Производство стали в электрических печах Преимущества электроплавки.Электроплавка — наиболее совершенный способ получения литой стали. Быстрый подъем и точное регулирование температуры, высокий нагрев и возможность создания окислительной, восстановительной, нейтральной атмосферы или вакуума в плавильном пространстве — все это позволяет выплавлять сталь любого и точного химического состава, с особыми физическими и химическими свойствами, раскислять сталь с образованием минимального количества неметаллических включений – продуктов раскисления. Поэтому электропечи используют для выплавки конструкционных, высоколегированных, инструментальных, специальных сталей и сплавов. Возможность получения высоких температур в электропечах допускает применение сильно известковых шлаков, которые способствуют почти полному удалению из металла серы и фосфора. В атмосфере электропечи мало кислорода, что позволяет легко вести восстановительный процесс раскисления и получать сталь, свободную от вредной закиси железа. Электроплавка дает возможность получения высококачественных сталей, содержащих в своем составе такие тугоплавкие элементы, как вольфрам, ванадий, молибден, расплавление которых в других печах затруднительно. В настоящее время большинство сортов специальных сталей выплавляется в электропечах. Работа электропечей и их виды.Электропечи могут работать как на жидкой, так и на твердой шихте. Работа на твердой шихте (лом, стружка, отходы проката) в основных печах является наиболее распространенной. Процесс плавки включает: 1) расплавление пихты; 2) окисление примесей; 3) раскисление стали; 4) удаление серы; 5) доводку стали до требуемого химического состава. Расплавление шихты и порядок выгорания примесей в электропечи аналогичен мартеновскому процессу. По мере расплавления металла происходит окисление железа и содержащихся в нем примесей. В качестве окислителей добавляют железную руду и окалину. После окисления примесей образуются разные химические соединения, которые переходят в шлак. В качестве шлакообразующих материалов в печь вводят известь или известняк и плавиковый шпат—флюорит (Тпл=1378°С). Современные электрические печи для выплавки стали можно разделить на две группы — дуговые и индукционные. Дуговые электрические печи. В дуговых печах теплота получается от горения электрической дуги с температурой до 6000 °С, образующейся непосредственно между электродами (печи с «независимой» дугой) или между электродами и металлической ванной (печи с «зависимой» дугой). Дуговая плавильная электропечь (рис. 5, а) питается трехфазным переменным током и имеет три цилиндрических электрода 9 из графитизированной массы. Электрический ток от трансформатора кабелями 7 подводится к электрододержателям, а через них – к электродам 9 и ванне металла. Рабочее напряжение 160 – 600 В, сила тока 1 – 10 кА. Во время работы печи длина дуги регулируется автоматически путем перемещения электродов. Подину 12 печи набивают огнеупорной массой. Плавильное пространство ограничено стенками 5, подиной 12 и сводом 6 из огнеупорного кирпича. Для управления ходом плавки имеются рабочее окно 10 и лётка для выпуска готовой стали по желобу 2 в ковш. Печь загружают при снятом своде. После загрузки шихты электроды через отверстия в своде опускаются и включается ток. При вертикальном положении электродов 4 (рис. 5, б) электрическая дуга 3 образуется между каждым электродом и металлом 1. Металлическая часть шахты служит промежуточным проводником. Печи этого типа получили преимущественное распространение. Такая печь состоит из металлического кожуха цилиндрической формы с плоским или сферическим дном 6, а внутри футерована основным (магнезитовый, магнезитохромитовый) или кислым (динасовый) огнеупорным кирпичем. С помощью особого механизма 2 печь можно устанавливать в наклонное положение. Если надо выпустить шлак, печь наклоняется на 10 … 15° в сторону рабочего окна 10. При выпуске металла печь наклоняется на 45° в сторону выпускного отверстия.  Рис. 5. Дуговая электропечь с вертикально расположенными электродами Электроды (угольные или графитовые) проходят через съемочный свод 5. Диаметр их 200—600 мм; длина до 3 м. Графитовые электроды более устойчивы при высоких темпера турах, имеют меньшее электросопротивление, чем угольные, и поэтому их применение в печах более целесообразно. Емкость современных дуговых электропечей колеблется от 250 кг до 400 т. Преимущества дуговых электропечей: 1) возможность получения самых высококачественных углеродистых и легированных сталей (конструкционных, инструментальных, жаропрочных, жаростойких) и тугоплавких сплавов с минимальным количеством газов, вредных примесей неметаллических включений; 2) гибкость работы при всех режимах и характерах производства, с использованием твёрдой и жидкой завалки с любым количеством дешевого стального лома; 3) самый маленький угар металла и особенно легирующих примесей по сравнению со всеми плавильными агрегатами; 4) простота устройства, компактность, лёгкость обслуживания и относительная дешевизна печей. Основным недостатком дуговых печей является науглероживание стали углеродом электродов, поэтому выплавлять стали с очень низким содержанием углерода нельзя. Производство стали в дуговых электропечах.В зависимости от футеровки различают кислые и основные электропечи. Собственно все виды передела чугуна на жидкую сталь являются процессами рафинирования, заключающимися в том, что находящиеся в чугуне в качестве примесей элементы (углерод, кремний, марганец и др.) подвергаются окислению кислородом воздуха или соединениями, легко отдающими кислород. При этом получаются газообразные или жидкие окислы, не растворяющиеся в металле или растворяющиеся в очень ограниченном количестве. Газообразные соединения уходят в атмосферу, а жидкие образуют шлаки, всплывающие благодаря меньшему удельному весу на поверхность металла и таким образом отделяющиеся от него. Шихта для плавки в дуговых печах содержит 90...100 % стального скрапа и до 10 % передельного чугуна. При кислом процессе нельзя удалить серу и фосфор (требуются чистые исходные материалы). В основных электропечах эти элементы удаляются легко, поэтому основные печи применяются для получения высококачественных сортов стали. Кислые же печи применяются главным образом для получения стальных фасонных отливок. Плавка в основной электропечи начинается с расплавления загруженного скрапа и чугуна. По ходу выгорания примесей различают несколько вариантов плавки: 1) с полным окислением; 2) с частичным окислением; 3) без окисления. Плавка с полным окислением применяется, когда в шихте содержится значительное количество фосфора и других примесей. В этих условиях примеси не успевают выгореть за время расплавления и для ускорения процесса окисления в ванну добавляют железную или марганцевую руду. Введение марганцевой руды предохраняет ванну от перенасыщения окислами железа. МnО2 разлагается с образованием , которая при соединении с углеродом дает СО по реакции: 2.23 Вследствие выделения СО ванна «кипит». Процесс получения стали в основной электропечи с полным окислением распадается на несколько периодов. В течение окислительного периода (кипа) происходит удаление из металла фосфора и значительной части газов (поглощаемых металлом во время расплавления). В процессе расплавления происходит окисление фосфора с образованием . Одновременно идет окисление Mn, Si, С. Продукты окисления примесей образуют шлак. После образования шлака берут пробу металла: если в пробе окажется значительное количество фосфора, то шлак «скачивают». Скачивание (дефосфация) необходимо для предупреждения перехода фосфора обратно в металл. Когда металл окажется достаточно чистым по содержанию фосфора, удалением «черного» шлака заканчивается окислительный период плавки. После этого начинается восстановительный период, во время которого, кроме раскисления металла, производят удаление серы (десульфурацию) и доводят химический состав стали до заданного. При плавке с полным окислением окисляется значительное количество углерода и содержание его в металле понижается. Для повышения содержания углерода до нужного предела ванну науглероживают (на поверхность металла забрасывают куски малосернистого кокса, бой электродов и т. д.). Одна часть углерода идет на восстановление растворенной в металле FeO, а другая расплавляется в металле. При дуговой электроплавке в отличие от мартеновской и конвертерной раскисление ванны производится не столько за счет присадки раскислителей, сколько за счет раскислительного шлака. Различают два вида раскислительного шлака: белый (известковый) и карбидный. Для получения белого шлака в печь на поверхность ванны забрасывают шлаковую смесь: 76% СаО; 19% и 5% кокса. Белый шлак обеспечивает наиболее полное удаление серы: 2.24 2.25 CaS, образуемый в ходе этих реакций, нерастворим в металле и уходит в шлак. Доводка и окончание плавки заключаются в присадке в печь небольшого количества раскислителей — ферросилиция и алюминия. Легирующими примесями, вводимыми в ванну при электроплавке, являются Ni, Mo, Cr, W, V. Никель и молибден окисляются в меньшей степени и вводятся до полного раскисления ванны, хром и вольфрам вводятся в уже раскисленную ванну, а ванадий — перед самым выпуском металла из печи. Плавка с полным окислением производится только для получения стали с малым содержанием углерода. Для получения фасонного литья чаще применяют плавку с частичным окислением. Единственным источником кислорода при такой плавке служат ржавчина или окалина железного лома и проникающий в печь воздух. Применяется этот способ, когда содержание фосфора в шихте лишь незначительно выше допустимого в готовом металле, так что для окисления фосфора достаточно тех окислов железа, которые имеются в ванне после расплавления. При частичном окислении выгорает лишь кремний, а фосфор, марганец и углерод в большей или меньшей степени остаются в металле. Плавка без окисления производится при восстановительном режиме на чистом по сере и фосфору и незаржавленном ломе. Это по существу переплавка чистого скрапа, и ведется она главным образом при наличии в скрапе хрома, вольфрама и других ценных примесей для получения соответствующих сталей. Руды при этом в ванну не подают и шлака не спускают. Плавка в кислой дуговой электропечи протекает подобным образом, но имеет свои особенности: 1) футеровка—динасовый кирпич; 2) сера и фосфор не удаляются, печь работает без спуска шлака, который в основном состоит из силикатов железа и марганца; 3) раскисление ведется присадками, роль шлака заключается в связывании FeO и МnО кремнеземом. В конце процесса идет восстановление кремния, способствующее раскислению ванны. Индукционные электрические печи.Индукционные печи удобны тем, что не требуют электродов, благодаря чему предотвращается опасность науглероживания металла и упрощается управление печью. Кроме того, под действием магнитного потока (магнитных силовых линий) усиливается циркуляция металла, что очень важно для ускорения химических реакций и получения однородного металла. Индукционные печи позволяют получать более чистый металл, чем при плавке в дуговых печах. В индукционных печах выплавляются высококачественные легированные стали с малым содержанием углерода и различные сложные сплавы. В них выплавляют сталь и сплавы из легированных отходов методом переплава или из чистого железа и скрапа с добавкой ферросплавов методом сплавления. В них отсутствует электрическая дуга, что позволяет выплавлять сталь с низким содержанием углерода, газов и малым угаром элементов. 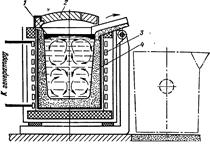 Рис. 6. Индукционная плавильная тигельная высокочастотная печь Однако эти печи менее распространены, главным образом в связи с тем, что плавка в них менее экономична, чем в дуговых электропечах. Также эти печи имеют малую стойкость футеровки, и температура шлака в них недостаточна для протекания металлургических процессов между металлом и шлаком. Принцип работы этих печей основан на выделении тепла при прохождении тока через проводник. Таким проводником является сама металлическая шихта. Индукционные печи бывают с железным сердечником и без него. Преимущественное распространение получили индукционные бессердечниковые печи, часто называемые высокочастотными. Индукционная тигельная плавильная печь (рис. 6) состоит из водоохлаждаемого (вода циркулирует внутри) спирального многовиткового индуктора 3 (обмотки из медной трубки), внутри которого находится тигель 4 с металлической шихтой. Через индуктор от мотор-генератора высокой частоты проходит однофазный переменный ток повышенной частоты (500 – 2500 Гц). Ток создает переменный магнитный поток, пронизывая куски металла в тигле, наводит в них мощные вихревые токи (Фуко), нагревающие металл 1 до расплавления и необходимых температур перегрева. Тигель изготовляют из кислых (кварцит) или основных (магнезитовый порошок) огнеупоров. Вместимость тигля 60 кг – 25 т. Для уменьшения потерь теплоты печь имеет съемный свод 2. Для питания печей могут применяться искровые генераторы. При вакуумной индукционной плавке индуктор с тиглем, дозатор шихты изложницы помещают в вакуумные камеры. Производство стали в индукционных печах.При загрузке тщательно подбирают химический состав шихты в соответствии с заданным, а необходимое количество ферросплавов для получения заданного химического состава металла загружают на дно тигля вместе с шихтой. После расплавления шихты на поверхность металла загружают шлаковую смесь для уменьшения тепловых потерь металла и уменьшения угара легирующих элементов, защиты его от насыщения газами. При плавке в кислой печи после расплавления и удаления плавильного шлака наводят шлак из боя стекла (SiO2). Металл раскисляют ферросилицием, ферромарганцем и алюминием перед выпуском его из печи. В индукционных печах с основной футеровкой выплавляют высококачественные легированные стали с высоким содержанием марганца, никеля, титана, алюминия, а в печах с кислой футеровкой – конструкционные, легированные другими элементами стали. В этих печах можно получать стали с низким содержанием углерода и безуглеродистые сплавы, так как в печах нет науглероживающей среди и науглероживания не происходит. При вакуумной индукционной плавке индуктор с тиглем, дозатор шихты и изложницы помещают в вакуумные камеры. Плавка, введение легирующих добавок, раскислителей, разливка металла в изложницы производятся без нарушения вакуума в камере. Таким способом получают сплавы высокого качества с малым содержанием газов, неметаллических включений, сплавы, легированные любыми элементами. Преимуществами индукционных печей по сравнению с дуговыми является возможность выплавки сталей с очень низким содержанием углерода так как нет науглероживания от электродов, очень малый угар легкоокисляющихся элементов: сталь характеризуется пониженным содержанием азота и высокой чистотой по неметаллическим включениям. Индукционные печи имеют высокую производительность и высокий электрический к.п.д. Раход электроэнергии 600 – 700 кВт/ч на 1т стали. Недостатками индукционных печей являются их малая ёмкость от десятка килограммов до 30 т по сравнению с дуговыми печами, высокая стоимость электооборудования, низкая стойкость основных тиглей (10…100 плавок). Шлак, нагреваемый только за счет тепла металлической ванны, имеет низкую температуру и, как следствие, малую химическую активность, что затрудняет удаление вредных примесей. Для плавки можно использовать только чистые шихтовые материалы, почти не требующие рафинирования. Основные технико-экономические показатели работы электроплавильных печей: - продолжительность плавки в крупной 100-тонной печи составляет 6 – 7 ч; - расход электроэнергии дуговых печей на 1 т стали около 600 кВт·ч; - расход электродов дуговых печей при этом составляет до 10 кг; - расход электроэнергии индукционных печей составляет 600 – 700 кВт·ч на 1 т стали; Разливка стали Разливка стали осуществляется из специальных сталеразливочных ковшей. Существует три способа разливки стали: 1) сверху; 2) снизу; 3) непрерывная. При двух первых способах сталь разливается в изложницы, отлитые из жаростойкого чугуна и представляющие собой толстостенную форму, открытую, как правило, сверху и снизу. Внутренние стенки изложниц выполняются с небольшой конусностью (расширяющиеся книзу или кверху), что облегчает извлечение слитка. Для удобства перемещения изложницы имеют цапфы или скобы. Перед заливкой стенки изложниц очищаются металлическими щетками и скребками. Для увеличения срока службы и предохранения от прикипания стали стенки предварительно подогретой до 80—100° изложницы покрывают смазкой из каменноугольной смолы или графита. При разливке сверху (рис. 7, а) разливочный ковш транспортируется электромостовым краном к подготовленным под заливку изложницам и останавливается над каждой из них. Изложницы, открытые снизу, устанавливаются перед заливкой на толстые чугунные плиты-поддоны и по периметру обмазываются огнеупорным материалом. После установки разливочного ковша над изложницей открывается стопорное устройство, и струя жидкого металла заполняет изложницу. Данная схема наиболее простая, но существует эффект разбрызгивания расплава в изложнице. При разливке снизу (сифонный способ) изложницы устанавливаются не на металлические поддоны, а на специальные керамические плиты (сифонный кирпич), соединенные между собой шамотными трубами (рис. 7, б). Эти плиты имеют внутри каналы, объединяющие их в единую литниковую систему. Через один общий литник можно отливать одновременно до 40 слитков. Такая схема разливки, при которой несколько керамических блоков объединяются в общую литниковую систему при помощи шамотных труб, получила название «паук». Существуют и другие способы установки изложниц для заливки сифоном. Отсутствие брызг при заполнении изложниц снизу позволяет получить более чистую поверхность слитка, но размывание металлом огнеупоров центрального литника и каналов сифонных кирпичей приводит к образованию большего количества неметаллических включений, чем при разливке сверху. Кроме этого, сифонная разливка имеет еще ряд недостатков: потеря металла в виде литниковой системы, более трудоемкая подготовка изложниц к заливке, однократное использование сифонного припаса (керамических (керамических плит, труб и др.). Однако, оценивая сравнительную экономичность обоих способов, следует иметь в виду, что дополнительные затраты на сифонную разливку полностью окупаются уменьшением стоимости зачистки поверхности слитков по сравнению с затратами на эту операцию при получении слитка способом заливки сверху.  Рис. 7. Разливка стали сверху (а) и снизу (б) Емкость изложниц от нескольких килограмм до 300 т и более. Некоторую особенность представляет получение слитков из кипящей стали, т.е. из стали, раскисление которой происходит в изложнице за счет взаимодействия углерода металла с растворенным в металле кислородом. Содержания FeO в такой стали достаточно для протекания реакции с образованием окиси углерода СО. Окись углерода СО, выделяющаяся в виде пузырей, создает впечатление кипения металла в изложнице. Одновременно сСО из стали выделяются и , растворимость которых в жидком металле при понижении температуры уменьшается. Таким способом получают малоуглеродистую сталь с содержанием от 0,05 до 0,25% С. Слиток кипящей стали имеет малую усадочную раковину, но значительное количество пузырей. При заполнении изложницы кипящей сталью необходимо в определенный момент прекратить выделение окиси углерода, так как в противном случае объем металла будет увеличиваться и над слитком образуется «шапка». Чтобы закрыть газам выход из металла, необходимо создать твердую корку в верхней части слитка. С этой целью после заполнения изложницы и некоторой выдержки на кипящую сталь накладывается чугунная плитка. 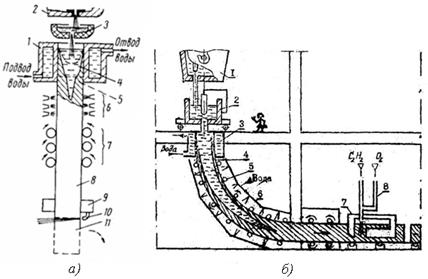 Рис. 8. Схема машины непрерывного литья заготовок (МНЛЗ) Образующаяся при этом корка затвердевшей стали приводит к повышению давления внутри слитка и прекращению выделения газов из металла. Газовые пузыри, распределенные по объему слитка, завариваются при последующей прокатке. Кипящая сталь обычно разливается сифонным способом. Наиболее прогрессивным является непрерывный способ разливки (рис. 8, а). Жидкая сталь из ковша 2 через промежуточное разливочное устройство 3 поступает в кристаллизатор 1, нижнее отверстие которого перед заливкой закрыто затравкой 5 — металлическим стержнем с сечением, соответствующим сечению кристаллизатора. Кристаллизатор представляет собой пустотелую сквозную изложницу, охлаждаемую проточной водой. Он может иметь круглое, квадратное или прямоугольное сечение заданных размеров. Металл 4 при помощи паза в виде «ласточкина хвоста» сцепляется с затравкой и затвердевает у ее поверхности и у стенок кристаллизатора. По достижении поступающим из ковша металлом определенного уровня включаются тянущие валки 7 и затравка вместе с приварившимся к ней слитком начинает вытягиваться из кристаллизатора. Слиток, имеющий еще жидкую сердцевину, проходит зону вторичного охлаждения 6, где обрызгивается водой и затвердевает по всему сечению. В нижней части установки на слиток 8 крепится тележка газорезки 9, которая начинает опускаться вместе со слитком. Перемещающийся по направляющим этой тележки автогенный резак 10 отрезает от слитка заготовку 11 необходимой длины, которая при помощи транспортера подается на склад для осмотра, зачистки и последующей прокатки. Данным способом отливают слитки с прямоугольным, квадратным и круглым поперечным сечением. При непрерывной разливке стали облегчаются условия труда, уменьшается площадь разливочного отделения, становится ненужным дорогостоящее оборудование разливочных пролетов (тележки, изложницы, сифонный припас и т. д.), обжимные прокатные станы, нагревательные колодцы и др. Исключается необходимость подготовки составов с изложницами, прокатки слитков на обжимных станах, блюмингах и слябингах. Но главное достоинство непрерывной разливки состоит в том, что отходы металла при этом способе составляют всего лишь 2—3% вместо 15—25% при получении слитков ранее рассмотренными способами. Потери металла здесь возникают только при разрезании слитка. Выход годных заготовок может достичь 96 … 98 % массы разливаемой стали вместо 75 … 80 % при разливке в изложницы. Слитки, полученные на МНЛЗ, имеют хорошее качество, плотную, мелкозернистую структуру, характеризуются высокой однородностью механических свойств в продольном и поперечном направлениях. Разливка под вакуумом позволяет получить металл с минимальным содержанием кислорода, азота и водорода.  Рис. 9. Разливка стали стали в вакуум-камере Сталь из разливочного ковша 1 (рис. 9) попадает в промежуточную воронку 2, выходное отверстие которой сообщено с камерой 4. Изложница 5 устанавливается в камере, крышка 7 герметически закрывается, и через патрубок 6 производится отсос воздуха. Расплавленный металл, заполняющий воронку 2, создает своеобразный «гидравлический» затвор, изолирующий внутреннюю полость камеры от атмосферы и позволяющий поддерживать необходимый вакуум при заполнении изложницы струёй металла. B начале разливки металл накапливается в воронке, для чего в ее нижней части вставляется алюминиевый лист 3 такой толщины, чтобы за время расплавления этого листа в воронке успело накопиться необходимое количество жидкой стали. При этом способе вакуумирование стали происходит в падающей струе металла. Более просто вакуумирование стали может быть осуществлено, если ковш с жидким металлом перед разливкой поместить в камеру, имеющую герметически закрывающуюся крышку. Соединив камеру с вакуум-насосом, из нее можно отсосать воздух и выделяющиеся из стали газы. В такой же камере можно установить изложницу и после заполнения ее сталью обработать вакуумом. |