Агротехнические требования 1. Отклонение глубины обработки при вспашке не должно превышать ±1см, при глубоком (20−30см) рыхлении — ±3−4см 2. Высота гребней должна быть не более 5 см 2. Степень сохранения стерни при плоскорезной обработке — 80−85%, высота свальных гребней и глубина развальных борозд при вспашке — не более 5 см 4. Заделка растительных остатков, сорных растений и удобрений при вспашке — не менее 95% 5. Выровненность поверхности почвы при вспашке на отрезке 10 м длины профиля — не более 10,7 м. Не допускаются не заделанные разъемные борозды, невспаханные свальные гребни, огрехи и необработанные поворотные полосы. Рано весной на полях, обработанных безотвальными орудиями, проводят рыхление почвы; на отвальной зяби — боронование и культивацию на глубину заделки семян (5−6см). После дискования, а также после боронования рыхлых почв, проводят прикатывание. Боронование. Предпосевное боронование проводят для рыхления почвы до мелкокомковатого состояния, уменьшения испарения влаги, выравнивания почвы и уничтожения проросших сорняков. В зависимости от вида сельскохозяйственной культуры и почвенно-климатических условий для предпосевной обработки почвы применяют следующие виды борон: зубовые; шлейф-бороны; ротационную мотыгу; дисковые бороны. Зубовые бороны в зависимости от давления на один зуб (определяют делением силы тяжести одного звена на число зубьев) подразделяют на тяжелые, средние и лёгкие с давлениями на один зуб соответственно 20...30, 10...20, 5...10 Н Организация работы агрегатов предусматривает организацию движения, а также выбор как общего требуемого числа агрегатов, так и числа агрегатов в составе одной группы. Бороновальные агрегаты для обеспечения равномерного рыхления почвы должны двигаться поперек пахоты или под углом к ней. Односледное боронование зубовыми боронами целесообразно вести челночным или диагональным способом, а двухследное диагонально-перекрёстным способом качество работы бороновальных агрегатов контролируют, оценивая три основных показателя - глубину рыхления, гребнистость и глыбистость (по диаметру комков). При наличии огрехов работу бракуют независимо от значений других показателей. Прикатывание почвы. Проводят его как до, так и после посева. Цель предпосевного прикатывания разрушение глыб, разрушение верхнего и уплотнение предповерхностного слоёв почвы, частичное выравнивание поверхности поля. Прикатывание посевов улучшает контакт семян с почвой и увеличивает приток влаги из нижних горизонтов, что способствует более быстрому появлению дружных и равномерных всходов. Прикатывание поля повышает также равномерность хода агрегатов на последующих операциях при более высокой скорости. Агротехнические требования: уплотнение почвы на глубину до 7 см и рыхление верхнего слоя на глубину 2...3 см; размер оставшихся комков не более 5 см; огрехи и пропуски не допускаются; перекрытие следов отдельных катков 7...10 см, а между смежными проходами агрегата — 10 см. ПРЯМОЕ КОМБАЙНИРОВАНИЕ. Уборка является одной из самых сложных операций в технологическом процессе. Существует два традиционных способа уборки: - Прямое комбайнирование.
- Раздельное комбайнирование.
При прямом комбайнировании хлебостой скашивается, обмолачивается, очищается зерно от различных примесей и грузится в транспортное средство. Транспортное средство отвозит зерно на ток, где оно сушится и сортируется. Прямое комбайнирование применяют, когда весь колос созревает одновременно. В этом случае хорошо обмолачивается как нижняя, так и верхняя часть колоса. Раздельное комбайнирование применяют, когда колос созревает неравномерно. Сначала созревает нижняя часть колоса, а через 10-14 дней верхняя часть. Если, обмолачивать хлебостой, при недозревшей верхней части колоса это приведет к потерям. Если обмолачивать хлебостой после созревания верхней части колоса, то нижняя часть перезреет и осыплется, что также ведет к потерям. В нашей зоне, центральный регион, колос созревает не одновременно, поэтому уборку проводят способом раздельного комбайнирования. При уборке, способом раздельного комбайнирования, хлебостой скашивается, подсушивается и дозревает в валках. Далее валки подбираются, обмолачиваются, зерно очищается от различных примесей и грузится в транспортное средство. Не зерновая часть урожая при обоих этих способах может убираться по нескольким технологиям: - Сбор соломы и половы комбайном в копнитель с выгрузкой копен на поле.
- Измельчение соломы и последующей её погрузкой вместе с половой в транспортное средство.
- Измельчение соломы и последующим разбрасыванием вместе с половой по полю.
- Измельчение соломы и разбрасыванием её по полю, полова грузится в транспортное средство.
- Измельчение соломы и последующей её укладкой вместе с половой в валок.
- Измельчение соломы и последующей её укладкой в валок, полова грузится в транспортное средств
24. 6. Определение нормы посадки. Картофель – пропашная культура, поэтому расчет нормы посадки производится исходя из массы посадочного материала и количества клубней, высаживаемых на 1 га. Густота посадки раннего картофеля зависит от сорта, условий возделывания и средней массы клубней. Для раннего картофеля рекомендуемая густота не менее 50-65 тыс. кустов на 1 га. Посадку рекомендуется проводить клубнями средней (50-80 г) величины, на 1 га высаживают 50-55 тыс. клубней. Для получения заданной густоты стояния растений картофель сажают по схеме 70×25. Один из критериев густоты посадки – заданная густота стеблестоя. Она должна быть 150-200 тыс/га. Считается, что 60-70 % ростков образуют основные стебли. Обычно образуется 3-4 стебля на один клубень. Исходя из этого определяют норму посадки. Так один клубень дает в среднем 4 стебля, а на одном га должно быть примерно 200 тысяч стеблей, то норма посадки составляет: 200000:4=50000 клубней/га. Важное условие получения высокого урожая картофеля – норма посадки, которая должна быть в пределах 3-3,5 т/га. При определении фактической густоты посадки картофелесажалка должна проехать с поднятыми заделывающими дисками около 20 м без заделки клубней при заданной рабочей скорости агрегата. Затем отмеряют на борозде отрезок длиной 14,3 м при ширине междурядий 70 см. Число клубней на данном отрезке (0,001 га), умножение на 1000, дает количество клубней, высаженных на 1 га. Лучше подсчитать на четырех рядках и высчитать среднее число клубней в рядке. Количество пропусков при посадке клубнями массой 50-80 г не должно быть более 1,5 %. 3.7. Сроки и способ посадки. Зависят от почвенно-климатических условий: технической оснащенности хозяйства, группы спелости возделываемых сортов, наступления физической спелости почвы. Сроки посадки дифференцируются по зонам. В хозяйствах, Рязанской области посадку картофеля начинают в первой декаде мая и заканчивают не позднее 20-25 мая. Для раннего картофеля наиболее оптимальным сроком является II декада мая. Картофель сажают при прогревании почвы на глубине10 см до 6-8 °С (среднесуточная температура воздуха 10 °С). У пророщенных на открытых площадках клубней ростки жизнеспособны при температуре 2-3 °С, поэтому от посадки пророщенных клубней в такую почву урожай можно получить в наиболее ранние сроки. Продолжительность посадки не должна превышать 8-10 дней. Картофель высаживают целыми клубнями. Однако при недостатке посадочного материала крупные клубни массой 100 г и более разрезают на части не менее 30 г с тремя-четырьмя глазками. Резать клубни надо только в день посадки. Резаные клубни высаживают вместе с целыми в соотношении 1: 3, так как одни резаные клубни плохо захватываются вычерпывающими ложечками и посевы получаются изреженными. Наиболее распространенная ширина междурядий при посадке картофеля 70 см. Способ посадки картофеля во многом определяется природно-климатическими условиями зоны. Существует гребневая и гладкая посадка картофеля. В основном применяется посадка в предварительно нарезанные гребни на глубину 8-12 см от вершины гребня. В западных и северо-западных районах Нечерноземной зоны и в других районах с прохладным климатом и избыточным или временно-избыточным увлажнением лучшие результаты дает гребневая посадка. Такой способ способствует равномерному размещению и лучшей заделке клубней, облегчает труд механизаторов, повышает производительность картофелесажалок и комбайнов. При посадке в ранние сроки, когда почва еще переувлажнена, а также в случае возврата похолоданий и наступления периода продолжительных дождей в Нечерноземной зоне следует применять предварительное гребневание почвы весной. Нарезку гребней с междурядьями 70 см проводят культиваторами-окучниками Л-115, Л-803. АК-2,8, КОН-2,8. Время нарезки гребней зависит от погодных условий. В холодную и влажную погоду гребни нарезают вслед за вспашкой или за несколько дней до посадки, в сухую – за дeнь или в день посадки. Нарезка гребней способствует повышению температуры почвы в зоне залегания клубней на 3-4 °С, в результате чего всходы появляются на 5-6 суток раньше. При посадке сошники картофелепосадочной машины идут по центру борозды, раздвигая в сторону почву. Клубни попадают на дно вновь образованных сошниками борозд и закрываются почвой с помощью заделывающих дисков. Предварительное нарезание гребней позволяет высаживать картофель на переувлажненных участках раньше за счет более быстрого просыхания и прогревания почвенных гребней. Для посадки картофеля используют картофелесажалки СН-4Б, КСМ-4, КСМ-6, Л-207, Л-201, Л-202, Л-205. При посадке рядки должны быть прямолинейными с сохранением заданной ширины междурядий. Отклонение ширины основных междурядий допускается не более +-2 см, стыковых – не более + -10 см. Отклонение по глубине посадки допускается в пределах +-2 см. Глубина посадки не должна превышать 6-8 см, (от верхней точки клубня до вершины гребня). Для получения наиболее ранней продукции картофель сажают как можно раньше. В этих случаях клубни заделывают мельче, чем при обычных сроках посадки. 25. Методы прогнозирования технического состояния машин и исходные данные для выполнения прогнозирования. Прогнозирование– один из основных элементов технической диагностики. Основная цель прогнозирования – установление (предсказание) сроков безотказной работы составных частей машины до очередного ТО или ремонта. Теоретической основой прогнозирования служит прогностика – наука, изучающая поведение прогнозируемых систем в зависимости от воздействия различных факторов. Полный процесс прогнозирования технического состояния и ресурса машин состоит из 3-х этапов. 1-й этап – заключается в исследовании процесса изменения параметров технического состояния составных частей машин в прошлом. 2-й этап – устанавливают номинальные, допускаемые и предельные значения параметров, измеряют текущие значения этих параметров в процессе диагностирования. 3-й этап – осуществляют прогноз* состояния составных частей машины, а затем по результатам анализа принимают конкретные решения о виде и объеме ремонтных работ, технического обслуживания, регулировочных операциях и остаточном ресурсе машины. При этом под остаточным ресурсом понимают НАРАБОТКУ от момента диагностирования до предельного состояния составных частей машины. прогноз* - заключение, вывод о предстоящем развитии и исходе события, на основании каких-нибудь данных. Различают два метода прогнозирования технического состояния и остаточного ресурса составных частей машин.
^ Метод. Прогнозирование по среднему статистическому изменению параметра составных частей машины. Сущность этого метода прогнозирования технического состояния и ресурса машин заключается в том, что предварительно (по данным статистики) устанавливают показатели изменения параметра и экономические характеристики, связанные с затратами на восстановление. По этим показателям определяют допускаемое значение параметра, их средний ресурс и межконтрольную наработку. Функция периодичности прогнозного состояния составных частей машины определяется так , где Р1, Р2, Р3 – соответственно, вероятные удельные издержки на поиск, измерение и регулировку параметра при известной межконтрольной наработке tм и допускаемых значениях параметра Пдоп. По результатам диагностирования инженер-диагност сравнивает измеренное значение параметра с его предварительно установленным допускаемым значением. П ри повышении измеренного значения параметра, если последний со временем увеличивается (радиальный зазор подшипников, удельный расход топлива двигателем). 1,2 – измеренные значения параметра. 3,4 – допускаемые значения параметра. Или если последний со временем уменьшается (диаметр вала, мощность ДВС, производительность машины).  1¢,2¢– измеренные значения параметра. То принимают решение о восстановлении номинального значения параметра путем замены деталей, регулирования зазора, давления и др. Таким образом, при этом методе прогнозирования по результатам диагностирования остается только сравнить измеренное значение параметра с его допускаемой величиной. ^ 2-й Метод. Прогнозирование по индивидуальному измерению параметра одной конкретной составной части машины. Сущность второго метода заключается в том, что по результатам диагностирования учитывают скорость изменения параметра у конкретной составной части по её наработке. Обычно второй метод применяют для прогнозирования надежной работы машины в течение заданной наработки – первая задача. Или для прогнозирования остаточного ресурса машины до капитального ремонта – вторая задача. Индивидуальное прогнозирование дает больший экономический эффект, чем прогнозирование по среднему статистическому изменению параметра, т.к. при индивидуальном прогнозировании погрешность учета скорости изменения параметра в несколько раз меньше, а значит и точнее прогноз. Для прогнозирования остаточного ресурса методом индивидуального прогноза необходимо знать исходное значение замеряемого параметра (с учетом состояния машины – новой или капитально отремонтированной); количество отработанных мото-часов (или израсходованного диз. топлива); значение замеренного параметра в момент диагностирования П(tн) Пусть в момент времени ti машине провели диагностирование и определили значение параметра П(tн) (на момент диагностирования). В этом случае прогнозирование остаточного ресурса может выполняться по одному из двух направлений: Первое: известна наработка tн от начала эксплуатации до момента диагностирования П(tн) и определено изменение параметра U(tн)=[ П(tм)-Пн] к моменту прогноза. Второе: отсутствуют сведения о наработке машины с начала эксплуатации, но зато известна наработка машины tм от последнего диагностирования Дп.д. (ремонта) до момента прогноза. Приведенные два направления применения метода индивидуального прогноза основаны на том, что интенсивность изнашивания одних и тех же механизмов машины одной марки не одинаковы. И ещё важное замечание нужно подчеркнуть в связи с тем, что РЕСУРС составных частей машины рекомендуется определять по основным, решающим параметрам, определяющим дальнейшую эксплуатацию машины без капитального ремонта. У тракторов к таким параметрам относятся: угар картельного масла; количество газов, прорывающихся в картер двигателя; давление масла в масленой магистрали; зазоры в подшипниках коленвала; плотность прилегания клапанов к гнездам головки цилиндров. Решение конкретных задач по прогнозированию остаточного ресурса двигателя внутреннего сгорания (ДВС). Сроки службы составных частей машин, с достаточной точностью, можно прогнозировать по следующим двум методикам: Методика прогнозирования остаточного ресурса при известной наработке от начала эксплуатации Чтобы определить остаточный ресурс конкретной составной части tост, мастер-диагност должен располагать исходными данными, приведенными в таблице 1. Таблица 1 – Сведения, необходимые для прогнозирования остаточного ресурса Исходные данные | Обозначение | Источник информации | Номинальное значение параметра (исходное значение) | Пн | Технологическая карта диагностирования | Наработка проверяемой составной части машины от начала её эксплуатации до момента диагностирования | tн | Показания мотосчетчика; техническая документация. | Значение параметра, замеренное в момент диагностирования (после наработки tн). | П(tн) | Средство измерения | Показатель изменения параметра (за период наработки tн ) | U(tн) | Технологическая карта диагностирования | Предельное значение | Ппр | Показатель степени функции изменения состояния параметра | a | Если известна наработка tн от начала эксплуатации, то остаточный ресурс tост мы можем определить по формуле , где Uпр – предельное изменение параметра, причем берется абсолютное значение параметра , где U(tн) – изменение параметра в момент диагностирования (к моменту прогноза). a - показатель степени функции изменения состояния параметра. По данным ГОСНИТИ, значение a для тракторов и сельхозмашин находится в пределах 0,8…2,0. Так, например, для расхода артерных газов: до замены поршневых колец a =1,3; после замены поршневых колец a=1,5. Угар картерного масла …a = 2,0 Мощность двигателя …a = 0,8. И т.д. При a=1 интенсивность изменения параметра, а следовательно, и скорость изнашивания деталей и сопряжений постоянны. В этом случае остаточный ресурс определяется так . Таким образом, для определения остаточного ресурса какого-либо сопряжения необходимо измерить значение соответствующего параметра в момент диагностирования и знать наработку к моменту измерения от начала эксплуатации. Значения остальных показателей берутся из таблиц. ^ Методика прогнозирования остаточного ресурса при неизвестной наработке от начала эксплуатации. При прогнозировании остаточного ресурса сведения о наработке отдельных составных частей машины от начала эксплуатации иногда отсутствуют. В подобных случаях остаточный ресурс определяют по значениям параметров, устанавливаемым при предыдущем и повторном диагностировании, а также наработке tм между первым и вторым измерениями. Например, при текущем ремонте на двигатель были поставлены детали цилиндро-поршевой группы с допускаемым износом, т.е. пригодные для эксплуатации; наработка их с начала эксплуатации неизвестна. При очередном диагностировании провели первую проверку технического состояния цилиндро-поршневой группы, а после того как двигатель проработал ещё один межконтрольный срок повторно измерили тот же параметр. Для данного случая имеем П1 – значение параметра, измеренное при первой проверке технического состояния объекта; П2 – значение параметра, измеренное при второй проверке технического состояния объекта: - изменение параметра от начала эксплуатации до первой проверки; - изменение параметра от начала эксплуатации до второй проверки; tм – межконтрольная наработка (за время работы между первой и второй проверками). В этом случае остаточный ресурс tост определяется по формуле , где R – коэффициент, учитывающий темп износа сопряжения (детали) между двумя измерениями (проверками). 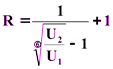 tостусл – условный остаточный ресурс, определяемый по формуле . Тогда  Таким образом, при неизвестной наработке от начала эксплуатации для определения остаточного ресурса необходимо измерить значение контролируемого параметра не менее двух раз и знать наработку за время работы между этими измерениями. Предельное и номинальное значение параметра берутся из таблиц. В практической деятельности инженерно-технических работников аналитические выражения неудобны, так как при определении остаточного ресурса необходимо выполнять сложные и трудные расчеты. В целях упрощения расчетов сотрудниками ГОСНИТИ разработана номограмма, построенная на основании рассмотренных нами выше аналитических уравнений. Она имеет вертикальные и горизонтальные шкалы на которых обозначены изменения параметров и остаточного ресурса, нормированного в долях наработки при различных значениях a. 26. Принципы системного подхода к вопросам ресурсосберегающего использования агрегатов, технологических комплексов и машинно-тракторного парка В условиях перехода к экономическим методам хозяйствования в сельском хозяйстве актуальны задачи ресурсосберегающего использования отдельных агрегатов, технологических комплексов и всего МТП. Соответственно разработка эффективных методов решения задач ресурсосбережения является одним из важных направлений дальнейшего развития курса МАШИНОИСПОЛЬЗОВАНИЕ. Отдельные МТА, технологические комплексы и МТП в целом представляют собой сложные мобильные технические системы, которые в процессе работы должны удовлетворять как агротехническим и экономическим требованиям, так и требованиям, обусловленным законами физики. При этом следует учитывать различие режимов работы агрегатов (рабочий ход; холостой ход; разгон; торможение и др.), разнообразие ресурсов, используемых при работе агрегатов (трудовые; финансовые; материальные; топливно-энергетические и др.), требования охраны окружающей среды и др. Изложенные особенности функционирования сельскохозяйственных агрегатов являются характерными признаками сложной системы, поэтому задачи ресурсосберегающего использования МТА и всего МТП можно комплексно решить лишь на основе принципов многоуровневого системного подхода. Основная идея такого подхода заключается в том, что сложная система исследуется в логической последовательности по взаимосвязанным более простым элементам (подсистемам). При этом в качестве элементов системы (или подсистем) на соответствующих уровнях можно рассматривать основные режимы функционирования агрегатов, включая рабочий и холостой ходы, режим технологического обслуживания и др. Для каждого уровня функционирования составляют соответствующую математическую модель с конкретным критерием ресурсосбережения (минимумом эксплуатационных или трудовых затрат, расхода топлива и т. п.). Уровни ресурсосбережения располагают в такой логической последовательности, чтобы экономия ресурсов на каждом данном уровне дополняла результаты экономии ресурсов, полученные на предшествующих уровнях. Таким образом, происходит сложение эффектов ресурсосбережения всех уровней. Учитывая важность данной задачи, можно сделать вывод, что дальнейшее развитие курса МАШИНОИСПОЛЬЗОВАНИЕ основывается на углублении принципов системного подхода с целью максимальной экономии ресурсов. 27. Особенности использования агрегатов в условиях крестьянских и других хозяйств новых типов Эксплуатация машинно-тракторного парка как наука длительное время развивалась в основном применительно к крупным сельскохозяйственным предприятиям — сначала к машинно-тракторным станциям (МТС), а затем (после расформирования МТС) к колхозам и совхозам. Предприятия указанного типа характеризовались огромными площадями сельскохозяйственных угодий, большим количественным составом МТП и значительной численностью механизаторских кадров. Поэтому в определенной степени был оправдан непрерывный рост единичных мощностей и энергонасыщенности тракторов, пропускной способности зерноуборочных и других комбайнов, а также производительности различных сельскохозяйственных машин. Нарождающиеся в новых условиях крестьянские или фермерские и другие частные хозяйства существенно отличаются от колхозов и совхозов как размерами возделываемых площадей земли, так и численностью работников, определяемой часто количеством взрослых членов семьи. Существенно ограничены и финансовые возможности таких хозяйств. Указанные особенности, естественно, должны учитываться как при разработке конструкций соответствующих машин и агрегатов, так и при их непосредственной эксплуатации. Малые объемы работ и ограниченные финансовые возможности диктуют необходимость приобретения малогабаритных агрегатов сравнительно небольшой мощности. Но, с другой стороны, при ограниченной численности работников желательно иметь более высокопроизводительную технику. Необходимо учитывать и то обстоятельство, что при больших единичных мощностях выход из строя (отказ) каждого отдельного агрегата при ограниченном их числе существенно увеличивает вероятность несвоевременного выполнения работ и соответствующего роста количественных и качественных потерь урожая. Совокупность подобных противоречий является характерным признаком для получения оптимального или наилучшего варианта решения. 28. Удельное и полное тяговое сопро-тивление с-х машин . Полное рабочее тяговое сопротивление машин для условий ровного рельефа определяют по упрощенной формуле R м = K м в м Где K м—удельное сопротивле-ние , приходящееся на 1м ширины захвата, кН/м; в м — ширина захвата машины, м. Сопротивление перемещению машин также входит в состав К м . Значения К м для соответствующих видов работ определяют по результатам опытов. Численное значение удельного тягового сопротивления в указанном диапазоне определяют из равенства K M = K Mo [ l +А K ( v ~ v o )], А-дельта где K M о — удельное сопротивление при скорости до vo = 1,4 м/с (5 км/ч), кН/м; АК-относительное приращение удельного сопротивления при увеличении ско рости на 1 м/с. Численные значения K M о , а также АК для всех основных ти пов машин приводятся в справочной литературе. В условиях неровного рельефа удельное сопротивление сельско хозяйственных машин рассчиты-вают по формуле K M = K Mo [l+ А K(vv o )]+/- 10 -3 m му gsina m му — удельная масса машины, приходящаяся на 1 м ширины захвата, кг/м. Суммарное удельное тяговое сопротивление всего агрегата К а = К м + 10 -3 m Cy g(f c cosa±sina), m с у — удельная масса сцепки в расчете на 1 м ширины захвата агрегата, кг/м; f с — коэффициент сопротивления качению сцепки – приводятся в справочниках Вероятностный характер тягового сопротивления рабочих машин Тяговое сопротивление рабочих сельскохозяйственных машин зависит от множества различных факторов: почвенно-климатических, конструктивных и эксплуатационных. Большинство этих факторов носит непрерывно изменяющийся случайный характер. Соответственно и тяговое сопротивление сельскохозяйственной машины будет иметь вероятностный характер изменения. Внешние возмущающие воздействия на МТА характеризуются частотой (периодом) и амплитудой колебаний [44]. В связи с различной скоростью изменения воздействия этих факторов будет различна и их степень влияния на вероятностную составляющую тягового сопротивления агрегата. На некотором промежутке времени постоянными можно считать климатические факторы. Хотя атмосферное давление и температура окружающей среды и оказывают влияние на работу двигателя энергосредства, но скорость их изменения достаточно мала в сравнении с другими эксплуатационными условиями. Например, такие параметры как влажность почвы, уклоны обрабатываемого участка поля и другие могут изменятся уже на протяжении гона [73]. Поэтому их необходимо учитывать при исследованиях МТА и их эксплуатации. Более сильное влияние, в связи с высокой динамичностью, на характер изменения тягового сопротивления агрегата оказывают факторы, которые непосредственно формируют тяговое сопротивление рабочих органов. Это плотность и твердость почвы, ее структура, микропрофиль поверхности ПОЛЯ, ширина захвата машины или орудия, глубина хода рабочих органов и др. Колебания внешней нагрузки МТА условно делятся на макроколебания (0 f 0,2 Гц), мезоколебания (0,2 f 3,0 Гц) и микроколебания (г 3...5Гц).[1] Применение вероятностно-статистических методов оценки дает возможность найти законы распределения, наиболее вероятные значения, пре делы изменения и частотные спектры тягового сопротивления машин и орудий. Для характеристики процесса имеющего вероятностную составляющую оценочными показателями являются математическое ожидание, дисперсия, среднеквадратическое отклонение и коэффициент вариации, функция распределения вероятностей и плотность распределения вероятностей случайной величины. Более полное описание процессов возможно получить, представив их в виде случайных функций-зависимостей какого-либо параметра, имеющего случайный характер (функции), от времени или текущего значения координаты, имеющих неслучайный характер (аргумента). Случайные функции так же могут быть оценены их математическим ожиданием и дисперсией, корреляционной функцией и спектральной плотностью случайной функции.[73]. Это позволяет изучить процессы, как в отдельности, так и их взаимосвязь в динамике. В результате анализа опытных данных исследований пахотных, посевных, культиваторных, уборочных и др. агрегатов установлено что процесс . изменения их тягового сопротивления соответствует нормальному закону распределения с вероятностью согласия Р(х ) от 0,2 до 0,85.[1, 71, 33]. Воздействие определенных факторов на характер изменения тягового сопротивления сельскохозяйственных машин подтверждается результатами многочисленных исследований [71, 79, 28, 48, 15, 93, 14, 45, 46, 65]. С увеличением рабочей скорости агрегата заметно возрастает удельное тяговое сопротивление. Это обусловлено свойствами обрабатываемой среды и конструктивными параметрами самого агрегата. Одновременно при увеличении скорости происходит и изменение амплитуды и частоты колебаний тягового сопротивления относительно математического ожидания. Например, исследованиями пахотного агрегата в составе трактора Э-151 и плуга П-5-35МГА установлено, что при рабочей скорости равной 4,78 км/ч коэффициент вариации тягового сопротивления составил 8,7%, а при увеличении скорости до 8,04 км/ч он равнялся 13,8% [93]. Подобный характер изменения наблюдается и при исследованиях агрегатов других типов. Наибольший диа пазон колебаний сопротивления наблюдается у пахотных агрегатов. На культивации, лущении и бороновании пределы изменения орудий примерно одинаковы [71]. Для МТА в составе ДТ-75А и плуга П-5-35 среднеквадратиче-ское отклонение тягового сопротивления составило 3,5 кН при среднем значении Рср=27,8 кН, а для культиваторного агрегата среднеквадратическое отклонение составило 1,58 кН при Рср=7,6 кН. Следует так же отметить, что наряду со случайным характером изменения таких факторов как свойства почвы и микрорельеф поверхности поля, подвержены изменению в эксплуатационных условиях и первоначально фиксированные значения - глубина обработки, ширина захвата машины или орудия, сцепной вес тягового средства и вес рабочей машины. От изменчивости характера тягового сопротивления машин существенно зависят показатели работы двигателя энергосредства: развиваемая мощность, удельный расход топлива, показатели надежности. Вопрос влияния колебаний нагрузки на параметры работы машинно-тракторных агрегатов и энергосредств подробно изучался многими известными учеными, начиная с В.Н. Болтинского и изложены в работах [1, 7, 9, 37, 2, 30]. Этими исследованиями установлено, что характеристики работы МТА, определенные с учетом вероятностной составляющей тягового сопротивления, не соответствуют характеристикам того же агрегата, определенным при статическом характере нагрузки. Изменяются не только абсолютные значения параметров, но и положение их оптимумов, что заставляет назначать режимы работы МТА, отличающиеся от режимов, рассчитанных классическими методами без учета вероятностного характера нагрузки. Вероятностный характер тягового сопротивления машин является определяющим при расчетах таких эксплуатационных характеристик энергосредств как степень использования тяговой мощности, силы тяги на крюке, эксплуатационной массы, скорости и насыщенности ряда передач и др. [30, 74]. Комплектование МТА на базе малогабаритных энергосредств осуществляется сельскохозяйственными машинами, имеющими меньшую ширину захвата. Это выполняется за счет сокращения числа рабочих органов стандартной широкозахватной машины. Вследствие этого уменьшается и количество факторов воздействующих на характеристики МТА. При проектировании малогабаритных энергосредств необходимо учитывать тяговое сопротивление сельскохозяйственных машин, которые предполагается с ними аг регатировать. То есть необходимо определить среднее значение тягового coat- противления (постоянная составляющая) и учесть характер и амплитуду его колебаний (вероятностная составляющая). 29.Баланс мощности МТА Мощность тракторного двигателя расходуется на выполнение полезной работы, преодоление внешних и внутренних сил сопротивления. Распределение мощности двигателя на преодоление различных видов сопротивлений называется балансом мощности, или рабочим балансом МТА (при равномерном движении), т.е. Ne = NM + Nf + Nδ + Nα + Ne вом + Nt. (1) Потери мощности в трансмиссии (кВт) связаны с преодолением сил трения в подшипниках, шестернях, механизмах гусеничной цепи. Их можно определить по формуле NM = Ne (1 - η мг),(2) где η мг — КПД трансмиссии (для колесных тракторов — в пределах 0,90—0,92, для гусеничных — 0,86—0,88; на его значения оказывают влияние такие эксплуатационные факторы, как качество смазки, технического обслуживания и регулировки). Потери мощности на перекатывание трактора связаны с образованием колеи ходовым аппаратом, а также с деформацией шин, преодолением сил трения в подшипниках колес (гусеницах) и др. Эти потери (кВт) зависят от скорости движения агрегата: Nf = Pf • vp = G• fт• vp(3) Здесь Pf = G • fr — сопротивление перекатыванию трактора, кН; vp — рабочая скорость агрегата, м/с. Потери мощности на буксование (кВт) обусловлены недостаточным сцеплением ходового аппарата с почвой. При этом почва сдвигается, что сопровождается буксованием и снижением поступательной скорости движения трактора: Nδ = Ne • η мг • δ/100.(4) где δ — буксование, %. Потери мощности (кВт) на преодоление трактором подъема можно определить, если известны сила сопротивления подъему Р(, и скорость движения агрегата: Nα = Pf • vp = G • vp • i /100 (5) Мощность Ne вом, которая расходуется двигателем на привод механизмов через ВОМ, рассчитывается по формуле: Ne вом = N вом / η вом (6) Полезная (тяговая) мощность (кВт), т.е. мощность, которая расходуется на тягу рабочих машин, зависит от условий работы. Для тяговых и тягово-приводных агрегатов Nt = RM • vp = vp (ko • b+ GM • i/100) (7) для транспортных агрегатов Nt = RM • vp = vp (ko • b+ GM • i/100) (8) " Затраты мощности зависят от скорости движения агрегата, поэтому баланс мощности можно изобразить с помощью графика (рис. 1). Если нанести на графике кривую удельного тягового расхода топлива, то увидим, что минимальный удельный расход соответствует максимальному значению тяговой мощности Nt max . Это очень важно для правильного комплектования машинно-тракторных агрегатов и выбора загрузочных и скоростных режимов их работы.  Рис. 1. График зависимости затрат мощности от скорости движения трактора Производительность агрегата пропорциональна тяговой мощности Nt, а расход топлива на единицу выполненной работы пропорционален удельному расходу. Значит, наибольшей производительности и экономичности (по расходу топлива) можно достичь, когда трактор работает в режиме максимальной тяговой мощности Nt max (или близкой к ней) при минимальном удельном расходе топлива gT min , т.е. при оптимальных рабочих скоростях. Для современных гусеничных тракторов эти скорости примерно равны 2,0—2,5 м/с, а для колесных — 3—4 м/с. Однако при комплектовании агрегатов не всегда удается этого добиться, так как могут быть ограничения рабочей скорости по агротехническим требованиям (качество работы), а также из-за превышения допустимого буксования и др. 30.Эксплуатационные св-ва двигателей тракторов и с/х машин.Осн. Экспл показатели – эффективная мощность N, вращающий момент М, частота вращения колн вала n, часовой GT и уд расход ge топлива, кот связаны между собой след соотношениями: N = 0.105Mn, ge = GT/N. Экспл показатели двигателя, трактора и МТА в целом зависят от коэф-та загрузки (степени использования мощности) EN = Ni/NH 2. |