ПОЗНАВАТЕЛЬНОЕ Сила воли ведет к действию, а позитивные действия формируют позитивное отношение Как определить диапазон голоса - ваш вокал
Игровые автоматы с быстрым выводом Как цель узнает о ваших желаниях прежде, чем вы начнете действовать. Как компании прогнозируют привычки и манипулируют ими Целительная привычка Как самому избавиться от обидчивости Противоречивые взгляды на качества, присущие мужчинам Тренинг уверенности в себе Вкуснейший "Салат из свеклы с чесноком" Натюрморт и его изобразительные возможности Применение, как принимать мумие? Мумие для волос, лица, при переломах, при кровотечении и т.д. Как научиться брать на себя ответственность Зачем нужны границы в отношениях с детьми? Световозвращающие элементы на детской одежде Как победить свой возраст? Восемь уникальных способов, которые помогут достичь долголетия Как слышать голос Бога Классификация ожирения по ИМТ (ВОЗ) Глава 3. Завет мужчины с женщиной 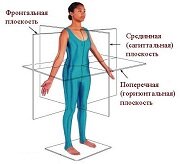
Оси и плоскости тела человека - Тело человека состоит из определенных топографических частей и участков, в которых расположены органы, мышцы, сосуды, нервы и т.д. Отёска стен и прирубка косяков - Когда на доме не достаёт окон и дверей, красивое высокое крыльцо ещё только в воображении, приходится подниматься с улицы в дом по трапу. Дифференциальные уравнения второго порядка (модель рынка с прогнозируемыми ценами) - В простых моделях рынка спрос и предложение обычно полагают зависящими только от текущей цены на товар. | Суммарная скорость нескольких последовательных превращений, широко различающихся по скорости, определяется скоростью наиболее медленной стадии. Основой кинетики реакций на поверхностях твердых тел в идеальном адсорбированном слое является закон действующих поверхностей . Этот закон, сформулированный И. Лэнгмюром [327] одновременно с теорией адсорбции, занимает в кинетике гетерогенных каталитических процессов место, аналогичное месту закона действующих масс в кинетике гомогенныхреакций. Скорость химической реакции — изменение количества одного из реагирующих веществ за единицу времени в единице реакционного пространства. Является ключевым понятием химической кинетики. Скорость химической реакции — величина всегда положительная, поэтому, если она определяется по исходному веществу (концентрация которого убывает в процессе реакции), то полученное значение умножается на −1. Например, для реакции: А+В->С+Д выражение для скорости будет выглядеть так:  В 1865 году Н. Н. Бекетовым и в 1867 году Гульдбергом и Вааге был сформулирован закон действующих масс:Скорость химической реакции в каждый момент времени пропорциональна концентрациям реагентов, возведенным в степени, равные их стехиометрическим коэффициентам. Для элементарных реакций показатель степени при значении концентрации каждого вещества часто равен его стехиометрическому коэффициенту, для сложных реакций это правило не соблюдается. Кроме концентрации на скорость химической реакции оказывают влияние следующие факторы: · природа реагирующих веществ, · наличие катализатора, · температура (правило Вант-Гоффа), · давление, · площадь поверхности реагирующих веществ. Если мы рассмотрим самую простую химическую реакцию A + B → C, то мы заметим, что мгновенная скорость химической реакции величина непостоянная. Химическая реакция (процесс) состоит в превращении одного или нескольких химических веществ, называемых исходными веществами, в одно или несколько других химических веществ, называемых продуктами реакции. Химические реакции, как правило, являются сложными, т. е. протекают через ряд элементарных стадий. Элементарная стадия является наиболее простой составной частью сложной реакции: каждый акт элементарной стадии представляет собой результат непосредственного взаимодействия и превращения нескольких частиц. Совокупность реакций из элементарных стадий называется механизмом реакции. При протекании реакции по стадиям получаются и расходуются промежуточные вещества. Промежуточными веществами обычно являются активные частицы с не спаренными электронами, так называемые радикалы. Сложные реакции могут состоять из двусторонних, параллельных и последовательных элементарных стадий. Все элементарные стадии являются двусторонними (обратимыми), т. е. - состоят из двух взаимно противоположных элементарных реакций, которые одновременно протекают в прямом и обратном направлениях, но с разной скоростью. При параллельном протекании нескольких элементарных стадий данное вещество одновременно расходуется по нескольким путям с образованием разных продуктов. При последовательном протекании элементарных стадий промежуточное вещество, полученное в одной стадии, расходуется другой. Механизм большинства реакций точно не известен, так как промежуточные вещества обычно очень неустойчивы и доказать экспериментально их существование довольно сложно. Поэтому, как правило, у сложных реакций промежуточные вещества неизвестны, а известен только наиболее вероятный механизм, т. е. предполагаемый механизм протекания реакции по стадиям, на основе которого можно получить закономерность (математическую модель), адекватно отражающую основные черты реального процесса. Таким образом, элементарной стадией химической реакции называется сумма актов химического превращения при одновременном сближении (столкновении) нескольких (обычно двух) частиц; при этом энергия связей перераспределяется между атомами с образованием активированного комплекса с его последующим распадом и получением новых частиц. В случае мономолекулярного акта образование активированного комплекса происходит за счет перераспределения энергии между связями атомов внутри молекулы, как следствие ее активации в результате внешних воздействий. Селективность.Выход продукта характеризует полученный результат, как долю от предельно возможного результата. Целесообразно оценить и реальную ситуацию, т. е. дать количественную оценку эффективности целевой реакции по сравнению с побочными взаимодействиями. Энергия активации элементарной реакции Е – это минимальный избыток энергии над средней внутренней энергией молекул, необходимый для того, чтобы произошло химическое взаимодействие (энергетический барьер, который должны преодолеть молекулы при переходе из одного состояния реакционной системы в другое) Пламенный реактор для конверсии жидких углеводородов Пламенные реакторы с предварительным смешением газов состоят из камеры смешения, диффузора, в котором заканчивается процесс смешения, и камеры сгорания, в которую равномерно поступают газы из диффузора. Промышленные горелки бывают пламенными и беспламенными. Пламенный реактор с диаметром D - 0 20 м находится на границе критической зоны тепловой устойчивости в зависимости от физических свойств сырья. Промышленные реакторы имеют диаметр не менее 0 25 м, в зависимости от химического состава и физических свойств сырья. Пламенный реактор такого диаметра имеет, как правило, производительность не менее 0 25 т ( UFg) / 4 или больше. Производительность мощного промышленного пламенного реактора превышает 1 т / ч; при необходимости производительность единичного аппарата можно еще повысить. Пламенные реакторы с предварительным смешением газов состоят из камеры смешения, диффузора, в котором заканчивается процесс смешения, и камеры сгорания, в которую равномерно поступают газы из диффузора. Промышленные горелки бывают пламенными и беспламенными. Пламенные реакторы относительно просты по устройству. Они состоят, как правило, из сопла (форсунки) для подачи исходных реагентов, цилиндрического или слегка расширяющегося книзу корпуса, сборника продуктов и системы обеспыливания отходящих газов. Расчет пламенных реакторов связан в основном с определением гидродинамических характеристик газового потока (холодного факела) и особенностями гидродинамики, горящего-факела. Верхняя часть пламенного реактора со смесителем уранового сырья со фтором. В промышленных пламенных реакторах сырьем является так называемое вторичное сырье, выгружаемое из системы улавливания фтора, расположенной за пламенным реактором. Экспериментально установлен состав вторичного сырья, при котором не происходит налипания на стенки реактора. Вторичное сырье подают в пламенный реактор шнеком. Верхняя часть пламенного реактора со смесителем уранового сырья со фтором. Она включает диспергатор 1, ось с крыльчаткой 2, шнек для транспорта дисперсного сырья в реактор 5, сопла для ввода фтора 4 ( до 20 шт. ). Тепловая устойчивость пламенного реактора в зависимости от температуры стенок. 1, 2, 3 - режимы работы реактора при различной теплопередаче через стенки с температурами Tci ТС2 Тсз.| Тепловая устойчивость пламенного реактора в зависимости от дисперсности сырья. 1, 2, 3 - режимы работы пламенного реактора в зависимости от тепловыделения для размеров частиц. Температура стенок пламенного реактора регулируется интенсивностью охлаждения. Однако применение пламенных реакторов в промышленных масштабах оправдано лишь в том случае, если скорость реакции достаточно велика, и для завершения процесса требуется время, не превышающее 0 5 - 1 0 сек. В противном случае эксплуатация реактора чрезвычайно усложнилась бы из-за его больших размеров. Поскольку интенсификация химических процессов в большинстве случаев достигается увеличением температуры, то пламенные реакторы отличаются от сопоставимых с ними других реакторов именно высокой рабочей температурой реагирующей смеси. Минимальными значениями температуры можно считать 600 - 800 С, но в большинстве случаев температура в зоне горения факела превышает 1000 и даже 2000 С. Ограничения применимости пламенных реакторов могут быть связаны и с величиной константы равновесия реакции. Если с повышением температуры, что необходимо для достижения высоких скоростей реагирования, константа равновесия заметно убывает, то применение реактора становится неоправданным. К таким реакциям относится процесс гидрофторирования двуокиси урана, равновесное состояние для которого уже при 500 - 700 С заметно сдвинуто в сторону гидролиза тетрафторида урана. При расчете пламенных реакторов исходят прежде всего из результатов, полученных на опытных установках. Если испытания не проводили, то необходимо опираться на литературные данные. Тепловая устойчивость пламенного реактора в зависимости от температуры стенок. 1, 2, 3 - режимы работы реактора при различной теплопередаче через стенки с температурами Тс ТС2 Тсз.| Тепловая устойчивость пламенного реактора в зависимости от дисперсности сырья. 1, 2, 3 - режимы работы пламенного реактора в зависимости от тепловыделения для размеров частиц. Температура стенок пламенного реактора регулируется интенсивностью охлаждения. Следовательно, при фиксированной зависимости Ql / ( Т) возможны различные режимы работы, обусловленные различными значениями Тс. Однако величина Тс ограничивается стабильностью материала, из которого изготовлен пламенный реактор. Кроме того, это влияние наблюдается в случае не слишком широкого реактора, когда пламя касается его стенок. Когда такого касания нет, величина Тс практически не влияет на устойчивость пламени. Такой режим работы не применим в технологии получения гексафторида урана сжиганием во фторе дисперсного уранового сырья. По характеру теплообмена пламенные реакторы работают в режиме, близком к чисторадиационному, который возможен при условии, что температура газов и стенок реактора превышает 1000 С и конвективный перенос тепла весьма незначителен. Схема верхней части пламенного реактора для получения гексафторида урана взаимодействием в газовой взвеси фтора с оксидным или фторидным урановым сырьем. Поэтому интерес к пламенному реактору для получения гексафторида урана фторированием оксидного или фторидного сырья в газовой взвеси не противоречит, с нашей точки зрения, общим концепциям, сформулированным выше. При проведении восстановления в пламенном реакторе образующийся на стенках гарнисаж затрудняет теплопередачу. В связи с этим поддерживают довольно низкую температуру стенок, а в зону реакции подают небольшие количества фтора или атомарного водорода. При взаимодействии фтора с водородом или рекомбинации атомов водорода выделяется тепло, достаточное для поддержания реакции восстановления. Пламенный реактор с горячими стенками для восстановления UFe. При внедрении в технологию урана пламенные реакторы были значительно изменены, так как к конечным продуктам передела предъявлялись требования высокой чистоты. Интересно отметить, что требование высокой экзотермичности основной реакции не является лимитирующим при оценке возможности применения пламенных реакторов. Так, для повышения количества выделяемого тепла в процессе восстановления гаксафторида урана водородом в реактор вводят элементарный фтор или атомарный водород. Рекомбинация атомарного водорода сопровождается выделением 431 3 кдж / моль. Параметры, определяющие тепловую устойчивость пламенного реактора. Практические результаты проектирования и эксплуатации различных пламенных реакторов применительно к фторированию UF4 и UsOg-1. Вероятность таких синтезов увеличивается при фторировании сырья, содержащего крупные частицы с низкой удельной поверхностью. Аппаратурно-технологическая схема получения гексафторида урана. О методах контроля процессов в пламенных реакторах имеется очень мало сообщений. Кривые относительных скоростей. Схема горящего факела при центральном зажигании. Для создания описанного режима в пламенном реакторе важным условием является по возможности наименьшая теплоотдача от циркулирующих потоков стенкам реактора. Возможности применения плазмотронов, которые обладают всеми достоинствами пламенных реакторов, но отличаются более высокими температурами и значительно большей интенсивностью процессов, в технологии ядерного горючего могут быть шире, чем возможности использования пламенных реакторов. В заключение следует отметить, что не всегда в пламенных реакторах доминирует передача тепла излучением. При небольших значениях эффективной длины лучей S, а также при больших отношениях диаметра насадка к диаметру реактора увеличивается вклад конвективной составляющей теплопередачи. В некоторых случаях, даже при температурах порядка 1500 С, конвекцией передается до 50 % от общего количества передаваемого газами тепла. Степень превращения (основной показатель процесса фторирования тетрафторида урана) в пламенном реакторе оказалась очень высокой - более 99 % при концентрации фтора в азоте 38 % мольн. Следует отметить, что в связи с меньшей коррозией аппаратуры загрязнение получаемого гексафторида урана металлами (примесями) значительно меньше по сравнению с процессами в других аппаратах. Зависимость приведенной константы k скорости реакции фторирования тетрафторида урана от обратной температуры. Еще более экзотермичны реакции фторирования окислов урана, которые можно проводить в пламенных реакторах. При переработке относительно малых количеств обогащенного материала целесообразно фторировать окислы урана непосредственно в пламенном реакторе. Переход окиси в гексафторид урана достаточно полный, хотя вследствие выделения большого количества тепла производительность реактора ниже, чем при фторировании тетрафторида. Сохранение динамического равновесия ( неподвижности) пламени является важным условием обеспечения нормальной производительности и безопасности работы пламенных реакторов. . Потеря напора в псевдоожиженном слое. Области существования взвешенного слоя.Взвешенный» псевдоожиженный или «кипящий» слой — частицы в результате воздействия движущейся через слой газовой или жидкой фазы находятся в хаотическом движении в пределах слоя, напоминая кипящую жидкость. Расстояние между частицами и объем слоя изменяются в зависимости от скорости потока, проходящего через слой. При восходящем потоке газа (паров или жидкости) через плотный слой зернистого материала при увеличении скорости потока растет сопротивление слоя и ослабляется взаимное давление частиц. При достижении некоторого критического значения скорости Wк сопротивление слоя становится равным его весу, частицы перестают оказывать взаимное давление, слой переходит во взвешенное состояние, частицы получают возможность перемещаться в пределах слоя. При дальнейшем увеличении скорости потока W>Wк расстояние между частицами увеличивается, порозность слоя е возрастает, вызывая тем самым снижение скорости потока в поровом канале (W0=W/ε), а следовательно, и силы, действующей на частицу, до значения, равного ее весу. Тогда восстанавливаются условия состояния взвешенного слоя, но уже при новом, большем значении его порозности ε. При дальнейшем увеличении скорости потока слой расширяется. В пределе его расширения порозность слоя стремится к значению ε=1, когда расстояние между частицами становится столь значительным по сравнению с их размерами, что концентрация частиц в данном объеме 1-ε будет несоизмеримо мала. Практически пределом существования взвешенного слоя является скорость потока, равная скорости витания данной частицы Wa; при скорости выше Wa поток выносит частицы из слоя и последний прекращает свое существование.При расширении слоя более чем на 20% потери напора начинают возрастать. Во взвешенном слое вследствие некоторой неравномерности скорости потока в различных сечениях слоя частицы интенсивно и хаотически перемешиваются внутри слоя. Взвешенный слой зернистого материала называют также кипящим или псевдоожиженным слоем. Подобное наименование возникло потому, что взвешенный слой зернистого материала обладает подвижностью, текучестью, вязкостью, способностью к отстаиванию более крупных частиц и другими особенностями, характерными для жидкостей, да и по внешнему виду он похож на кипящую жидкость. Интенсивное перемешивание частиц во взвешенном слое обусловливает высокую эффективность проходящих процессов: значительно возрастает скорость внешней диффузии, эффективнее протекает теплообмен между потоком и частицами, между частицами и соприкасающейся с ними поверхностью, легко обеспечивается выравнивание температур в большом объеме слоя и т.д. Вместе с тем в связи с интенсивным перемешиванием частиц взвешенному слою свойствен и ряд недостатков, среди которых уменьшение движущей силы процесса, износ твердых частиц, эрозия аппаратуры и др. Промышленные реакторы. Трубчатые, змеевиковые реакторы. Промышленный реактор (Production reactor) – ядерный реактор, предназначенный главным образом для производства делящихся материалов в промышленном масштабе. Обычно этот термин относится к реакторам для производства плутония, урана-233 итрития. В связи с малой производительностью ускорителей, промышленная наработка плутония шла наядерных реакторах. Первыми промышленными реакторами – наработчиками плутония – были канальные реакторы на тепловых нейтронах с графитовым замедлителем и прямым проточным воднымохлаждением, работающие на природном металлическом уране при сравнительно низких температурах. Сокращённо такие реакторы называют ПУГР – промышленныйурано-графитовыйреактор). Чтобы получать плутоний в достаточном количестве, нужны сильнейшие нейтронные потоки. В принципе, любой атомный реактор является источником нейтронов, но для промышленного производства плутония используется специально разработанный для этого. Помимо высоких потоков нейтронов, особенностью промышленного реактора является возможность удаления облучённого материала без остановки реактора. Впервых промышленных реакторах использовалась проточная схема охлаждения, когда вода забиралась из водоема, после очистки охлаждала активную зону и сбрасывалась для охлаждения в другую часть водоема. В 1950 были начаты исследования повозможности перехода назамкнутый контур охлаждения, что позволяет существенно сократить выход радиоактивности в окружающую среду. Такой двух контурный уран-графитовый реактор ЭИ-2 был разработан в НИКИЭТ (НИИ-8), ис 1958 он действовал на СХК. Эта линия развития промышленных реакторов стала основной и была использована в новых реакторах типа АДЭ, которые были построены как на СХК, так и на Красноярском ГХК. Существуют и промышленные реакторы на обычной воде. Пример - реактор «Руслан», пущенныйна«Маяке» в 1985. Это реактор бассейнового типа, в котором теплоносителем и замедлителем одновременно является обычная (лёгкая) вода высокой степени очистки (бидистиллят). Отвод тепла осуществляется по двух контурной схеме. Реактор используется для наработки плутония и радиоактивных изотопов. Работает в режиме кампаний. По окончании каждой кампании производится перегрузка топлива, а в течение кампании делается несколько остановок для перегрузки поглотителей и выполнения ремонтных работ. Наработка плутония первоначально проводилась на уран-графитовых реакторах, но в последствии к ним подключились мощные реакторы на тяжёлой воде. В 1944 осуществлён пуск первого ядерного реактора на природном уране с тяжелой водой в качестве замедлителя (Аргоннская национальная лаборатория. США). В 1949 осуществлён пуск первого советского тяжеловодного реактора (А.И.Алиханов). В 1951 на «Маяке» были пущен промышленный тяжёловодный реактор ОК-180. Подобные реакторы использовались с начала для наработки плутония для атомных зарядов, потом одновременно плутония итрития – одного из компонентов водородной бомбы, а в настоящее время с их помощью производят широкую номенклатуру радиоактивных изотопов, легирование кремния и т.п.Для многотоннажного производства в качестве окислительных аппаратов употребляют пустотелые колонны, также трубчатые змеевиковые реакторы с вертикальным расположением труб. Окисление сырья в трубчатом реакторе происходит в турбулентном потоке воздуха. Движение воздуха и сырья — прямоточное. При всем этом содержание кислорода в газовой фазе миниатюризируется экспоненциально. Основное количество битумов выходит в окислительных колоннах, где процесс протекает в барботажном слое. Процесс окисления в кубе начинают с закачки сырья, после этого в низ куба через барботер подают воздух. Расход воздуха изменяют, таким образом, чтоб температура окисления поддерживалась на нужном уровне: при понижении температуры наращивают расход воздуха, при повышении — уменьшают. Готовый продукт сливают самотеком. Вследствие маленький высоты барботажного слоя степень использования кислорода воздуха в реакциях окисления невелика. На окисление в змеевиковый трубчатый реактор подают смесь сырья, воздуха и рециркулята — готового битума. На выходе из змеевика прореагировавшая газожидкостная смесь делится на газовую и водянистую фазы в сепараторе, газы выводят с верха сепаратора, жидкость — с низа. Поток воды делят, огромную часть возвращают в процесс, наименьшую выводят в качестве готового продукта. Размер рециркулята определяют, исходя из необходимости обеспечения в обскурантистской консистенции более 8% водянистой фазы (по размеру), что требуется для сотворения развитой поверхности контакта с целью заслуги высокой степени использования кислорода воздуха, и удельного расхода воздуха на окисление. Пути интенсификации реакторных устройств. (Лекция 15)Схема расчета реакционных аппаратов. Расчет основных размеров реакторов. Расчет аппаратов выполняется с целью обоснования его размеров, выбор оптимального режима работы, определении и расходов(топливо, водяной пар, вода, электроэнергия, реагенты, катализатор и пр.), выбор конструкции аппарата в целом и его отдельных узлов, а также и материального оформления. Основными являются следующие три типа расчетов, выполняемых для процессов и аппаратов: технологический, гидравлически и механический. Технологически расчет. При его проведении обосновываются рабочий параметр процесс (давление, температур и т.п.), определяются материальный и энергетически поток и уточняются расходные нормы. Гидравлически расчет. При его проведении определяются размер рабочих сечений аппарата и перепад давления, обеспечивающий работу при полученных в технологическом расчете материальных и энергетических потока рабочих сред. Механически расчет. При его проведении обосновываются выбор материалов, конструкций элементов аппарата, толщин стенок и т.п., обеспечивающим безопасную, надежную и длительную эксплуатацию аппарата. Расчет процессов и аппаратов является одним и основных факторов, обеспечивающих выбор экономически целесообразных и технически оправданных условий работы оборудования. При использовании стандартизованной аппаратуры проводится проверочный расчет, задачей которого является обоснование производительности аппарата и режим егр работы на основе имеющихся размеров, а также выявление возможности использования данного стандартного аппарата при заданных рабочих условиях. Для расчета размеров аппарата (площади поперечного сечения, высоты, размеров внутренних устройств и т.п.) недостаточно знать только внешние потоки веществ и энергии, необходимо определить материальные и тепловые потоки в соответствующих сечениях внутри аппарата. Реактор с твердым теплоносителем для прямого окисления атмосферного азота.Вредное влияние окислов азота, образующихся прп сжигании всех видов топлива в результате окисления атмосферного азота при высоких температурах в топках котлов — проблема сравнительно новая и недостаточно изученная. В последние годы в СССР установлено, что при сжигании различных топлив в дымовых газах содержится до 1 г/м окислов азота (в пересчете на КОа). Применяя различные меры по снижению образованияокислов азота при сжигании топлив, можно снизить их концентрацию вдымовых газах только до 0,5 г/м . Оксиды азота образуются за счет окисления атмосферного азота во всехтехнологических процессах, проходящих при температурах, значительно превышающих тысячу градусов, в частности в электрических печах I—>-3000°С), в топливных металлургических печах (—)-1600°С) и т. д. При температуре выше 2000 °С становится заметным окисление атмосферного азота, которое протекает по реакции Главной проблемой при использовании алканов как топлив являетсязагрязнение окружающей среды за счет сгорания примесей, имеющихся в алканах, неполного сгорания самих алканов и окисления атмосферного азота впроцессе сгорания. Эти проблемы являются наиболее острыми при использовании алканов как топлива в двигателях внутреннего сгорания.Технологические аспекты использования топлив и меры, принимаемые для уменьшения выделения несгоревших алканов, оксида углерода и оксидов азотаавтомашинами и реактивными двигателями выходят за рамки этой главы. Внастоящее время алканы легко доступны и могут быть получены из природного газа, нефти и путем каталитического крекинга высококипящих сырых нефтяных фракций [6]. [c.96] Явление окисления атмосферного азота в электрической дуге было обнаружено еще В. В. Петровым. На основе этого явления в начале текущего столетия был разработан и получил промышленное применение дуговой способ получения азотной кислоты (Норвегия, Швеция). Основная масса окислов азота образуется при сжигании всех видов топливав результате окисления атмосферного азота при высоких температурах втопках котлов и печей. В дымовых газах содержится до 1 г/м окислов азота (в пересчете на МОг). Другим источником поступления окислов азота Общим недостатком полимеров является их способность к окислению атмосферным кислородом. Окисление протекает во всех случаях, когда полимер находится в контакте с воздухом при переработке, хранении и эксплуатации полимеров, полимерных материалов и изделий и сопровождается изменениемфизических и химических свойств полимера, а в пределе — его полным разрушением. Одновременно в ходе окисления образуютсянизкомолекулярные продукты, многие из которых токсичны или обладают неприятным запахом. Единственным способом прекращения процессов окисления полимера является полная изоляция его от кислорода и других окислителей, что возможно только в исключительных условиях. Для случаев, когда такая изоляция невозможна, разработаны различные методы замедления процессов, протекающих в полимере под действием кислорода, получившие название антиокислительной стабилизации полимеров. [c.5] Основными причинами образования оксидов азота в отходящих дымовых газах реакторов огневого обезвреживания являются окисление атмосферного азота и образование оксидов азота нз азотсодержащих соединений В области температур отходящих газов 900—1200 °С, характерных дляогневого обезвреживания от.ходов, равновесие реакции 2N0 a N2-Ь02 сильно сдвинуто вправо, т. е. с позиций термодинамики содержание N0 в отходящих газах должно быть ничтожно мало. Однако скорость диссоциации N0 очень мала, и концентрация его при обезвреживании некоторых азотсодержащих соединений может оказаться намного выше равновесной. Наоборот, приокислении атмосферного азота при умеренных температурах в топочных устройствах концентрация N0 в отходящих газах может быть на порядок ниже равновесной [177]. [c.120] Образование оксидов азота при окислении атмосферного азота. Образование МО.х при окислении ат.мосферного азота в процессах огневого обезвреживания отходов в циклонных реакторах не имеет существенного значения. На образование ЫО большое влияние оказывает организация рабочего процесса. Как правило, в циклонных реакторах зона горения топливапространственно отделена от зоны испарения капель отходов и окисления примесей. Однако зона горения находится в состоянии лучистого теплообмена сзоной обработки отходов, для которой характерны умеренные температуры. Поусловиям окисления примесей и надежного выпуска расплава солейтемпература отходящих газов обычно составляет 950—1100°С. В этих условияхзначительное количество тепла из зоны горения может передаваться излучением в зону обработки отходов. Поэтому процесс горения топлива даже при. хорошей изоляции зоны горения протекает прн сравнительно невысоких температурах — не выше 1400—1500 °С (прн использовании неподогретого воздуха), что предопределяет низкую степень окисления ат.мосфер-ного азота. Реактор синтеза аммиака.В качестве основного реакционного аппарата синтеза аммиака используется многополочная колонна. Колонна представляет собой цилиндр высотой около 30 м и диаметром примерно 2,5 м, выполненный из специальной стали, способной выдерживать высокие давления, температуры и агрессивное воздействие азота, водорода и аммиака. Холодный газ подается в нижнюю часть колонны и направляется вверх между корпусом колонны и корпусом катализаторной коробки. В верхней части реактора холодный газ попадает в межтрубное пространство теплообменника, в котором он нагревается до 400°С за счет теплоты выходящего из реактора по трубам теплообменника газа синтеза. Подогретая азотно-водородная смесь проходит последовательно четыре слоя катализатора и попадает в центральную трубу, по которой направляется к теплообменнику. При этом газ охлаждается примерно до 330°С.В связи с тем, что реакция синтеза аммиака экзотермична газ на катализаторных полках сильно нагревается. При этом температура значительно отклоняется от оптимальной. Для регулирования температурного режима предусмотрена подача байпасного потока холодной азото-водородной смеси через патрубки в каждый слой катализатора.Синтез аммиака протекает в соответствии со стехиометрическим уравнением  Реакторы вытеснения. Конструктивное оформление реакторов вытеснения.Реакторы вытеснения – трубчатые аппараты, имеющие вид удлиненного канала. В трубчатых реакторах перемешивание имеет локальный характер и вызывается неравномерностью распределения скорости потока и ее флуктуациями, а также завихрениями. Идеальное вытеснение предполагает, что любое количество реагентов и продуктов через реактор перемещается по длине реактора (в пространстве); в соответствии с особенностями реакции и сопровождающих ее физических явлений устанавливается определенное распределение концентраций участников реакции, температуры и других параметров. Реактор идеального вытеснения представляет собой длинный канал, через который реакционная смесь движется в поршневом режиме. Каждый элемент потока, условно выделенный двумя плоскостями, перпендикулярными оси канала, движется через него как твердый поршень, вытесняя предыдущие элементы потока и не перемешиваясь ни с предыдущими, ни со следующими за ним элементами. Рис. 5.4. Схема реактора идеального вытеснения Естественно, что при проведении химической реакции, например реакции, в которой участвуют два или более реагентов, перемешивание участников реакции является необходимым условием ее осуществления, иначе невозможным будет контакт между разноименными молекулами, в результате которого и происходит элементарный акт реакции. Если в реакторе идеального смешения перемешивание носит глобальный характер и благодаря ему параметры процесса полностью выравниваются по объему аппарата, в реакторе идеального вытеснения перемешивание является локальным: оно происходит в каждом элементе потока, а между соседними по оси реактора элементами, как уже указывалось, перемешивания нет. Идеальное вытеснение возможно при выполнении следующих допущений: 1) движущийся поток имеет плоский профиль линейных скоростей; 2) отсутствует обусловленное любыми причинами перемешивание в направлении оси потока; 3) в каждом отдельно взятом сечении, перпендикулярном оси потока, параметры процесса (концентрации, температуры и т. д.) полностью выравнены. Реакторы каталитического крекинга с движущимся слоем катализатора. Каталитический крекинг - термокаталитическая переработка нефтяных фракций с целью получения компонента высокооктанового бензина, легкого газойля и непредельных жирных газов. Каталитический крекинг - один из важнейших процессов, обеспечивающих глубокую переработку нефти. Внедрению каталитического крекинга в промышленность в конце 30-х гг. 20 в. (США) способствовало создание эффективного с большим сроком службы катализатора на основе алюмосиликатов (Э. Гудри, 1936 г).Основное достоинство процесса - большая эксплуатационная гибкость: возможность перерабатывать различные нефтяные фракции с получением высокооктанового бензина и газа, богатого пропиленом, изобутаном и бутенами; сравнительная легкость совмещения с другими процессами, например, с алкилированием, гидрокрекингом, гидроочисткой, адсорбционной очисткой, деасфальтизацией и т. д. Такой универсальностью объясняется весьма значительная доля каталитического крекинга в общем объёме переработки нефти. При каталитическом крекинге происходят следующие основные реакции: разрыв связей С-С, то есть перераспределение водорода (гидрирование и дегидрирование), деалкилирование, дегидроциклизация, полимеризация, конденсация. Каталитический крекинг проводят в прямоточных реакторах с восходящим потоком микросферического катализатора (лифт-реакторах) или в реакторах с нисходящим компактным слоем шарикового катализатора. Отработанный катализатор непрерывно выводят из реакторов и подвергают регенерации путем выжига кокса в отдельном аппарате. Реактор - с кратность циркуляции катализатора к сырью - 10:1 (для установок с лифт-реактором), температура - 510-540 °C, давление - 0,5-2 атм Регенератор :температура - 650-700 °C, давление - 1-3 атм Используется цеолитсодержащий микросферический катализатор (размер частиц 35-150 мкм). Площадь поверхности 300-400 м²/гр. Он представляет собой крекирующий цеолитный компонент, нанесенный на аморфную алюмосиликатную матрицу. Содержание цеолита не превышает 30%. В качестве цеолитного компонента используется ультрастабильный цеолит Y, иногда с добавками цеолита ZSM-5 для увеличения выхода и октанового числа бензина. Ряд компаний при приготовлении катализатора также вводят в цеолит редкоземельные металлы. В катализаторе крекинга также содержатся добавки, уменьшающие истирание катализатора, а также промоторы дожига СО, образующегося в регенераторе при выжиге кокса, до СО2. Различают установки по организации процесса: Периодические (реакторы Гудри). Через нагретый стационарный слой катализатора пропускают сырье и после того как он закоксуется реактор ставят на регенерацию; Непрерывной регенерации. Из реактора выводится закоксованный катализатор, с поверхности которого выжигается кокс в отдельном аппарате и возвращается в реактор. После регенерации катализатор сильно нагрет, чего хватает для процесса крекинга, поэтому процесс каталитического крекинга не нуждается в подводе внешнего тепла. Установки непрерывной регенерации подразделяются: Реакторы с движущимся слоем катализатора. Слой шарикового катализатора движется сверху вниз по реактору навстречу поднимающимся парам сырья. При контакте происходит крекинг, катализатор через низ отправляется на регенерацию, продукты на разделение. Регенерация протекает в отдельном аппарате с помощью воздуха; при этом выделяющееся при сгорании кокса теплоиспользуют для генерации пара. Типовая установка - 43-102. Реакторы с кипящим слоем катализатора. Микросферический катализатор витает в потоке паров сырья. По мере закоксовывания частицы катализатора тяжелеют и падают вниз. Далее катализатор выводится на регенерацию, которая проходит также в кипящем слое, а продукты идут на разделение. Типовые установки - 1А/1М, 43-103. Реакторы с лифт-реактором. Нагретое сырье в специальном узле ввода диспергируется и смешивается с восходящим потоком катализатора в специальном узле. Далее смесь катализатора и продуктов крекинга разделяется кипящем слое в сепараторе специальной конструкции. Остатки продуктов десорбируются паром в десорбере. Время контакта сырья и катализатора составляет несколько секунд. Типовая установка - 43-107. Миллисеконд. Характерная особенность процесса - отсутствие лифт-реактора. Катализатор поступает в реактор нисходящим потоком, в катализатор перпендикулярно направлению его движения впрыскиваются пары сырья. Общее время реакции составляет несколько миллисекунд, что позволяет (повысив соотношение катализатор:сырье) добиться повышения выхода бензиновой фракции вплоть до 60-65% На данный момент наиболее совершенными являются лифт-реакторы. Так, выход бензина на них составляет 50-55% с октановым числом 91/92 , тогда как у реакторов с кипящим слоем выход бензина 37% с октановым числом 90/91. Реакторы колонного типа. Бывают реакторы-колонны насадочного и тарельчатого типа. В настоящее время колонны с насадкой являются наиболее распространенными аппаратами. Колонна с насадкой состоит из следующих основных частей: собственно колонны, тарелки, и оросителя. Собственно колонна представляет собой полый цилиндр из материала, соответствующего условиям труда. Обычно колонны изготавливают из стали и дополнительно покрывают материалом, стойким и коррозионному воздействию рабочей среды. Применяют также колонны из специальных марок стали (в производстве азотной кислоты), чугуна, керамики (в производстве серной кислоты), графита и т.д. Насадка применяется для создания большой поверхности контакта между жидкой и газовой фазами. Нормальная работа колонны в значительной степени зависит от правильного выбора материала и геометрической формы загружаемой в колонну насадки. Необходимо чтобы насадка обладала большой удельной поверхностью, большим свободным объемом и была бы достаточно легкой, механически прочной и дешевой. Кроме этого насадка должна оказывать малое гидравлическое сопротивление потоку газа и хорошо смачиваться абсорбентом (жидкостью). Реакторы непрерывного действия. Критериями, по которым классифицируют реакционную аппаратуру, являются периодичность или непрерывность процесса, его гидродинамический и тепловой режимы, физические свойства взаимодействующих веществ. По принципу организации процесса химическая реакционная аппаратура может быть разделена на три группы: - реактор непрерывного действия; - реактор периодического действия; - реактор полунепрерывного (полупериодического) действия. По гидродинамическому режиму различают следующие типы: - реактор вытеснения непрерывного действия (РВНД); - реактор смешения непрерывного действия (РСНД); - реактор промежуточного типа (с промежуточным гидродинамическим режимом). По тепловому режиму работы реакторы делят на следующие типы: - изотермический реактор; - адиабатический реактор; - политропический реактор. |