Технологическая схема производства шликерного литья Национальный Исследовательский Технологический Университет «МИСиС» Институт: ЭкоТех Кафедра: порошковой металлургии и функциональных покрытий Курсовой проект Тема: «Проект участка по производству изделий-тигли Из смеси ЦМ 322 » Выполнила: ст. гр. РПМ-09 Пилипенко Д.А. Руководитель: Костиков В.И Москва 2013 Содержание 1. История завода 2. Описание изделия 2.1 Состав смеси и характеристики ее компонентов 2.1.1 Состав смеси 2.1.2 Характеристики компонентов 2.2 Применение смеси 3. Технологическая схема производства шликерного литья 4. Основные производственные цеха и участки 5. Материальный баланс 6. Опасные и вредные факторы на каждой операции и меры техники безопасности 7. Описание полуавтомата для литья керамических изделий 7.1 современные машины для литья История завода «Завод технической керамики» с 1992 года успешно работает в России на рынке производства изделий из тонкой технической керамики, твердых сплавов и их полуфабрикатов. Предприятие создано на базе ФГУП «Всероссийский научно-исследовательский и проектный институт тугоплавких металлов и твердых сплавов». «ЗТК» занимается производством керамических режущих сменных многогранных пластин (СМП) и износостойких изделий для различных отраслей промышленности и техники, а также разработкой новых композиционных материалов для режущих инструментов. Производство изделий из тонкой технической керамики имеет полный технологический цикл: от размола и обжига керамического сырья до производства готовых шлифованных изделий, включая высокотемпературное газостатическое доуплотнение изделий. Завод оснащен передовым высокопроизводительным технологическим оборудованием. Коллектив «ЗТК» составляют ученые и инженеры, прошедшие школу основоположников науки о твердых сплавах, а также опытные квалифицированные специалисты. Заказчиками «ЗТК» являются предприятия в различных отраслях промышленности, использующие конструкционную керамику, наплавочные порошковые материалы и режущий инструмент для металлообработки. 2. Описание изделия На заводе технической керамики изготовляются изделия-тигли из смеси ЦМ 332 рис.1. Масса изделия составляет 28 г. Годовой выпуск продукции 3600штук в год.  Рис.1 Изделие- тигель из смеси ЦМ 3322. . 2.1 Состав и характеристики компонентов смеси 2.1.1 Состав смеси - Оксид алюминия ГН по ГОСТ 30559-98
- Оксид магния по ГОСТ 4526-75 (в количестве 0,6% масс.)
2.1.2 Характеристики компонентов смеси 1. Оксид алюминия ГН по ГОСТ 30559-98 (ГОСТ 30559-98 Глинозем неметаллургический. Технические условия: Настоящий стандарт распространяется на глинозем, представляющий собой кристаллический порошок оксида алюминия различных модификаций: с высоким содержанием альфа-оксида алюминия - для производства электроизоляционных, электро- и радиокерамических изделий, специальных видов керамики, электрофарфора, огнеупоров, шлифовальных и абразивных материалов; с низким содержанием альфа-оксида алюминия - для производства высокоглиноземистых цементов в качестве катализаторов и др.) Так же существуют другие ГОСТы. рис.2  Рис. 2 ГОСТы по глинозему Настоящий стандарт распространяется на глинозем, представляющий собой кристаллический порошок оксида алюминия различных модификаций: с высоким содержанием альфа-оксида алюминия — для производства электроизоляционных. электро- и радиокерамических изделий, специальных видов керамики, электрофарфора, огнеупоров, шлифовальных и абразивных материалов; с низким содержанием альфа-оксида алюминия — для производства высокоглиноземистых цементов в качестве катализаторов и др. В зависимости от физико-химического состава выпускают марки глинозема, указанные в таблице I. 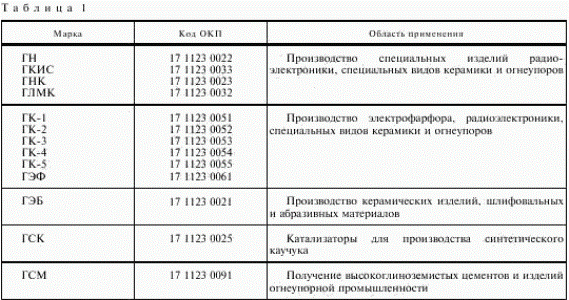 Неметаллургический глинозем выпускают в соответствии с требованиями настоящего стандарта. По физико-химическим показателям глинозем должен соответствовать требованиям, установленным в таблице 2.  Массовая доля влаги в глиноземе всех марок не должна быть более 1.0 %. При определении массы партии глинозема влажность не учитывают. В глиноземе марки ГН содержание монозерен размером более 11 мкм не должно быть более 8 %. В глиноземе всех марок не допускаются видимые невооруженным глазом посторонние включения, технологически не связанные с производством. По степени воздействия на организм человека глинозем относят 4-му классу опасности (вещества малоопасные) по ГОСТ 12.1.005 и ГОСТ 12.1.007. Глиноземная пыль оносится к аэрозолям, преимущественно фиброгенного действия, предельно допустимая концентрация глиноземной пыли в воздухе рабочей зоны составляет 6 мг/м3 по ГОСТ 12.1.005. Воздушную среду рабочей зоны контролируют в соответствии с требованиями ГОСТ 12.1.005, ГОСТ 12.1.007. Анализ проб воздуха на содержание глиноземной пыли проводят по методикам, утвержденным Министерством здравоохранения. Глинозем пожаро- и взрывобезопасен. На предприятиях—производотелях и потребителях глинозема должна быть разработана нормативная документация по безопасности труда на производстве, применении и хранении глинозема в соответствии с ГОСТ 12.1.007. Для индивидуальной зашиты органов дыхания от глиноземной пыли применяют респиратор ШБ-1 «Лепесток» по ГОСТ 12.4.028. 2. Оксид магния по ГОСТ 4526-75 (в количестве 0,6% масс.) Настоящий стандарт распространяется на оксид магния, представляющий собой белый порошок, почти нерастворимый в воде, хорошо растворимый в кислотах: на воздухе постепенно поглотает углекислый газ и влагу. Показатели технического уровня, установленные настоящим стандартом, предусмотрены для высшей категории качества. Формула МgO. Молекулярная масса (по международным атомным массам 1971 г.) — 40,31. Оксид магния должен быть изготовлен в соответствии с требованиями настоящего стандарта по технологическому регламенту, утвержденному в установленном порядке. По химическим показателям оксид магния должен соответствовать нормам, указанным в табл. I.   Оксид магния может вызывать раздражение слизистых глаз и носа. При работе с препаратом следует применять индивидуальные средства зашиты (респираторы типа «Лепесток», резиновые перчатки, зашитые очки), а также соблюдать правила личной гигиены. Помещения, в которых проводятся работы с оксидом магния, должны быть оборудованы обшей приточно-вытяжной вентиляцией. Глинозём марки ГН, химическая формула Al2O3. Содержание примесей в глиноземе должно быть минимальным. Насыпная плотность 0.9-1 г/см3. Оксид магния препятствует росту кристаллов и является хорошим связующим средством. 2.2 Применение смеси Смесь ЦМ-332 обладает высокой твердостью, её красностойкость достигает 1200°С. Она отличается низкой прочностью при изгибе (350-400 МН/м2) и большой хрупкостью. Существенным недостатком смеси является её крайне низкое сопротивление циклическому изменению температуры. Применяется для обтачивания чугуна, сталей, неметаллических материалов и некоторых сплавов на основе цветных металлов. Технологическая схема производства шликерного литья Подготовка дисперсной фазы Размол Подготовка термопластичной связки Сушка Приготовление шликера Загрузка Расплавка Вакуумирование Подготовка формы к заполнению шликером Заливка под давлением Низкотемпературный отжиг, удаление связки Высокотемпературный отжиг Операция | Т, ᵒС | Время, t | Давление, Р | Оборудование | Подготовка дисперсной фазы | Размол | | от нескольких часов до нескольких суток | - | ШВМ, планетарные центробежные мельницы, вихревые мельницы | Сушка | 100-150 оС | 2-3 ч. | - | Сушильные шкафы | Подготовка термопластичной связки (Парафин,воск,олеиновая кислота)-смешение | | | | | Подготовка шликера | Загрузка | - | - | - | Установка для вакуумирования шликера (емкость, оборудованная пропеллерной мешалкой, подключенная к ресиверу и вакуумному насосу) | Расплавка | 60-80 оС | | - | Вакуумирование | 5-6 мин | 0,8 атм | Подготовка формы к заполнению шликером | - | - | - | Форма собирается вручную. | Заливка под давлением | 70-100 оС | до 60 мин | 0,3 – 0,6 МПа | Подается в форму от установки для вакуумирования шликера | Низкотемпературный отжиг | 650-700 С | 3 - 4 ч | - | Печи различных типов | Удаление связки | 1200 – 1300 оС | Будет зависеть от используемой связки-основы | - | Печи предварительного спекания | Высокотемпературный отжиг | 1690 – 1700 оС | 2-4 ч | - | Печь с выкатным подом и высокотемпературные печи | Шликерное формование позволяет получать изделия сложных форм, мало- и крупногабаритные, полые с равномерной толщиной стенок, с высокой чистотой поверхности и точных размеров. К основным свойствам шликеров относят текучесть, характеризующую его способность течь, заполнять форму и увеличивать массу заготовки, и устойчивость, то есть способность не расслаиваться в течение длительного времени. Различают седиментационную и агрегативную устойчивость. Седиментационная устойчивость определяется скоростью оседания твердых частиц в жидкости. Она зависит от плотности материала порошка, формы и размера частиц (размера в большей степени), а также от концентрации твердой фазы в шликере. Чем тяжелее частицы, чем ближе их форма к сферической, тем быстрее произойдет расслоение. Агрегативная устойчивость связана со слипанием отдельных частиц в более крупные агломераты под действием электростатических сил Величина этих сил зависит от природы твердой и жидкой фаз, дисперсности порошка, формы частиц, величины удельной поверхности, поверхностных энергий обеих фаз, характера процессов на межфазных границах. Обычно концентрация твердой фазы в шликерах от 40 до 70%, в данном случае около 80%. Дисперсность порошка, используемого при приготовлении шликеров составляет от 1 – 3 мкм (W, Mo) до 5 – 10 мкм (Fe, Ni, Cu). Предельным значением видимо является 40 мкм (Al и другие легкие металлы). Жидкая фаза шликера должна иметь низкую упругость пара, быть нетоксичной, пожаровзрывобезопасной (желательно), не должна активно взаимодействовать с твердой фазой, одновременно хорошо смачивая ее. Смачиванием можно управлять, добавляя в жидкость поверхностно-активные вещества (ПАВ). Наиболее часто в качестве основы жидкой фазы используют воду, которая обеспечивает шликеру достаточную жидкотекучесть, хорошее заполнение формы и даже возможность прокачки по трубопроводам. Для нашего случая используется олеиновая кислота. Подготовка дисперсной фазы включает в себя получение или выделение порошка заданной дисперсности и формы, что призвано обеспечить максимальную плотность укладки без ухудшения технологических свойств шликера. Крупные порошки дают неустойчивые суспензии и заготовки с пониженной прочностью. Высокодисперсные порошки (обеспечивая шликеру хорошую седиментационную устойчивость, а заготовкам достаточную прочность) имеют низкую скорость набора массы; полученные формовки могут коробиться при спекании из-за анизотропии усадки. Измельчение порошка для шликера целесообразно проводить в жидкости во избежание адсорбции на его поверхности газов, ухудшающих смачивание. Затем идет просушка. При приготовлении термопластичных шликеров (ТПШ) в качестве связки чаще (и в нашем случае тоже) всего используют парафины (предельные углеводороды) с общей формулой CnH2n+2: от нонадекана C19H40 до пентатриоктана C35H72. Температура плавления этих соединений меняется в диапазоне от 49 до 54 оС. Парафины легко растворяются в органических растворителях. Кроме них можно использовать церезины и полиэтилен. Последний хорошо смешивается с парафинами, и его применяют в качестве добавки, увеличивающей устойчивость шликеров. Есть упоминания об использовании при приготовлении ТПШ воска, твердых жиров, пеков, фенолформальдегидных смол. Любая связка в расплавленном состоянии должна смачивать твердую дисперсную фазу и не должна образовывать вокруг ее частиц толстые структурированные оболочки с аномально высокой вязкостью. Термопластичные шликеры готовят, перемешивая порошок с расплавленной связкой, причем частицы твердой фазы часто предварительно подогревают до 60 – 80 оС. Содержание связки (пластификатора) в ТПШ 8 – 15% (14,35%). Обычно формы для этой разновидности шликерного формования изготавливают из стали; при производстве небольших партий изделий их делают из меди, алюминиевых сплавов, пластика и даже гипса. В нашем случае использовалась стальная форма. Термопластичные шликеры на парафиновой основе формуют, предварительно разогревая их до 70 – 100 оС и заливая в равномерно подогретые резервуары, откуда шликеры будут перекачиваться в формы под избыточным давлением 0,3 – 0,6 МПа. Помимо перекачки это давление обеспечит хорошее заполнение всего объема формующей полости, особенно тонких каналов и сечений. Важно, чтобы избыточное давление поддерживалось в системе до момента полного затвердевания шликера, чтобы естественно возникающая усадка не изменила геометрию заготовки. Очень важной операцией при формовании ТПШ является отгонка пластификатора, которая в большинстве случае сочетается с начальным (неизотермическим) периодом спекания. Она осуществляется при медленном нагреве, с промежуточными изотермическими выдержками. В качестве поглотителя расплавленного пластификатора используют ламповую сажу, активированный уголь, оксид алюминия, прокаленный при 1200 – 1300 оС. В нашем случае изделие спекалось при 1150 оС при первом низкотемпературном отжиге для удаление связки. Процесс удаления связки включает в себя ее плавление, улетучивание легких фракций углеводородов, пиролиз (термическое разложение) тяжелых фракций, выгорание углеродного остатка. Общая продолжительность этого процесса, длительность отдельных его этапов, скорости подъема температуры, температуры и время изотермических выдержек будут зависеть от используемой связки-основы ТПШ. Второй раз мы спекаем в печи высокотемпературного отжига при 1690 – 1700 оС. Коэффициент усадки изделия в конечном итоге составляет 1,2-1,19. Конечная плотность изделия 3,85 – 3,90 г/см3. 4.Основные производственные цеха и участки 1.Участок размола порошка Рис. 1, 2 | Содержит шаровые вращающиеся мельницы, гуммированные резиной, в которых осуществляется мокрый размол порошка. Производительность- 50 т в месяц. | 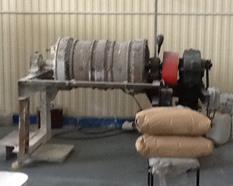 Рис. 1 Рис. 2 2.Участок приготовления смеси Рис. 3,4 | В результате размола получают пульпу, которая поступает на сушку. Полученную смесь просеивают на вибросите. В зависимости от дальнейшего цикла производства в порошок может быть добавлена связка (каучука в бензине, поливиниловые спирты, растворы ПВС в воде). После смешивания идет протирка и грануляция смеси, в результате которой уходит весь бензин и смесь становится очень пластичной. Количество связки зависит от способа формования порошка. Так, например, для прессования на гидравлическом прессе вводят 4-5 об. % связки, тогда как для шликерного формования необходимо 30-40 об. % . Приготовление шликера также происходит в этом цехе. | | |  | | |  | Рис. 3 Рис. 4 3.Цех формования Рис. 5 Гидравлический пресс Рис. 6 Механический пресс Рис.7 Машина для литья ТПШ Рис.8 Пресс горячего прессования | Основным производственным помещением является цех формования, в котором установлены гидравлические пресса, гидравлический длинноходовой пресс мундштучного формования усилием 100т, механические пресса с автоматической подачей навески, на которых получают 1000-3000 изделий за смену, машина для литья термопластичного шликера и пресс горячего формования. |  Рис. 5 Рис. 6 Рис. 7 Рис. 8 4.Участок удаления связки и спекания Рис. 9,11 Рис.10 Печь с выкатным подом | После формования заготовки, необходимо удалить связку. Процесс проводят в печах предварительного спекания объемом 200 л. Температура удаления связки 1150°С. Если заготовки имеют небольшие размеры, то удаление связки происходит в капсуле. Засыпкой служит, в основном, глинозём. акже на этом участке установлена печь с выкатным подом и высокотемпературные печи, максимальная температура нагрева в которых 1700°С. |  Рис. 9 Рис. 10 Рис. 11 5. Цех механической обработки Рис. 12 | В этом цехе установлены шлифовальные машины для механической обработки изделий, фрезерные станки и др. |  Рис. 12 |