ПОЗНАВАТЕЛЬНОЕ Сила воли ведет к действию, а позитивные действия формируют позитивное отношение Как определить диапазон голоса - ваш вокал
Игровые автоматы с быстрым выводом Как цель узнает о ваших желаниях прежде, чем вы начнете действовать. Как компании прогнозируют привычки и манипулируют ими Целительная привычка Как самому избавиться от обидчивости Противоречивые взгляды на качества, присущие мужчинам Тренинг уверенности в себе Вкуснейший "Салат из свеклы с чесноком" Натюрморт и его изобразительные возможности Применение, как принимать мумие? Мумие для волос, лица, при переломах, при кровотечении и т.д. Как научиться брать на себя ответственность Зачем нужны границы в отношениях с детьми? Световозвращающие элементы на детской одежде Как победить свой возраст? Восемь уникальных способов, которые помогут достичь долголетия Как слышать голос Бога Классификация ожирения по ИМТ (ВОЗ) Глава 3. Завет мужчины с женщиной 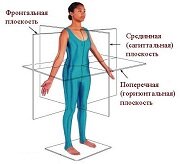
Оси и плоскости тела человека - Тело человека состоит из определенных топографических частей и участков, в которых расположены органы, мышцы, сосуды, нервы и т.д. Отёска стен и прирубка косяков - Когда на доме не достаёт окон и дверей, красивое высокое крыльцо ещё только в воображении, приходится подниматься с улицы в дом по трапу. Дифференциальные уравнения второго порядка (модель рынка с прогнозируемыми ценами) - В простых моделях рынка спрос и предложение обычно полагают зависящими только от текущей цены на товар. | Расчет прямых валов на прочность и жесткость Назначение, классификация конструкций и материалы Осислужат для поддержания вращающихся вместе с ними или на них различных деталей машин и механизмов. Вращение оси вместе с установленными на ней деталями осуществляется относительно ее опор, называемых подшипниками. Примером не вращающейся оси может служить ось блока грузоподъемной машины (рис. 16.1, а), а вращающейся оси — вагонная ось (рис. 16.1,6). Оси воспринимают нагрузку от расположенных на них деталей и работают на изгиб. Валы – стержни на подшипниковых опорах, приспособленные для поддержания установленных на них деталей и передачи между ними вращающего момента (в осевом направлении). Валы, несущие на себе детали, через которые передается крутящий момент, воспринимают от этих деталей нагрузки и, следовательно, работают одновременно на изгиб и кручение. При действии на установленные на валах детали (конические зубчатые колеса, червячные колеса и т. д.) осевых нагрузок валы дополнительно работают на растяжение или сжатие. Некоторые валы не поддерживают вращающиеся детали (карданные валы автомобилей, соединительные валки прокатных станов и т. п.), поэтому эти валы работают только на кручение. Общие сведения По назначению различают валы передач, на которых устанавливают зубчатые колеса, звездочки, муфты и прочие детали передач, и коренные валы, на которых устанавливают не только детали передач, но и другие детали, например маховики, кривошипы и т. д. По форме оси представляют собой прямые стержни (рис. 1, а,б,в), а валы различают прямые (рис. 1, г.д.е.), коленчатые (рис.1, ж.)и гибкие (рис.1 з.). Валы бывают входными (рис.5, б) , промежуточными и выходными (Рис.5, а.), тихо- и быстроходными, распределительными и т. п. В зависимости от воспринимаемых сил различают простые валы, торсионные валы и оси. Простые валы (просто валы) применяют в передачах (зубчатых, ременных и т. д.). Они передают вращающий момент и воспринимают осевые и радиальные (поперечные) силы, вызывающие изгиб. В конструкциях широко распространены прямые валы в форме тел вращения (рис. 5, а, б), устанавливаемые в подшипниковых опорах. В зависимости от распределения нагрузок вдоль оси вала и главным образом условий сборки — прямые валы выполняют гладкими (рис. 5, в) или ступенчатыми (Рис 5, а.), близкими по форме к балкам равного сопротивления изгибу. Гладкие валы более технологичны и получают большое распространение в последние годы. Быстроходные валы изготовляют сравнительно часто как одно целое шестернями зубчатых передач ( валы–шестерни; рис. 1,д, рис 5, б). В некоторых конструкциях применяют полые валы (рис. 1, в). Канал уменьшает массу вала и используется часто для размещения соосного вала, деталей управления, подачи масла, охлаждающего воздуха и т. д. Торсионные валы (торсионы) используют для соединения узлов и агрегатов между собой, такие валы передают только вращающие моменты.  Рис.1. Типы осей и валов В ряде машин (сельскохозяйственных, дорожных и т. д.) применяют длинные составные валы (до 20 м), используемые для передачи вращающего момента к исполнительным органам. Их называют трансмиссионными. В поршневых двигателях и компрессорах используют коленчатые валы, имеющие «ломаную» ось. Коленчатые валы в кривошипно-шатунных передачах служат для преобразования возвратно-поступательного движения во вращательное или наоборот и применяются в поршневых машинах (двигатели, насосы). Для передачи вращающего момента(вращения) между агрегатами со смещенными в пространстве осями входного и выходного валов применяют гибкие валы (рис. 1., з), имеющие криволинейную геометрическую ось при работе. Такие валы обладают высокой жесткостью при кручении и малой жесткостью при изгибе. Гибкие валы, представляющие собой многозаходные витые из проволок пружины кручения, применяют для передачи момента между узлами машин, меняющими свое относительное положение в работе (механизированный инструмент, приборы дистанционного управления и контроля, зубоврачебные бормашины и т. п.). Коленчатые и гибкие валы относятся к специальным деталям, их изучают в соответствующих специальных курсах. Материалы валов и осей Оси и валы изготовляют из углеродистых и легированных конструкционных сталей, так как они обладают высокой прочностью, способностью к поверхностному и объемному упрочнению, легкостью получения прокаткой цилиндрических заготовок и хорошей обрабатываемостью на станках. Для осей и валов без термообработки используют углеродистые стали СгЗ, Ст4, Ст5, 25, 30, 35, 40 и 45. Оси и валы, к которым предъявляют повышенные требования к несущей способности и долговечности шлицев и цапф, выполняют из среднеуглеродистых или легированных сталей с улучшением 35, 40, 40Х, 40НХ и др. Для повышения износостойкости цапф валов, вращающихся в подшипниках скольжения, валы делают из сталей 20, 20Х, 12ХНЗА и других с последующей цементацией и закалкой цапф. Ответственные тяжелонагруженные валы изготовляют из легированных сталей 40ХН, 40ХНМА, ЗОХГТ и др. Тяжелонагруженные валы сложной формы, например, коленчатые валы двигателей, делают также из модифицированного или высокопрочного чугуна. Расчет прямых валов на прочность и жесткость Валы относятся к числу наиболее ответственных деталей машин. Существенное нарушение формы вала из-за высокой радиальной податливости или колебаний, а тем более разрушение вала влечет за собой выход из строя всей конструкции. Поэтому к валам предъявляют высокие требования, как по точности изготовления, так и по прочности, жесткости, устойчивости и колебаниям. Для обеспечения работоспособности валы и оси должны удовлетворять условиям прочности и жесткости. Для расчета на прочность необходимо знать напряжения в сечениях вала от внешних нагрузок (постоянных и переменных), которые передаются от сопряженных деталей (зубчатых колес, шкивов). Эти нагрузки могут быть определены расчетным путем (в редукторах, конвейерах, грузоподъемных устройствах и т.п.) или экспериментально. Если внешние нагрузки известны, то при расчетном определении внутренних силовых факторов в сечениях вал рассматривают обычно как балку, шарнирно закрепленную в двух жестких опорах. Такая модель формы вала и закрепления близка к реальной для валов, вращающихся в опорах качения. Если в одной опоре размещают два подшипника качения, то условную опору размещают по центру внутреннего подшипника пары. Для валов, опирающихся по концам на подшипники скольжения, условную опору располагают на расстоянии (0,25—0,3) В от внутреннего торца подшипника, что обусловлено смещением в эту сторону максимальных контактных напряжений вследствие деформаций вала и подшипника. Нагрузки от зубчатых колес, шкивов, звездочек и других подобных деталей передаются на валы через поверхности контакта. В расчетах валов эти нагрузки для упрощения заменяют сосредоточенными эквивалентными силами, приложенными в середине или по краям ступицы (рис. 2, сечение 3). Критерии работоспособности и расчета Основные критерии работоспособности осей и валов — прочность и жесткость. Прочность осей и валов определяют размером и характером напряжений, возникающих под влиянием сил, действующих со стороны установленных на них деталей машин. Переменные по размеру или направлению силы, действующие на оси и валы, вызывают переменные напряжения. Постоянные по размеру и направлению силы вызывают в неподвижных осях постоянные напряжения, а во вращающихся осях и валах — переменные напряжения. Вращающиеся вместе с осями и валами нагрузки (например, центробежные силы) вызывают постоянные напряжения. Неподвижные оси, в которых возникают постоянные напряжения, рассчитывают на статическую прочность. Из-за опасности усталостного разрушения оси и валы быстроходных машин рассчитывают на сопротивление усталости. Тихоходные оси и валы, работающие с перегрузками, рассчитывают не только на сопротивление усталости, но и на статическую прочность. При проектировании осей и валов для предварительного определения размеров и принятия соответствующей конструкции их рассчитывают на статическую прочность, а затем окончательно на сопротивление усталости. В отдельных случаях оси и валы рассчитывают не только на прочность, но и на жесткость. Пример расчета ведомого вала цилиндрической косозубой передачи на статическую прочность. Исходные данные: из расчета зубчатых передач: T2 = 22× 10 3 Н× мм ; Ft = 541 H; Fr = 1292H; Fx = 3550 H; dw2 = 80мм ; из компоновки редуктора, расстояние между опорами L = 320мм Расположение передачи относительно опор – симметричное На компоновке редуктора расставляют все внешние силы и моменты, действующие в зацеплении и нагружающие валы приводя, представляя направления их действия в двух взаимно перпендикулярных плоскостях – ( горизонтальной Х и вертикальной У ). Марка стали | Диаметр заготовки, мм, не более | Твердость НВ, не ниже | Механические характеристики сталей, МПа | s В | s Т | t Т | s - 1 | t - 1 | Сталь | Любой | | | | | | | Сталь 40Х | Любой | | | | | | | Сталь 40ХН | Любой | | | | | | | Сталь 20Х | | | | | | | | Сталь 12ХН3А | | | | | | | | В этих же плоскостях строят эпюры изгибающих М х и М у и крутящего М к моментов. Назначаем материал для изготовления валов: Сталь 45 НВ ³ 200; sв = 560 МПа; sт = 280 МПа; s-1 = 250 МПа; t-1 = 150 МПа.  Рис.2 Схема распределения напряжений по сечениям выходного вала. 1. Определение опорных реакций 1.1 От действия окружной силы Ft = 541 Н SМП =0; R Л t× (l1 + l2) - Ft× l2 = 0 R Л t = = = 270,5H; R П t = Ft – R Л t = 541 – 270,5 = 270,5H; 1.2 От действия радиальной силы Fr = 1292 Н SМП = 0; R ЛR × (l1 + l2) – Fr × l2 = 0 RЛR = = = 646H; RПR = FR – RЛR = 1292 - 646 = 646H; 1.3 От действия осевой силы Fx = 3550 Н R Лx = RПx = 443,75H; 2. Расчет изгибающих моментов 2.1 В сечении 2 (слева от сечения); Mиt = RЛt × l1 = 270,5× 160 = 43,28 Н× м MиR = - RЛR × l1 = - 646 × 160 = - 103,36 Н× м Mиx = - R Лx × l1 = - 443,75× 160 = - 71 Н× м 2.1 В сечении 2 (справа от сечения); Mиt = RП t × l2 = 270,5× 160 = 43,28 Н× м MиR = - RПR × l2 = - 646 × 160 = - 103,36 Н× м Mиx = R Пx × l2 = 443,75× 160 = 71 Н× м 7.3. Суммарный изгибающий момент в наиболее нагруженном сечении - 2, слева MиS = = = 180 Н× м 7.4. Приведенный момент Mпр = = = 181Н× м 7.5. Диаметры вала в опасных сечениях d1 = d2 = = = 13,4 мм; d3 = = = 27,1 мм . Диаметры валов, ослабленных шпоночными пазами увеличиваем на 10% . При наличии на валу муфты, принимаем диаметр вала по отверстию муфты ( ближайший больший ). Принимаем d1 = 22мм , d3 = 30мм где - [s]и = 90 МПа -– допускаемое напряжение изгиба; = 2 – ориентировочное значение коэффициента концентрации S = 2…2,5 – ориентировочное значение коэффициента запаса прочности. Принимаем S = 1,7 . После расчета на прочность проводят конструирование вала на компоновке редуктора, учитывая особенности конструкции сопрягаемых с ним деталей. Особенности конструкций валов и осей Оси и валы в большинстве случаев бывают круглого сплошного сечения. Иногда, в случаях, когда требуется уменьшить массу конструкции, например в самолетах а также осей сателлитов планетарного редуктора , или разместить внутри другую деталь, применяют валы кольцевого поперечного сечения. Оси небольшой длины изготовляют одинакового диаметра по всей длине (рис. 1,а), а длинные и сильно нагруженные — фасонными (рис.1,6). Прямые валы в зависимости от назначения также делают либо постоянного диаметра по всей длине, либо ступенчатыми, т.е. различного диаметра на отдельных участках. Наиболее распространены ступенчатые валы, так как их форма удобна для установки на них деталей, каждая из которых должна к своему месту проходить свободно (валы редукторов см. на рис. 5. а, б) Иногда валы изготовляют заодно с шестернями (см. рис. 5,б) или червяками . Участки осей и валов, которыми они опираются на подшипники, называют при восприятии радиальных нагрузок цапфами, при восприятии осевых нагрузок — пятами. Концевые цапфы, работающие в подшипниках скольжения, называют шипами (рис. 3), а цапфы, расположенные на некотором расстоянии от концов осей и валов,— шейками . Цапфы осей и валов, работающие в подшипниках скольжения, бывают цилиндрическими, коническими и сферическими. Самые распространенные - цилиндрические цапфы, так как они наиболее просты, удобны и дешевы в изготовлении, установке и работе. Цилиндрические цапфы, работающие в подшипниках скольжения, обычно делают несколько меньшего диаметра по сравнению с соседним участком оси или вала, чтобы благодаря заплечикам и буртикам оси и валы можно было фиксировать от осевых смещений. На некоторых осях и валах для фиксирования подшипников качения рядом с цапфами предусматривают резьбу для гаек (рис. 5, б) или кольцевые выточки для фиксирующих пружинных колец . Посадочные поверхности осей и валов, на которых устанавливают вращающиеся детали машин и механизмов выполняют цилиндрическими и гораздо реже коническими (Рис.5, б). Последние применяют, например, для облегчения постановки на вал и снятия с него тяжелых деталей при повышенной точности центрирования деталей. 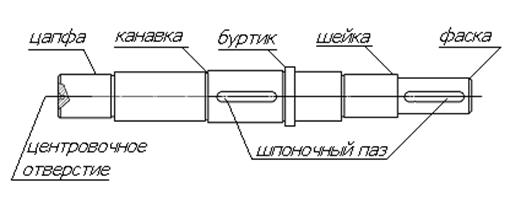 Рис. 3. Элементы вала Поверхность плавного перехода от одной ступени оси или вала к другой называется галтелью (Рис.7). Переход от ступеней меньшего диаметра к ступени большего диаметра выполняют со скругленной канавкой для выхода шлифовального круга (см. рис. 7). Для снижения концентрации напряжений радиусы закруглений галтелей и канавок принимают возможно большими, а глубину канавок — меньшей (ГОСТ 10948-64 и 8820-69). Разность между диаметрами соседних ступеней осей и валов для снижения концентрации напряжений должна быть минимальной. Торцы осей и валов для облегчения установки на них вращающихся деталейи предупреждения травмирования рук делают с фасками, т. е. слегка обтачивают на конус (см. рис. 3). Радиусы закруглений галтелей и размеры фасок нормализованы ГОСТ 10948 — 64. Длина осей обычно не превышает 2...3 м, валы могут быть длиннее. По условиям изготовления, транспортировки и монтажа длина цельных валов не должна превышать 6...7 м. Более длинные валы делают составными и отдельные части их соединяют муфтами или с помощью фланцев. Диаметры посадочных участков осей и валов, на которых устанавливаются вращающиеся детали машин и механизмов, должны быть согласованы с ГОСТ 6636-69 (СТ СЭВ 514-77). Общая технология конструирования вала: В результате расчета вала на прочность получают его диаметры в характерных сечениях. На компоновке передачи эти диаметры откладывают симметрично оси вращения вала. Соединив полученные точки прямыми линиями, получают теоретический профиль вала или конфигурацию стержня равного сопротивления, используемого для конструирования вала (Рис. 4, б,в). Руководством по конструированию, позволяющим учесть особенности конструкции вала может служить его прототип, содержащийся в готовом изделии (см. Рис.4, г). Рабочая конструкция вала должна соответствовать нескольким основным условиям. 1. Условие сборки. Во избежание повреждения поверхностей, через которые деталь проводится к месту сопряжения с валом, они должны быть меньше посадочной. Для выполнения этих условий вал должен быть ступенчатым. Сборку следует организовать со стороны ближайшей к посадочному месту опоры, что увеличивает жесткость вала и уменьшает длину распорных втулок. 2. Технологическое условие. Вал должен иметь возможно меньшее количество ступеней. Качество обработки поверхностей должно быть минимальным (экономически обоснованным) для достижения принятого вида сопряжения. Для повышения качества механической обработки, базирования деталей, и уменьшения местных напряжений в ступенчатых валах, переходы между ступенями вала и уступами разделяют проточками, канавками, галтелями и фасками. 3. Типизация и секционирование вала на участки сходные по размерам и видам сопряжений с насаживаемыми на вал деталями. В конструкции ступенчатого вала условно выделяют: концевые участки, участки перехода от ступени к ступени, места посадки подшипников, уплотнений и деталей, передающих момент вращения. Каждый участок отличается своими особенностями конструктивного оформления. См. рис.4. Сходные по функциональному назначению секции 1 – 2 и 5 – 7 под детали передающие крутящий момент; 3 – 4 и 7 – 8 под подшипники качения. Секция 2 – 3 под уплотнение и уступ секции 2 – 3 для осевой фиксации деталей, секция 4 – 5 – для осевой фиксации вала. 4. Назначение диаметров посадочных поверхностей с учетом теоретического профиля вала, вида соединения и стандартов на посадочные диаметры деталей. По ГОСТ 6636-69 Ряд размеров используемых для диаметров валов: 16,17,18,19,20,21,22,24,25,26,28,30,32,34,36,38,40,42,45,48,50,53,56,60,63,67,71,75,80,85,90,95,100,105,110,120,125,130,140,150. Под подшипники качения используют размеры:10,12,15,17,20, далее размеры увеличиваются через 5 мм Рис. 4 5. Корректировка формы и размеров поверхности, назначение посадок и шероховатости поверхностей в соответствии с видом соединения и размерами соединяемых с валом деталей, обоснование применения галтелей проточек, уступов и других элементов конструкции вала.  Рис. 5. Примеры конструкции валов Конструкция валов в основном определяется деталями, которые на них размещаются, расположением опор и видом уплотнений подшипниковых узлов. В большинстве своем валы одноступенчатых редукторов выполняются по форме, близкими к балкам равного сопротивления изгибу, т. е. ступенчатыми (рис. 5, а, б). Такие валы удобны при сборке, а уступы используют обычно для упора деталей, насаживаемых на вал, и передачи сил, действующих вдоль него. При конструировании ступенчатого вала следует стремиться к минимальному числу степеней, что сокращает число переходов и номенклатуру инструмента, а следовательно, обеспечивает технологичность конструкции. В настоящее время наметилась тенденция к конструированию гладких валов (рис. 5, в). Здесь при одном и том же номинальном диаметре участки вала отличаются допусками и шероховатостью поверхности. Необходимо иметь в виду, что любая насаживаемая на вал неразъемная деталь должна проходить до своего места посадки без натяга, во избежание ослабления посадок из-за повреждения поверхностей. Концевые участки выполняют цилиндрическими или коническими. Посадка деталей на конус обеспечивает легкость сборки и разборки, высокую точность базирования, возможность создания любого натяга. Поэтому выходные концы валов редукторов серийного производства, как правило, делают конусными. Поскольку цилиндрические концы валов проще в изготовлении, то при единичном и мелкосерийном производстве они имеют преимущественное распространение. Рис. 6. Демонтаж подшипника без выемки шпонки | При конструировании выходного конца валаи диаметра под подшипник следует предусмотреть посадку подшипника без съема призматической шпонки. Решается это путем прочерчивания сечения вала со шпонкой (рис. 6.). 1. Расчет вала на выносливость( Гузенков П.Г. п.16.4) Уточненные расчеты на выносливость отражают влияние разновидности цикла напряжений, статических и усталостных характеристик материалов, размеров, формы и состояния поверхности. Для расчетов на выносливость выбирают предположительно опасные сечения с учетом эпюр нагружения вала, концентраторов напряжений и состояния поверхности вала. В каждом из них определяют расчетный коэффициент запаса прочности и сравнивают его с допускаемым значением [S], принимаемым обычно [S] = 1,3 …2,1. В расчетах валов принимают, что нормальные напряжения изменяются по симметричному циклу s a = s и = и sm = 0, а касательные напряжения по отнулевому циклу tа = tm = 0,5× tкp = 0,5× . wнетто – см. таблицу Рассчитываем на усталость вал в сечении 6( Рис. 4) по d3 = 30мм, с концентратором в виде шпоночного паза с поперечным сечением шпонки b x h = 8 x 7 мм. 2.1. Коэффициент запаса усталостной прочности по нормальным напряжениям ( изгиба ) для опасных сечений. Ss = = = 164,2 где s -1 – предел выносливости материала при изгибе; Ks - эффективный коэффициент концентрации напряжений; Kd = влияние абсолютных размеров поперечного сечения ( масштабный фактор ); KF = коэффициент влияния шероховатости; KV - коэффициент, учитывающий упрочнение материала; sa – амплитуда нормального напряжения; Ys – коэффициент чувствительности материала к асимметрии цикла напряжений; sm – среднее напряжение цикла. 2.2 Коэффициент запаса усталостной прочности по касательным напряжениям; St = 25,3 где t-1 – предел выносливости материала при кручении; kt – эффективный коэффициент концентрации напряжений при кручении; tm – амплитуда касательных напряжений; yt – коэффициент чувствительности к асимметрии цикла напряжений; tm - среднее напряжение цикла. 2. Определение коэффициентов Ks и Kt При действии в одном и том же сечении вала нескольких факторов концентрации напряжений от формы учитывают наиболее опасный из них. Общий эффективный коэффициент концентрации напряжений от формы и состояния поверхности: при изгибе Ks = Ks + KF – 1 ; при кручении Kt = Kt + KF – 1 t t Рис.7 Ступенчатые переходы с галтелью, значения коэффициентов Ks и Kt t / r | r / d | Ks при sв | Kt при sв | | | | | | | | | | 0,01 | 2,55 | 1,6 | 1,65 | 1,7 | 1,4 | 1,4 | 1,45 | 1,45 | 0,02 | 1,8 | 1,9 | 2,0 | 2,15 | 1,55 | 1,6 | 1,65 | 1,7 | 0,03 | 1,8 | 1,95 | 2,05 | 2,25 | 1,55 | 1,6 | 1,65 | 1,7 | 0,05 | 1,75 | 1,9 | 2,0 | 2,2 | 1,6 | 1,6 | 1,65 | 1,75 | | 0,01 | 1,9 | 2,0 | 2,1 | 2,2 | 1,55 | 1,6 | 1,65 | 1,75 | 0,02 | 1,95 | 2,1 | 2,2 | 2,4 | 1,6 | 1,7 | 1,75 | 1,85 | 0,03 | 1,95 | 2,1 | 2,25 | 2,45 | 1,65 | 1,7 | 1,75 | 1,9 | | 0,01 | 2,1 | 2,25 | 2,35 | 2,5 | 2,2 | 2,3 | 2,4 | 2,6 | 0,02 | 2,15 | 2,3 | 2,45 | 2,65 | 2,1 | 2,15 | 2,25 | 2,4 | Значения коэффициента KF в зависимости от состояния поверхности валов sВ , МПа | | | | Шлифование Rz 16…0,4 | | | | Обточка Rz 10…16 | 1,05 | 1,10 | 1,25 | Обдирка Rz 80…10 | 1,20 | 1,25 | 1,5 | Необработанная поверхность с окалиной | 1,35 | 1,5 | 2,2 | Значения коэффициентов Ks и Kt для шпоночных канавок sв | Ks при выполнении паза фрезой | Kt | | | концевой | дисковой | | | 1,6 | 1,4 | 1,4 | | | 1,9 | 1,55 | 1,7 | | | 2,15 | 1,7 | 2,05 | | | 2,5 | 1,9 | 2,4 | | Значения коэффициентов Ks и Kt для шлицевых канавок и резьб sв | Ks для | Kt для шлицев | шлицев | резьбы | прямобочных | эвольвентных | | 1,45 | 1,8 | 2,25 | 1,43 | | 1,6 | 2,2 | 2,45 | 1,49 | | 1,7 | 2,45 | 2,65 | 1,55 | | 1,75 | 2,9 | 2,8 | 1,6 | Значения коэффициента KF Среднее арифметическое отклонение профиля Ra ,мкм | KF при sв | | | | | 0,4 … 0,1 | 1,0 | 1,0 | 1,0 | 1,0 | 3,2 … 0,8 | 1,05 | 1,10 | 1,15 | 1,25 | Значения коэффициента Kd Напряженное состояние и материал | Значение Kd при диаметре вала d, мм | | | | | | Изгиб для углеродистой стали | 0,88 | 0,85 | 0,81 | 0,76 | 0,71 | Изгиб для высокопрочной легированной стали и кручение для всех сталей | 0,77 | 0,73 | 0,70 | 0,67 | 0,62 | | Значения коэффициента KV Вид упрочнения | sв сердцевины | KV | Гладкие валы | Ks >1,5 | Ks =1,8…2,0 | Закалка с нагревом ТВЧ | 600 …800 | 1,5 …1,7 | 1,6 …1,7 | 2,4 …2,8 | 800 …1000 | 1,3 …1,5 | – | – | Дробеструйный наклеп | 600 … 1500 | 1,1 …1,25 | 1,5 …1,6 | 1,7 …2,1 | Накатка роликом | – | 1,1 …1,3 | 1,3 …1,5 | 1,6 …2,0 | Значения ys и yt зависят от механических характеристик материала. Обычно принимают: ys = 0,05 и yt = 0 - углеродистые мягкие стали ys = 0,1 и yt = 0,05 - среднеуглеродистые стали ys = 0,15 и yt = 0,1 - легированные стали. 2.3 Коэффициент запаса усталостной прочности по каждому из опасных сечений; S = = = 3,5. S ³ [S]; 3,5 ³ 3 где - [S]= 2,5…3 – допускаемый коэффициент запаса усталостной прочности. В рассмотренном сечении вал имеет достаточный запас прочности. |