ПОЗНАВАТЕЛЬНОЕ Сила воли ведет к действию, а позитивные действия формируют позитивное отношение Как определить диапазон голоса - ваш вокал
Игровые автоматы с быстрым выводом Как цель узнает о ваших желаниях прежде, чем вы начнете действовать. Как компании прогнозируют привычки и манипулируют ими Целительная привычка Как самому избавиться от обидчивости Противоречивые взгляды на качества, присущие мужчинам Тренинг уверенности в себе Вкуснейший "Салат из свеклы с чесноком" Натюрморт и его изобразительные возможности Применение, как принимать мумие? Мумие для волос, лица, при переломах, при кровотечении и т.д. Как научиться брать на себя ответственность Зачем нужны границы в отношениях с детьми? Световозвращающие элементы на детской одежде Как победить свой возраст? Восемь уникальных способов, которые помогут достичь долголетия Как слышать голос Бога Классификация ожирения по ИМТ (ВОЗ) Глава 3. Завет мужчины с женщиной 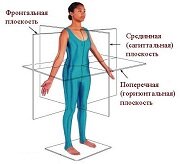
Оси и плоскости тела человека - Тело человека состоит из определенных топографических частей и участков, в которых расположены органы, мышцы, сосуды, нервы и т.д. Отёска стен и прирубка косяков - Когда на доме не достаёт окон и дверей, красивое высокое крыльцо ещё только в воображении, приходится подниматься с улицы в дом по трапу. Дифференциальные уравнения второго порядка (модель рынка с прогнозируемыми ценами) - В простых моделях рынка спрос и предложение обычно полагают зависящими только от текущей цены на товар. | Установка в зажимное приспособление с пневматическим зажимом Литье: | | | | | | | | | | | в песчаную форму машинной формовки по металлической модели | — | | | | | | | | | | | | | | | | | | | | | | | | | | | | | | | | | | | | | | | | | | | | | | | | | | в постоянную форму | | | | | | | | | | | | | | | | | | | | | по выплавляемой модели | | | | | | | | | — | — | | | | | | | | | | | под давлением | | | | | | | | | — | — | Горячая штамповка | — | | | | | | | | | — | Горячекатаная | | | | 100 55 | 110 60 | | | — | — | — | Предварительно обработанная | | | | | | | | | | | | Шлифованная | | | | | | | | | | | Примечания: 1. Установка на магнитной плите не дает погрешности закрепления. 2. Поперечный размер заготовки принимать наибольшим в сечении по нормали к обрабатываемой поверхности. 3. Погрешность закрепления дана по нормали к обрабатываемой поверхности. 41. Элементы допусков по недоштамповке Нед и износу штампов Иш определяемые по весу штампованных заготовок мм Масса штампованных поковок, кг | По недоштамповке для групп точности | По износу штампов для групп точности | 1-Й | 2-Й | 3-Й | 1-й | 2-й | 3-й | <0,25 | 0,40 | 0,6 | 1,0 | 0,20 | 0,3 | 0,5 | 0,25—0,63 | 0,50 | 0,8 | 1,5 | 0,25 | 0,4 | 0,7 | 0,63—1,60 | 0,63 | 1,2 | 2,0 | 0,32 | 0,5 | 1,0 | 1,60—2.50 | 0,80 | 1,4 | 2,5 | 0,40 | 0,6 | 1,3 | 2,50—4,00 | 0,90 | 1,6 | 2.7 | 0,45 | 0,7 | 1,4 | 4,00—6,30 | 1,00 1,00 | 1,7 | 3,0 | 0,50 | 0,8 | 1,6 | 6,30—10,00 | 1,10 | 1,8 | 3,5 | 0,55 | 0,9 | 1,9 | 10,00—16,00 | 1,20 ,20 | 2,0 | 3,7 | 0,60 | 1,0 | 2,0 | 16,00—25,00 | 1,40 | 2,2 | 4,0 | 0,70 | 1,1 | 2,2 | 25,00—40,00 | 1,60 | 2,5 | 5,0 | 0,80 | 1,2 | 2,5 | 40,00—63.00 | 2,00 | 3,0 | 6,0 | 1,00 | 1,3 ,3 | 2,8 | 63,00—100,00 | 2,60 | 4,0 | 8,0 | 1,30 | 1,4 ,4 | 3,4 | 100,00—125,00 | 3,00 | 4,6 | 9,0 | 1,50 | 1,5 ,5 | 3,7 | 125,00—160,00 | 3,60 | 5,4 | 11,0 | 1,80 | 1,6 ,6 | 4,3 | 160,00—200,00 | 4,10 | 6,4 | 13,0 | 2,00 | 1,8 ,8 | 4,9 | 42. Элементы допусков Нез, не зависящие от износа штампов, определяемые по размерам штампованных поковок, мм Толщина (высота), длина или ширина штампованных поковок, мм | Для групп точности | 1-й | 2-й | 3-й | <50 | ±0,10 | ±0,2 | ±0,3 | 50–120 | ±016 | ±0,4 | ±0,6 | 120–180 | ±0.20 | ±0,5 | ±0,7 | 180–260 | ±032 | ±0,6 | ±0,9 | 200–360 | ±0.40 | ±0,7 | ±1,1 | 360–500 | ±0,63 | ±0,8 | ±1,2 | 500–630 | ±0.80 | ±0,9 | ±1.3 | 630–800 | ±1,00 | ±1,0 | ±1,5 | 800–1000 | ±1,15 | ±1,2 | ±1.8 | 1000–1250 | ±1,25 | ±1.5 | ±2,1 | 1250–1600 | ±1,40 | ±1,8 | ±2,5 | 1600–2000 | ±1,60 | ±2,2 | ±3,0 | 2000–2500 | ±1,80 | ±2.7 | ±3,5 | | | | | | Колебания усадки принимают Ку = 1,0 мкм/мм. Суммарные значения расчетных допусков следует округлять с точностью до 0,1 мм для 1-й и 2-й групп точности и с точностью 1,0 мм для 3-й группы точности штампованных заготовок. Значения промежуточных допусков для различных видов механической обработки определяются по классам точности, приведенным в таблицах экономической точности обработки (приложение ///). Пример 1. Рассчитать припуски на обработку и промежуточные предельные размеры для диаметра 50+°'06 отверстия корпуса, показанного на рис. 15. На остальные поверхности (I, 2, 3) назначить припуски и допуски по ГОСТ 1855—55. Заготовка представляет собой отливку 1-го класса точности, массой 3,5 кг. Технологический маршрут обработки отверстия 50+0,05 состоит из двух операций: чернового и чистового растачивания, выполняемых при одной установке обрабатываемой детали. Заготовка базируется на данной операции на плоскость основания 2 и два отверстия Æ 10А, изготовленные предварительно. Схема установки при обработке ясна из рис. 15.  Рис. 15. Корпус (чертеж и схема установки при обработке отверстия Æ 50+0,'05) Расчет припусков на обработку отверстия 0 50+0'06 ведем путем составлении табл. 43, в которую последовательно записываем технологический маршрут обработки отверстия и все значения элементов припуска. Суммарное значение /?; и Т, характеризующее качество поверхности литых заготовок, составляет 600 мкм (табл. 27). После первого технологического перехода величина Т для деталей из чугуна исключается из расчетов, поэтому для чернового и чистового растачивания находим по табл. 29 только значения Rz, соответственно 50 и 20 мкм. и записываем их в расчетную таблицу. Суммарное значение пространственных отклонений для заготовки данного типа определится по формуле 
43. Расчет припусков и предельных размеров по технологическим переходам на обработку отверстия в 50+0.06 корпуса (рис. 14) Технологические переходы обработки поверхности 50+0."- | Элементы припуска, «км | Расчетный припуск 2zmin, мкм | Расчетный размер dp, мм | Допуск d, мм | Предельный размер, мм | Предельные значения припусков, мкя | rz | Т | r | e | dmin | dinax | |  | Заготовка . . . | | | | | | 48,078 | | 47,68 | 48,08 | | | Растачивание: | | | | | | | | | | | | черновое . , , | | — | | | 2×920 | 49,918 | | 49,75 | 49,92 | | | чистовое . . . | | — | —. | | 2×66 | 50,05 | | 50,00 | 50,05 | | | | | | | | | | | | | | | | | | | | | | | | Итого....................... 1970 2320 Величину коробления отверстия следует учитывать как в диаметральном, так и в осевом его сечении, поэтому  Величину удельного коробления для отливок находим по табл. 32 (d и / — диаметр и длина обрабатываемого отверстия). При определении rсм в данном случае следует принимать во внимание точность расположения базовых поверхностей, используемых при данной схеме установки и полученных на предыдущих операциях относительно обрабатываемой в данной установке поверхности. Так, если бы для получения размера (5) (47-0,34) при обработке плоскости основания 2 использовалось отверстие, то последующая погрешность расположения отверстия относительно поверхности 2 была бы равна допуску, который выдерживался при обработке поверхности 2 от отверстия, т. е. 0,34 мм. Если же при обработке поверхности 2 в качестве базы использовалась, как это и бывает в большинстве случаев, какая-то наружная поверхность, то следует учитывать смещение стержня, который формирует отверстие относительно наружной поверхности. Последнее принято определять как отклонение от номинального размера в отливке, определяемое допуском, на размер соответствующего класса точности. Эти же соображения следует принимать во внимание при определении погрешности размера (Г) в горизонтальной плоскости, т. е. смещения положения отверстия заготовки относительно наружной ее поверхности. Так как в качестве базы при сверлении и развертывании отверстий Æ 10А использовалась боковая поверхность отливки, то для определения погрешности расположения обрабатываемого в данной установке отверстия 50+0,05 относительно базовых отверстий Æ10А следует принять смещение стержня относительно наружной поверхности отливки, определяемое допуском на размер (Г) в отливке. Учитывая, что суммарное смещение отверстия в отливке относительно наружной ее поверхности представляет геометрическую сумму в двух взаимно перпендикулярных плоскостях, получаем  где dБ и dГ — допуски на размеры (Б) и (Г) по классу точности, соответствующему данной отливке (табл. 7). Таким образом, суммарное значение пространственного отклонения заготовки составит  Величина остаточного пространственного отклонения после чернового растачивания: P1 = 0,05r3 = 0,05 ×294 = 15 мкм. Погрешность установки при черновом растачивании  Погрешность базирования в данном случае возникает за счет перекоса заготовки в горизонтальной плоскости при установке ее на штыре приспособления. Перекос при этом происходит из-за наличия зазоров между наибольшим диаметром установочных отверстий и наименьшим диаметром штырей. Наибольший зазор между отверстиями и штырями определяется как Sмах = dA + dB +S min где dA — допуск на отверстие: dA == 16 мкм = 0,016 мм; dB — допуск на диаметр штыря: dB == 14 мкм == 0,014 мм; Smin — минимальный зазор между диаметрами штыря и отверстия; Smin = 13 мкм = 0,013 мм. Тогда наибольший угол поворота заготовки на штырях может быть найден из отношения наибольшего зазора при повороте в одну сторону от среднего положения к расстоянию между базовыми отверстиями:  Погрешность базирования на длине обрабатываемого отверстия в этом случае составит eб = l tga =100 0,0004 = 0,04 мм = 40 мкм, где l — длина обрабатываемого отверстия. Погрешность закрепления заготовки (табл. 40) eЗ принимаем равной 120 мкм. Тогда погрешность установки при черновом растачивании  Остаточная погрешность установки при чистовом растачивании e2== 0,05e1 + eИНД » 6 мкм. Так как черновое и чистовое растачивание производится в одной установке то eИНД=0 На основании записанных в таблице данных производим расчет минимальных значений межоперационных припусков, пользуясь основной формулой  Минимальный припуск под растачивание: черновое  чистовое  Графа «Расчетный размер» (dР) заполняется, начиная с конечного, в данном случае чертежного, размера последовательным вычитанием расчетного минимального припуска каждого технологического перехода. Таким образом, имея расчетный (чертежный) размер, после последнего перехода (в данном случае чистового растачивания 50,05) для остальных переходов получаем: для чернового растачивания dР1„ =50,05r3— 0,132=49,918 мм для заготовки dР2= 49,918 — 1,84 = 48,078 мм. Значения допусков каждого перехода принимаются по таблицам в соответствии с классом точности того или иного вида обработки. Так, для чистового растачивания значение допуска составляет 50 мкм (чертежный размер); для чернового растачивания d = 170 мкм; допуск на отверстие в отливке 1-го класса точности по ГОСТ 1855—55 составляет б == 400 мкм. В графе «Предельный размер» наибольшее значение (dmax) получается по расчетным размерам, округленным до точности допуска соответствующего  Рис. 16. Схема графического расположения припусков и допусков на обработку отверстия Æ 50+0105 корпуса (рис. 14) перехода. Наименьшие предельные размеры (dmin) определяются из наибольших предельных размеров вычитанием допусков соответствующих переходов. Таким образом, для чистового растачивания наибольший предельный размер — 50,05 мм, наименьший — 50,05—0,05 = 50 мм; для чернового растачивания наибольший предельный размер — 49,92, а наименьший — 49,92—0,17=49,75; для заготовки наибольший предельный размер — 48,08 мм, наименьший — 48,08 — 0,4 == 47,68 мм. Минимальные предельные значения припусков zпрmin равны разности наибольших предельных размеров выполняемого и предшествующего переходов, а максимальные значения zпрmax — соответственно разности наименьших предельных размеров, Тогда для чистового растачивания 2zпрmin = 50,05-49,92 = 0,13 = 130 2zпрmax = 50 - 49,57 = 0,25 = 250 для чернового растачивания 2zпрmin = 49,92-48,08 = 1840 мкм 2zпрmax = 49,57 - 47,68 = 2,07 = 2070 мкм Все результаты произведенных расчетов сведены в табл. 43 На основании данных расчета строим схему графического расположения припусков и допусков по обработке отверстия 50+0,05 (рис. 16). Общие припуски z0min и z0max определяем, суммируя промежуточные припуски и записываем их значения внизу соответствующих граф: 2z0min = 130 + 1840 = 1970 мкм 2z0max = 250 - 2070 = 2320 мкм Общий номинальный припуск z0ном = z0min =ВЗ - ВД =1970 + 200 - 50 = 2120 мкм dЗном = dДном – z0ном =50-2,1 = 47,9 мм Производим проверку правильности выполненных расчетов: zпрmах2 - zпрmin2 = 250 – 130 = 120 мкм; d1-d2 = 170-50 = 120 мкм; zпрmах1 - zпрmin1 = 2070 – 1840 = 230 мкм; d3-d2 = 400 - 170 = 230 мкм; На остальные обрабатываемые поверхности корпуса припуски и допускг выбираем по таблицам (ГОСТ 1855—55) и записываем их значения в табл. 44. 44. Припуски и допуски на обрабатываемые поверхности корпуса (рис. 15) по ГОСТ 1855—55 (размеры в мм) Поверхность | Размер | Припуск | Допуск | табличный | расчетный | 3,4 | Æ50 | 2×2,0 2,0 2,0 | 2×1,06 — — | ±0,2 ±0,3 ±0,3 | | | | | | | | | На рис. 17 показан чертеж заготовки корпуса с припусками на механическую обработку. Пример 2. Рассчитать припуски на обработку и промежуточные предельные размеры на поверхность Æ шестерни ведущей (рис. 18). На остальные обрабатываемые поверхности назначить припуски и допуски по таблицам ГОСТ 7505—55. Заготовки — штамповка на ГКМ, группа точности — 2-я. Масса заготовки 11,3 кг.  Рис.17 Заготовка корпуса (рис 15) с начисленными допусками и припусками 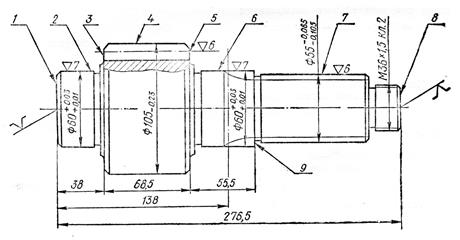 Рис 18. Шестерня ведущая (чертеж и схема установки при обработке поверхности Æ ) Технологический маршрут обработки поверхности Æ состоит из o6тачивания предварительного и окончательного и шлифования предварительного и окончательного. Обтачивание и шлифование производится в центрах, схема установки показана на рис. 18. Так же как и в предыдущем примере, записываем технологический маршрут обработки в расчетную табл. 45. В таблицу также записываем соответствующие заготовке и каждому технологическому переходу значения элементов припуска. Так как в данном случае обработка ведется в центрах, то погрешность установки в радиальном направлении равна нулю, что имеет значение для рассчитываемого размера. В этом случае эта величина исключается из основной формулы для расчета минимального припуска, и соответствующую графу можно не включать в расчетную таблицу. Суммарное отклонение  Допуск на поверхности, используемые в качестве базовых на фрезерно-центровальной операции, рассчитываем по формуле dЗ, = Нед + ИШ + КУ ; Нед = 2,0 мм; ИШ = 1,0 мм; Ку = 1,0×60 = 60 мкм = 0,06 мм; d3 = 3.06 мм » 3,0 мм;   Остаточная величина пространственного отклонения: после предварительного обтачивания p 1 = 0.06 1820 = 109 мкм; после окончательного обтачивания р2 = 0,04 1820 = 73 мкм; после предвартельного шлифования р3 = 0,02 × 1820 = 36 мкм. Расчет минимальных значений припусков производим, пользуясь основ ион формулой: 2zmini =2(Rzi-1-i+Ti-1+ri-1) Минимальный припуск: под предварительное обтачивание 2zmin1 = 2 (150 + 250 + 1820) = 2 × 2220 мкм; под окончательное обтачивание 2zmin2 = 2 (50 + 50 + 109) =2×209 мкм; под предварительное шлифование 2zmin3 = 2 (30 + 30 + 73) = 2 × 133 мкм; Г под окончательное шлифование 2zmin4 = 2 (10 + 20 + 36) = 2 × 66 мкм. Аналогично предыдущему примеру производим расчет по остальным графам таблицы. 45. Расчет припусков и предельных размеров по технологическим переходам на обработку поверхности 0 60+0'03 шестерни ведущей (рис. 17) Технологические переходы обработки поверхности Æ  | Элементы припуска, мкм | Расчетный припуск 2zmin. мкм | Расчетный размер dp, mm | Допуск d, МКМ | Предельный размер, MM | Предельные значения припусков, мкм | RZ | T | r | dmin | dmax | 2zпрmin | 2zпрmax | Заготовка | | | | | 65,27 | | 65,3 | 68,3 | | | Обтачивание: | | | | | | | | | | | предварительное | | | | 2×2220 | 60.83 | | 60,9 | 61,3 | | | Окончательное | | | | 2×209 | 60,41 | | 60,41 | 60,53 | | | Шлифование: | | | | | | | | | | | предварительное | | | | 2×133 | 60,14 | | 60,14 | 60,17 | | | Окончательное | | | | 2×66 | 60,01 | | 60,01 | 60,03 | | | Итого. . . | | | | | | | | | | | | | Графа «Расчетный размер» (dp ) заполняется, начиная с конечного (чертежного) размера, путем последовательного прибавления расчетного минимального припуска каждого технологического перехода. dP3 = 60,01 + 0,132 = 60,142 » 60,14 мм; dP2 = 60,14 + 0,266 = 60,406 » 60,41 мм; dP1 = 60,41 + 0,418 = 60,828 » 60,83 мм; dP3 = 60,83 + 4,444 = 65,274 » 65,27 мм. Записав в соответствующей графе расчетной таблицы значения допусков на каждый технологический переход и заготовку, в графе «Наименьший предельный размер» определим их значения для каждого технологического перехода, округляя расчетные размеры увеличением их значений. Округление производим до того же знака десятичной дроби, с каким дан допуск на размер для каждого перехода. Наибольшие предельные размеры вычисляем прибавлением допуска к округленному наименьшему предельному размеру; dmах4=60,01 + 0,02 =60,03 мм; dmах3 = 60,14 + 0,03 = 60,17 мм; dmах2 = 60,41 + 0,12 = 60,53 мм; dmах1 = 60,09 + 3,0 = 68,3 мм; dmах3 = 65,3 + 3,0 = 68,3 мм. Предельные значения припусков zпрmax определяем как разность наибольших предельных размеров и zпрmin — как разность наименьших предельных размеров предшествующего и выполняемого переходов: 2zпрmax4 = 60,17 — 60,03 = 0,14 мм = 140 мкм; 2zпрmax3 = 60,53—60,17 = 0,36 мм = 360 мкм; 2zпрmax2 = 61,3 — 60,53 = 0,77 мм = 770 мкм; 2zпрmax1 = 68,3 — 61,3 = 7,00 мм = 7000 мкм; 2zпрmin4 = 60,14 — 60,01 = 0,13 мм = 130 мкм; 2zпрmin3 = 60,41 — 60,14 = 0,27 мм = 270 мкм; 2zпрmin2 = 60,9 — 60,41 = 0,49 мм = 490 мкм; 2zпрmin1 = 65,3 — 60,9 = 4,4 мм = 4400 мкм. Общие припуски z0min и z0max рассчитываем так же, как и в предыдущем примере, суммируя промежуточные припуски и записывая их значения внизу соответствующих граф. Аналогично проверяется правильность произведенных расчетов и графическое расположение полей припусков и допусков, учитывая в данном случае, что построение производится на наружную, а не на внутреннюю поверхность. Величину номинального припуска в данном случае определяем с учетом несимметричного расположения поля допуска заготовки: z0ном = z0min +H3 – HД;  z0ном = 5290 +1030 – 20 = 6400мкм; dЭном = 60,01 + 6,4 =66,4 мм. На остальные обрабатываемые поверхности детали припуски и допуски принимаем по таблице (ГОСТ 7505—55) и записываем их значения в табл. 46. 46. Припуски и допуски на обрабатываемые поверхности шестерни ведущей (Рис. 181) по ГОСТ 7505—55 (размеры в мм) Поверхность | Размер | Припуск | Допуск | табличный | расчетный | 1,8 | 276,5 | 2 × 4,4 | — | +2.7 1,7 | | | | 2×3,2 | +2,0 | 2,6 | Æ  | 2 × 3,7 | — | -1,0 | | | | — | +2,0 | 3,5 3,0 | 68,5 | 2 × 3,7 | | -1,0 | | | | — | +2,0 | | Æ105-0,23 | 2 × 3,7 | — | -1,0 | | Æ | 2 × 3,7 | — | +2,0 | | | — | -1,0 | | 55,5 | 3,7 | — | +2,0 | | | | — | -1,0 | | | | | | | Чертеж заготовки (штамповки на ГКМ) шестерни ведущей показан на рис. 19. Так же, как и другие расчеты в курсовом проекте, расчет припусков удобно построить в виде расчетного формуляра, пример которого дан в приложении XIV.  Рис. 19. Заготовка шестерни ведущей (рис. 17) с начисленными припусками и допусками Наряду с необходимыми исходными данными в начале расчета приводится схема установки обрабатываемой заготовки; на ней должны быть показаны все те поверхности, для которых рассчитываются или назначаются по таблицам припуски на обработку. На схеме условными обозначениями, принятыми для технологических операционных эскизов, показывается также базирование заготовки в данной установке. Следует иметь в виду, что в один расчет можно включать только последовательно выполняемые переходы при одной и той же (неизменной)установке обрабатываемой заготовки. В том случае, если обработка даже одной поверхности производится за несколько различных установок, необходимо для каждой установки, показав ее схему, произвести самостоятельный расчет. В заголовках вертикальных граф расчетной таблицы, как показано в приведенном примере формуляра, достаточно записать только индексы рассчитываемых параметров, например zпрmax. Цифровые индексы составляющих элементов припуска по переходам, например, r1, r2 и т. д. соответствуют порядковым номерам выполняемых переходов. В том случае, когда расчет какого-то элемента, как, например, zпрmin=dmaxi-dmaxi-1 представляет несложное вычисление суммы или разности двух-трех составляющих, то в формуляре следует привести только формулу в общем виде, а расчет при наличии исходных данных, уже записанных в таблицу, для каждого из переходов в формуляре можно не производить, записывая только результаты расчета в соответствующую графу таблицы. Номинальные значения припусков рассчитываются только для сопоставления с табличными или производственными величинами. При расчете номинальных припусков значения B3, H3 заготовки берутся из таблиц соответствующих стандартов, а для штамповок рассчитываются по приводимым выше формулам. Эскиз заготовки с начисленными припусками и допусками дан в вышеприведенных расчетах и формуляре в качестве примера, который может быть использован для оформления чертежа заготовки. Так как выполнение в курсовом проекте чертежа заготовки со всеми размерами, а также припусками на обработку обязательно, то эскиз заготовки в расчетном формуляре можно не делать, а нанести все результаты аналитического и табличного расчетов припусков непосредственно на чертеж заготовки. ОФОРМЛЕНИЕ РАСЧЕТНО-ПОЯСНИТЕЛЬНОЙ ЗАПИСКИ Расчетно-пояснительная записка к курсовому проекту оформляется в соответствии с общими требованиями к текстовым документам по ГОСТ 2.105—68. Текстовую часть записки пишут чернилами на бланках формата 11 с рамками и основной надписью по ГОСТ 2.106— 68 (формы 5 и 5а). Общее содержание расчетно-пояснительной записки должно соответствовать формулировке «расчетно-пояснительная», т. е. она должна состоять из расчетов, выполненных по проекту, с необходимыми обоснованиями и пояснениями по принятым решениям. Как уже говорилось выше, расчеты в проекте целесообразно оформить на расчетных листах — формулярах. Такое выполнение расчетов позволяет выдержать наиболее целесообразную последовательность проекта, сократить время, необходимое для его выполнения, свести расчет в систему, позволяющую осуществить простую и быструю проверку его правильности. Кроме того, оформление расчетов в виде формуляров исключает излишний описательный текст, способствуя, таким образом, краткости расчетно-пояснительной записки вообще. Пояснительный и описательный материал записки может касаться таких вопросов, как обоснование выбора метода получения заготовки, выбора варианта технологического процесса, анализ технологичности конструкции обрабатываемой детали и некоторых других. Однако во всех случаях необходимо сделать выводы на основании сопоставления количественных показателей, т. е. свести рассуждения к расчетам, считая расчет главным элементом любого вопроса, поэтому пояснения к расчету должны быть по возможности краткими. Иллюстрировать изложенный материал при необходимости можно фотографиями, графиками, схемами, поясняющими и облегчающими восприятие текста. Поэтому в настоящем пособии значительнее место отводится построению таблиц и графиков, иллюстрирующих сущность тех или иных вопросов и способствующих предельно краткому их изложению в расчетно-пояснительной записке. Не допускается переписка из учебников общих определений и формулировок, например: что такое операция, переход, припуск и т. п. Таким образом, записка отражает сущность проделанной работа, дает обоснования принятым решениям, содержит необходимые расчеты, результаты которых сводятся в таблицы или графики. Расчетно-пояснительная записка начинается титульным листом, выполненным как одно целое с обложкой на чертежной бумаге по форме, приведенной в приложении XIV (повторение титульного листа не допускается). Надписи на титульном листе выполняются тушью чертежным шрифтом. Вслед за заглавным листом помещается ведомость курсового проекта, в которой перечисляются все документы, входящие в разработанный проект. Ведомость выполняется по форме 4 (ГОСТ 2.106—68). Пример заполнения ведомости курсового проекта приведен в приложении XIV. Далее, в записке помещается задание на курсовое проектирование, выданное студенту. Бланк задания — обязательный документ, на основании которого можно судить о правильности и полноте разработки вопросов, выполненных проектантом. Затем идет оглавление. В оглавлении и в самой записке должны содержаться следующие разделы. 1. Введение (1—2 страницы). В нем нужно описать: a) значение машины, в которую входит обрабатываемая деталь, для народного хозяйства СССР; б) перспективы развития данной отрасли машиностроения; в) особенности задачи, поставленной перед студентом при выполнении курсового проекта, если они имели место. В этом разделе также следует по возможности прибегнуть к графической иллюстрации таких, например, вопросов, как рост показателей развития отрасли промышленности за какой-то промежуток времени. 2. Назначение и конструкция детали. (1,5—2 страницы). Сущность и объем вопросов, которые должны быть описаны в этом разделе, изложены выше. 3. Анализ конструкции обрабатываемой детали (1—2 страницы). Этот вопрос также достаточно подробно изложен в настоящем пособии. 4. Определение т и па производства (1—2 страницы). Этот раздел также должен быть выполнен в соответствии с вышеизложенными рекомендациями. Для серийного производства рассчитывается, кроме того, размер партии. 5. Выбор заготовки (1—2 страницы). Раздел может быть выполнен отдельно от выбора варианта технологического маршрута либо как часть следующего раздела пояснительной записки. Последнее целесообразно в том случае, если эффективность технологического процесса не может быть определена без учета метода получения заготовки, т. е. припуски на обработку при различных методах получения заготовки оказывают существенное влияние на выбор варианта технологического маршрута. 6. Анализ существующего технологического процесса (1—2 страницы). Этот раздел, хотя и выделяется в самостоятельный, но может быть связан как с предыдущим, так и с последующим. Иногда дается сравнение разрабатываемого варианта технологического процесса с существующим. 7. Выбор варианта технологического маршрута и предварительный технико-экономический расчет (2—3 страницы). Роль этого раздела исключительно велика, так как здесь дается технико-экономическое обоснование выбранного варианта технологического маршрута. Следует также отметить, что для наглядного сравнения сопоставимых вариантов целесообразнее всего производить это сравнение в форме таблиц или графиков. В этом же разделе необходимо обосновать технологический процесс, т. е. высказать те соображения, которые не содержатся в технологических картах. Для каждой операции технологического процесса следует дать обоснование выбора баз, оборудования, последовательности выполнения операций, примененного инструмента и оснастки. 8. Расчет припусков (2—3 страницы). Расчет припусков производится по приведенной выше методике с обязательным графическим изображением полей общих и межоперационных припусков и допусков. Для припусков, выбранных по таблицам, следует указать их величины, поверхности, для которых они выбраны, и источники. 9. Режимы резан и я (3—4 страницы). Раздел излагается в соответствии с рекомендованными выше методиками с обязательным оформлением результатов расчетов в виде сводной таблицы. В этом же разделе под соответствующим параграфом необходимо вычислить и свести в таблицы коэффициенты загрузки оборудования, коэффициенты использования оборудования по основному времени, коэффициенты использования оборудования по мощности и значение выбранных периодов стойкости режущего инструмента. Эти данные используются затем для построения соответствующих графиков. Графики можно привести в этом же разделе расчетно-пояснительной записки. 10. Нормирование технологического процесса (1—2 страницы). Здесь приводятся только пояснения и обоснования с указанием источников для выбора составляющих норм штучного времени для операций технологического процесса. Все данные по нормированию записываются в технологические операционные карты, а также сводятся в таблицу. 11. Приспособление и режущий инструмент (2—3 страницы). По возможности следует применять универсальные и быстродействующие приспособления. В случае применения специальных приспособлений в этом разделе приводится обоснование выбора данной конструкции. Кроме того, здесь приводятся прочностные и точностные расчеты элементов, приспособления и краткое описание его работы. Для пояснения расчетов усилий зажима и точности работы приспособления целесообразно в этом разделе привести схематическое изображение рассчитываемых элементов и конструкций, например схемы передачи усилия от пневматического цилиндра до элементов, осуществляющих зажим детали, и т. п. Необходимо указать источники, из которых взяты формулы и цифровые данные. По окончании расчетов обязательно сделать выводы. Например, производя расчеты погрешностей, необходимо указать на годность или негодность приспособления и на изменения в конструкции и посадках для обеспечения требуемой точности. Расчеты режущего инструмента производятся в тех случаях, когда по условиям проектирования невозможно использовать стандартизованные или нормализованные инструменты и должен быть применен специальный инструмент. 12. Определение потребного количества оборудования и построение графи ков (2—3 страницы). Данные для определения потребного количества станков рассчитываются при нормировании технологического процесса и расчете режимов резания. В этом разделе целесообразно свести в форму таблиц все сведения, необходимые для построения графиков загрузки оборудования, использования оборудования по основному времени, использования оборудования по мощности и периодов стойкости инструмента. Графики, как уже говорилось выше, можно строить как на отдельном чертеже формата 24, так и в тексте расчетно-пояснительной записки. 13. Технико-экономический расчет (3—4 страницы). В этом разделе в сжатой форме со ссылками на источники приводятся расчеты затрат всех статен себестоимости изготовления детали по курсовому проектированию при заданной годовой программе. Методика приведена в разделе «Определение затрат по статьям себестоимости». Основные технико-экономические показатели технологического процесса в сравнении с существующим на производстве или другим его вариантом в конце этого раздела сводятся в таблицу, форма которой прилагается. В таблице указаны также источники или расчетные формулы. 14. Список использованной литературы. Список составляется в той последовательности, которая определяется ходом курсового проекта. Вслед за порядковым номером литературного источника указывается автор, затем его инициалы, наименование источника, том, город, в котором издана книга, издательство и год издания. Например: 6. Чарнко Д. В. Основы выбора технологического процесса механической обработки. М., Машгиз, 1963. Указание городов Москва и Ленинград дается сокращенно, начальными буквами (М. и Л.), остальные города указываются полным наименованием. В тексте расчетно-пояснительной записки ссылки на литературные источники следует делать в виде квадратных скобок с цифрой внутри, соответствующей номеру этого источника в списке литературы. Целесообразно раньше составлять список литературы, а затем приступать к окончательному оформлению расчетно-пояснительной записки. В списке литературы должны быть обязательно указаны те источники, которые послужили основанием для высказывания предложений по применению новых методов обработки, способов получения заготовок, прогрессивным режимам резания, новым маркам режущих инструментов и т. п. Все листы расчетно-пояснительной записки необходимо пронумеровать в специально отведенных для этого графах, в оглавлении должны быть проставлены страницы всех разделов. Пример построения оглавления и ряда формуляров расчетно-пояснительной записки приведен в приложении XIV. Приложения I. ПРИБЛИЖЕННЫЕ ФОРМУЛЫ ДЛЯ НОРМ ВРЕМЕНИ ПО ОБРАБАТЫВАЕМОЙ ПОВЕРХНОСТИ [11] Основное технологическое время Ту, мин Черновая обточка за один проход | 0,00017 dl | Чистовая обточка по 4-му классу точности | 0,00010 dl | Чистовая обточка по 3-му классу точности | 0,00017 dl | Черновая подрезка торца V 4 | 0,000037(D2 — d2) | Чистовая подрезка торца V 6 | 0,000052 (D2 — d2) | Отрезание | 0,00019D2 | Черновое и чистовое обтачнвание фасонным резцом | 0,00063 (D3 — d2) | Шлифование грубое по 4-му классу точности | 0.00007 dl | Шлифование чистовое по 3-му классу точности | 0,0001 dl | Шлифование чистовое по 2-му классу точности | 0,00015 dl | Растачивание отверстий на токарном станке | 0.000l8 dl | Сверление отверстии | 0,00052 dl | Рассверливание d = 20 — 60 | 0,0003 dl | Зенкерование | 0,00021 dl | Развертывание черновое | 0,00043 dl | Развертывание чистовое | 0,00086 dl | Внутреннее шлифование отверстий 3-го класса точности | 0,0015 dl | Внутреннее шлифование отверстий 2-го класса точности | 0,0018 dl | Черновое растачкчанне отверстии за один проход V 3 | 0.0002 dl | Черновое растачивание под развертку | 0,0003 dl | Развертывание плавающей разверткой по 3-му классу точности | 0,OO027 dl | Развертывание плавающей разверткой по 2-му классу точности | 0,00052 dl | Здесь d. — диаметр, 1 — длина обрабатываемой поверхности, D—диаметр обрабатываемого торца, D—d—разность наибольшего и наименьшего диаметров обрабатываемого торца. | | Протягивание отверстии и шпоночных канавок, | T0 = 0,0004l | где 1 — длина протяжки, мм. | | Строгание черновое на продольно-строгальных станках | T0 = 0,0000655Bl | Строгание чистовое под шлифование или шабрение | T0 =0,0000345Bl | Фрезерование черновое торцевой фрезой: | | за проход | T0 = 0,006l | чистовое | T0 = 0,004l | Фрезерование черновое цилиндрической фрезой | T0 = 0,007l | Шлифование плоскостей торцом круга | T0 = 0,0025l | Здесь В—ширина обрабачываемой поверхности, мм; | | 1 — длина обрабатываемой поверхности, мм. | | Фрезерование зубьев червячной фрезой (D = 80 — 300) | T0 = 0,0022Db | Обработка зубьев червячных колес (D = 100—400) | T0 = 0,0603D | Здесь D—диаметр зубчатого колеса, мм; | | Ь—длина зуба, мм.. | | Фрезерование шлицевых валов методом обкатки | T0 = 0,0090lz | Шлицешлифование | T0 = 0,0046lz | Здесь 1—длина шлицевого валика, млг, г — число шлицев. | | | Величина коэффициента jК Виды станков | Производство | единичное и мелкосерийное | крупносерийное | Токарные Токарно-револьверные Токарно-многорезцовые Вертикально-сверлильные Радиально-сверлильные Расточные Круглошлифовальпые Строгальные Фрезерные Зуборезные | 2,14 1,98 1,72 1,75 3,25 2,10 1,73 1,84 1.66 | 1,36 1,35 1,50 1,30 1,41 - 1,55 1,51 1.27 | 11. СРЕДНИЕ ЗНАЧЕНИЯ kM,. и a ПО ГРУППАМ ОБОРУДОВАНИЯ [39] Наименование группы оборудования | Характеристика станка | *м | а | | | | | | Высота центров, мм: | | Токарно-винторезные | <200 200—300 300—400 400—500 500—600 | 0,9 1,3 1,6 3,0 3,5 | 0,23 0,26 0,30 0,47 0,47 | | Диаметр планшайбы, мм: | | Токарно-карусельные | <1120 1120—1400 1400—2000 2000—2800 2800—4000 | 2,7 3,6 4,9 6,4 13,4 | 0,40 0,41 0,57 0,65 0,47 | | Высота центров, мм | | Токарные многорезцовые полуавтоматы | <150 150—200 200—250 | 1,4 1,8 2,8 | 0,37 0,39 0,44 | | | | | | | | | | Диаметр обрабатываемых изделий, мм | Токарно-револьверные | 18—36 36-65 >65 в патроне 500 | 0,9 1,3 1,5 0,9 | 0,32 0,34 0,35 0,46 | Наибольший диаметр сверла, мм: | Вертикально-сверлильные | <12 12-35 35-70 >70 | 0,5 0,7 1,2 0,7 | 0,19 0,22 0,30 0,36 | Наибольший диаметр сверла, мм: | Радиально-сверлильные | <35 35—75 75—100 >100 | 1,4 1.6 2.2 3,3 | 0,29 0,34 0,42 0,47 | Диаметр выдвижного шпинделя, мм | Горизонтально-расточные | <80 80-110 110—150 150—175 175—200 | 1,7 3,1 4,4 8,5 13,6 | 0,42 0,56 0,65 0,70 0,72 | | Высота центров | | Круглошлифовальные | <100 100—200 200—275 275—370 >370 | 2,5 1,8 2,4 3,2 6,5 | 0,25 0,36 0,37 0,48 0,50 | Размеры горизонтального стола, мм: | Плоскошлифовальные | < 1000Х300 1000х300—2000х400 2000х400—2000х800 | 1,4 1,6 3.4 | 0,24 0,25 0,40 | | Диаметр изделия, мм | | Зубофрезерные | 750-1250 | 2,4 | 0,26 | | Диаметр изделия,мм | | | Зубодолбежные | <500 500-1250 | 1,7 2,7 | 0,25 0,40 | | | | | | | | | | | Диаметр изделия, мм: | | | Зубошлифовальные | <320 700—800 >800 | 2,6 3.6 7.8 | 0,60 0,66 0,77 | | Поверхность стола, мм: | | Горизонтально-фрезерные | < 1000х250 1000Х250—1600Х400 | 1,1 1,5 | 0,26 0,29 | | Поверхность стола, мм: | | Вертикально-фрезерные | < 1000х250 1000х250—1250х300 1250Х300—1600Х400 1600Х400—2000х800 >2000Х800 | 1,1 1,5 1,8 1,9 5,5 | 0,23 0,28 0,31 0,31 0,57 | | Поверхность стола, мм: | | Универсально-фрезерные | < 1000Х250 1000Х250—1200Х300 1250Х300—1600Х400 | 1,1 1,2 1,5 | 0,29 0,30 0,30 | | Поверхность стола, mm! | | Продольно-строгальные | (3000х900)—(4000 х 1250) 4000 X 1250—6000Х2500 >8000Х2400 | 5,0 6,3 9,0 | 0,44 0,47 0,65 | | Наибольший ход ползуна, mm | | Поперечно-строгальные | <700 700-900 | 1.1 1.3 | 0.33 0,34 | | Ход долбяка, мм: | | Долбежные | <200 200—320 | 1,1 1,4 | 0,37 0,44 | | Максимальное усилие. Т; | | Горизонтально-протяжные | <20 20—40 | 3,0 3,6 | 0,20 0,24 | | Масса падающих частей, кг | | Молоты пневматические ковочные | <150 150—400 750—1000 >1500 | 1,5 2,7 6,0 21,7 | 0,39 0,34 0,32 0,21 | | | | | | Максимальное усилие, Т: | | Прессы механические | <25 25—50 50—100 100—160 160—250 400—630 2000—2500 | 0,5 0,7 1,0 2.5 3,5 4,2 17,7 | 0,51 0,53 0,53 0,53 0,56 0,64 0,70 | | Максимальное усилие, Т: | | Горизонтально-ковочные машины | <100 100—250 250—630 630—800 | 2,1 4,4 6,3 9,6 | 0,4 0,51 0,70 0,76 | Толщина разрезаемого листа, мм: | Гильотинные ножницы | <3 »6,3 » 10 »16 | 0,6 1.1 2,2 2,9 | 0,52 0,54 0,61 0.63 | III. ТАБЛИЦЫ ЭКОНОМИЧЕСКОЙ ТОЧНОСТИ ОБРАБОТКИ НА МЕТАЛЛОРЕЖУЩИХ СТАНКАХ III. 1. Средняя точность и чистота обработки наружных поверхностей тел вращения Способ обработки | Класс точности | Класс чистоты | Обтачивание однократное | | | Обтачивание предварительное | | | Обтачивание чистовое | 4—За | | Обтачивание однократное | | | Шлифование однократное | За-3 | 6-7 . | Обтачивание предварительное | | | Обтачивание чистовое | 3—2 | | Шлифование однократное | | | Обтачивание предварительное | | | Обтачивание чистовое | 2а-2 | | Обтачивание тонкое | | | Обтачивание однократное | Шлифование предварительное | 2а-2 | | Обтачивание предварительное | | | | | | Обтачивание чистовое | | | Шлифование предварительное | | | Шлифование чистовое | | | Способ обработки | Класс точности | Кллсс чистоты | Обтачивание предварительное | | ©2015 www.megapredmet.ru Все права принадлежат авторам размещенных материалов. |