Подробно описать технологию горячего эмалирования. Эмалирование – вид декоративной отделки, связанный с покрытием участков изделия легкоплавкой стекловидной массой. В эмалированных изделиях удачно сочетаются механическая прочность металла с химической устойчивостью стекла с его декоративными характеристиками. Основой под эмаль служат : медь и её сплавы, драгоценные металлы и их сплавы. Как и всех технологические процессы, эмалирование начинается с подготовительных операций. К этим операциям относятся: подготовка к нанесению самых эмалей и поверхности металла-основы. Подготовка металла-основы. Хорошему сцеплению эмали с металлом-основой способствует– безукоризненное состояние металла-основы: гомогенная структура металла, отсутствие вредных примесей и внутренних напряжений, чистая поверхность металла. При эмалировании следует избегать разнотолщинности металла, применения деталей и фрагментов со сложными пайками, длинных прямоугольников, абсолютно гладких плоскостей. Больше всего для эмалирования подходят слегка выпуклые формы, т.к. они не деформируются при обжиге. Выгнутая поверхность по сравнению с вогнутой увеличивает яркость эмали. Металл с раковинами и вздутиями непригоден для дальнейшей обработки, т.к. в большинстве случаев эти дефекты проявляются на заключительных этапах. Подготовка металла-основы состоит из следующих этапов: 1) Отжиг.Изделие подвергают кратковременному нагреву до достижения цвета тёмно-красного каления (~0,65-0,7t0пл металла). Благодаря рекристаллизации металла, исчезают напряжения, образующиеся при обработке, сгорают все остатки клеёв, масел и жиров. 2) Отбеливание. После отжига изделие охлаждают в воде и травят в 10 %-ом растворе серной кислоты t0 раствора 50-60°С. Золото, медь и томпак можно отбеливать в 10 %-ом растворе азотной кислоты, также можно травить в растворе лимонной кислоты. Нельзя погружать в кислоту горячие изделия, т.к. кислота проникает в поры и микротрещины на поверхности металла и в дальнейшем вызывает дефекты эмалей. В результате травления поверхность становится шероховатой, что улучшает сцепление эмали с основой. 3) Промывка. Промывку производят последовательно в горячей и холодной воде. Последнюю промывку необходимо произвести в дистиллированной воде. 4) Сушка. 5) Обезжиривание.Изделие обезжиривают, если его нельзя отжинать и протравливать. Производят с помощью трихлорэтилена, спирта, аммиака, раствора соды. После чего тщательно промывают под проточной водой. Подготовка эмалей.Подготовка эмалей состоит из следующих этапов. 1. Дробление и размалывание. Этим этапом начинается подготовка эмалей, если они поступили в кусках. Для этого берут нужное количество кусков эмали, прокаливают в муфельной печи в течении 10 мин при температуре 400 оС и охлаждают в воде, для упрощения размалывания. Далее эти куски помещают в фарфоровую ступку с пестом и размалывают до нужного размера фракции. 2. Растирание. Эмаль растирают до нужного размера зерна в фарфоровой ступке с небольшим добавлением дистиллированной воды. Периодически мутную воду сливают и заменяют свежей. Важно помнить, что крупнозернистые эмали расплавляются легче и обладают большим блеском, чем мелкозернистые. Но размер зерна эмали также зависит от размера заполняемых ячеек. 3. Отмучивание. Растёртую эмаль помещают в фарфоровую чашу и тщательно перемешивают пластиковым шпателем, чтобы вода охватила всю эмалевую массу. Оставшуюся сверху мутную воду сливают и заменяют свежей. Этот процесс повторяют до тех пор, пока вода не станет совсем прозрачной. Нанесение эмали.После подготовительных операций следует этап нанесения эмали. Эмаль наносят двумя основными способами: «сухим» и «мокрым». «Сухим» способом эмалевый порошок наносят с помощью сита, насеивая его на поверхность основы, или распылением с помощью пистолета-распылителя. Эмали при этом способе наносятся неотмученные, что может привести к помутнению прозрачных эмалей этот способ особенно хорош для нанесения глухих эмалей. «Мокрый» способ наиболее часто используется при изготовлении горячих эмалей. Увлажнённую эмаль наносят в подготовленные ячейки кистью или шпателем, выравнивают и уплотняют лёгкими постукиваниями по изделию сбоку. Отмученный порошок должен быть увлажнён, но без избытка влаги. Сушка эмали. Сначала влагу из нанесённой эмалевой кашицы удаляют с помощью кисти, а затем изделий сушат при температуре 60-80оС в течении ~30 мин. Время сушки зависит от толщины нанесённого слоя и от помола. В результате неполной просушки эмали возможны дефекты покрытия: - водяной пар взрывоподобно улетучивается, захватывая с собой частицы эмали, в результате чего образуются непрокрытые участки. - при вскипании воды частицы эмали смещаются в соседние иначе окрашенные поля, образуя инородные цветовые пятна. - у эмали тонкого помола образуются морщины и трещины - эмаль отслаивается с нижней стороны и с вертикальных плоскостей. - при обжиге могут появиться пузыри в эмалевом покрытии Обжиг эмалей. Обжиг эмалей осуществляют в муфельной печи при температуре выше температуры плавления эмали на 20-40 оС. это уменьшает время обжига, улучшает цвет эмали, металл основы меньше окисляется. Температура плавления эмалей находится в диапазоне 600-900 оС, поэтому обжиг эмалей начинают с наиболее тугоплавкой с последующим понижением температуры плавления. Принцип последовательного понижения температуры плавления эмалей позволяет избежать дефектов эмалевого покрытия, но увеличивает трудоёмкость процесса. Поэтому необходимо подбирать эмали с пересекающимися температурными интервалами плавления, для снижения количества обжигов. Охлаждение и правка после обжига. После обжига подставку с изделием достают из муфеля и дают намного остыть рядом с ним. После этого изделие снимают с подставки на теплоизоляционную плиту для дальнейшего охлаждения. Слишком медленное охлаждение приведёт к помутнению эмалей, а слишком быстрый отвод тепла – к повреждению (растрескиванию) эмалевого покрытия. При обжиге изделия могут деформироваться. Правку производят, когда на эмали исчезнет цвет красного каления. В этот момент эмаль и металл ещё находятся в пластичном состоянии. Для правки плоских поверхностей используют деревянные пуансоны, покрытые асбестом, металлические правильные доски. Наиболее часто достаточно сильно прижать предмет к подставке двумя штапелями. Избежать деформации изделия при обжиге можно использованием правильно сконструированной отожжённой подставки, нанесением контрэмали, снятием внутренних напряжений в металле-основе. Очистка изделий от окалины. Очистку эмалированных изделий производят химическим и механическим способом. Наиболее часто используется механический способ, т.к. травление в кислотах может привести к растрескиванию эмалей. Химическому травлению подвергают изделия с кислотоустойчивыми эмалями. На эмали, чувствительные к агрессивным средам наносят защитный слой из смеси парафина и канифоли в соотношении 1:1. Травление производят в растворах соляной, серной, азотной или лимонной кислот с малой их концентрацией. Травление кратковременно, травящий раствор и изделие д.б. холодными. Более устойчивы к травлению прозрачные эмали, особо чувствительны – глухие красных, светло-жёлто, зелёных, чёрных цветов. Промывка и сушка.Промывка используется для удаления остатков травящих растворов и полировальных паст. Далее производится сушка при комнатной температуре. Шлифование и полирование. Если на изделии эмали и металл должны иметь одну поверхность, изделие подвергают следующим операциям: - шлифование производят при помощи абразивных брусков и шкурки различной зернистости. Этот процесс проводят на шлифовально-полировальном станке и бормашине. Шлифование должно производиться с достаточной подачей воды, для удаления частиц абразива. После шлифования изделие необходимо промыть в мыльной воде с помощью щётки, затем промыть в дистиллированной воде и тщательно высушить. - горячее полирование – обжиг отшлифованного изделия до появления зеркального блеска на эмали. После изделие охлаждают, механически удаляют окалину. Этот этап часто исключают из процесса отделки эмалей, ограничиваясь только механической обработкой. - финишная полировка осуществляется на шлифовально-полировальном станке и бормашине с использованием мягких фетровых и войлочных кругов и полировальной пасты. - промывка. После полирования изделия очищают от остатков полировальных паст с помощью обезжиривания (сода, аммиак и др.). После этого изделие промывают в проточной воде и с помощью пароструйного генератора. Билет №21 Набор для сервировки стола (ложка , вилка, нож) из мельхиора в стиле «барроко». Годовой выпуск – 1500 шт. 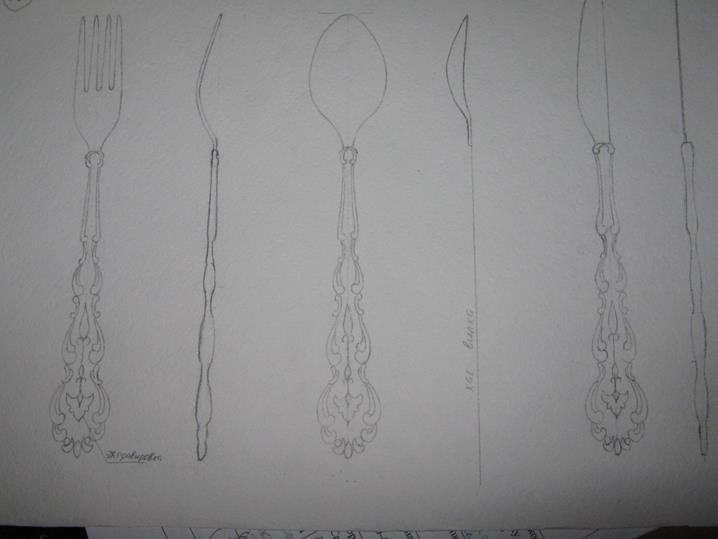 1.3 Дать краткую аннотацию набора и его композиционный анализ, отразив художественную ценность, оригинальность, пропорции, симметрию, ритм, пластику, динамику или статику всего изделия, или его отдельных элементов. Барокко - броская цветистость и динамичность - соответствовали самоуверенности. Основные элементы барочного стиля, так же, как и ренессансного, восходят к античности; главное же, что отличает барокко, - это повышенная динамичность форм, беспокойный ритм кривых линий. Пышные, помпезные формы барокко находят широкое применение в первую очередь в культовом строительстве, в архитектуре и интерьере новых церквей и монастырей. Стиль барокко появился в XVI—XVII веках в Европе. Барокко свойственны контрастность, напряжённость, аффектация, стремление к величию и пышности, к совмещению реальности и иллюзии. Характерные детали барокко — атланты, кариатиды, маскароны. Для барокко свойственно влечение к необычному, удивительному, поразительному. Основные цвета:красный, розовый, белый, голубой с желтым акцентом. Сочетание контрастных цветов (популярное – белый с золотом), богатые цветовые палитры (от изумрудного до бордо). Интересный выпукло-вогнутый асимметричный рисунок; в формах полуокружности, прямоугольника, овала; выраженное горизонтальное членение. Соблюдается общая симметрия. Разработанный набор для сервировки стола выполнен с характерным для барокко стремлением к помпезности, пышности и сдержанному величию, которые выражаются нагромождением декоративных элементов, не играющих конструктивной роли и являющихся лишь украшением. Используется причудливый, асимметричный декор, но общая симметрия изделий соблюдена. Дополнительная декоративная обработка – электрохимическое гравирование выполнена в виде орнамента характерного для барокко. 2 Разработать технологический процесс изготовления изделия 2.1. Технология – листовая штамповка и электрохимическое гравирование металлов Листовая штамповка Наиболее оптимальным процессом изготовления столовых приборов из цветного металла (мельхиора) является штамповка – один из видов обработки металлов давлением, производимый при помощи штампов на прессах. Все холодноштамповочные операции могут быть разделены на следующие основные группы: разделительные, формообразующие, комбинированные и штампосварочные. Штамповка — процесс пластической деформации материала с изменением формы и размеров тела. Существуют два основных вида штамповки - листовая и объёмная. Листовая штамповка подразумевает в исходном виде тело, одно из измерений которого пренебрежимо мало по сравнению с двумя другими (лист-до 6 мм). В противном случае штамповка называется объёмной. Для процесса штамповки используются прессы - устройства, позволяющие деформировать материалы с помощью механического воздействия. Листовая штамповка. Сущность способа заключается в процессе, где в качестве заготовки используют полученные прокаткой лист, полосу или ленту, свёрнутую в рулон. Для деталей, получаемых листовой штамповкой, характерно то, что толщина их стенок незначительно отличается от толщины исходной заготовки. К преимуществам листовой штамповки относятся: возможность получения деталей минимальной массы при заданной их прочности и жёсткости; достаточно высокие точность размеров и качество поверхности, сравнительная простота механизации и автоматизации процессов штамповки, обеспечивающая высокую производительность. Электрохимическое гравирование металлов Основой методики является метод электрохимического травления металлов. Коротко он заключается в следующем. Деталь, на которой делается надпись, рисунок (предварительно нанесенный специальным лаком), погружается в раствор электролита, она является анодом. Катодом, который также погружен в раствор электролита, служит полоска нержавеющей стали. При включении тока происходит электрохимическое травление, то есть растворение незащищенных лаком поверхностей детали. На рисунке схематично показан принцип процесса. Цифрами показаны: 1. Металлическая деталь. 2. Протравленный участок. 3. Слой лака сохраняет металл не протравленным. 2.2Выбор и обоснование выбора основных и вспомогательных материалов Основной материал: Мельхиор –сплав меди главным образом с никелем (5—30%). М. — однофазный сплав, представляющий собой твёрдый раствор; хорошо обрабатывается давлением в горячем и холодном состоянии, после отжига имеет предел прочности около 400 Мн/м2 (40 кгс/мм2). Наиболее ценное свойство М. — высокая стойкость против коррозии в воздушной атмосфере, пресной и морской воде. Увеличенное содержание никеля, а также добавки железа и марганца обеспечивают повышенную коррозионную и кавитационную стойкость, особенно в морской воде и в атмосфере водяного пара. Благодаря никелю М., в отличие от латуней и бронз, имеет не желтоватый, а серебристый цвет, который в сочетании с высокой коррозионной стойкостью предопределил применение сплава МН19 (19% Ni) для изготовления посуды и др. изделий массового потребления, в том числе чеканных. МН19 Температура плавления: 1190 °C Температура горячей обработки: 900 - 1030 °C Температура отжига: 600 - 780 °C Химический состав в % материала МН19 Ni+Co | Fe | C | Si | Mn | S | P | Cu | As | Pb | Mg | Zn | Sb | Bi | Примесей | 18 - 20 | до 0.5 | до 0.05 | до 0.15 | до 0.3 | до 0.01 | до 0.01 | 78.5 - 82 | до 0.01 | до 0.005 | до 0.05 | до 0.3 | до 0.005 | до 0.002 | всего 1.5 | Электроды (катоды, -). Самый подходящий материал - мягкая нержавеющая сталь. Чаще всего электроды представляют собой полоски листовой стали, расположенные с двух сторон по стенкам ванны травления. Если деталь имеет вытравливаемый рисунок с одной стороны, необходимо разместить электрод напротив вытравляемой поверхности, в противном случае возможно травление с различной (неравномерной) глубиной, что является заметным дефектом. Электрод должен превышать вытравливаемую площадь. Описать технологию изготовления ложки методом штамповки: разработать схему вырубного штампа; задать схему раскроя; приближенно определить коэффициент использования металла; определить технологические режимы вырубки; усилие вырубки, зазор между матрицей и пуансоном, на один из размеров рассчитать исполнительные размеры матрицы и пуансона При вырубке контуры вырубаемых заготовок должны быть удалены друг от друга на величину технологической перемычки. а1 – межконтурная перемычка (м/у контурами деталей) а – боковая (м/у контуром детали и краем заготовки) Деталь – ложка с габаритами 165×23мм. Для вырубки данного вида детали выбираем прямой раскрой полосы заготовки: Материал МН19, толщина металла S= 2 мм, B1=181 мм, B2=27 мм, толщина перемычек а=2 мм, а1= -2 мм. Ширину полосы определяем по формуле: bп = B + 2·а = 181 + 4 = 185 мм Принимаем длину полосы L = 1000 мм Площадь полосы S = В · L = 185 · 1000 = 185000 мм2 Шаг штамповки t = B + а1 = 27 -2 = 25 мм Количество деталей, получаемых из полосы: L/t = 1000 / 25 = 40 шт (40 ложки) Неиспользуемый остаток полосы: L ост = L – t · 40 = 1000 –1000 = 10 мм Количество полос, необходимых для выполнения год. программы (1500 шт/год): 1500 / 40 = 38 шт Площадь листа: S л = 38 · S = 7,030м2 Расчет коэффициента использования металла. Для листовой штамповки выбор исходной заготовки осуществляется путем экономического анализа возможных вариантов раскроя материала и определения оптимального. Общий коэффициент использования металла при штамповке из полосы или ленты определяется следующим образом: η = 100 · (f · n / L · b) f – площадь детали, мм2. При определении площади разделения - параметры изделия определяем укрупнено. f = 2400мм2 n – количество фактических деталей, получаемых из полосы с учетом использованных концевых отходов L – длина полосы или ленты, мм b – ширина полосы или ленты, мм η = 100 · ( 2400 · 40 / 1000 · 185) = 52,0 % Выбор схемы вырубки-пробивки. Вырубка в данном случае осуществляется без прижима. Расчет усилия вырубки-пробивки. Усилие вырубки-пробивки штампами с плоскими режущими кромками определяется по формуле: Р=К · L · S · σср , [ H ] К – коэффициент притупления режущих кромок (1,1 ÷ 1,3) σсд – сопротивление сдвигу, МПа σсд = 300-400 МПа L – длинна контура вырубаемой детали L1 = 450 мм; S – толщина детали = 2 мм Р = 1,3 · 410 · 2 · 350 = 373100 Н = 373,1 кН Выбор конструктивных элементов матрицы и пуансона. Деталь с размерами: B1=181h14(), B2=27h14() Толщину матрицы Hм определяют следующим образом: Нм = S+ Kм√(ap+ bp) + 7 S – толщина штампуемого материала, мм ap + bp – размеры рабочей зоны матрицы, мм Kм – коэффициент = 0,5 Нм = 2 + 0,5 √(181 + 27) + 7 = 11,96 мм Принимаем Нм = 12 мм а) двухсторонний зазор между матрицей и пуансоном: z = 8% S; z = 2 × 0.08 = 0,16 мм б) глубина матрицы 12 мм в) толщина рабочего пояска матрицы 3 мм Расчет исполнительных размеров пуансона и матрицы, назначение допусков на них. Толщина материала 2 мм. При вырубке наружного контура: Bм = (bH – δИ)+δ bП = (bH – δИ – z )-δ δИ – допуск размера изделия; δМ – допуск размера матрицы; δП – допуск размера пуансона; +δ – допуск размера матрицы; -δ – допуск размера пуансона; z – зазор. Bм1 = (bH –0,8 · δИ)+δ = 181 - 0,8 · 1,15 = 180,08+0,122+0,055 Bм2 = (bH –0,8 · δИ)+δ = 27 - 0,8 · 0,52 = 26,584+0,033 bП1 = (bH – 0,8 · δИ – z )-δ = 181 - 0,8 · 1,15 – 0,16 = 179,92-0,057 bП2 = (bH – 0,8 · δИ – z )-δ =27 - 0,8 · 0,52 – 0,16 = 26,424-0,021 Схема расположения допусков на исполнительные рабочие размеры пуансона и матрицы.  Рис. 1. Схема полей допусков размеров матрицы и пуансона при вырубке.  Рис. 2. Схема допусков размеров матрицы и пуансона при пробивке. Квалитеты при изготовлении пуансона и матрицы определяют в зависимости от квалитета штампуемых изделий. Изделия по 9 квалитету, матрица – по 8, пуансон – 7. 2.5 Технология электрохимического гравирование 1. Подготовка детали заключается в обезжиривании её поверхности, куда будет наноситься лак. Обезжиривание необходимо для очистки изделий от различного рода загрязнений. С хорошо обезжиренного металла вода стекает полностью, не оставляя капель и потеков. Если остаются капли, вода прилипает к металлу (точное выражение), то в этих местах есть жир. Потрите их щеткой с раствором более тщательно и повторите промывку и проверку. 2. Приготовление специального лака. Для нанесения надписей и рисунков на металл используется специальный лак. Лак обеспечивает надежную защиту участков детали от вытравливания и легко удаляется в конце процесса. Гудрон - основной компонент 93%. Требуемое количество практически равно объему готового лака. Канифоль в измельченном виде около 30 см3 – 5%. Гудрон необходимо измельчить (расколоть молотком) и поместить в металлическую посуду с крышкой, в которой и будем готовить лак. Добавим туда скипидар (2%) и помешиваем для растворения. Можно оставить на некоторое время для растворения кусочков гудрона. Канифоль так же измельчают и перемешивают с кусочками гудрона. Хотя некоторые источники рекомендуют добавлять канифоль в уже растворенный гудрон. Тут главное обеспечить расплавление и равномерное их перемешивание. Желательно получить вязкость жидкой сметаны. Теперь необходимо подогреть смесь для лучшего перемешивания до температуры 200-250 град. 3. Нанесение рисунка на металл производят по шаблону или через копировальную бумагу. 4. Покрытие лаком производится с помощью кисти вручную. Под рабочую руку подкладывают деревянную подставку, для снятия напряжения с руки, и во избежание задевания изделия руками. Затем лаку дают подсохнуть примерно 2-3 часа. Следующей операцией идет подработка рисунка, с помощью пера или заостенного стержня из оргстекла. Процарапывание рисунка относят к операции гравировки. Она заключается в процарапывании тонких линий с помощью острой иглы. Удаление крупинок лишнего лака нужно выполнять сдуванием либо с помощью ваты, смоченной в спирте. Спирт не растворяет лака, но удаляет грязь с поверхности изделия. В случае дефектов при покрытии лаком, его можно полностью смыть бензином либо другим растворителем. 5. Сушка лака. Самый распространенный и надежный способ - это сушка в сушильном шкафе. Температура 100-130 град. Время сушки - 30-40 мин. После чего охлаждение при комнатной температуре. Другой способ - это естественная сушка. Просто оставляем деталь при комнатной температуре в проветриваемом месте. Обычно за 3-4 дня лак высыхает полностью. 6. Операция после сушки. Перед последующей травкой необходимо дополнительно промыть и обезжирить деталь, что делают путем легкого протирания ватой, смоченной спиртом. 7. Подготовка детали к травлению. Главное требование - обеспечить герметичную защиту частей, не подвергаемых травлению. Это можно закрыть с помощью полиэтилена или пластилина. Источник постоянного тока. В общем случае источник должен обеспечивать постоянный ток силой 3-10 ампер, обязателен амперметр, постоянно показывающий ток. Желательно иметь защиту от короткого замыкания по неосторожности, которая с успехом обеспечивается плавким предохранителем соответствующего номинала. Ванна для травления. Желательно, чтобы ванна была изготовлена из непроводящего ток материала. Например: полиэтилен, пластмассы и т.д. Главное требование: деталь должна свободно помещаться в ванне полностью погруженная в электролит. Состав электролита. для травления мельхиора обычно травят в 10—12%-ном растворе серной кислоты с добавлением хромпика из расчета 5 г на 1 л раствора. Предварительно хромпик растворяют в воде. Рабочая температура 30-40%оС. Электроды (катоды, -). Самый подходящий материал для изготовления это - мягкая нержавеющая сталь. Чаще всего электроды представляют собой полоски листовой стали, расположенные с двух сторон по стенкам ванны травления. Если деталь имеет вытравливаемый рисунок с одной стороны, необходимо разместить электрод напротив вытравляемой поверхности, в противном случае возможно травление с различной (неравномерной) глубиной, что является заметным дефектом. Электрод должен превышать вытравливаемую площадь, в противном случае возможно получение неравномерной глубины травления. Срок службы катодов не ограниченный. Они не растворяются при работе, а только загрязняются. На них осаждаются соли металлов. Уход за ними заключается в промывке горячей водой и немного зачистить наждачной шкуркой. 8. Процесс травления. Время на травления необходимо 30 минут. Контролируют глубину визуально, время от времени доставая деталь. Сила тока 2-3 А. 9. Смывка. Протравленную деталь отсоединить от электродов, убрать пластилин и другие средства защиты. Лак смыть тряпочкой, смоченной в скипидаре. Окончательную, чистовую промывку делают растворителем. |