ПОЗНАВАТЕЛЬНОЕ Сила воли ведет к действию, а позитивные действия формируют позитивное отношение Как определить диапазон голоса - ваш вокал
Игровые автоматы с быстрым выводом Как цель узнает о ваших желаниях прежде, чем вы начнете действовать. Как компании прогнозируют привычки и манипулируют ими Целительная привычка Как самому избавиться от обидчивости Противоречивые взгляды на качества, присущие мужчинам Тренинг уверенности в себе Вкуснейший "Салат из свеклы с чесноком" Натюрморт и его изобразительные возможности Применение, как принимать мумие? Мумие для волос, лица, при переломах, при кровотечении и т.д. Как научиться брать на себя ответственность Зачем нужны границы в отношениях с детьми? Световозвращающие элементы на детской одежде Как победить свой возраст? Восемь уникальных способов, которые помогут достичь долголетия Как слышать голос Бога Классификация ожирения по ИМТ (ВОЗ) Глава 3. Завет мужчины с женщиной 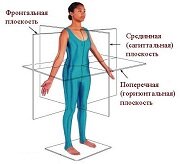
Оси и плоскости тела человека - Тело человека состоит из определенных топографических частей и участков, в которых расположены органы, мышцы, сосуды, нервы и т.д. Отёска стен и прирубка косяков - Когда на доме не достаёт окон и дверей, красивое высокое крыльцо ещё только в воображении, приходится подниматься с улицы в дом по трапу. Дифференциальные уравнения второго порядка (модель рынка с прогнозируемыми ценами) - В простых моделях рынка спрос и предложение обычно полагают зависящими только от текущей цены на товар. | Легірленген аспапты болаттар Аспап жасайтын болаттардың қаттылығы, тозуға, беріктігі мен жылуға төзімділігі де жоғары болуы керек. Шынықтырылуы оңай өтуі қажет. Бұл қасиеттеріне қарай болаттардан кескіш, соғу штампын және өлшеу аспаптарын жасауға болады. Кесу кезінде кескіш аспаптар жиегі 500°-900°С дейін қызады, қызғанда аспап кесу қабілеті мен жоғарғы қаттылығын жоғалтпауы керек. Бұл қасиет аспаптық болаттардың негізгі қасиетіне жатады да оны жылуға төзімділігі (қызылды төзімділік) дейді. Бұл болаттардың жылуға төзімділігі 300°С аспайды. Аз легірленген аспап болары құрамында қосып есептегенде қоспалы элементтер мөлшері 1-6%, ал көміртегі 0,9-1,2%-ға дейін болады. Бұл болаттардың шынықтырылғыштығы жақсы болады, МЕСТ 5950-83 бойынша X, 9ХС, ХВСГ, ХГ, ХВГ, 9ХВСГ, 9ХВГ, 9Х5ВФ, ХВ5 маркалар шығарылады. Мұндағы негізі қоспалы элементтерге хром, вольфрам, ванадий кіреді. Бұл қоспалы элементтер карбит түзейтіндерге жатады, болаттың шынықтыру қаттылығын жоғарылатады және оның төзуға төзімділігін арттырады. Бұл болаттардың термиялық өңдеуіне 8000-8500 С температурасындағы майда шынықтыру мен 150° - 200°С төменгі жұмсартудан тұрады, бұл температураны соғу аспаптарына 300°С көтереді. Жоғары берілген болаттардан ұңғылағыш (развертка), жонғыш (фреза), бұрғы (сверло), үңгі (зенкер), бұрандаойғыш (метчик), тартажонғыш (протяжка), сотан (пуансон), сымкөз (фильера, волока) және басқалар жасалады. Тез кескіш болаттар жоғарғы жылдамдықта жұмыс істейтін аспаптар жасауға қолданылады, былай айтқанда кескіш жылдамдығы болаттарға қарағанда 3-4 есе артық. Бұл болаттардың негізгі қоспалы элеметіне вольфрам жатады, ол 18% дейін, 0,7-1,5% дейін оттегі, 4,5% дейін хром, 5% дейін Мо, 10% дейін Со (кобальт). Тез кескіш болаттардың көп тараған маркаларына МЕСТ 265-73 бойынша Р18, Р9, МЗ, Р9М5, Р12, Р6МЗФ2, Р18Ф2, Р9К5, Р9КЮ, Р10, К5Ф5, Р18Ф2К5, Р4, Р7Т жатады. Марка белгіленуіне Р әрпі «Раnиg» - жылдамдық деген сөзден алынған, одан кейінгі сан құрамындағы вольфрамның орташа мөлшерін көрсетеді, ал қалған әріптерден кейінгі сандар құрамына кіретін элементтер мөлшері. Тез кескіш болаттар кесу қасиетіне байланысты үш топқа бөлінеді: қалыпты өнімділікті, көтеріңкі өнімділікті, өнімділігі төмен. Қалыпты өнімділікті болаттарға Р18, Р9, Р18Ф2, Р12, Р6МЗФ2 маркалары жатады. Бұл топқа кіретін болаттардың жылуға төзімділігі 6200 С дейін болады (қызыл төзімділігі), мұндай температурада қаттылығын НRС 60 төмен түсірмей сақтайды. Бұлар жақсартудан өткен конструкциялық болаттар мен қаттылығы НВ=300 аспайтын шойындарды кесуге қолданылады. Өнімділігі жоғары болаттардың қызылды төзімділігі 650°С дейін және қиын өңделетін материалды кесуге қоданылады. Бұл топтағы болаттар құрамына вольфрамнан басқа әжептеуір мөлшерде ванадий мен кобальт кіреді. Бұл болаттарға Р9К5, Р9К10, Р10К5Ф5, Р18Ф2К5 маркалары кіреді. Өнімділігі төмен болаттардың төзімділігі қызылды төзімділігі 6000 С дейін болады. Бұл болаттарға Р4 мен Р7Т маркалары жатады, олардан бұрандаойғыштар (метчиктер), темір кескіш ара пышақтары, ағаш өңдеу аспаптары және т.б. жасалады. Бұл болаттардың жоғарғы кескіш қасиеттері термиялық өңдеуден, яғни шынықтыру мен жұмсартудан кейін пайда болады. Бұл болаттардың құрылымы бойынша ледебуритті класқа жатады. Алынған құйманы әуелі шыңдайды, сосын 860-9000С температурасында жұмсартады. Жұмсартудан кейін болаттың құрылымы сорбиттен, аустениттен бөлінген екінші майда карбиттен және эвтектикаға кіретін өте ірі алғашқы карбиттерден тұрады. Ең соңғы термиялық өңдеуден кейін керекті қасиетті болат алынады. Мысалы, Р18 болат шынықтыруын 1250 - 1280°С температурасына дейін қыздырып, май арасында суытады. Қыздыру температурасы жоғары болған сайын, қоспалы элементтер аустенитте ериді, сондықтан мартенситгегі қоспалы элементтер мөлшері көп болады. Тез кескіш болаттардың жылу өткізгіштігі өте төмен, сондықтан оларды қыздыру сатылы жүргізіледі: аспапты әуелі 500-6000 С температуралы тұзды астауда, сосын температурасы 8000С-қа тең астауда және содан кейін үшінші астауда 12000С дейін қыздырады. Шынықтырылғаннан кейін болаттың құрылымы мартенситтен және қалдықты аустениттен (30% дейін) тұрады. Қаттылығы НRС 60-62. Құрамындағы аустенит кескіш қасиетін төмендетеді, сондықтан аспап 5600С температурасында үш ретті жұмсартудан өтеді. Бұл өңдеуден кейін қалдықты аустенит саны 2-ден 3% дейін азаяды да, қаттылығы НRС 64-65 дейін артады. Шынықтыру мен жұмсарту арасында суықпен өңдеу (-800-1000С) жүргізіледі, ол аспап дайындау процесін қысқартады. Тез кескіш болаттардан оның қымбаттылығына байланысты кескіштің жұмысшы бөлігін ғана жасайды, ал аспап тұлғасы көміртекті аспап болаттан жасалады. Соғу штампты аспаптар жасауға арналған легірленген болаттар Бұл болаттың қаттылығы мен тозуға төзімділігі жоғары болуы қажет. Штампты болаттар МЕСТ 5950-73 бойынша маркаланады. Суықтай штамптау штамптарын жасауға қолданылатын болаттар жоғарыда айтылған қасиеттерден басқа термиялық өңдеуде аз деформациялануы қажет, өйткені штамп өзгереді. Штампты дайындау үшін X, Х9, 9ХС, ХЮМ, ШХ15, ХВ2, Х12Ф, ХГЗСВ және т.б. қолданылады. Егер штампқа соққы күштері әсер ететін болса, онда штамптар жасауға 4ХС4, 4ХВС, 5ХНМ, 5ХГМ маркалы болаттар қолданылады. Бұл болаттардың тұтқырлығы жоғары. Егер штамптар тозу мен қысым жағдайында жұмыс істесе, онда штамптарды Х12, XI2Ф, ХГЗСВ болаттарынан жасайды. Бұл болаттардың қаттылығы шынықтырумен 480°-580°С температурасында жұмсартудан кейін НRС 38-45-ке тең болады. Ыстыққа деформацияланатын штамптар жасауға арналған болаттардың жоғарыда айтылған қасиеттерден басқа жылуға, ыстыққа төтімділігі, термотөзімділік қасиеттері және жылу өткізгіштігі жоғары болуы қажет. Бұл қасиеттер болатты 600°С дейін қыздырғанда сақталуы тиіс, ол үшін болаттарға хром, Мо және вольфрам, ал шынықтырғыш қасиетін арттыру үшін никель мен марганец қосады. Құрамындағы көміртегі онша көп емес (0,5-0,6% С), ол соғу тұтқырлығын қамтамасыз етеді. Шынықтыру мен жоғарғы жұмсартудан кейін мұндай болаттардың қаттылығы НВ 350-450 тең болады. Бұл болаттаға 5ЖНМ, 5ХГМ, 5ХНВ маркалары жатады. Өлшеуіш аспап өз формасы мен өлшемін ұзақ уақыт сақтауы, беріктігі, қаттылығы, тозуға төзімділігі жоғары және сызықша ұлғаю коэффициенті төмен болуы керек. Өлшеуіш аспаптар үшін маркалары V8, V12, X, Х19, ХГ көміртекті және т.б. цементтейтін, азоттайтын болаттар қолданылады. Шынықтырудан соң аспаптарды төмен температурада жұмсартады. 4 дәріс Шойындар Жоспары: 1.Шойындар 2.Шойынның алынуы Құрамында 2,14%-дан 6,67%-ға дейін көміртегі бар көміртекті темір қорытпалар шойын деп аталады. Құрылысына байланысты шойындар ақ және сұр шойын болып екіге бөлінеді. 1.Ақ шойынның құрамында көміртегі темірмен химиялық қосылыс (цементит) түрінде кездеседі. Бұл шойынның кристалдану процесі темір-цементит диаграммасы бойынша жүреді, оның қаттылық, беріктік, үйкеліске беріктік, морттық қасиеттері жоғары болып келеді. Шойынның морттық қасиеті құрамындағы көміртегі мөлшерінің артуына байланысты. Өндірісте құрылысы перлит-ледебуритті эвтектикаға дейінгі шойындар қолданылады. Ақ шойын өңдеуге келмейтіндіктен олардан механикалық өңдеуді керек етпейтін қорытпалар алынады. Мұндай қорытпалардың сыртқы беті ақ шойын, ішкі жағы (өзегі) сұр шойын түрінде кристалдануы үшін сыртқы бетін тез, ал ал ішкі жағын баяу жылдамдықпен суытады. Ақ шойынды соқаның пышағын, прокат валдарын, диірменнің шарларын жасау және соғылғыш шойын (ковкий чугун) алу үшін пайдаланады. 2. Сұр шойында көміртегі бос күйінде пластикалы графит формасында (қалпында) болады. Мұндай шойындар құрамында графит болғандықтан сынығы сұр түсті болады. Cұр шойынның құрамындағы графиттің түзілу табиғаты осы күнге дейін толық анықталмаған. Графиттің балқыған көміртекті темір қорытпаларынан немесе аустениттен түзілу процесі тек оларды баяу жылдамдықпен суытқанда жүреді. Бүйір беті ақ, ортасы сұр болып келетін шойын қорытпалары ағартылған шойын деп аталады. Шойынның құрамындағы әдеттегі элементтер немесе белгілі мақсатпен енгізілген элементтер графит түзгіш және карбид түзгіш элементтер болып екіге бөлінеді. Сұр шойындардың құрамында тұрақты қоспалар болады: 2,4-3,8% - G, 1,2-3,5% - Sі, 0,5%о - Мn, 0,12% - S және 0,5% - Р. Кремний, никель, алюминий және т.б. элементтер шойынның құрамындағы темір мен көміртегінің өзара тартылыс күшін әлсіретіп, графиттің түзілуіне жағдай туғызады. Марганец, хром, вольфрам элементтері карбид түзеді. Шойын ферритті, феррит-перлитті немесе перлитті (4.1-сурет) негізінде болып, ондағы графит тілім (пластинчатый), үлпек (хлопьевидный) немесе шар түрінде бөлініп тұрады.  4.1 -сурет. Феритті, ферит-перлитті және перлитті негізіндегі шойындардың құрылысы. Сұр шойындар былайша белгіленеді: СЧ-12-23, СЧ15-32,СЧ32-52 т.б. (мұндағы СЧ - серый чугун, 12 шойынның үзілуге беріктік шегі, 23 иілуге беріктік шегі). Сұр шойындардың механикалық қасиетін арттыру мақсатымен оларды балқытып, оларға модификатор деп аталатын, ұнтақталған (ферросилиций, феррокальций, магний) қоспаларды модификациялайтын шойынға қосады, қоспаның мөлшері 0,5-1% шамасында болуы тиіс. Әдетте құрамында көміртегі мен кремний элементтерінің мөлшері аз шойындар модификацияланады. Мысалы, 2,9-3,2% - G, 1-1,5% - Sі, 0,8-1,2%, - Мn, 0,12% - 3, 0,3% - Р. Шойынды магний элементімен модификациялау шойынның жаңа түрін - беріктігі жоғары шойындар - алуға мүмкіндік береді. Мұндай шойынның құрамындағы графит шар түрінде болады. Бұл шойындар былайша белгіленеді: ВЧ40-10, ВЧ-60-2 (ВЧ-беріктігі жоғары шойын; бірінші цифр созуға беріктік шегін, екінші цифр - салыстырмалы ұзару коэффициентін көрсетеді). Созылғыш шойынның тұтқырлығы жоғары. Соғылғыш шойын құйма күйінде ақ шойындар қатарына жатады. Құрамындағы темір карбидін бөліп, бос графит алу үшін термиялық өңдеуден өткізеді. Мұндай шойынның құрамындағы графит үлпек түрінде болады. Соғылғыш шойынның мынандай түрлері бар: КЧ-38-12, КЧ-40-6, КЧ-35-4, КЧ-30-3 (мұндағы КЧ соғылғыш шойын, бірінші цифр соғуға беріктік шегін, екінші цифр - салыстырмалы ұзару коэффициентін көрсетеді). Структурасына қарай олар перлитті және ферритті болып екіге бөлінеді. Шойынның алынуы  Домна пешінің құрылысы: 1 – газ шығаратын патрубок; 2- себушіаппарат; 3 – отқа төзімді қабат; 4 – болат қабат 5 – салқындатқыш тұрба; 6 - тіректер; 7 – шойынды төгу үшін арналған лётка; 8 – тірек сақина; 9 – шлак төгу үшін арналған лётка; 10 – фурма үшін арналған сақина коллектор. 1 Шойын өндіруге арналған метариалдар Металдар мен қорытпаларды өндірумен шұғылданатын ғылым, техника және өндіріс саласын металлургия деп атайды. Қара металлургияға шойын, болат және ферроқорытпа өндірісі жатады. 1.1 Шойын өндірісінің шикізаттары Шойын домна пештерінде қорытылады. Шойын қорытуға керекті шикізаттар: 1) темір кені; 2) марганец кені; 3) флюс; 4) отын. 1.1.1 Темір және марганец кені Техниканың даму деңгейінде тау жынысынан темір алу экономикалық тиімді болса, оны темір кені деп атайды. Темір кені кен бөлігі мен бос жыныстан тұрады. Кен бөлігіне темірдің оттегімен, СО2- мен және т.б. қосылыстары жатса, бос жынысқа – кварцит немесе құмнан (көбінесе балшық қосылған, сирегірек-доломит пен әк тас) тұратын бөлігі. Темір көніндегі темір мөлшері 30-42 %-ден 45-70 %-ға дейін болады. Осыған орай, темір кенін кедей және бай деп атайды. Шойын өндірісінде қолданыс тапқан темір кендері төмендегідей бөлінеді: 1) магнитті теміртас (магнетитті кен); 2) қызыл теміртас (гематитті кен); 3) қоңыр теміртас; 4) шпатты теміртас. Магнетитті темір кені магнетит Fe3O4 минералынан тұрады. Бос жынысы қышқылды (SiO2, Al2O3). Қазақстанда Соколовск, Сарыбай және Қашар (Қостанай облысы) магнетитті темір кен орындары бар. Соколовск және Сарыбай кен орындарының магнетитті кендерінде 43-48 % Fe; 1-4 % S; 0,10-0,14 % Р бар. Кенді магниттік тәсілмен байыту арқылы 65 % Fe бар концентрат алынады. Қашар кен орнының темір кенінде ең көбі 59 % Fe болса, ең азы 43 % Fe болады. Темірі аз кеннен 65 %-дан жоғары темірі бар концентрат алынады. Магнетитті темір кенінің қоры 4 млрд.т. Гематитті темір кені гематит Fe2O3 минералынан тұрады. Қызыл теміртас тотыққан магнетит. Гематитте 1-8 % магнетит болады. Бос жынысы негізінен қышқылды (SiO2, Al2O3). Қарағанды облысының Атасу темір кені негізінен магнетит-гематитті. Кенде 55 % Fe, 0,5-1,0 % S, 0,04 % Р бар. Кеннің қоры 0,3 млрд.т. Лимонит 2Fe2O3×3Н2О және гетит Fe2O3×Н2О минералынан тұратын кен қоңыр теміртас деп аталады. Қостанай облысында қоры 9,8 млрд.т. қоңыр теміртас – Лисаковск және Аят кен орындары бар. Кендегі темір мөлшері 35-38 %; күкірт 0,03-0,35 %; фосфор 0,35-0,55 %. Кеннің бос жынысы кремнезем мен глинозем. Кенді байыту күрделілеу тәсілді керек етеді, сондықтан алынған концентраттағы темір мөлшері онша жоғары емес (47-55 %). Сидерит FeCO3 минералынан тұратын кен шпатты теміртас деп аталады. 30-40 % Fe бар. Темір кендерінде басқа элементтердің де қосылыстары кездеседі. Олар пайдалы және зиянды элементтер болып бөлінеді. Пайдалы элементтерге V, Ti, Ni және т.б. жатса, зияндыға – S, P, As, Zn, Cu және т.б. Темір кендерінің бос жынысы SiO2, Al2O3, CaO, MgO –дан тұратын әр түрлі қосылыс түрінде болады. Темір кенінің бос жынысы негізінен қышқылды (SiO2) болып келеді. Шойын өндірісінде аз мөлшерде болса да, марганец кені пайдаланылады. Кендегі 25-48 % Mn марганецтің түрлі оксидтері (MnO2, Mn2O3, Mn3O4) түрінде болады. Кеннің бос жынысының құрамында кремнезем көбірек, глинозем азырақ болады. 40-56 % Mn бар концентрат алу үшін гравитациялы – магниттік тәсілмен байытады. Марганец кені Жезді (Қарағанды облысы) кен орнынан шығарылады. 1.1.2 Қожтүзгіш материал Темір мен марганец кендерінің бос жынысымен және отын күлімен балқу температурасы төмен қож түзу үшін шиқіқұрамдық материалға флюс қосылады. Кен бос жынысының негізгі құраушысы SiO2 болғандықтан, флюс ретінде негізді материал - әк тас CaCO3 (сирегірек CaCO3 × MgCO3) қолданылады. Флюс құрамында зиянды элементтер (S, P) және SiO2 мөлшері төмен болғаны жөн. Отын Домна пешінде шойын қорыту жоғары температуралық үрдіс болғандықтан, жылу көзі ретінде отын пайдаланылады. Отын табиғи және жасанды болып бөлінсе, агрегатты күйі бойынша қатты, сұйық және газ күйінде болады. Домна үрдісінде отынның үш түрі де қолданыс тапқанымен, негізгісі қатты отын. Қатты отынға қойылатын талаптар мыналар: 1) жылу шығарғыштығы жоғары; 2) механикалық беріктігі жоғары; 3) кеуектілігі; 4) зиянды элементтердің төмендігі; 5) күлі аз; 6) экономикалық арзандығы және т.б. Қатты отынға қойылатын талаптардың жоғарылығынан, қазіргі кезде жасанды қатты отын кокс қолданыс тапты. Кокстелетін тас көмірді кокс пешінде 1000-1200 0С-да ауасыз қыздыруда алынатын өнім кокс деп аталады. Кокстеу уақыты 14,5-16 сағат. Кокс құрамында 80-88 % С; 8-12 % күл; 2-5 % ылғал; 0,7-1,2 % ұшпалы зат; 0,5-1,8 % S және 0,02-0,2 % Р болады. 1 т шикіқұрамдық материалдан 750-800 кг кокс және 320-330 м3 кокс газы алынады. Кокс газының құрамы: 57 % Н2, 20-23 % СН4, ~ 8 % N2. Сонымен қатар бензол, фенол, нафталин, көмір шайыры, сульфат аммониі және т.б. алынады. Кокстың жылу шығарғыштығы 27,2-31,4 МДж/кг, кокс газының – 17,5-18,5 МДж/м3. Кокс қымбат болғандықтан, оны басқа отын түрлерімен алмастыру шаралары қарастырылады. Қазіргі кезде кокстің бір бөлігін табиғи газ, мазут немесе тозаң көмір суспензиясымен алмастырады. 1.1.4 Оттөзімді материал Минерал шикізаты негізінде жасалып, өзінің қасиетін сондайлық өзгеріссіз жоғары температурада сақтай алатын материалды оттөзімді деп атайды. Металлургияда қолданылатын оттөзімді материалдардың негізгі міндеті: жоғары температуралы балқыма мен қож және газды ортада өзінің қасиетін сақтай отырып, ұзақ уақытқа жарамды әрі арзан болуы. Металлургиялық зауыттарда қолданылатын техникалық жіктелім бойынша барлық оттөзімді бұйымдар үш топқа бөлінеді: 1) қышқылды; 2) негізді; 3) бейтарап. Оттөзімділігі бойынша үш топқа бөлінеді: 1) оттөзімді (1580-1770 0С); 2) жоғары оттөзімді (1770-2000 0С); 3) өте жоғары оттөзімді (2000 0С-дан жоғары). Оттөзімді бұйымдар пішіні мен өлшемі бойынша бөлінеді: 1) қарапайым (түзу, сыналы); 2) фасонды (қарапайым, күрделі, өте күрделі, ірі блокты); 3) арнайы. Оттөзімді бұйымның қасиеті, оның химиялық құрамына, жасау тәсіліне және эксплуатациялық жағдайына байланысты. Бұйымның негізгі қасиеттері: 1) оттөзімділік; 2) жүктеме әсерінен жоғары температурада деформациялану; 3) термиялық төзімділік; 4) химиялық төзімділік; 5) кеуектілік; 6) газөтімділік; 7) жылуөтімділік; 8) жылусыйымдылық; 9) механикалық беріктік және т.б. Оттөзімді материалдар мен бұйымдар табиғи және жасанды болып бөлінеді. Металлургия өндірісінде қолданылатын оттөзімді материалдардың көпшілігі жасанды. Оларды жасаудың жалпы технологиялық сұлбасы мынадай: 1) шикізаттық материалдарды дайындау (қыздыру, ұсақтау, сұрыптау); 2) шикіқұрамды дайындау (араластыру, су қосу); 3) бұйымды қалыптау; 4) бұйымды кептіру; 5) бұйымды күйдіру. Домна пешінің шегенін қалау үшін шамот, жоғары глиноземді кірпіш және көміртекті блоктар пайдаланылады. Шамоттың құрамында 28-45 % Al2O3, қалғаны кремнезем. Шамоттың оттөзімділігі 1580-1750 0С. Жоғары глиноземді кірпіште 45 %-дан жоғары Al2O3 бар, оттөзімділігі жоғары. Домна пешінің жоғарғы жағының қаламасы ретінде шамот қолданылса, төменгі жағын жоғары глиноземді кірпіштен қалаған жөн. Пештің түбін көміртекті блоктар мен жоғары глиноземді кірпіштен қалайды. 1.2 Домна үрдісінің шикіқұрамдық материалдарын дайындау Шойын өндірісінің шикізаттарын (темір, кені, флюс, кокс) пешке салмастан бұрын алдын ала даярлайды. 1.2.1 Материалдарды ұсату мен сұрыптау Флюсті уатып, електен өткізіп, елесе, коксті тек елейді. Темір кенін даярлау едәуір күрделі, оны дайындаудың кезеңдері төмендегідей: 1) ұсату және ірілігі бойынша сұрыптау; 2) орташалау; 3) байыту; 4) кесектеу. Темір кенін ұсату мен ұсақтау кезеңдері: 1) ірі ұсату (өлшемі 100-350 мм); 2) орташа ұсату (40-60 мм); 3) кіші ұсату (6-25 мм); 4) ұсақтау (1 мм-ге дейін); 5) ұнтақтау (өте ұсақтау) (1 мм-ден кіші). Кенді ірі ұсату үшін жақты және конусты уатқыштар қолданыс тапса, орташа және кіші ұсату үшін – білікті. Ұсақтау үшін диірмендер пайдаланылады. Кенді ұсату және ұсақтау операцияларында, оларды ірілігі бойынша сұраптау және классификациялау (бөлу) орын алады. Ұсатылған материалды ірілігі бойынша сұрыптау (1-3 мм) үшін елек қолданылады. Гидравликалық классификация ірілігі әр түрлі материалдардың суда құлау жылдамдығының айырмасына негізделген. Гидравликалық және ауадағы классификация арқылы ірілігі 1 мм-ден кіші ұсақталған материал алынады. Темір кенін орташалау Кеннің химиялық құрамы бірдей болмаса, оны орташалайды. Ол үшін арнайы орташалау қоймасын пайдаланады және кенді тасымалдау кезінде орташалану орын алады. Темір кенін байыту Байыту тәсілдері арқылы темір кенінің кен минералын бос жынысынан айырып, темірі жоғары концентрат алуды темір кенін байыту дейді. Кейбір кендердің бос жынысы саз қосылған құм болып, сумен жақсы шайылады. Мысалы, марганец кені, қоңыр теміртас. Кен минералы магнетит (Fe3O4) болса, магниттік тәсілмен темірдің мөлшерін арттырады. Гематит (Fe2O3) минералының магниттігі төмен болғандықтан, оны алдымен магниттік қыздырудан (600-800 0С) өткереді, яғни Fe2O3 Fe3O4-ке тотықсыздандырылады: 3Fe2O3+CO=2Fe3O4+CO2; 3Fe2O3+H2=2Fe3O4+H2O. Содан кейін магниттік сепараторда бос жынысынан айырады. Кейбір темір кендеріне кен бөлігі мен бос жыныс тығыздығының әр түрлілігіне негізделген гравитациялық тәсілді қолданады. Домна үрдісінің өзіне тән ерекшелігіне байланысты шикіқұрамдық материалдар белгілі бір кесек мөлшерде болуы керек, ұнтақ тәріздес материалдар қолданылмайды. Сондықтан байытылған темір кендерінің ұсақ бөлігі, енді кесектеуді керек етеді. Кесектеу Темір кенінің ұсақ фракциясы мен концентратты кесектеудің екі тәсілі бар: 1) агломерациялау; 2) окатыш жасау. Ұсақ темір кенін, концентрат және т.б. материалдарды агломерациялау үшін агломерациялық машина қолданылады. Алынған өнім агломерат және флюстелген агломерат болып бөлінеді. Флюстелген агломерат алуға арналған шикіқұрамдық материал құрамы төмендегідей, %: Темір кені, концентрат (ірілігі 8 мм-ден кіші) .....................40-50 Әк тас (2 мм-ден кіші)..........................................................15-20 Ұсақ агломерат (10 мм-ден кіші).........................................20-30 Коксик (3 мм-ден кіші).........................................................4-6 Ылғал ...................................................................................6-9 Шикіқұрамдық материалды барабанда араластырып, содан кейін ылғалдап түйіршіктейді. Агломашинаның конвейерлік таспасының колоснигінде өлшемі 10-25 мм агломерат қалдықтарын төсеп, оған дайын болған шикіқұрамдық материалдарды салады (биіктігі 250-350 мм). Колосниктік тордың астын эксгаустерге қосып, ауаны сиреткенде (7-10 кПа), сыртқы ауа шикіқұрам қабатынан өте бастайды. Шикіқұрамды үстінен жаққанда коксиктің жану зонасы төменгі қабатқа қарай жылжиды. Коксиктің жану зонасында температура жоғарылап (1450 0С), нәтижесінде кесек өнім флюстелген агломерат алынады. Флюстелген агломератты салқындатып, екшеп, содан кейін домна цехына жібереді. Темір кендерінің байыту дәрежесін жоғарылату нәтижесінде өте уақ концентрат (0,07 мм кіші) алынып, кесектеудің жаңа тәсілі окатыш жасау дүниеге келді. Окатыш жасау үрдісі 2 сатыдан тұрады: 1) шикі оқатыш жасау; 2) окатышты беріктендіру. Окатыштың шикіқұрамдық материалдары төмендегідей: 1) концентрат; 2) окатыш қалдықтары; 3) бентонит (байланыстырғыш материал); 4) ылғал (8-10 %). Флюстелген окатыш алу көзделсе, онда әк тас қосады. Окатыш жасау барабанды немесе тәрелкелі грануляторда іске асырылады. Шикіқұрамдық материалды араластырып, бентонит пен су қосып, тәрелкелі (немесе барабанды) грануляторде диаметрі 20-30 мм окатыш алынады. Алдымен окатышты кептіріп (300-600 0С), содан кейін күйдіріп (1200-1350 0С), беріктендіреді. Дайын окатышты салқындатып, уағын екшеп, домна цехына жібереді. 5 дәріс Металдарды жаймалау. Металдарды термиялық өңдеу Қазіргі заман техникасының тетіктері, құрылымдары және басқа бұйымдары негізінен металл мен қорытпалардан металлургиялық және машина жасау кәсіпорындарында жасалады. Металдан жасалған бұйымдарды және олардың жартылай өнімдерін жасаудың негізгі тәсілдері болып мыналар саналады: 1)құю; 2) қысыммен өңдеу; 3)кесумен өңдеу. Осы тәсілдердің ішінде ерекше рольді металдарды қысыммен өңдеу (МҚӨ) алады. Металдарды қысыммен өңдегенде металдың пішінін, оны деформациялау жолымен пластикалық өзгертеді. Металдарды қысыммен өндеу (орыс. Обработка металлов давлением) — дайындаманы, илемді деформациялап, дайын тетіктердің өлшемдеріне, түріне жақын өлшемдер мен түр беру. 1.Металдарды қысыммен өңдеу үлкен өнімділікпен және аз шығынмен дайын тетікке пішіні жақын тетіктерді немесе дайындама түрінде олардың жартылай өнімдерін жасауға мүмкіндік береді. Металл суық және ыстық күйде пластикалық деформациялаумен өңделеді. Пластикалық деформация процесінде металдың құрылымы өзгереді және оның механикалық қаcиеті жоғарлайды. Сондықтан аса жоғары күш түсетін машиналар тетіктерін қысыммен өңдеп жасайды. Пластикалық деформациялау әр түрлі тәсілдермен іске асырылады. Осы тәсілдерге мыналар жатады: илемдеу; еркін соғу; көлемдік қалыптау; баспақтау; қаңылтырлы қалыптау; сымдау және МҚӨ арнайы тәсілдері. Металдардың пішінін өзгертуді жоғары өнімділікпен және аз шығынмен жүргізуге мүмкіндік бар болғандықтан, ал тағы да олардың механикалық қасиетін жоғарлатуға да мүмкіндік бар болғандықтан қысыммен өңдеудің ролі қазіргі заманғы өндірісте өте үлкен болып түр. Тұтастай алғанда металдарды қысыммен өңдеу машинажасау мен металлургияның дайындаушы базасы болып саналады. Негізінен алғанда МҚӨ сапалық дамуынан және толық жетілуінен қуатты энергетикалық құрылымды, жаңа ұшатын аппаратарды, қазіргі заманғы автомобилдер мен жүккөтергіш машиналарды, жаңа электронды және космосты техниканы жасау тәуелді болады. Металдарды экономдау – МҚӨ алдына қойылатын негізгі міндеттердің бірі болып саналады. Экономикалық көрсеткіштерді бағалау үшін тетіктің массасы мен оны жасау үшін жұмсалған металдың массасының сандық қатынасын қолданады. Осы қатнасты процентпем көрсетілген металды қолдану коэффициентті (МҚК) деп атайды. Металды қолданудың ең үлкен мәніне суықтай көлемдік қалыптау және илемдеу (82 және 85 %, сәйкесті жазылған) иемденген. Металөңдеу процестері, мысалы МҚӨ, экономикалық тым тиімді өңдеу тәсілдерін жасау бағытында дамитын болады. Осы тиімді тәсілдерге бірінші кезекте қиыстырылған және қатар қолданылатын процестерді жатқызуға болады. Осындай да металлургиялық қайта өңдеуді қысқарту өндірістің үздіксіз технологиялық сұлбасын ұйымдастырумен байланысты. Бұл процестің еңбексиымдылығын және энергиясиымдылығын едәуір азаютуға және металдың жарамды болып шығуын үлкейтуге алып келеді. Металдарды қысыммен өңдеген кезде бастапқы материал ретінде құймакесек, шыбық, әр түрлі сортты пішіндер және т.б. түріндегі болаттардың барлық таңбасы, алюминий, магний, титан қорытпалары, ал тағы да мыс, никель негізіндегі қорытпалар қолданылады. Соғу үшін мысалы құюға дейін толық оттексіздендірілетін тыныш болатты қолданады. Қайнаған болаттан жасалған құймакесек соғу үшін азырақ жарамды. Өйткені осы құймакесектегі бос орындарды, көпіршіктерді деформациялау процесінде толық пісіру қиын. Илемдегеннен кейін алынған болаттан немесе түсті металдан жасалған дайындамаларды қалыптау үшін қолданады. Керекті пластикалық қасиетті қамтамасыз ету үшін металл мен қорытпаларды суық және ыстық (басымырақ) күйде деформациялайды. Болаттар, көміртегісі бар темір қорытпалары (2,14%) өндірістің кез келген саласында: машина жасауда, металлургияда, құрлыста, автомобил жасауда және т.б. қолданылады. Химиялық құрамына байланысты болаттар: көміртекті (Ст3, 08кп және т.б.) және қоспаланған (3Х2В8Ф, 5ХНМ және т.б.) болып екіге бөлінеді. Белгілеуіне байланысты болаттарды құрылымдық және құрал-саймандық деп екіге бөледі. Алыну тәсіліне байланысты болаттар мартендік, бессемерлік, тамастық болып үшке бөлінеді. Оттексіздендіруіне байланысты айтылған болаттарды тыныш, жартылай тыныш және қайнаған деп үшке бөледі. Көміртекті болаттар төменгі көміртекті (0,25 % дейін көміртек), орташа көміртекті (0,25-0,6 %) және жоғары көміртекті (0,6 жоғары) болып үшке бөлінеді. Төменгі және орташа көміртекті болаттар құрылымдық, ал жоғары көміртекті болаттар құрал-саймандық болып саналады. Осы болаттарда пластикалық деформацияның үлкен қоры бар. Сондықтан олар 80 % дейінгі деформация дәрежесімен деформациялануы мүмкін. Жоғары көміртекті және жоғары қоспаланған болаттар өңдеудің бір циклінде 60 % дейін деформация дәрежесімен деформацияланады. Сондықтан оларды орташа пластикалық материалдарға жатқызады. Алюминий қорытпалары кішкентай меншікті салмаққа және жоғары беріктіктік қасиетке иемденген. Оларды жұмсақ қорытпалар (АМц, АД31, АМГ), орташа қаттылықты қорытпалар (Д1, Д16, АК1) және жоғары беріктікті қорытпалар (АК8, В95) деп үшке бөледі. Осымен бірге алюминий қорытпаларын термиялық беріктенетін және термиялық беріктенбейтін деп айырады. Алюминий қорытпалары жоғары пластикалық қасиетке иемденген. Осы себептен оларды көлденең гидравликалық баспақта баспақтап, олардан өте күрделі құрылымы және әр түрлі қимасы бар көптеген пішіндерді жасайды. Алюминий қорытпаларының кішкентай тығыздығы, жегідеге жоғары тұрақтылығы, салыстырмалы жоғары механикалық қасиеттері, олардан жасалған бұйымдарды машинаның, автомобилжасаудың, құрылыс құрылымының және архитекторлық ғимараттың әр түрлі тетіктерінде қолдануға мүмкіндік берді. Алюминий қорытпаларынан жасалған тұтас және қуыс пішіндердің негізгі тұтынушысы болып авиациалық, кеме жасау, тоңазытқыш техникасы, электртехникалық өндірістер және т.б. саналады. Соңғы жылдары алюминий қорытпаларынан жасалған қуыс пішіндердің түржиыны көбейді. Өйткені оларды құрылымдық және құрлыстық тетіктерді жасау үшін құрлыста кеңінен қолдана бастады. Мыс және оның негізіндегі қорытпаларды өндірістің көптеген салаларында кеңінен қолданады, мысалы: электртехника, құрылыс, жылуэнергетика және т.б. Мыста жоғары пластикалық қасиет бар. Сондықтан одан МҚӨ барлық тәсілдерімен тетіктер жасайды. Қорытпаларды мынандай екі топқа бөледі: қолалар, жездер. Қысыммен өңделетін жездерді (мыстың мырышпен қорытпалары) 8 таңбаға бөледі. Ыстықтай металдарды қысыммен өңдеу үшін кеңінен Л62 және Л68 таңбалы жездер қолданылады. Қолалар (мыстың қалайы, алюминий, марганец, кремний, бериллий және басқа элементтермен (мырышты қоспағанда) қорытпасы) 10 таңбаға бөлінеді. Қалайысыз қолалар жақсы антифрикциялық және антижегіделік қасиеттермен сипатталады. Олар тұзды суда, майда, буда жақсы жұмыс істей алады. Магний қорытпалары (МА2, МА5, ВМ 65-1) жеңіл қорытпаларға жатады. Олар жоғары жегіделік қасиетке бейім екендігін көрсетеді. Осы себептен оларды белгілі бір шекпен машинажасауда қолданады. Негізінен оларды авиациялық өндірісте кұрылымдық материал ретінде қолданады. Қолдану аймағы мынандай: ракета жасау; ұшақ жасау; автомобиль жасау; электр-техникалық өндіріс. Титан қорытпалары (ВТ-1) ең үлкен меншікті беріктікке, жоғары антижегіделік тұрақтылықа және отқа төзімділікке иемденген. Осы қорытпаларды авиажасауда, химиялық және көліктік машинажасауда, яғни оларды ракета, ұшақ, сүнгір қайық және т.б. машиналардың тетіктерін жасау үшін қолданады. Жоғарыда айтылған металдармен бірге халық шаруашылығының әр түрлі саласында басқа металдар мен қорытпалар қолданылады. Мысалы, зергерлік бұйымдарды өндіру үшін алтын, платина, палладий, күміс және олардың негізіндегі қорытпаларды қолданады. Электртехникалық өндіріс үшін вольфрам, молибден және т.б. баяу балқитын қорытпаларды қолданады. Осымен бірге сәндік қорытпа ретінде мысникелді қорытпаларды қолданады, мысалы, мельхиор, нейзильбер және басқа. Металл өңдеуді металдарды қысыммен өңдеу тәсілдерін қолданып болашақта ары қарай дамытуды келесі жолмен жетуге болады: металдарды қысыммен өңдеудің процестерін барлық жақтан механизациялау және автоматтандыру; қара және түсті металдарды және олардың қорытпаларын қатар қолданып өңдейтін жаңа үздіксіз процестермен өңдеу; өндірістік жабдықтардың қуатын және өнімділігін үлкейту; МҚӨ тәсілдерімен бұйымды шығарудың кішкентай шығынды және шығынсыз технологияларын жасау; МҚӨ технологиялық процестерін жобалау және басқару үшін қазіргі кезде қолданылып жүрген бағдарламалық құралдарды қолдану; қиындеформацияланатын және пластикалық қасиеті кішкентай қорытпаларды өңдеу үшін жаңа материалдарды, жабдықтардың түрін және технологияны жасау; МҚӨ процестері үшін технология мен құрал-сайманды автоматты жобалайтын жүйені жасау. 2. Илемдеу өндірісі – бұл илемдеу өнімінің сапасын және илемдеу цехының техник-экономикалық көрсеткішін анықтайтын бір бірімен кешенді байланыста болатын технологиялық қайта өңдеулер. Илемдеу өндірісінің дамуы жаңа, едәуір жетілдірілген қыздыру, илемдеу және таза өңдеу жабдықтарын қолдануға негізделген. Осы жабдықтар жылдамдығы жоғары және жұмысының режімі қарқынды болатын бір қатар технологиялық процестердің және операциялардың ағынды болуымен сипатталуы қажет. Илемдеу өндірісінде технологиялық процестің шешуші бағыты болып өндірістік процесті кешенді механизациялау, өнімнің түржиынын кеңейту, оның сапасын жақсарту және металдан экономды түрде өнім жасау саналады. Қара және түсті металдардан өндірісте илем шығаратындығын оқулықтарда айтылып жатыр. Бірақта болаттан илемді өндіру басым болып келеді. Түсті металдар мен қорытпалардан илемді шығарған кезде шығарылатын өнімнің көлемінде үлкен үлесті қаңылтыр илемдеу өндірісі алады. Дайындаманың көлденең қимасын азайтып оған керекті пішінді беру үшін бастапқы дайындаманы илемдеу орнағының айналатын пішінбілігімен жаншитын пластикалық өңдеудің бір түрін илемдеу деп айтады. Илемдеудің мынандай үш негізгі тәсілдері бар: ұзына бойлы, көлденең және көлденең-бұрандалы. Ұзына бойы илемдеген кезде дайындаманы деформациялау әр түрлі бағытта айналатын пішінбіліктер арасында іске асырылады. Илемдейтін пішінбіліктер, ал тағы да өңделетін дайындамалар осьтері параллельді екені (немесе кішкентай бұрышпен қилысатыны) көлденең илемдеудің қарапайым сұлбасынан көрініп түр. Көлденең илемдегенде қапастағы екі пішінбілікте бір бағытта айналады, ал көлденең қимасы дөңгелек дайындама кері бағытта айналады. Көлденең илемдеу процесінде өңделетін дайындаманы пішінбілікте арнайы құрылғы көмегімен ұстап тұрады. Дайындаманы диаметр бойынша жаншу және оған қима бойынша керекті пішінді беру пішінбілікті сәйкесті пішіндеумен және олардың арасындағы арақашықты өзгертумен қамтамасыз етіледі. Осы тәсілмен айналу денесі болып саналатын бұйымдарды (шар, ось, тістегіріштер және басқа) шығарады. Көлденең-бұрандалы немесе қисық илемдеу орнақ қапасында бір біріне белгілі бір бұрышпен орнатылған бір бағытта айналатын пішінбіліктермен орындалады. Қисық илемдеу орнағын құбырды өндіргенде, ең бастысы, құймакесекті немесе дайындаманы тесіп гильзаны жасағанда қолданады. Өңделетін дайындаманың осіне еңкейіп орналасқан айналатын пішінбілікпен металл жанасқан уақытта, дайындаманың осінің бойымен бағытталған күштер және оның көлденең қимасына жанамамен бағытталған күштер пайда болады. Осы күштердің бірлесіп әсер етуі айналуды, тарылатын саңылауға өңделетін дайындаманы тартып кіргізуді және деформациялауды қамтамасыз етеді. Илемдеуді қаңылтырлы және сортты деп екі бөледі. Сортты илемдеген кезде пішінбіліктің бөшкесінде жылға бар болады. Осы жылғалар екі және одан да көп пішінбіліктерді құрастырғанда пішіні және өлшемі бойынша жасалатын жартылай өнімге сәйкес келетін мөлшерлегішті құрады. Қаңылтырлы илемдеу кезінде пішінбіліктің тегіс бөшкесі қолданылады. Ең көп таралған болып «дуо» және «трио» орнақтарында илемдеу саналады. Осы орнақтардың қапастарында сәйкесті екі және үш жұмысшы пішінбіліктер бар. Жұқақаңылтырлы илемді және фольганы өндірген кезде көппішінбілікті илемдеуді қолданады. Бұндай жағдайда илемдеу төрт (кварто), алты, он екі және жирма пішінбілігі бар қапастарда іске асырылады. Қағида бойынша әмбебапты қапастарда екі тік және екі көлбеу пішібіліктер орнатылған. Осы пішінбіліктер дайын илемнің пішіні мен өлшеміне сәйкес келетін жабық мөлшерлегішті құрады. Илемдеу өндірісінің өнімі. Илемдеу өндірісінің өнімі халық шаруашылығының барлық саласында өте кең қолдануды тапты. Осы өнім әр түрлі пішіні бар дайындама ретінде машинаның, білдектің, трактордың, автомобильдің, вагондардың, теміржолдың және т.б. жабдықтардың тетіктерін жасау үшін қолданылады. Илемделетін пішіннің түржиыны. Илемдеудің профилі деп оның көлденең қимасының пішінін айтады, ал түржиіні деп бір орнақта немесе орнақтар тобында илемдеумен алынатын әр түрлі өлшемі бар бір қатар профилдерді айтады. Илемденетін профилдердің түржиыны өте көп. Осы түржиынды мынандай бес топқа бөледі; 1) сортты илем; 2) қаңылтырлы илем; 3) құбырлар; 4) илемнің арнайы түрлері (дөңгелектер, құрсаулар, сақиналар және т.б.); 5) периодты илем. Сортты металдың профилін мынандай екі топқа бөледі: қарапайым геометриялық пішінді (квадратты, дөңгелек пішінді және жолақты болат) және күрделі-фасанды пішінді (екітаврлы арқалықтар, швеллерлер, рельстер және т.б.). Қаңылтырлы илемді (болатты) мынандай түрлерге бөледі: қалыңқа-ңылтырлы болат (қалыңдығы 4 мм үлкен), жұқақаңылтырлы болат (қалыңдығы 4 мм кіші) және кеңжолақты немесе әмбебапты болат. Қалыңдығы 3 – 8 мм болатын қаңылтырды жиі отраша қалыңдығы бар қаңылтыр деп атайды. Қалыңқаңылтырлы болатың қалыңдығы 4-тен 160 мм дейін және ұзындығы 4-тен 12 м дейін өзгерген кезде, олар 600-ден 5000 мм дейін өзгеретін енге иемденеді. Бронялы тақта ені бойынша 4500 мм-ге дейін және қалыңдығы бойынша 550 мм дейін жасалады. Жұқақаңылтырлы болаттың ені 500-ден 2500 мм дейін, қалыңдығы 0,2-ден 3,75 мм дейін, ал ұзындығы 700-ден 4000 мм дейін өзгереді. Қалыңдығы 0,2 мм-ден кіші болатын қаңылтырларды фольга деп айтады. Қаңылтырлардың жиегі кесілу қажет. Қаңылтырлар жиегі бойынша кесілген болуы қажет. Электр-техникалық және трансформаторлы болатарда 750 және 1000 мм тең болатын ен және 0,35-тен 1,0 мм-ге тең болатын қалыңдық бар болуы қажет. Кеңжолақты немесе әмбебапты болаттар 200-ден 1500 мм-ге дейін өзгеретін енге және 4-тен 60 мм-ге дейін өзгертін қалыңдыққа иемденген. Болаттан жасалған таспалар қалыңдықтарына байланысты 20-дан 2500 мм-ге дейін ені өзгеретін етіп және ұзындығы 300 мм-ге жететін етіп жасалады. Болаттан жасалған құбырлар мынандай екі топқа бөлінеді: диаметрлері 25-тен 600 мм-ге дейін өзгеретін жіксіз құбырлар; диаметрлері 10-нан 1400 мм-ге дейін өзгеретін пісірілген (түйістіріп пісірілген, айқастырып пісірілген, суықтайпрофилденген). Периодты илем көлденең қимасының пішіні мен ауданы бойынша бірдей болып қалмайтын, ал периодты өзгеретін дайындама болып саналады. Түсті металдар мен қорытпалар басымырақ мынандай қарапайым профилдерге илемденеді: пішіні кваратты, қаңылтырға ұқсайтын түрі бар жолақтар (тікбұрышты), әр түрлі өлшемі бар таспалар (қалыңдықтары 0,2-ден 25-30 мм-ге дейін өзгереді; қаңылтырдың ені 3000 мм-ге, ал таспаныкі 600 мм-ге жететін етіп жасалады; қалыңдыққа байланысты қаңылтырлар 6 м жететін ұзындықпен, ал таспалар 300 м және одан көп ұзындықпен жасалады). Илемдеудің технологолиялық сипаттамасы ретінде мынандай көрсеткіштерді қолданады: өнімділік; илемдеу жылдамдығы; бір өтімдегі деформация дәрежесі (жаншу); кермелеу. Жалпы жағдайда илемдеген кезде деформация дәрежесінің жалпы көрсеткіші болып мынандай формуламен есептелетін кермелеу саналады: λ = Fо/F1. Осы көрсеткішті дайындаманың көлденең қимасының ауданын F0 дайын бұйымның көлденең қимасының ауданына F1 бөліп табады. Мынандай мөлшерді: ΔH = H0 − H1 абсолюттік жаншу деп атайды, ал мынандай мөлшерді: εh = (ΔH/H0)⋅100% салыстырмалы жаншу деп атайды (мұндағы H0 және H1 – жартылай өнімнің, сәйкесті, деформацияға дейінгі және кейінгі биіктігі). Қаңылтырлы илемді (қаңылтыр, жолақ, таспа) өндіруді ыстықтай (қалыңқаңылтырлы материал) және суықтай (жұқақаңылтырлы материал, фольга) илемдеу тәсілдерімен іске асырады. Ыстықтай илемдеуді екі, үш және төрт пішінбілікті қаңылтыр илемдеу орнағында жүргізеді. Бастапқы материал болып әдістемелік пеште қыздырылатын массасы 7,5 тоннадан 45 тоннаға жететін слябтар саналады. Минимальды қалыңдығы 0,15 мм жететін болатты суықтай илемдеуді төрт-алты қапасты үздіксіз орнақта немесе орауышпен қамтамасыз етілген «кварто» орнағында жүргізеді. Алюминилік фольганы өндіру үшін үздіксіз құйылған дайындаманы қолданады. Осы дайындаманы 6 мм қалыңдықтан микрондық өлшемге дейін «кварто» орнағында илемдейді. Қаңылтырлы және сортты илемдерді өндіру үшін илемдеу цехторында әр түрлі типтері және белгілеулері бар орнақтарды орнатады. Шартты мынандай бірнеше топты бөліп көрсетеді: 1. Дайындаушы орнақтар: блюмингтер, слябингтер, үздіксіз дайындаушы орнақтар. Блюмингтер мен слябингтер – бұл пішінбіліктерінің диаметрі 850 – 1500 мм тең болатын ірі жаншушы жабдықтар. Осы жабдықтарда илемдеуді 11 – 15 өтімде кері қайтымды режіммен жүргізеді. Қағида бойынша, бұл тікбұрышты (сляб) және квадратты (блюм) дайындамалар түрінде ірі өлшемді дайындамаларды өндіру үшін қолданылатын бірқапасты орнақтар. Үздіксіз дайындаушы орнақтарды тікелей блюмингтен немесе слябингтен кейін орналастырады. Осы орнақ әрбіреуінде алты қапас бар екі үздіксіз топтан тұрады. Сортты орнақтарға мыналар жатады: ірі сортты, рельсарқалықты, орташасортты және кішісортты. Қаңылтырлы орнақтарға мыналар жатады: қалың қаңылтырды илемдейтін орнақтар; жұқа қаңылтырды (орамды) илемдейтін орнақтар. Құбыр илемдейтін орнақтарға мыналарды жатқызады: тесетін, жаймалайтын орнақтар және құбырды суықтай илемдейтін орнақтар, ал тағы пісірілген құбырды алу үшін қолданылатын орнақтар. Арнайы орнақтарға периодты, иілген профилдерді, шарды, дөңгелекті илемдейтін және басқа да орнақтарды жатқызады. Сортты илем орнақтарында негізгі параметр ретінде жұмысшы пішінбіліктердің диаметрін қабылдайды. Мысалы, «Кварто 400» орнағы белгілеуі мынаны білдіреді: орнақта 4 пішінбілік бар; осы пішінбіліктердің 2 тіреуші, ал 2 жұмысшы; жұмысшы пішінбіліктің диаметрі 400 мм. Қаңылтыр өндіретін орнақтарда негізі параметр ретінде пішінбіліктің бөшкесінің ұзындығы қабылданған. Сондықтан «Орнақ 2000» белгілеуі, осы орнақ пішінбілігінің бөшкесінің ұзындығы 2000 мм тең екендігін білдіреді. Жұмысшы қапастардың орналасуы бойынша илемдеу орнақтарын келесі түрлерге бөледі: бірқапасты; тізбекті; көпқапасты; бір ізді, жартылайүздіксіз және үздіксіз. Пішінбіліктерді мөлшерлеу деп илемдеу орнағының пішінбіліктерінде орналасып, берілген өлшемі бар профилді алуды қамтамасыз ететін мөлшерлегіштің тізбегін айтады. Орнақтың типіне байланысты әрбір мөлшерлегіште металды бір немесе бірнеші өтіммен илемдейді. Нәтижесінде дайындама керекті қимасы бар илемге айналады. Мөлшерлеу түсінігі мыналарды өзіне тағы да қосады: мөлшерлегіштің пішіні мен өлшемін анықтау; осы мөлшерлегіштерді илемдеу орнағының пішінбіліктерінде орналастыру (яғни пішінбіліктердің мөлшерлегішін жобалау процесі). Мөлшерлегіштерді екіпішінбілікті үшін және көппішінбілікті үшін деп екіге бөледі. Сонымен бірге кейбір пішіндері бірдей мөлшерлегіштер екі және одан да көп пішінбіліктермен құрылуы мүмкін. Илемдеу өндірісінің практикасында мынандай мөлшерлегіштер орын тапты: екіпішінбілікті; үшпішінбілікті және төртпішінбілікті. Мөлшерлегіштерді пішіні бойынша, пішінбіліктерде орналасуы бойынша және белгіленуі бойынша топтайды. Пішіні бойынша мөлшерлегіштерді мынандай екі негізгі топқа бөледі: қарапайым пішінді (жәшікті немесе тікбұрышты, ромбылы, алтыбұрышты, сопақ пішінді, дөңгелек пішінді, квадратты, алтықырлы) және фасонды пішінді (арқалықты, швеллерлі, бұрышты, рельсті, таврлы және т.б.). Пішінбіліктерде орналасуы бойынша мөлшерлегіштерді былай айырады: ашық, жабық, жартылай жабық және диагональді. Ашық мөлшерлегіште пішінбіліктер белдемесі арасындағы көлденең саңылау жуықты мөлшерлегіш биіктігінің ортасында орналасады. Жабық мөлшерлегіште жоғырада айтылған саңлау мөлшерлегіш шегінің сыртында орналасады, ал жартылай жабық мөлшерлегіште – мөлшерлегіш табанына немесе немесе шыңына жақын жерлерде орналасады. Диагональды мөлшерлегіште белдеме арасындағы саңлау диагональ бойынша орналасады (мысалы, сол жақтағы белдемеде мөлшерлегіштің төменгі жағында, ал оң жақтағы белдемеде мөлшерлегіштің жоғары жағында орналасады). а – ойық ; б – шығыңқылық; в – ойық және шығыңқылық, г - ойық және шығыңқылық. Жылғалармен құрылған мөлшерлегіштерді белгілеуі бойынша былай бөледі: жаншитын, қаралай өңдейтін, алдын ала тазалай өңдейтін және тазалай өңдейтін. Жаншитын мөлшерлегіштер бастапқы құймакесектің, блюмнің немесе дайындаманың көлденең қимасының ауданын кішірейту үшін арналған. Жаншитын мөлшерлегіште өңдеудің мақсаты кейінірек керекті профиль жасалатын дайындаманы алу. Жаншушы мөлшерлегіш ретінде әдетте жәшікті мөлшерлегішті қолданады. Осы мөлшерлегіштер блюмингті және дайындаушы орнақтарда, ал тағы да сортты орнақтардың бірінші өтімдерінде илемдеген кезде қолданады. Қаралай өңдейтін мөлшерлегіштер илемденетін фасонды профильдерді (мысалы, екітаврлы арқалықтар, швеллерлер және т.б.) біртіндеп жасауға арналған. Сортты орнақтарда қаралай өңдейтін мөлшерлегіштер жаншушы мөлшерлегіштерден кейін орналасады. Карапайым сортты профилдерді (дөңгелек, кварат, алтықыры бар) илемдеген кезде қаралай өңдейтін мөлшерлегішерге қарапайым пішіні бар мөлшерлегіштерді жатқызады. Осы соңғы мөлшерлегіштерде өңделіп жатқан дайындаманың көлденең қимасының ауданы ары қарай азайады. Осындай да бұл мөлшерлегіштерді ең үлкен кермелеуді қамтамасыз ететіндей ретпен орналастырады, яғни олар кермелеуші ретінде қолданылады. Қаралай өңдейтін мөлшерлегіштер орнақтың қаралай өңдейтін және аралық топтарында қолданылады. Бастапқы материалдардан әр түрлі түрде металл шығаратын толық металлургиялық циклі бар металлургиялық завод құрамына келесі цехтар кіреді: доменді цех (шойын өндіру); мартендік, конверторлы, электрбалқыту цехтары (болатты және басқа материалдарды өндіру); ыстықтай илемдеу цехтары (ыстықтай илемделген илем және құбырлар); суықтай илемдеу цехтары (қалыңдығы бойынша өлшемдердің дәлдігімен, бет жағы жақсы тазалай өңделумен, ал тағы да қосымша физика-механикалық қасиетпен айрмашылықта болатын суықтай илемделген қаңылтырды, жолақты және құбырды өндретін); мөлшерлейтін цехтар (бетінің сапасы жоғары және өлшемі бойынша шақтамасы жақсы болатын шыбықты және додалы мөлшерленген металды өңдіретін); антижегіделі және басқа түрлі қаптама цехторы (қалайлылау, мырыштау, алюминдеу, хромдау және т.б.); иілген профилді шығаратын цехтар (қаңылтырлы илемнен |