполняют заподлицо с плоскостью изделия или утопленные в стенку на величину 0,2 —0,3 мм. Применение рифлений на боковых поверхностях требует дополнительных плоскостей разъема пресс-формы и значительно усложняет их конструкцию. Однако, если рифления не глубокие, а изделие пустотелое и изготавливается из эластичного полимера, то их можно расположить и на боковой поверхности, но боковые стенки рисок (углублений) должны иметь наклон. Надписи и рисунки Надписи и рисунки обычно получают в процессе прессования или литья под давлением. При изготовлении матрицы или пуансона механической обработкой, рельеф "негатива" надписи делают углубленным в металле, поэтому надпись на изделии будет выступать над поверхностью, как показано на Рис. 2.316. В том случае, если надпись находится на поверхности, которая подвергается трению, чтобы она не истиралась при эксплуатации изделия, вокруг надписи делается выступающее защитное ребро, высота которого несколько больше, чем высота надписи. Высота надписей, выступающая над поверхностью обычно должна быть в пределах 0,3 — 0,5 мм. Если высота букв больше, они должны иметь технологические уклоны. При изготовлении формующих знаков пресс-форм холодным выдавливанием (мастер пуансоном), надписи на поверхности изделия получаются углубленными, см. Рис. Надписи, полученные по этому способу, получаются менее четкими и с меньшей глубиной букв. Форма сечения надписей может быть весьма разнообразной и зависит от способа изготовления пресс-форм, а также от геометрии режущего инструмента. Общее требование к геометрической форме надписей, они не должны иметь острых граней или углов, см. Рис. Рисунок на изделии во время формования может изготавливаться за счет гравирования матрицы или пуансона. Рисунок свободно формуется на днище или крышке изделия, но его можно предусматривать и на боковых конических поверхностях, когда выступающий рельеф рисунка не мешает извлечению изделия из формы. Контур рисунка при таком способе выступает над поверхностью. Однако для нанесения рисунка на пуансон или матрицу можно использовать различные электрохимические методы, поэтому рисунки могут быть или углубленными или выступающими над поверхностью изделия.  Рис. 2.32. Формы сечений элементов надписей. При выполнении рисунка, как правило, не требуется глубокая гравировка, он бывает заметен на полированной поверхности изделия достаточно четко за счет различной шероховатости поверхности. При разработке рисунков необходимо учитывать форму изделия, они должны композиционно согласовываться друг с другом. 2.3.7 Резьбовые соединения пластиковых изделий. Как правило, получается в процессе формования. При изготовлении резьбы необходимо считаться с усадкой материала и спецификой изготовления формующих знаков и колец (шиберов). Резьбовыми кольцами (шиберами) оформляются резьбы на внешней поверхности изделия. Могут использоваться как цельные, так и разборные кольца. Цельные кольца (матрицы), применяются при литье прочных пластиков (полипропилен). Разборные кольца рекомендуются при литье хрупких пластмасс, и полностью исключает повреждения поверхности при съёме изделия. Однако это усложняет конструкцию формы и требует, в некоторых случаях, зачистки облоя по плоскостям разъёма. Профиль резьбы может быть любым, но предпочтительна метрическая резьба. Примеры оформления резьбы приведены на рисунке 17. Соотношения диаметров и длин рабочей части резьбовых знаков могут быть приняты такими же, как для гладких стержней, оформляющих отверстия, однако обычно не требуется слишком глубоких резьбовых отверстий, и глубина формования назначается равной 1,5 – 2 диаметрам резьбового знака. Также стоит увеличивать примерно в 1,5 раза перемычку между резьбовыми отверстиями и расстояние от краёв отверстий до краёв детали, по сравнению с гладкими отверстиями.  а б  в г а – однозаходная и многозаходная резьба, б – резьба одинакового шага на последовательно расположенных участках, в – неправильное оформление резьбы, г – правильное оформление резьбы Рисунок 17 – Примеры оформления резьбы в пластиковых изделиях Если резьба в изделии имеется в 2-х и более местах, то она должна иметь одинаковый шаг. Заходная часть резьбы выполняется так, чтобы на начальной длине не было нарезки (облегчает свинчивание), а на другом конце резьбы также желателен участок без нарезки. Также нужно учитывать возникновение в резьбовом соединении осевой силы, которая создаёт растягивающие осевые напряжения в стенках изделия и сжимающие напряжения на поверхности резьбы. При этом с увеличением числа витков, сжимающие напряжения уменьшаются, а растягивающиеся увеличиваются, и возрастает опасность разрушения изделия. Число витков резьбы рассчитывается по следующим формулам: - из условия равнопрочности стенки изделия на растяжение и резьбы на смятие:  , где: σр – предел прочности резьбы на растяжение; σсм – предел прочности резьбы на смятие; δ – толщина стенки изделия, определённая по впадинам резьбы; h – высота резьбы. - из условия равнопрочности на растяжение и изгиб стенки резьбового соединения: 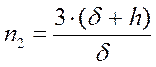 При этом всегда n2 > n1. Если в резьбовом соединении используется металлический болт, то пластиковую гайку выполняют с запрессованной металлической арматурой, чтобы предотвратить быстрое разрушение пластмассы. 2.3.8 Пластиковые изделия с металлической арматурой. Это неразъёмные соединения, образованные в результате формования, за счёт усадки материала и разности коэффициентов теплового линейного расширения пластмассы и металла. Необходимость применения арматуры появляется в нескольких случаях – когда без неё нельзя повысить прочность и жёсткость отдельных участков изделия, для повышения точности и прочности при сопряжении с другими изделиями, для повышения стойкости к износу и т.д. Арматура бывает 3-х видов – втулочная, стержневая и листовая, причём она может находиться, внутри изделия, или выступать из него. Варианты установки арматуры в пластиковом изделии представлены на рисунке 18.  Рисунок 18 – Варианты фиксации арматуры в пластиковых изделиях Однако существует ряд конструктивных ограничений – появление микротрещин в материале изделия из-за повышенных напряжений, в связи с разным коэффициентом линейного расширения пластмассы и металла; увеличение времени процесса формования, связанного с загрузкой армирующих элементов; увеличение стоимости формующего инструмента. Пластиковые изделия с металлической арматурой необходимо рассчитывать на прочность, определяя растягивающие и сжимающие напряжения в стенке изделия. |