ПОЗНАВАТЕЛЬНОЕ Сила воли ведет к действию, а позитивные действия формируют позитивное отношение Как определить диапазон голоса - ваш вокал
Игровые автоматы с быстрым выводом Как цель узнает о ваших желаниях прежде, чем вы начнете действовать. Как компании прогнозируют привычки и манипулируют ими Целительная привычка Как самому избавиться от обидчивости Противоречивые взгляды на качества, присущие мужчинам Тренинг уверенности в себе Вкуснейший "Салат из свеклы с чесноком" Натюрморт и его изобразительные возможности Применение, как принимать мумие? Мумие для волос, лица, при переломах, при кровотечении и т.д. Как научиться брать на себя ответственность Зачем нужны границы в отношениях с детьми? Световозвращающие элементы на детской одежде Как победить свой возраст? Восемь уникальных способов, которые помогут достичь долголетия Как слышать голос Бога Классификация ожирения по ИМТ (ВОЗ) Глава 3. Завет мужчины с женщиной 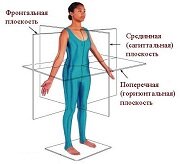
Оси и плоскости тела человека - Тело человека состоит из определенных топографических частей и участков, в которых расположены органы, мышцы, сосуды, нервы и т.д. Отёска стен и прирубка косяков - Когда на доме не достаёт окон и дверей, красивое высокое крыльцо ещё только в воображении, приходится подниматься с улицы в дом по трапу. Дифференциальные уравнения второго порядка (модель рынка с прогнозируемыми ценами) - В простых моделях рынка спрос и предложение обычно полагают зависящими только от текущей цены на товар. | Изготовление стальных изделий Классификация Металлы, как материалы, обладают комплексом ценных для строительной техники свойств - большой прочностью, пластичностью, свариваемостью, выносливостью; способностью упрочняться и улучшать другие свойства при термомеханических и химических воздействиях. Этим обуславливается их широкое применение в строительстве и других областях техники. В чистом виде металлы, вследствие недостаточной прочности, твердости и высокой пластичности применяются редко. Главным образом они используются в виде сплавов с другими металлами и неметаллами, например, углеродом. Железо и его сплавы (сталь С < 2,14%, чугун С > 2,14%) называют черными металлами, остальные (Be, Mg, Al, Ti, Cr, Mn, Ni, Cu, Zn и др.) и их сплавы - цветными. (таб.1) Наибольшее применение в строительстве имеют черные металлы. Стоимость их значительно ниже цветных. Однако последние обладают рядом ценных свойств - высокой удельной прочностью, пластичностью, коррозионной стойкостью и декоративностью, расширяющими области их применения в строительстве, в первую очередь архитектурно-строительных деталей и конструкций из алюминия. Сырьем для получения черных металлов служат руды железа, представленные минералами класса оксидов - магнетитом (FeFe2O4) гематитом (Fe2Оз), хромитом (FeCr2O4) и др. Для производства цветных металлов используются бокситы; сульфидные и карбонатные руды меди, никеля, цинка и др. Табл. 1 Классификация металлов и сплавов.  СТРОЕНИЕ И СВОЙСТВА ЖЕЛЕЗОУГЛЕРОДИСТЫХ СПЛАВОВ Металлы, как и другие вещества, могут существовать в различных кристаллических формах (модификациях). Это явление называется полиморфизмом. Полиморфные превращения в металлах происходят при изменении температуры. Так, при температуре свыше 723°С железо переходит из α-модификации в γ-модификацию, при этом изменяются физико-механические свойства металла. При резком охлаждении металла высокотемпературные модификации могут и не переходить в низкотемпературные. На этом, например, основана термообработка металлов (закалка, отпуск, нормализация). Химически чистые металлы на практике используют редко. Это связано с трудностью получения чистых веществ, а также с возможностью получать металлы с определенными требуемыми свойствами путем создания различных сплавов. В металловедении различают три типа сплавов: твердый раствор, механическую смесь, химическое соединение. Если атомы входящих в состав сплава элементов незначительно отличаются размером и строением электронной оболочки, то они могут образовывать общую кристаллическую решетку. Сплав с таким строением называют твердым раствором. Если элементы сплава не образуют твердого раствора, а каждый из них кристаллизуется самостоятельно, то такой сплав называют механической смесью. Если элементы сплава вступают в химическое взаимодействие, образуя новое вещество, такой сплав называют химическим соединением. Практически сплавы могут сочетать в себе все три типа строения. Рассмотрим зависимость свойств сплава от его состава и строения на примере железоуглеродистых сплавов (сталей и чугунов). Чистое железо — серебристо-белый мягкий пластичный металл, почти не окисляющийся на воздухе. Прочность его значительно ниже прочности стали и чугуна. При производстве в черные металлы в виде примесей к железу попадают углерод, кремний и некоторые другие вещества. Наибольшее влияние на их свойства оказывает углерод, содержащийся в количестве 0,5...5 %. Способность железа растворять углерод и другие элементы служит основой для получения разнообразных сплавов. Углерод, растворяясь в железе, образует твердые растворы. В низкотемпературной модификации железа (α - железо) растворяется мало углерода (до 0,02 %), такой раствор называют ферритом. Феррит обладает низкой твердостью и высокой пластичностью. Чем больше в сплаве содержится феррита, тем он мягче и пластичнее. Высокотемпературная модификация железа (γ - железо) лучше растворяет углерод (до 2 %), образуя твердый раствор аустенит, также характеризующийся высокой пластичностью. Химическое соединение железа с углеродом — карбид железа, в котором содержится 6,67 % углерода, называют цементитом. Цементит хрупок и имеет высокую твердость. Чем больше цементита в сплаве, тем он более твердый и хрупкий. В некоторых случаях (например, в присутствии больших количеств кремния) цементит не образуется, а углерод выделяется в виде графита (например, в сером чугуне). В сталях и чугунах феррит, аустенит и цементит существуют в виде механических смесей. Иными словами, сталь и чугун — поликристаллические материалы, свойства которых зависят как от химического состава (количества железа,' углерода и других примесей), так и от структуры (типа и размера кристаллов). Например, при нагревании до температуры выше 723 °С твердая и прочная углеродистая сталь, состоящая из смеси феррита и цементита, становится мягкой и прочность ее падает, так как смесь феррита и цементита переходит в аустенит — раствор углерода в γ-железе. На этом основана горячая обработка (прокат, ковка) углеродистых сталей. Этим же объясняется резкое падение прочности и, как следствие, деформация и разрушения стальных конструкций из-за нагрева во время пожара. Железо имеет четыре полиморфные модификации: α-Fe, β-Fe, γ-Fe и δ-Fe. Практическое значение имеют модификации α-Fe и γ-Fe. Переход железа из одной модификации в другую происходит при определенных критических температурах. Модификация α-Fe имеет кубическую объемно-центрированную кристаллическую решетку, γ-Fe-кубическую гранецентрированную кристаллическую решетку. Атомы в решетке стремятся занять положение, соответствующее минимуму ее энергии, образуя плотнейшие упаковки - кубическую объемно - и гранецентрированную.  Рис.1. Координационные числа (плотность упаковки) кристаллических решеток: а) кубической гранецентрированной (К 12); 6) объемноцентрированной (К8); Плотность упаковки характеризуется координационным числом, представляющим собой число соседних атомов, находящихся на равном и наименьшем расстоянии от данного атома. Чем больше число, тем плотнее упаковка. Для объемноцентрированной кубической упаковки оно равно 8 (К8); гранецентрированной - 12 (К12). В кубической объемно-центрированной решетке кристаллизуются: К, Na, Li, α-Fe, Mo, W, V, Cr, Ba и др.; кубической гранецентрированной - Ni, Ag, Au, Pt, Си, γ- Fe; Расстояние между центрами ближайших атомов в решетке называется периодом решетки. Основы получения чугуна Разновидности чугуна Чугун получают в ходе доменного процесса, основанного на восстановлении железа из его природных оксидов, содержащихся в железных рудах, коксом при высокой температуре. Кокс, сгорая, образует углекислый газ. При прохождении через раскаленный кокс он превращается в оксид углерода, который и восстанавливает железо в верхней части печи по обобщенной схеме: Fe2O3àFe3O4àFeОàFe. Опускаясь в нижнюю горячую часть печи, железо плавится в соприкосновении с коксом, и частично растворяя его, превращается в чугун. В готовом чугуне содержится около 93% железа, до 5% углерода и небольшое количество примесей кремния, марганца, фосфора, серы и некоторых других элементов, перешедших в чугун из пустой породы. В зависимости от количества и формы связи углерода и примесей с железом, чугуны имеют разные свойства, в том числе цвет, подразделяясь по этому признаку на белые и серые. Рис. 1. Схема доменной печи: 1 - летка для выпуска жидкого чугуна; 2 - расплавленный шлак; 3 — загрузочное устройство; 4 — газоотводная труба; 5—капли расплавленного чугуна; 6 — капли шлакового расплава; 7 — фурма для подачи воздуха; 8 — летка для выпуска расплавленного шлака; 9— жидкий чугун. Белый чугун (передельный) содержит весь углерод в химически связанном состоянии в виде карбида железа, именуемого цементитом Fе3С. При нормальной температуре его структура слагается из двух фаз: феррита и цементита. Белым этот чугун называется потому, что в изломе он имеет матово-белый цвет. Белый чугун имеет высокую твердость и большую хрупкость, вследствие чего его невозможно обрабатывать режущим инструментом. Его применяют, главным образом, для выплавки стали, а также для получения ковкого чугуна. Серые чугуны содержат углерод в свободном состоянии в виде графита (100% С); они называются серыми потому, что вследствие наличия в них графита имеют в изломе серый цвет. Содержание С — до 3,8%. По форме графитовых включений серые чугуны разделяют на обычный серый с пластинчатым графитом, вермикулярный серый, высокопрочный и ковкий. По структуре металлической основы разделяют на ферритный, ферритно-перлитный и перлитный. Обычный серый чугун получают медленным охлаждением жидкого расплава или аустенита высокоуглеродистых сплавов. В нем частицы графита имеют пластинчатую форму. В зависимости от механических свойств и назначения серый чугун с пластинчатым графитом разделяют на марки: СЧ-25, СЧ-30, СЧ-35, СЧ-40, СЧ-45 (цифры показывают минимальный предел прочности при растяжении, кгс/мм2). Вермикулярный серый чугун получают путем специальной плавки или обработки с изменением формы графита на волокнистую, червеобразную (вермикулярную), вследствие чего этот чугун обладает лучшими свойствами по сравнению с обычным серым чугуном. Высокопрочный чугун содержит шаровидный графит, получаемый при выплавке с присадкой небольшого количества магния или церия. Благодаря шаровидной форме графита прочность при растяжении и изгибе высокопрочного чугуна значительно выше, чем обычного серого чугуна с пластинчатым графитом. Высокопрочный чугун разделяют на марки: ВЧ38-17, ВЧ42-12, ВЧ45-5, ВЧ50-2, ВЧ50-7, ВЧ70-2, ВЧ80-2, ВЧ100-2, ВЧ120-2. Буквы ВЧ означают высокопрочный чугун, первые числа за ними — минимальный предел прочности при растяжении (в кгс/мм2), а последующие числа — минимальное относительное удлинение (в %). Ковкий чугун содержит хлопьевидный графит. Его получают из белого чугуна путем графитизирующего отжига (томления), при котором происходит распад цементита. Хлопьевидный графит имеет почти равноосную компактную форму. Этот чугун . разделяют на марки: КЧЗО-6, КЧЗЗ-8, КЧ35-10, КЧ37-12, КЧ45-6, КЧ50-4, КЧ60-3, КЧ63-2. В обозначение марки входят буквы КЧ (ковкий чугун), затем число - - минимально допустимый предел прочности при растяжении ( кгс/мм2), второе число — относительное удлинение ( %). Свойства серых чугунов зависят от свойств металлической основы, вида и количества графитных включений. Графит имеет низкие показатели механических свойств, и включения его можно условно рассматривать как пустоты и трещины. Чем больше графита, крупнее графитные включения, тем ниже механические свойства чугуна и особенно прочность при растяжении и изгибе. Прочность при сжатии и твердость чугуна зависят в основном от металлической основы и мало отличаются от сталей. В некоторых случаях графитные включения полезны благодаря смазывающему действию графита. Такой чугун легче обрабатывается резанием, чем сталь, стружка становится ломкой, когда резец доходит до графитных включений. Подобно другим железоуглеродным сплавам, чугуны содержат постоянные примеси кремния, марганца, серн и фосфора в больших количествах, чем в сталях. Эти примеси оказывают значительное влияние на графитизацию, структуру и свойства чугунов. В чугуны часто вводят также медь, алюминий, титан, хром, никель. Эти элементы оказывают влияние на процесс графитизации. Подобно сталям такие чугуны называют легированными. Серые чугуны применяют при изготовлении опорных элементов для ферм, железобетонных балок и колони, тюбингов в метро, при производстве многих других строительных конструкций, а также находят широкое применение в деталях машин, не подвергающихся большим растягивающим напряжениям и ударным нагрузкам. Основы получения стали Сталь получают из чугуна путем удаления из него части углерода и примесей. Существуют три основных способа производства стали: конвертерный, мартеновский и электроплавильный. Конвертерный основан на продувке расплавленного чугуна в больших грушевидных сосудах – конвертерах сжатым воздухом. Кислород воздуха окисляет примеси, переводя их в шлак; углерод выгорает. При малом содержании в чугуне фосфора, конвертеры футеруют кислыми огнеупорами, например динасом, при повышенном - основными, периклазовыми. Соответственно выплавляемую в них сталь по традиции называют бессемеровской и томасовской. Конвертерный способ отличается высокой производительностью, обусловившей его широкое распространение. К недостаткам его относятся повышенный угар металла, загрязнение шлаком и наличие пузырьков воздуха, ухудшающими качество стали. Применение вместо воздуха кислородного дутья в сочетании с углекислым газом и водяным паром, значительно улучшает, качество конвертерной стали. Мартеновский способ осуществляется в специальных печах, в которых чугун сплавляется вместе с железной рудой и металлоломом (скрапом). Выгорание примесей происходит за счет кислорода воздуха, поступающего в печь вместе с горючими газами и железной рудой в составе оксидов. Состав стали хорошо подаются регулированию, что позволяет получать в мартеновских печах высококачественные стали для ответственных конструкций. Электроплавление является наиболее совершенным способом получения высококачественных сталей с заданными свойствами, но требует повышенного расхода электроэнергии. По способу ее подведения электропечи подразделяются на дуговые и индукционные. Наибольшее применение в металлургии имеют дуговые печи. В электропечах выплавляют специальные виды сталей - средне- и высоколегированные, инструментальные, жаропрочные, магнитные и другие. Изготовление стальных изделий Выплавляемую сталь разливают на слитки. Стальные слитки — полуфабрикат, из которого различными методами получают необходимые изделия. В основном применяют, обработку стали давлением: металл под действием приложенной силы деформируется, сохраняя приобретенную форму. При обработке металла давлением практически нет отходов. Для облегчения обработки сталь часто предварительно нагревают. Различают следующие виды обработки металла давлением: прокатка, прессование, волочение, ковка, штамповка. Наиболее распространенный метод обработки — прокатка; им обрабатывается, более 70 % получаемой стали. При прокатке стальной слиток пропускают между вращающимися валками прокатного стана, в результате чего заготовка обжимается, вытягивается и в зависимости от профиля прокатных валков приобретает заданную форму (профиль), Прокатывают сталь в основном в горячем состоянии. Сортамент стали горячего проката — сталь круглая, квадратная, полосовая, уголковая равнобокая и неравнобокая, швеллеры, двутавровые балки, шпунтовые сваи, трубы, арматурная сталь гладкая и периодического профиля и др. При волочении заготовка последовательно протягивается через отверстия (фильеры) размером меньше сечения заготовки, вследствие чего заготовка обжимается и вытягивается. При волочении в стали появляется так называемый наклеп, который повышает ее твердость. Волочение стали, обычно производят в холодном состоянии, при этом получают изделия точных профилей с чистой и гладкой поверхностью. Способом волочения изготовляют проволоку, трубы малого диаметра, а также прутки круглого, квадратного и шестиугольного сечения. Ковка — обработка раскаленной стали повторяющимися ударами молота для придания заготовке заданной формы. Ковкой изготовляют разнообразные стальные детали (болты, анкеры, скобы и т. д.). Штамповка — разновидность ковки, при которой сталь, растягиваясь под ударами молота, заполняет форму штампа. Штамповка может быть горячей и холодной. Этим способом можно получать изделия очень точных размеров. Прессование представляет собой процесс выдавливания, находящейся в контейнере стали через выходное отверстие (очко) матрицы. Исходным материалом для прессования служит литье или прокатные заготовки. Этим способом можно получать профили различного сечения, в том числе прутки, трубы небольшого диаметра и разнообразные фасонные профили. Холодное профилирование — процесс деформирования листовой или круглой стали на прокатных станах. Из листовой стали получают гнутые профили с различной конфигурацией в поперечнике, а из круглых стержней на станках холодного профилирования путем сплющивания — упрочненную холодносплющенную арматуру. СВОЙСТВА СТАЛЕЙ Сталь наряду с бетонами — главнейший конструкционный материал. Широкому использованию в строительстве сталь обязана высоким физико-механическим показателям, технологичности (возможности получения из нее конструкций различными методами) и большими объемами производства. Плотность стали — 7850 кг/м, что приблизительно в 3 раза выше плотности каменных материалов (например, обычный тяжелый бетон имеет плотность — 2400 ±50 кг/м3). Прочностные и деформативные свойства стали, обычно определяются, испытанием стали на растяжение. При этом строится диаграмма «напряжение — деформация». Сталь, как и другие металлы, ведет себя как упруго-пластичный материал. В начале испытаний деформации у стали пропорциональны напряжениям. Максимальное напряжение, при котором сохраняется эта зависимость, называется предел пропорциональности δy (при этом напряжении остаточные деформации не должны превышать 0,05 %). При дальнейшем повышении напряжения начинает проявляться текучесть стали - быстрый рост деформаций при небольшом подъеме напряжений. Напряжение, соответствующее началу течения, называют предел текучести δτ. Затем наступает некоторое замедление роста деформаций при подъеме напряжений («временное упрочнение»), после чего наступает разрушение образца, называемое временным сопротивлением δв, что является, фактическим пределом прочности стали (Rp). Относительное удлинение стали ε, в момент разрыва характеризует ее пластичность. Оно рассчитывается по формуле: ε = ((l1 - l0)ll0) • 100, где lо — начальная длина расчетной части образца, мм; l1 — длина этой части в момент разрыва образца, мм. Испытание на растяжение является основным при оценке механических свойств сталей. Модуль упругости стали составляет 2,1- 105 МПа. Твердость сталей испытывают путем вдавливания в него под определенной нагрузкой стального шарика, алмазного конуса или пирамиды (рис.1.) и оценивают по величине произведенной пластической деформации (отпечатку). В зависимости от вида используемого наконечника и критерия оценки различают твердость по Бринеллю, Роквеллу и Виккерсу.  Рис.1. Схема определения твердости: а) по Бринеллю; б) по Роквеллу; в) по Виккерсу. Твердость металлов по Бринеллю рассчитывают по формуле: HB=2P/πD(D - √D2 – d2)10-6 , Мпа, где Р. - нагрузка, (Н); D - диаметр стального шарика, (м). В приборе принят D = 1 • 10-2 м; d - диаметр отпечатка (лунки), (м). При испытании значение Р принимают: для стали и чугуна -3 *104 Н, меди и сплавов – 1 * 104 Н, а очень мягких металлов (алюминия, баббита) - 2,5 * 103 Н. Метод применим для металлов и сплавов с твердостью не более 4500 МПа, так как при большей твердости стальной шарик может деформироваться. Твердость по Роквеллу измеряют в условных единицах по формулам: HR = 100-е (при вдавливании алмазного конуса с углом при вершине 120°), HR — 130-e (при вдавливании стального шарика, D= 1,588-10-3м), где е = (h – h0)/2*10-6- глубина внедрения наконечника (м), под действием общей нагрузки Р после снятия основной нагрузки Р1, h0-глубина внедрения наконечника под действием предварительной нагрузки Ро, (М). Предварительная нагрузка P0 при испытаниях независимо от вида наконечника принята 100 Н; основная Р/ для стального шарика - 900 Н (шкала В), алмазного конуса - 1400 Н (шкала С) и 500 Н (шкала А). В соответствии с этим твердость по Роквеллу обозначается HRA, HRB, HRC. Метод широко применяется в промышленности, особенно для твердых и тонколистовых металлов и сплавов. Твердость по Виккерсу определяют по формуле: HV = 1, 8544 (Р/d2) *10-6, МПа, Где Р - нагрузка на алмазную пирамиду от 500 до 1200 Н; d - среднеарифметическое значение двух диагоналей отпечатка, м. Твердость по Виккерсу обозначается HV5, HV10 и т.д. Чем тоньше и тверже металл и сплав, тем меньше должна быть нагрузка при испытании. Для определения микротвердости мелких изделий и структурных составляющих металлов используют также метод Виккерса в приборном сочетании с металлографическим микроскопом. Ударная вязкость — свойство стали противостоять динамическим (ударным) нагрузкам. Ее значение определяют по величине работы, необходимой для разрушения образца на маятниковом копре. Ударная вязкость зависит, от состава стали, наличия легирующих элементов и заметно меняется при изменении температуры. Так, у Ст3 ударная вязкость при +200С составляет 0,5….1 МДж/м2 , а при -200С - 0,3...0,5 МДж/м2. Технологические свойства стали показывают ее способность принимать определенные деформации, аналогичные тем, которые стальное изделие будет иметь при дальнейшей обработке или в условиях эксплуатации. Для строительных сталей чаще всего производят пробу на холодный загиб. При испытании на загиб определяются не усилия для осуществления деформации, а условия (угол загиба, диаметр оправки), при которых возможно протекание деформации без нарушения сплошности образца (т. е. без появления трещин и расслоения). Чем пластичнее сталь, тем меньше диаметр оправки при испытаниях (см. табл.1) |