ПОЗНАВАТЕЛЬНОЕ Сила воли ведет к действию, а позитивные действия формируют позитивное отношение Как определить диапазон голоса - ваш вокал
Игровые автоматы с быстрым выводом Как цель узнает о ваших желаниях прежде, чем вы начнете действовать. Как компании прогнозируют привычки и манипулируют ими Целительная привычка Как самому избавиться от обидчивости Противоречивые взгляды на качества, присущие мужчинам Тренинг уверенности в себе Вкуснейший "Салат из свеклы с чесноком" Натюрморт и его изобразительные возможности Применение, как принимать мумие? Мумие для волос, лица, при переломах, при кровотечении и т.д. Как научиться брать на себя ответственность Зачем нужны границы в отношениях с детьми? Световозвращающие элементы на детской одежде Как победить свой возраст? Восемь уникальных способов, которые помогут достичь долголетия Как слышать голос Бога Классификация ожирения по ИМТ (ВОЗ) Глава 3. Завет мужчины с женщиной 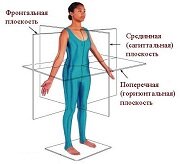
Оси и плоскости тела человека - Тело человека состоит из определенных топографических частей и участков, в которых расположены органы, мышцы, сосуды, нервы и т.д. Отёска стен и прирубка косяков - Когда на доме не достаёт окон и дверей, красивое высокое крыльцо ещё только в воображении, приходится подниматься с улицы в дом по трапу. Дифференциальные уравнения второго порядка (модель рынка с прогнозируемыми ценами) - В простых моделях рынка спрос и предложение обычно полагают зависящими только от текущей цены на товар. | АНАЛИЗ СУЩЕСТВУЮЩЕГО ТЕХНОЛОГИЧЕСКОГО ПРОЦЕССА Работа по подготовке к выполнению курсового проекта начинается во время прохождения студентами производственной технологической практики, когда изучаются действующие на производстве технологические процессы, оборудование, оснастка, экономические, организационные вопросы и т. д. При изучении существующих процессов ставятся задачи их глубокого анализа, так как без него невозможно оценить технологический процесс и, следовательно, высказать какие-то предложения по его улучшению и модернизации. Анализ существующего технологического процесса должен быть проведен с точки зрения обеспечения заданного качества продукции. Иными словами, при анализе технологического процесса следует выяснить, правильно ли он составлен для обеспечения требований чертежа и соблюдаются ли все требования технологического процесса в цехе. Для выполнения этой работы в определенной последовательности можно рекомендовать следующий примерный перечень вопросов: а) рациональность метода получения заготовки для данного масштаба производства; б) соответствие реальной заготовки чертежу в отношении фактических припусков на обработку и выполнения прочих технических 1ребован11Й; в) правильность выбора черновых, чистовых и промежуточных баз на операциях технологического процесса, соблюдение принципа единства технологических баз; г) правильность установки последовательности операций процесса для достижения заданной точности детали; д) соответствие параметров установленного оборудования требованиям данной операции; е) соответствие режимов резания прогрессивным; ж) степень оснащенности операций; з) применяемость высокопроизводительного режущего инструмента и новых марок материалов его режущей части; и) соблюдение технологического процесса на операциях и качество обработки деталей; к) степень концентрации операций технологического процесса и т. д. Качество обработки деталей на каждой операции оценивается на основании данных о браке. Первоначальным источником о количестве брака по операциям могут служить данные, полученныеизотдела технического контроля. Однако для большей объективности следует руководствоваться личными наблюдениями и результатами измерений важнейших параметров на операциях технологического процесса. Следует также проанализировать причины появления брада и обратить внимание на реальное состояние оборудования в отношении возможности обеспечения заданной точности на операциях. Правильность разработки технологического процесса и выбора оборудования целесообразно оценить с помощью таких количественных показателей, как коэффициент загрузки оборудования, коэффициент использования оборудования по основному времени и по мощности. Способ определения этих коэффициентов дан & разделе «Определение потребного количества оборудования и построение графиков». Экономические показатели существующего технологического процесса по операциям на данном этапе проектирования сводятся к определению технологической себестоимости, так как сопоставление вариантов предлагаемого процесса с существующим достаточно произвести на основании этого показателя. Результаты анализа существующего технологического процесса должны быть детально изложены в соответствующем разделе расчетно-пояснительной записки, так как именно анализ может дать предпосылки для разработки варианта процесса. Поэтому совершенно недопустимо заменять анализ технологического процесса простым его описанием или переписыванием сведений из технологических карт. Анализ целесообразно выполнять со ссылками на технологические карты. Следует заметить, что при разработке курсового проекта перед студентом не ставится задача коренной переработки существующей технологии, если это не диктуется соответствующими особыми условиями , например резким увеличением производственной программы, связанным с изменением типа производства и т. п. В большинстве случаев оказывается вполне достаточным рассмотреть варианты по изменению нескольких, а иногда двух-трех технологических операций и сопоставить их по методике, предлагаемой в следующем разделе. Расчет припусков При выполнении курсового проекта расчет припусков на механическую обработку производится расчетно-аналитическим методом и по таблицам. Расчет припусков и определение их величин по таблицам могут производиться только после выбора оптимального для данных условий технологического маршрута и выбора метода получения заготовки. На основании результатов определения припусков расчетно-аналитическим методом для рассчитанных поверхностей в конце этого раздела приводится графическая схема расположения общих и межоперационных припусков и допусков (схема приведена на рис. 14). Для удобства расчет следует производить в виде табл. 43. Данные таблицы используются непосредственно для построения графической схемы, а также для быстрой проверки правильности произведенных расчетов. Рис. 12. Схема для определения минимального и максимального промежуточных припусков при обработке на настроенном станке | Рис.13. Схема расположения промежуточных припусков | В основном, за редким исключением, при разработке курсовых проектов применяется метод автоматического получения размеров, т. е. обработки на предварительно настроенных станках. Так как в этом случае заготовки поступают на обработку с колебанием размеров поверхностей, подлежащих обработке в пределах допуска, то и действительные припуски на обработку для этих поверхностей на данном переходе будут иметь различные величины. Колебание размеров, получаемых при обработке, происходит по причине нежесткости технологической системы, т. е. различной ее податливости в результате колебаний припуска на обработку. Таким образом, как видно из рис. 12, у заготовки с наименьшим предельным размером amin при обработке в размер b наименьший припуск на обработку — zmin, а у заготовки с наибольшим предельным размером amax наибольший припуск на обработку — zi max. Расположение полей припусков и межоперационных допусков на двух смежных переходах обработки элементарной поверхности при обработке на предварительно настроенном станке можно графически изобразить, как показано на рис. 13, а. Иначе выглядит расположение минимального и максимального припусков в том случае, когда обработка производится по методу пробных проходов. Этот случай показан на рис. 13, б. Так же выглядит схема расположения полей припусков при последовательном приближении к заданному размеру, например при многопроходной обработке (шлифование, хонингование и т. п.). При этом из-за сравнительно небольших усилий резания упругие отжатия в технологической системе почти отсутствуют. Этому способствует также стремление рабочего получить наибольший предельный размер по проходному калибру. Порядок расчета припусков на обработку и предельных размеров по технологическим переходам приведен в табл. 25. 25. Порядок расчета припусков на обработку и предельных размеров по технологическим переходам [3] Для наружных поверхностей | Для внутренних поверхностей | | | 1. Пользуясь рабочим чертежом детали и картой технологического процесса механической обработки, записать в расчетную карту обрабатываемые элементарные поверхности заготовки и технологические переходы обработки в порядке последовательности их выполнения по каждой элементарной поверхности от черновой заготовки до окончательной обработки 2. Записать значения RZ, Т, r, e и d 3. Определить расчетные величины минимальных припусков на обработку по всем технологическим переходам 4. Записать для конечного перехода в графу «Расчетный размер» наименьший предельный размер детали по чертежу | 4. Записать для конечного перехода в графу «Расчетный размер» наибольший предельный размер детали по чертежу | 5. Для перехода, предшествующего конечному, определить расчетный размер прибавлением к наименьшему предельному размеру по чертежу расчетного припуска zmin | 5. Для перехода, предшествующего конечному, определить расчетный размер вычитанием из наибольшего предельного размера по чертежу расчетного припуска zmin | 6. Последовательно определить расчетные размеры для каждого предшествующего перехода прибавлением к расчетному размеру следующего за ним смежного перехода расчетного припуска zmin | 6. Последовательно определить расчетные размеры для каждого предшествующего перехода вычитанием из расчетного размера следующего за ним смежного перехода расчетного припуска zmin | 7. Записать наименьшие предельные размеры по всем технологическим переходам, округляя их увеличением расчетных размеров; округление производить до того же знака десятичной дроби, с каким дан допуск на размер для каждого перехода | 7. Записать наибольшие предельные размеры по всем технологическим переходам, округляя их уменьшением расчетных размеров; округление производить до того же знака десятичной дроби, с каким дан допуск на размер для каждого перехода | 8. Определить наибольшие предельные размеры прибавлением допуска к округленному наименьшему предельному размеру | 8. Определить наименьшие предельные размеры путем вычитания допуска из округленного наибольшего предельного размера | 9. Записать предельные значения припусков zmax как разность наибольших предельных размеров и zmin как разность наименьших предельных размеров предшествующего и выполняемого переходов | 9. Записать предельные значения припусков zmax как разность наименьших предельных размеров и zmin как разность наибольших предельных размеров выполняемого и пре; шествующего переходов | 10. Определить общие припуски zOmax и zOmin, суммируя промежуточные припуски на обработку. | 11. Проверить правильность произведенных расчетов по формулам:  | 12. Определить общий номинальный припуск по формулам:  | 12. Определить общий номинальный припуск по формулам:  | Примечания: 1. В связи с разнохарактерностью действия при расчете размеров для наружных и внутренних поверхностей рекомендуется во избежание от бок группировать в расчетной карте наружные и внутренние поверхности, а не записывать их вперемежку. 2. При обработке взаимосвязанных плоских поверхностей от переменных баз рекомендуется строить размерные цепи, определяющие взаимосвязь обрабатываемо поверхности с измерительной базой. 3. В ряде случаев целесообразно по соображениям режимных условий обработки припуск, рассчитанный на черновую обработку, распределять между черновой и получистовой обработкой; при этом 60—70% расчетного припуска рекомендуется снима1 при черновой обработке и 30—40% — при получистовой обработке. 4. Поминальный припуск определяется лишь в целях сопоставления с табличными или производственными данными. Для удобства все аналитические формулы определения расчетных величин минимальных припусков zmin для различных видов механической обработки и различных поверхностей сведены в табл. 26. С это же целью систематизированы и приводятся в виде таблиц значения составляющих, входящих в формулы для определения минимального припуска. Так, значения Rz, и Т для основных видов заготовок различных методов механической обработки заготовок из прокат; штамповок и отливок, а также для наиболее распространенных виде обработки отверстий приводятся в табл. 27—30. В табл. 31 даны расчетные формулы для определения суммарно! значения пространственных отклонений, т. е. отклонений от правильно геометрической формы поверхностей и их взаимного расположения для различных видов заготовок при их обработке на первой операции, с учетом методов базирования заготовок, влияющих на величину пространственного отклонения. Для наглядного представления характера и составляющих пространственного отклонения таблица иллюстрируется эскизами. К таблице целесообразно сделать следующие пояснения. 26. Расчетные формулы для определения величины припуска на обработку Вид обработки | Расчетная формула | Последовательная обработка противоположных или отдельно расположенных поверхностей |  | Параллельная обработка противоположных плоскостей | | Обработка наружных или внутренних поверхностей вращения | | Обтачивание цилиндрической поверхности заготовки, установленной в центрах; бесцентровое шлифование |  | Развертывание плавающей разверткой, протягивание отверстий |  | Суперфиниш, полирование и раскатка (обкатка) |  | Обработка лезвийным или абразивным инструментом без выдерживания раз мера (как чисто) черной поверхности |  | Шлифование после термообработки; | | а) при наличии ei |  |  | б) при отсутствии ei |  | |  | Примечание: при при при при  27. Качество поверхности различных видов заготовок Вид заготовки | Класс точности | Rz | T | мкм | Отливки в земляные формы I класса | 7—9 | | наибольший габаритный размер отливки, мм: £ 1250 | | | 1250—3150 | | | то же II класса | 8—9 | | наибольший габаритный размер отливки, мм: £ 1250 | | | 1250—3150 | | | Отливки в кокиль | 5-7 | | | Литье в оболочковые формы | 5-7 | | | Литье под давлением | 3-5 | | | Литье по выплавляемым моделям | 2-5 | | | Масса, кг: | | | | £ 0,25 | | | | 0,25 - 2,5 | | | | 2,5-25 | | | | 25 – 100 | | | | 100 – 200 | | | | Прокат | | | | горячекатаный диаметр, мм | | | | 5 – 25 | | | | 26-75 | | | | 80 – 150 | | | | 160 – 250 | | | | калиброванный гладкотянутый | 2а – 5 | | | калиброванный шлифованный | 2 – 3 | | | Примечание. Для отливок в земляные формы указано суммарное значение Rz + Т, 28. Качество торцевой поверхности после резки заготовок из горячекатаного проката (размены в мм) Способ резки | Диаметр отрезаемой заготовки D | Допускаемое отклонение размеров по длине заготовки | R,+T | Отклонение от перпендикулярности торца к оси заготовки | По упору на ножницах, дисковыми пилами и приводными ножовками | 5-25 | ±1,0 | | | 26—75 80—150 | ±1,3 ±1,8 | 0,3 | 0,01D | | >150 | ±2,3 | | | На прессах и дисковыми фрезами на отрезных станках | 5—25 | ±0,3 | 0,2 | 0,0007D | 26—75 | ±0,4 | | | Отрезными резцами на станках токарного типа | 5—25 | ±0,25 | | | 26—75 80—150 | ±0,35 ±0,40 | 0,2 | 0,045D | | 160—250 | ±0,50 | | | Примечание. При резке на ножницах получаются вмятина и скос; вел чина вмятины в направлении, перпендикулярном к поверхности среза, достигает 0,2D, а величина скоса по торцу 3°. Величину вмятины и скоса необходимо учитывать при последующей обработке отрезанной заготовки соответственно по диаметру и торцу. 29. Параметры, достигаемые после механической обработки наружных поверхностей Вид обработки | Класс чистоты | RZ | Т | мкм | Обдирочная обработка лезвийным инструментом отливок II класса, горячего проката обычной точности, нежестких валов, поковок с большими припусками и т. п. | 2—3 | | | Черновая обработка лезвийным инструментом заготовок всех видов | 3-4 | | | Чистовая обработка лезвийным инструментом и однократная обработка заготовок с малыми припусками | 4-5 | | | | | | | | | Чистовое торцевое фрезерование | 5-6 | | | Протягивание наружное | 6—7 | | | Тонкая обработка лезвийными инструментами | 7—9 | | | Шлифование: | | | | предварительное | | | | чистовое | 7-8 | | | Бесцентровое шлифование калиброванного проката 3—За классов точности: | | | | | | | До термообработки | | | | после термообработки | 8—10 | 3—0,8 | | 30. Параметры, достигаемые после механической обработки отверстий Вид обработки | Класс чистоты | RZ | Т | мкм | Сверление спиральными сверлами | 3-4 | | | Глубокое сверление | | | | Зенкерование черновое | | | | » чистовое | 4-5 | | | Растачивание черновое | | | | » чистовое | | | | Развертывание нормальное | | | | » точное | | | | » тонкое | | | - | Протягивание | | | | Калибрование шариком или оправкой | | 0,6 | | Примечание. Виды развертывания (нормальное, точное и тонкое) определяются допусками на диаметральные размеры разверток. 31. Суммарное значение пространственных отклонений для различных видов заготовок и механической обработки Тип детали и метод базирования | Эскиз | Расчетные формулы | 1 Литые заготовки | Корпусные детали, по отверстиям с параллельными осями и перпендикулярной к ним плоскости |  |  | То же, по плоскости, противоположной обрабатываемой |  |  | Детали — тела вращения, в самоцентрирующих патронах по наружному диаметру с прижимом к торцевой поверхности |  |  | 2. Штампованные заготовки | Стержневые детали (валы ступенчатые, рычаги и т. п.) с базированием по крайней ступени (поверхности) |  |  | Стержневые детали при обработке в центрах |  | при  | Детали типа дисков с прошиваемым центральным отверстием (шестерни, диски и т. п.) с установкой по наружному диаметру и торцу |  | 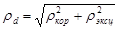 | То же, при обработке торцевых поверхностей |  |  | III. Заготовки из сортового поката | при консольном закреплении в самоцентрирующих патронах |  |  | При обработке в центрах |  | при  | IV Зацентровка заготовок | При установке в самоцентрирующих зажимных устройствах |  |  | При установке на призмах с односторонним прижимом |  | (при a= 90o) (при a= 120o) | V. Сверление заготовок | Детали всех типов, при обработке отверстия в неподвижной детали |  |  | Для литых заготовок при обработке плоской поверхности корпусной детали с отверстиями, оси которых параллельны обрабатываемой поверхности, существенное значение приобретает способ базирования этой детали на первой операции. Если деталь базируется на отверстия и перпендикулярную к ним поверхность, то суммарное пространственное отклонение складывается из величины коробления обрабатываемой поверхности и погрешности расположения базовых отверстий относительно той же обрабатываемой поверхности, т. е. смещения этих отверстий к наружной поверхности отливки. Смещение в данном случае обусловлено неточностью расположения стержня к наружной поверхности и регламентируется допуском на размер от обрабатываемой поверхности до оси базовых отверстий (А±d). На эскизе в таблице векторы коробления и смещения базовые отверстий по отношению к направлению выдерживаемого размера— коллинеарны и для определения суммарного пространственного отклонения можно принять алгебраическую сумму составляющих rкор и rсм, однако эта сумма является крайним случаем, поэтому для получения значений с большей вероятностью, учитывая нормальный закон распределения действительных размеров, следует производить геометрическое сложение векторных составляющих rкор и rсм. При установке деталей на плоскость, противолежащую и параллельную обрабатываемой, суммарное значение пространственных отклонений обрабатываемой поверхности выражается величиной се коробления. Общая величина коробления поверхности отливки определяется как произведение удельной кривизны на наибольший размер обрабатываемой поверхности в направлении обработки. Для литых деталей типа тел вращения при обработке участков наружной поверхности и базировании по наружной поверхности пространственное отклонение — овальность— выражается произведением удельной кривизны на соответствующий диаметр отливки. Если базирование при обработке наружной поверхности осуществляется по внутреннему диаметру, то для суммарного значения пространственного отклонения следует, так же как и для коробчатых деталей, учитывать смещение стержня отливки относительно наружной поверхности. Величину смещения можно принимать равной допуску на толщину стенки отливки. Так как направление векторов коробления и смещения неопределенны друг относительно друга, то производится геометрическое сложение векторов. Значения удельной кривизны заготовок (коробления) приведены в табл. 32. Для двух последних случаев, так же как и для корпусных деталей, базируемых по отверстиям, величину удельного коробления следует принимать как для корпусов. При работке торцевых поверхностей отливок тел вращения пространственное отклонение обрабатываемой поверхности выражается в виде коробления и определяется так же, как произведение удельной кривизны на диаметр обрабатываемой поверхности. Для штампованных заготовок (при обработке цилиндрических поверхностей деталей типа ступенчатых валов и консольном их закреплении по крайней ступени) суммарное значение пространственных отклонений выражается в виде коробления детали и смещения одних участков поверхностей относительно других. Это смещение обусловлено несовпадением верхней и нижней частей штампов при штамповке заготовок поперек оси, а также несовпадением полуматриц в горизонтально-ковочных машинах и, наконец, смещением штампуемой части заготовки относительно стержня исходного материала. В табл. 30 приводятся данные по общей или наибольшей кривизне штампованных заготовок, которую следует принимать в расчет при консольном закреплении заготовок. При обработке штампованных заготовок в центрах для расчетов кривизны или стрелы прогиба в обрабатываемом сечении следует брать произведение удельной кривизны после правки или термообработки па расстояние от обрабатываемого сечения до ближайшей опоры. В этом случае следует, кроме вышеприведенных факторов, учитывать радиальное биение обрабатываемой поверхности в результате погрешности зацентровки. Способ определения погрешности зацентровки приводится ниже. Так как векторы всех перечисленных погрешностей имеют неопределенное положение в пространстве относительно оси обрабатываемой детали, следует определять их геометрическую сумму. Для заготовок типа дисков с прошиваемыми при штамповке центральными отверстиями (зубчатые колеса, фланцы и т. п.) суммарное значение пространственных отклонений (при базировании детали на первой операции по наружному диаметру) складывается из смещения частей штампов, формирующих заготовку по обе стороны разъема, и эксцентричности прошитого центрального отверстия по отношению к наружному контуру заготовки. Величины погрешностей заготовок по эксцентричности приводятся в табл. 33, а по смещению в табл. 34. Так же, как и в предыдущем случае из-за неопределенного положения в пространстве векторов погрешностей, суммарное пространственное отклонение определяется геометрическим сложением. 32. Удельная кривизна заготовок Д„ в мкм на 1 мм длины Материал и состояние | Диаметр заготовки, мм | 5—25 | 25—50 | 60—75 | 75—120 | 120—150 | > 150 | 1. Прокат калиброванный: | | 2-й класс точности | 0,50 | 0,50 | | | | | 3-й » » | | 0,75 | 0,5 | | | | За—4-й » | | | | | | | 5-й » » | | | | | | | Прокат калиброванный после термообработки | | 1,3 | 0,6 | | | | Горячекатаный прокат: | | после правки на прессе | 0,15 | 0,12 | 0,10 | 0,08 | 0,06 | 0,05 | после термообработки | 2,0 | 1,3 | | 0,06 | 0,3 | 2. Штампованные заготовки: | | после правки | 2,0 | 1,5 | 1,0 | | после термообработки | 1,0 | 0,8 | 0,7 | 0,6 | 0,5 | | 3. Отливки | | | | | | | плиты | | | 2—3 | | | корпуса | | | 0,7—1 | | | Примечания: I. Общая кривизна прутка не должна превышать произведения допускаемой удельной кривизны на длину прутка. 2. Кривизну отрезанной заготовки определяют в зависимости от способа базирования при обработке (см. табл. 31). 3. При термообработке проката т. в: ч. табличные значения принимать с коэффициентом 0,5. 4. Для ступенчатых валов средний диаметр  где d1, d2… dn—диаметры ступеней; l1, l2… ln —длины ступеней; l— общая длина вала. 5. Для стержневых деталей типа рычагов и пластин dср рассчитывают по среднему сечению стержня. 33. Погрешности штампованных заготовок по эксцентричности rэксц и короблению rкор получаемых на прессах и ГКМ, мм Толщина, (высота) длина или ширина штампованных заготовок, мм | По эксцентричности отверстий для группы точности | По кривизне (стреле прогиба) и короблению для группы точности | | | | | | | < 50 | 0,5 | 0,8 | 1,0 | 0,25 | 0,5 | 0,5 | БО—120 | 0,63 | 1,4 | 1,5 | 0,25 | 0,5 | 0,5 | 120—180 | 0,8 | 2,0 | 2,5 | 0,32 | 0,5 | 0,7 | 180—260 | 1,0 | 2,8 | 3,5 | 0,32 | 0,6 | 0,9 | 260—360 | 1,5 | 3,2 | 4,5 | 0,4 | 0,7 | 1,0 | 360—500 | 2,5 | 3,6 | 5,5 | 0,5 | 0,8 | 1.1 | | | | | | | | | 34. Погрешности заготовок, штампованных на прессах и ГКМ, по смещению rсм, мм Масса заготовок, кг | Для групп точности | | | | <0,25 | 0,2 | 0,3 | 0,5 | 0,25—0,63 | 0,25 | 0,4 | 0,6 | 0,63—1,6 | 0,3 | 0,5 | 0,7 | 1,6—2,5 | 0,35 | 0,6 | 0,8 | 2,5—4,0 | 0,4 | 0,7 | 0,9 | 4,0—6,3 | 0,5 | 0,8 | 1,0 | 6,3—10,0 | 0,6 | 0,9 | 1,2 | 10,0—16.0 | 0,6 | 1,0 | 1,3 | 16,0—25,0 | 0,7 | 1,1 | 1,4 | 25,0—40,0 | 0,7 | 1,2 | 1,6 | 35. Удельный увод DК и смещение С0 оси отверстий при сверлении Диаметр отверстия, мм | Сверление спиральными сверлами | Глубокое сверление | DК, мкм/мм | С0, мкм | DК, мкм/мм | С0, мкм | 3—6 | 2,1 | | 1,6 | | 6—10 | 1,7 | | 1,3 | | 10—18 | 1,3 | | 1,0 | | 18—30 | 0,9 | | 0,7 | | 30—50 | 0,7 | | | | При обработке торцевых поверхностей штампованных заготовок в качестве пространственных отклонений учитывается коробление обрабатываемой поверхности. Оно определяется, как и для литых заготовок, произведением удельной кривизны (берется из табл. 32 для штампованных заготовок после правки) на диаметр обрабатываемой поверхности. Для заготовок из сортового проката определение суммарного значения пространственных отклонений производится аналогично штампованным заготовкам типа валов в зависимости от способа базирования. При консольном закреплении в расчет принимается только кривизна в обрабатываемом сечении, а при обработке в центрах в векторную сумму включается погрешность зацентровки. Кривизна в обрабатываемом сечении определяется на основана удельной кривизны (табл. 32) с учетом правки или термической обработки в соответствии с состоянием заготовки. Погрешность зацентровки заготовок из сортового проката, а также штампованных стержневых заготовок возникает вследствие погрешности базирования на этой операции приводит к радиальному биению наружной поверхности заготовки относительно оси центровых отверстий. При использовании на операции зацентровки для закрепления заготовок самоцентрирующих зажимных устройств допуск на наружный диаметр не оказывает влияния на погрешность зацентровки, которая в этом случае определяется погрешностью настройки центре вального станка (0,25 мм). При установке деталей на призму с односторонним прижимом погрешность зацентровки, кроме того, зависит от допуска на наружный диаметр заготовки и угла призмы. Для определения суммарного значения погрешности зацентровки следую брать геометрическую сумму указанных составляющих. Обработка отверстий в неподвижной детали сверлением характеризуется в отношении пространственных отклонена смещением отверстия и уводом — искривлением —его оси вследствие нежесткости сверл. Суммарное пространственное отклонение равно векторной сумме этих составляющих, величины которых приведены в табл. 35. Остаточные пространственные отклонения и на обработанных поверхностях, имевших исходные отклонения, являются следствием копирования погрешностей при обработке. Величина этих отклонений зависит как от режимных условий обработки так и от параметров, характеризующих жесткость технологической системы и механические свойства обрабатываемого материала. При выполнении курсового проекта для определения промежуточных значений припусков на механическую обработку можно с достаточной для практических целей точностью воспользоваться приведенной ниже эмпирической формулой (30) где kу — коэффициент уточнения формы. Значения коэффициента уточнения для различных видов заготовок и методов обработки можно принять следующими. Однократное и черновое точение штампованных заготовок, заготовок из горячекатаного проката, предварительное шлифование проката За и 4-го классов точности .................................................................................................. 0,06 Получистовая обработка заготовок из проката, штампованных заготовок, рассверливание отверстий, смещение оси отверстия после черновой обработки 0,05 Чистовое точение заготовок из сортового проката обыкновенного качества, штампованных заготовок, после первого технологического перехода обработки литых заготовок, после чистового шлифования прока га За и 4-го классов точности 0,04 Двукратное обтачивание калиброванного проката или двукратное шлифование заготовок после токарной обработки..................................................... 0,02 Получистовая обработка (зенкерование и черновое развертывание отверстий).................................................................................................................. 0,005 Чистовая обработка — развертывание отверстий........................... 0,002 При обработке торцевых поверхностей штампованных заготовок с центральным отверстием остаточную величину пространственного отклонения (коробления) можно определять: после черновой обработки (31) после получистовой обработки (32) после чистовой обработки (33) где R и r — радиусы наружной поверхности и отверстия (см. табл. 31). Погрешность установки Су на выполняемом переходе при определении промежуточного припуска характеризуется величиной смещения обрабатываемой поверхности, которое должно компенсироваться дополнительной составляющей промежуточного припуска. (34) где eб — погрешность базирования; eз — погрешность закрепления; eпр — погрешность положения заготовки. Все составляющие представляют поля рассеивания случайных величин, поэтому суммируются в общем случае по правилу геометрического сложения. Погрешность базирования eб, имеет место при несовмещении установочной и измерительной баз и зависит также от допуска и погрешности формы базовых поверхностей. В табл. 36 приводятся формулы для определения погрешности базирования при обработке заготовок в приспособлениях. Погрешность закрепления eз возникает в результате смещения обрабатываемых поверхностей заготовок от действия зажимной силы. Это смещение может быть учтено настройкой станка, если оно и велико, но постоянно по величине. В ряде случаев, особенно, когда применяются пневматические, гидравлические, электромеханические и другие зажимные устройства, обеспечивающие постоянство усилий зажима, погрешность закрепления можно исключить из расчетов. Погрешность положения заготовки eпр является следствием неточности изготовления станочного приспособления и износа его установочных элементов, а также погрешности установки самого приспособления на станке. Сюда относится также погрешность индексации — поворота зажимных устройств при обработке заготовок на многопозиционных станках, которая в большинстве случаев принимается равной 0,05 мм. За исключением последней составляющей элементы погрешности положения заготовки часто затруднительно выявить как самостоятельные значения, поэтому их учитывают входящими в погрешность закрепления. С учетом сказанного, для однопозиционной обработки формула (34) примет вид (35) Если векторы es и ey коллинеарны, как это имеет место при обработке плоских поверхностей, параллельных установочной базе, то ey =es +eз (36) Значения погрешностей закрепления для различных видов обработки в зависимости от обрабатываемого материала и технологической оснастки приводятся в табл. 37—40. Определение значений допусков на заготовки производится по соответствующим для каждого метода ГОСТам, указанным в разделе «Выбор заготовки» настоящего пособия. Для первого технологического перехода при обработке черных заготовок всех видов и при выдерживании размера от черной базы допуск d следует принимать не табличный, а определять по формуле (37) где dзаг — допуск на размер черной заготовки; dобр — допуск по классу точности, указанному в таблице для соответствующего метода обработки. При определении допусков штампованных заготовок следует учитывать следующие факторы: недоштамповку Нед, допускаемый износ окончательного ручья штампа Иш, колебания усадки заготовки по температурному интервалу штамповки Ку и элемент допуска, не зависящий от износа штампов и недоштамповки Нез. Размеры штампованных заготовок (рис. 14) по-разному зависят от перечисленных факторов. Допуски на размеры, зависящие от недоштамповки или двустороннего износа штампов, определяются как (размеры А на рис. 14) d = Нед + Иш + Ку (38) при этом верхнее отклонение (плюс) (39) нижнее отклонение (минус) (40) Допуски на размеры углублений и внутренних поверхностей (размеры D и А) также рассчитываются по формуле (38), при этом верхнее отклонение (плюс) (41) а нижнее отклонение (минус) (42) Допуски на наружные размеры поверхностей, зависящие от одностороннего износа штампов (параллельные плоскости разъема – размеры Б), (43) При этом верхнее отклонение (плюс) , (44) нижнее отклонение (минус) , (45) Для размеров внутренних поверхностей в этом случае (размеры Б} верхнее отклонение (плюс) . (46) нижнее отклонение (минус) . (47) Допуски на размеры, определяющие расстояние между осями бобышек или других элементов, не выходящих к периферии заготовки, не зависящие от износа ручьев штампов (размеры В), и на размеры, зависящие от одностороннего равномерного износа ручьев (размеры Г), d= Нез + Ку (48) При этом верхнее (плюс) и нижнее (минус) отклонения равны . (49) Элементы допусков по недоштамповке Нед, износу штампов Иш и не зависящие от износа штампов Нез приводятся в табл. 41 и 42. Базирование | Схема установки | Погрешность базирования e для размеров | | | | По центровым отверстиям: на жесткий передний центр |  |  | На плавающий передний центр |  |  | По внешней поверхности: в зажимной цанге по упору |  |  | В самоцентрирующем патроне с упором торцом |  | (при параллельном подрезании торцов) | В самоцентрирующих призмах |  |  | В призме по обработке отверстий по кондуктору |  | ** | На плоской поверхности при обработке отверстия по кондуктору |  |  | В призме при обработке плоскости или паза |  |  | То же | |  | » » | |  | По отверстию: На жесткой оправке со свободной посадкой |  | при установке оправки на плавающий передний центр, в гильзу или патрон по упору  | На разжимной оправке: на жесткой оправке с натягом | | При установки оправки на жесткий передний центр  | По двум отверстиям на пальцах: При обработке верхней поверхности | |  | По плоскости: При обработке уступа |  |  | *Dц – просадка центров Значения Dц принимать следующие Наибольший диаметр центрового отверстия, мм | 1; 2; 2,5 | 4; 5; 6 | 7,5; 10 | 12,5; 15 | 20; 30 | | | Просадка центров Dц, мм | 0,11 | 0,14 | 0,18 | 0,21 | 0,23 | ** eе — смещение оси отверстия относительно оси внешней поверхности (отклонение от концентричности) dD — допуск на диаметр внешней поверхности. smin .—минимальный гарантированный зазор. dA — допуск на размер базового отверстия. dB — допуск на размер оправки. 37. Погрешность закрепления заготовок Ед п~н установке н радиальном направлении для обработки на станках, мкм | Характеристика базовой поверхности | Поперечные размеры заготовки, мм | 6—10 | 10—18 | 18-30 | 30—50 | 50-80 | 80—120 | 120-180 | 180—260 | 260—360 | 360—500 | Установка в зажимной гильзе (цанге) | Холоднотянутая калиброванная | | | | | | — | — | — | — | — | Предварительно обработанная | | | | | | — | — | — | — | — | Чисто обработанная | | | | | | — | — | — | — | — | Установка в трехкулачковом патроне | Литье: | | | | | | | | | | | в песчаную форму машинной формовки по металлической модели | | | | | | | | | | | в постоянную форму | | | | | | | | | | | по выплавляемой модели | | | | | | | | | — | — | под давлением | | | | | | | | | — | — | Горячая штамповка | | | | | | | | | | — | Горячекатаная | | | | | | | | — | — | — | Предварительно обработанная | | | | | | | | | | | Чисто обработанная | | | | | | | | | | | Установка в пневматическом патроне | Литье: | | | | | | | | | | | в песчаную форму машинной формовки по металлической модели | | | | | | | | | | | в постоянную форму | | | | | | | | | | | по выплавляемой модели | | | | | | | | | — | — | под давлением | | | | | | | | | — | — | Горячая штамповка | | | | | | | | | | — | Горячекатаная | | | | | | | | — | — | — | Предварительно обработанная | | | | | | | | | | | Чисто обработанная | | | | | | | ДО | | | | | | | | | | | | | | | | Примечания! 1. При установке на оправку надо учитывать погрешность базирования и принимать погрешность закрепления в зависимости от крепления оправки в гильзе, патроне или зажимном приспособлении. 2. Установка в жестких центрах не дает погрешности закрепления в радиальном направлений. Погрешность закрепления, получающаяся при установке в плавающий передний и вращающийся задний центры, не учитывается, так как перекрывается отклонением заготовки под действием силы резания. 38. погрешность закрепления заготовок eЗ при установке в осевом направлении для обработки на станках, мкм Характеристика базовой поверхности | Поперечные размеры заготовок, мм. | 6—10 | 10—18 | 18—30 | 30—50 | 50—80 | 80—120 | 120—180 | 180—260 | 260—300 | 300—500 | Установка в зажимной гильзе (цанге) по упору | Холоднотянутая калиброванная | | | | | | .— | — | — | ,— | — | Предварительно обработанная | ©2015 www.megapredmet.ru Все права принадлежат авторам размещенных материалов. |