Обоснование и разработка теоретической схемы базирования Схема базирования детали в приспособлении должна обеспечивать выполнение заданных чертежом размеров. По чертежу необходимо выдержать размер 17±0,1. С целью придания заготовке совершенно определенного положения в пространстве ее необходимо лишить шести степеней свободы, т.е. возможности перемещения вдоль трех осей координат, а также поворота вокруг этих осей. С этой целью необходимо и достаточно ориентировать заготовку по шести опорным точкам(рисунок 2.3.1). 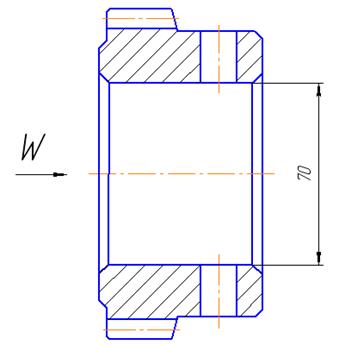 Рисунок 2.3.1. – Схема базирования заготовки Для данной заготовки базирование осуществим плоскости А и отверстию ВØ70H7. Три координаты, определяющие положение детали относительно плоскости XOY, лишает ее трех степеней свободы – возможности перемещаться в направлении оси OZ и вращаться вокруг осей OY и OX (1,2,3). Базируя заготовку по плоскости А она тем самым лишается трех степеней свободы, а именно перемещения вдоль оси OY и вращения вдоль осей OZ, OX. Базируя по отверстию Б заготовка устанавливается на цилиндрической оправке, что лишает ее двух степеней свободы, а именно перемещения вдоль осей OZ и OX. Чтобы лишить заготовку шестой степени свободы (вращения вдоль OY) применим винтовой зажим. 2.4 Расчет режимов резания Исходные данные: 1) Обрабатываемый материал – Сталь 40Х Твёрдость 170-229HB кгс/мм2. Предельная прочность = 600МПа. Предельная текучесть =720 МПа. 2) Режущий инструмент определяем в пункте 2.2. пояснительной записки. Рассчитаем режимы резания и произведем нормирование технологических переходов по обработке отверстия. В связи с тем, что расчет режимов резания и основного времени для всех технологических переходов будет аналогичным, его целесообразно выполнить в форме таблицы 3. Предварительно определим характеристику рядов подач и чисел частот вращения шпинделя вертикально-сверлильного станка. Для станка 2Н118 пределы подач 0.1…0.56 мм/об, число подач- 6 (по паспорту станка). Определим глубину резания по формуле: t=0.5*D где D - диаметр обработки t=7мм [3, с 252] – показатель знаменательного ряда, = 0,1 мм/об = 0,56 мм/об  По источнику [7 с,104] = 1,41. Рассчитаем Sоn подачу на оборот нормативную [7 с, 126] Sон = 0,3 *1,3=0,39мм/об (при стали HB<229 умножают на1,3).  Где Somin- минимальное значение ряда подач, мм/об; Sон- нормативная подача на оборот при сверлении, мм/об. Принятое значение подачи [3, с 252] Принимаем значение Sо =0.28мм/об. Определение периода стойкости инструмента по нормативам T, мин. По карте С – 3 [7] период стойкости сверла определяется по формуле: T=Tм×λ Где: Тм – период стойкости в минутах машинной работы станка, Тм=30 мин. λ – коэффициент времени резания каждого инструмента, равный отношению длины резания Lрез. этого инструмента к длине рабочего хода Lр.х λ=40/118=0,33 Т=30×0,33=10,2 мин Рассчитываем длину рабочего хода Lрх=Lрез+Y+Lдоп , мм, [7 с,104] где Lрез – длина резания, мм, Lрез=20*2=40мм по рисунке (2.4.1) Y – величина врезания и перебега, мм. [7 с,303] Y=y1+y2, где y1 и y2 величина врезания и перебега соответственно. y1=4мм; y2=4мм Y=8мм. Исходя из рисунка (2.4.1) Lдоп=70мм. Согласно рисунку 2.4.1длина рабочего хода при сверлении составит Тогда Lрх = 40 + 8+70 = 118 мм. S W  Рисунок 2.4.1 – Схема для определения длинны рабочего хода Определяем скорость резания по формуле Скорость резания для сверления определяется по формуле [7 с.105], где – табличные значения скорости, = 24,5 м/мин. – коэффициент, зависящий от обрабатываемого материала, = 0,9, – коэффициент, зависящий от стойкости инструмента, = 1,25 – коэффициент, зависящий от отношения длины резания к диаметру, =1. Тогда скорость м/мин. Определяем ряд чисел частот вращения шпинделя Число ступеней скоростей =9  [3 с, 252] Определим частоту вращения шпинделя станка , об/мин. , об/мин. Пользуясь знаменателем , получим ряд чисел частоты вращения шпинделя: 180; 253,8; 357,86; 504,58; 711,46; 1003,16; 1414,46; 1994,38; 2800. Из полученного ряда выбираем ближайшее меньшее значение частоты вращения шпинделя мин -1 . Определяем основное время Т0 , мин. [7 с,122], где – длина рабочего хода, мм; – подача на оборот принятая, мм/об.; – принятая частота вращения шпинделя, мин-1. T0=118/(504,58*0,28)=0,83 мин. Проверим правильность выбора станка по мощности резания и по осевой силе. Проверку производим для операции сверления отверстия диаметром 14 мм. Осевая сила , [7 с, 125] где – табличное значение осевой силы, Н; при S0 = 0,141 мм/об = 410 Н. – коэффициент, зависящий от обрабатываемого материала, = 1; Н Наибольшее усилие подачи станка равно 5600 Н. Мощность резания , кВт [7 с,126] где – значение мощности резания, кВт = 1,9 кВт; – коэффициент, зависящий от обрабатываемого материала, = 1; ,кВТ Наибольшая мощность станка =2,2 кВт. Станок подходит для данной операции. |