ПОЗНАВАТЕЛЬНОЕ Сила воли ведет к действию, а позитивные действия формируют позитивное отношение Как определить диапазон голоса - ваш вокал
Игровые автоматы с быстрым выводом Как цель узнает о ваших желаниях прежде, чем вы начнете действовать. Как компании прогнозируют привычки и манипулируют ими Целительная привычка Как самому избавиться от обидчивости Противоречивые взгляды на качества, присущие мужчинам Тренинг уверенности в себе Вкуснейший "Салат из свеклы с чесноком" Натюрморт и его изобразительные возможности Применение, как принимать мумие? Мумие для волос, лица, при переломах, при кровотечении и т.д. Как научиться брать на себя ответственность Зачем нужны границы в отношениях с детьми? Световозвращающие элементы на детской одежде Как победить свой возраст? Восемь уникальных способов, которые помогут достичь долголетия Как слышать голос Бога Классификация ожирения по ИМТ (ВОЗ) Глава 3. Завет мужчины с женщиной 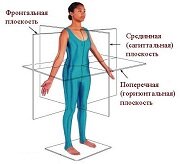
Оси и плоскости тела человека - Тело человека состоит из определенных топографических частей и участков, в которых расположены органы, мышцы, сосуды, нервы и т.д. Отёска стен и прирубка косяков - Когда на доме не достаёт окон и дверей, красивое высокое крыльцо ещё только в воображении, приходится подниматься с улицы в дом по трапу. Дифференциальные уравнения второго порядка (модель рынка с прогнозируемыми ценами) - В простых моделях рынка спрос и предложение обычно полагают зависящими только от текущей цены на товар. | Параметри якості діелектричних плівок КУРСОВА РОБОТА З дисципліни “ТЕХНОЛОГІЧНІ ОСНОВИ ЕЛЕКТРОНІКИ” Тема роботи: “Формування діелектричних шарів при виробництві напівпровідникових ІМС” Виконала: Малашенко А. Г. ФЕ - 01 Перевірив: Опанасюк Н.М. Суми - 2012 ЗМІСТ Вступ……………………………………………………………………………..3 1Інтегральна мікросхема…………………………………………….......4 2 Окислення………………………………........................................................5 3 Методи нанесення тонких плівок………………………………………………….13 4 Діелектричні плівки та параметри їх якості....……………………………….26 5 Технологічне устаткування для отримання діелектричних плівок………....30 Висновки………………………………………………………………………..34 Список використаної літератури………………………………………..........35 ВСТУП Сучасна людина більшою мірою, ніж це здається на перший погляд, користується у своєму повсякденному житті - у побуті, професійній діяльності - досягненнями електроніки - лазерами, різнофункціональними сенсорами, пристроями, насиченими інтегральними мікросхемами, напівпровідниковими елементами тощо. Створення, розвиток і широке впровадження в промисловість планарной технології кремнієвих ІМС значною мірою зобов'язане тому, що на поверхні кремнію можна сформувати діелектричну плівку, що володіє прекрасними маскуючими і пасивуючими властивостями. При цьому найбільш поширеним і якісним діелектриком був і залишається діоксид кремнію. Використання окисленої поверхні кремнію як маска обумовлене хімічною інертністю діоксиду кремнію SiO2 по відношенню до багатьох реагентів. Досить сказати, що плівка SiO2 розтворима тільки в плавиковій кислоті і концентрованих розчинах лугів. Проте роль таких плівок не вичерпується застосуванням їх як маски при формуванні елементів ІМС і захисту цих елементів від впливу зовнішніх дій (домішок, вологи, випромінювання і т. п.). Діелектричні плівки служать також для електричної ізоляції окремих приладів і комутаційних (особливо багатошарових) провідників в ІМС. Нарешті, не менш важливе використання плівок SiO2 як діелектрик підзатвора в МДС-ІМС. Такі пристрої називають МОН (метал — оксид — напівпровідник) -ІМС. Окислення Окислення або оксидування - один із основних і відповідальних процесів, які використовуються при виготовленні інтегрованих мікросхем. Окислення застосовується для формування маскуючого шару при локальній обробці і пасивації поверхні готової мікросхеми. Процес окислення поверхні напівпровідникових пластин можна проводити: за рахунок взаємодії кисню з матеріалом пластин, нарощуючи окисел в результаті реакцій піролітичного розкладу; анодного окислення у розчинах електроліту; окислення у тліючому розряді. Процес окислення, інтенсифікований нагрівом до високих температур, прийнято називати термічним окисленням. Кремній має високу спорідненість з киснем, і тому старанно очищена його поверхня вже при кімнатній температурі покривається шаром окислу, товщиною близько 10-15 Ǻ. Термічне окислення кремнію проводять при високих температурах в одній з таких атмосфер: сухого кисню; сухого кисню з додатком зволожених газів (кисню, азоту, аргону); сухої кисню і водяної пари при атмосферному чи підвищеному тиску; в суміші хлористого водню і кисню (HCI+O2). Окислення в атмосфері сухого кисню проводиться при температурі кремнієвої пластини 1000-1200°С в установці, схем якої показана на рис. 1. Чим вища температура пластини, тим більша швидкість формування окисного шару. Наприклад, для формування окисного шару, товщиною 0,5 мкм при Т=1000°C треба біля 1800 хв, а при Т=1200°С лише 320 хвилин. Значно зменшується час окислення, якщо збільшувати тиск кисню в реакторі.  Рис. 1 – Схема установки для термічного окиснення кремнію Після якісного очищення підготовлені пластини завантажують в кварцевий реактор установки, через який продувають сухий кисень. Процес окислення здійснюється за рахунок дифузії кисню в кремнієву пластину і хімічної взаємодії його з кремнієм за реакцією: SiO2+O2 = SiO2 (1) Недоліком цього процесу є великий час окислення. Щоб зменшити його, було запропоновано до сухого кисню додавати зволожуючі гази чи водяну пару. Із застосуванням зволожуючих газів чи водяної нари значно зменшується час окислення, зокрема, щоб одержати плівку товщиною 0,5 мкм при Тпл=1200°С і при тиску водяної пари 105 Па, час окислення буде в межах 240-300 хв. Якщо збільшиш тиск водяної нари до 2,5·106 Па, навіть при Тпл=900°С плівку, товщиною 0,5 мкм, можна одержати за 10 хв. Збільшення тиску зволожуючого газу в реакторі дає можливість знизити температуру окислення до 800-900°С та значно зменшити час окислення (в десять і більше paзів), а значить зменшити кількість домішок в окислі, які знижують його якісні характеристики. Отже, застосування зволожуючих газів чи парів води значно скорочує час окислення (рис. 2).  Рис. 2 – Залежність товщини оксиду кремнію від часу та температури при окисленні в парах води (а) і в сухому кисні (б) В установках для термічного окислення передбачається під´єднання до газової магістралі зволожувача, наповненого парами деіонізованої води. У випадку застосування зволожених газів (кисню, азоту, аргону), їх необхідно пропускати через зволожувач. При використанні для окислення пари треба, щоб вода не конденсувалася на стінках реактора. Процес термічного окислення можна сумістити з другою стадією дифузії, яка вимагає високої температури для "розгону" домішки. Тривалість окислення можна істотно зменшити, поліпшивши при цьому діелектричні властивості окислу, за рахунок використання суміші HCl+O2. Такий процес при окисленні називають хлоруванням. Швидкість окислення при хлоруванні збільшується за рахунок наявності хлору в технологічному середовищі окислювача, що приводить до створення напруги в гратці окисного шару і полегшує дифузію кисню в глибину пластини. Окислення в атмосфері НС1+О2 проводять при температурах 900-1100°С. Всі методи термічного окислення дають можливість отримати тонкі окисні шари (долі мікрона) з добрими захисними діелектричними властивостями. Піроліз силанів використовують для отримання товстих плівок окислу кремнію (SiO2) при низьких температурах, коли високотемпературне окислення може привести до порушеня геометричних розмірів вже сформованих в пластині дифузійних ділянок. Піроліз силанів, залежно від вимог до температури процесу і якості окисного шару, проводиться двома методами: піролізом в потоці газу-носія та вакуумі. Піроліз у потоці гaзy-носія (наприклад, азоту), проводять в однозонних печах (в таких, як проводять термічне окислення), де передбачається подання з певною швидкістю суміші газів: силан-кисень (SiH4+O2) чи тетраетоксилану. Процес окислення силану переважно проходить при температурах 250-350°С з осадженням окислу кремнію на кремнієвих пластинах. Хімічну реакцію окислення силану з утворенням SiO, можна записати: SiH4+O2 = SiO2+H2O (2) У результаті розкладу силанів отримують окисні шари з добрими захисними властивостями. Параметри плівок при цьому дуже залежать від режимів технологічного процесу і неправильно вибрана швидкість подачі газу призводить до нерівномірності окисного шару по товщині. Пояснюється це складністю отримання ламінарного потоку без завихрень, який забезпечує рівномірність плівки всією площею осадження. Цей недолік методу піролітичного розкладу усувається, якщо піроліз проводити у вакуумі. Якість окисних шарів значно підвищується за рахунок піролізу в чистому середовищі. Особливість цього методу - це можливість проведення окислення при температурі 250-350°С. Товщина окисного шару залежить від швидкостей подачі силану і кисню в реактор. На рис. 3 показано, що з ростом швидкості подачі силану товщина плівки росте лінійно, але швидкість подачі кисню обмежує її ріст. Піролітичний розклад тетраетоксилану проводять при температурі 730-750°C: Si(OC2H5)4 = SiO2+4C2H2+2H2O (3) 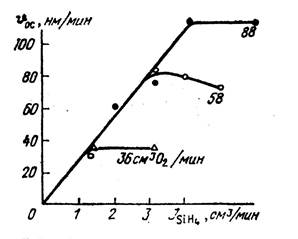 Рис. 3 – Залежність швидкості росту оксиду кремнію від швидкості потоку силану при реакції SiH4 та O2 Мегод одержання SiO2 з силану є відносно низькотемпературним, але сам силан дуже токсичний і вибухонебезпечний. Тому у виробництві надають перевагу більш високотемпературною методу. Для проведення вакуумного піролізу використовую і установки, які містять від двох до чотирьох реакторів. У них забезпечується створення вакууму 30-60Па і передбачено конструктивний фланець, через який проводять завантаження пластин у реактор. Промислові установки комплектуються автоматичними пристроями, які виконують всі операції від завантаження до вивантаження касет з пластинами. Освоєні основні типи таких установок: для піролізу при високих температурах використовуються реактори без роздільного введення газів; при низькотемпературному піролізі передбачено роздільне введення гачів і екранування човника з пластинами для отримання рівномірних за товщиною шарів. В інтервалі температур 800-900°С отримують плівки SiO2 при використанні системи SiH4+N2O+N2 та SiH2Cl2+N2O. Система SiH4+N2O+N2 не знайшла широкого застосування через малу швидкість росту плівок. Система SiH2Cl2+N2O забечнечує однорідні за товщиною шари SiO2 і при великій швидкості їх росту. Швидкість росту в даному випадку залежить від температури і співвідношення N2O/SiH2Cl2. Кількість закису азоту (N2O) повинна бути у 2-4 рачи більшою, ніж дихлорсилану (SiH2Cl2). Низькотемпературні (при 360-460°С) плівки SiO2 отримують в системі SiH4+O2+N2 в установках з розділеним введенням газів. Максимальна швидкість осадження досягається при відношенні газів O2/SiH4, рівною 3. Окисні шари в процесі низькотемпературного піролізу можна легувати фосфором чи миш'яком, якщо використовувати системи SiH4+PH3+O2+N2 чи SiH4+AsH3+O2+N2. Піроліз силанів можна використовувати і для отримання шарів SiO2 на поверхні арсенід-галієвих пластин. Недоліком методу піролізу силанів є складність створення контрольованої атмосфери в реакційній трубі. Крім вище згаданих методів для отримання окисних шарів використовують: анодне окислення у розчинах електроліта; окислення в тліючому розряді; реакційне розпилення. Останній метод знайшов широке застосування для нанесення плівок SiO2 на поверхню арсенід-галієвих пластин як маскуючого покриття при локальній обробці. Останнім часом ведуться інтенсивні пошуки способів низькотемпературного одержання окисних плівок для того, щоб хоча б частково вирішиш проблеми зв’язані з прогином і коробленням напівпровідникових пластин, перерозподілом домішок, генерацією дефектів і їх розповсюдженням. З цією метою для інтенсифікації низькотемпературного окислення можна використовувати стимуляцію лазерним променем. Пропонується проводити процес окислення в атмосфері кисню при тиску 10 Па. Під дією лазерного променя енергією 5мДж і тривалістю імпульса 5нс підкладка швидко нагрівається аж до температури плавлення. Лазерний промінь може бути сфокусований тільки на те місце, де потрібно одержати окисний шар. Гусита енергії лазерного променя, сфокусованого па поверхню підкладки в площу розміром, 1,0 х 0,5 мм, досягає 0,9Дж/см2 і при частоті повторення мпульсів 100 Гц і загальній дії променів в 1 мкс. Під дією лазерного променя нагрівається тільки та частина, куди спрямований промінь, а неопромінена частина підкладки залишається холодною. Для зменшення напруг, які виникають в підкладці при швидкому нагріві і охолодженні, проводять підігрів з допомогою резистивного нагрівача до температури 400°С. Дія імпульсів разом із скануванням, сфокусованим лазерним променем для створення конфігурації елементів, приводить до утворення окисною шару. Такий метод окислення створює можливість виключити з технологічного циклу дві операції: маскування і травлення, яке застосовують для усуненню окислу з певної частини пластин. Метод забезпечує можливість контрольованого управління і створення заданої товщини окислу шляхом зміни густини енергії лазерного променя. Вибір методу окислення залежить від того, на якій стадії технологічної обробки знаходиться напівпровідникова пластина і від її розмірів. На початкових стадіях технологічного процесу можна використовувати термічне окислення. На наступних операціях необхідно по можливості скорочувати час окислення та зменшувати температуру. Використання великого діаметру пластин робить їх дуже чутливими до механічних навантажень, причиною виникнення яких є внутрішні механічні напруження системі Si-SiO2, як результат перепадів температур при проведенні технологічних операцій і невідповідності коефіцієнтів лінійного розширення. Особливо це відчутно, коли окисел наноситься на епітаксійний шар, що веде до зміни товщини цього шару. Виникнення внутрішніх механічних напружень в системі кремній - окис кремнію приводить до згинів і короблення пластин, що спричиняє зменшення виходу придатних мікросхем. Чим вища температура окислення, тим більші механічні напруження. Але окислення кремнію у вологому кисні веде до їх зменшення більше, ніж при використанні сухою кисню. Зменшуються напруження також, якщо в процесі одержання SiO2 легують бором чи фосфором. Ці домішки наближають коефіцієнти лінійного розширення SiO2 і кремнієвої підкладки, що зменшує термічні напруження. Експериментальні дослідження підтверджують, що внутрішні механічні напруження в системі Si-SiO2 переважно носять термічний характер. Також внаслідок дифузії атомів кисню в гратку кремнію при проведенні термічного окислення утворюється кремній-кисневі тетраедри. Утворення таких тетраедрів приводить до збільшення об'єму гратки, що супроводжується утворенням в плівці SiO2 стискаючих напруг. Все це змінює механічні властивості структури, зокрема, модуль Юнга плівки SiO2 буде набагато вищий, ніж основного матеріалу. Це підтверджують теоретичні розрахунки і експериментальні дані, одержані методом голографічної інтерферометри. Наявність деформацій згину пластин ускладнює проведення таких технологічних операцій: фотолітографії; механічної обробки неробочої частини пластини; дифузії та інших. В таких випадках, коли відома величина механічних напружень в системі Si-SiO2, можна прогнозувати величину деформацій, їх вилив на якість технологічного процесу, вибирати оптимальні режими процесу, при яких одержуються мінімальні згини і викривлення пластин. Тому, починаючи від механічної обробки напівпровідникових пластин, на всіх наступних технологічних операціях необхідно вести контроль не тільки електрофізичних, а також механічних характеристик напівпровідникових пластин. Параметри якості діелектричних плівок Залежно від області застосування діелектричних плівок у виробництві ІМС до їх параметрів якості пред'являються різні вимоги. При використанні SiO2 як технологічної маски для її травлення зазвичай застосовуються розчини плавикової кислоти (HF) у воді з різними добавками. Було встановлено, що плівки, вирощені термічним окисленням, мають найменшу швидкість розчинення (як щільніші), а плівки, вирощені термовакуумним випаровуванням, — найбільшу (як менш щільні). Якщо отримані піролізом плівки відпалювати при високих температурах, то можна досягти такої ж якості їх, як і при термічному окисленні, що видно з рис. 4.  Рисунок 4 – Залежність швидкості травлення плівки SiO2, отриманий піролізомтетроетоксилану в аргоні, від її товщині: 1 – осадження плівки при Тос=750°С; 2, 3, 4 – відпалення плівки в парах води при tот=10, 20, 30 хв відповідно; 5 – термічний оксид Швидкість травлення плівок залежить від температури розчинення, мало залежить від швидкості перемішування розчинника і практично не залежить від того, чи піддавалися перед окисленням пластини механічній або хімічній поліровці і як проводилося вирощування діоксиду кремнію - в сухому або вологому кисні або в парах води. У технології виготовлення ІМС важливо, щоб швидкість розчинення мало залежала від концентрації розчинника. Для вирішення цього завдання були створені так звані буферні травники, до складу яких входить фтористий амоній NH4F. Наприклад, травник, що складається з 10см3 48%-ного водного розчину HF і 100 см3 40%-ного водного розчину NH4F, розчиняє термічно вирощений діоксид із швидкістю 20 нм/хв. Наявність домішок підвищує швидкість травлення плівок SiO2, особливо коли домішки потрапляють в SiO2 з газової фази. В процесі обробки фотолітографії одночасно травляться ділянки діоксиду кремнію, що не містять і містять домішки. Неоднакова швидкість травлення цих ділянок може призводити до підтравлювання, що викликає значне розширення областей, з яких віддаляється оксид, за рахунок проникнення травника в бічному напрямі під шар резисту. У технології ІМС часто хімічна обробка діоксиду проводиться на всій поверхні пластини без захисту окремих ділянок фоторезистом. При цьому наявність в діоксиді домішок там, де їх не повинно бути, може привести до локального збільшення швидкості травлення, а отже, видаленню потрібної ділянки діоксиду, нехай навіть дуже невеликого розміру. Це може стати надалі причиною виникнення браку. В процесі створення шарів SiO2 на поверхні кремнієвих пластин в них можуть виникати різного роду дефекти, які надалі приводять до погіршення або нестабільності параметрів елементів ІМС. Розглянемо коротко основні види таких дефектів. Ці дефекти можуть мати атомні або більші розміри. Перші обумовлені недоліком або надлишком іонів кисню, наявністю в діоксиді атомом або іонів сторонніх домішок і утворенням ненасичених зв'язків на межі між кремнієвою підкладкою і шаром діоксиду. Крупніші дефекти - це пори чи канали в оксидному шарі, мікротріщини або межі між кристалічними і аморфними ділянками слою. Багато дефектів подібного роду виникають в оксидному шарі при термічному окисленні підкладок, що мають порушення на поверхні. У місцях розташування цих порушень можуть утворитися дефекти типу точкових проколів або ділянки з підвищеною швидкістю травлення. Такі дефекти і приводять згодом до погіршення параметрів ІМС. На підкладках достатньо високої якості можна виростити SiO2 без подібних дефектів. Залежно від умов термічного окислення на поверхні кремнію може бути сформований не тільки аморфний, але й кристалічний діоксид кремнію (у модифікації α і β кристобаліту). Його поява пов'язана з вищою температурою окислення. Надалі при термообробках можуть з'являтися тріщини в кристалічних шарах SiO2 і на межах між кристалічними і аморфними ділянками. Одна з причин утворення дефектів в шарах SiO2 і на їх межі з кремнієм - механічна напруга. Така напруга з'являється в шарах, отриманих різними способами: термічним нарощуванням, піролізом Si(OC2H5)4 і низькотемпературним окисленням силана. Напруга виникає із-за відмінності термічних коефіцієнтів, розширення підкладки і оксидного шару; змін, що відбуваються в шарах при подальших термообробках; деяких явищах, пов'язаних з характером зародження і зростанням шару, але не пов'язаних з відмінністю коефіцієнтів розширення шару і підкладки (так звані «власні» напруження). Напруга в шарі SiO2, вирощеному на кремнієвій підкладці при високій температурі, є такими, що стискають, оскільки термічний коефіцієнт розширення кремнію в кілька разів вище, ніж у SiO2. Напруження має значення порядку 108 Па. Очевидно, що значення напруги і її роль тим більша, чим більша товщина шару. Напруга в шарах призводить до появи в них тріщин і відшарування їх від підкладки. Малі напруги можуть не викликати цих дефектів, але сприяти концентрації вакансій біля границі розділу з підкладкою, що приводить до зміни щільності енергетичних перебувань на межі між оксидом і кремнієм. Вплив напруги в шарі SiO2 позначається при його обробці фотолітографією. Неоднорідний розподіл напруги призводить до неоднорідного травлення шару, яке спостерігається як в місцях концентраїні напруги, так і в місцях скупчення забруднення. Забруднення можуть з'являтися на підкладці перед окисленням або потрапляти на поверхню SiО2 в подальших технологічних операціях. В результаті після часткового травлення в шарі SiО2 можуть утворитися точкові отвори - проколи. Ці проколи - одні з серйозних джерел браку в технології ІМС. З погляду дефектності найкращими є шари, вирощені термічним окисленнем на вільних від дефектів підкладках, найгіршими - отримані анодним окисленням в розчинах електролітів без подальшої термічної обробки. Значення щільності плівок SiО2, вирощених різними способами, практично мало відрізняються і складають 2,2 г/см3. Питомий електричний опір дуже сильно залежить від технології отримання плівок, особливо від концентрації домішок і дефектів в них. Кращі плівки мають питомий опір 1015-1016 Ом·см, гірші, - 1012 Ом·см. Діелектрична проникність складає від 3 до 3,8 залежно від методу вирощування плівок. Електрична міцність змінюється від 106 до 107 В/см, але може різко зменшуватися при появі в плівках дефектів. Для плівок, використовуваних в якості підзатворних діелектриків в МДП-ІМС, всі параметри повинні бути якнайкращими. При формуванні оксидних плівок важливо також брати до уваги зміну об'ємів, які зайняті оксидом і початковим кремнієм, як показано на рис. 5.  Рисунок 5 – Зміна об'ємів шарів при уитворенні оксиду термічним окисненням кремнію: 1 – оксид; 2 – початкова поверхня кремнію; 3 – границя оксид-кремній; 4 – кремнієва пластина |