Расчет основных элементов корпуса и крышки Назначение посадок, шероховатостей и допусков формы и располоржения поверхностей Допуски и посадки для деталей редуктора назначаем по ГОСТ 25346-82.  Для валов в местах установки на нах деталей - 6 квалитет точности. От посадок с гарантированным зазором до посадок с натягом. Рекомендуется принимать следующие квалитеты точности для посадок: Свободные поверхности валов, втулок, ступиц и пр. – (8-12) квалитет точности. Обработка корпусных деталей (отверстий) для установки в них сопрягаемых деталей - 7,8 квалитет точности. Свободные поверхности остальных деталей - (8-14) квалитет точности. Для выбора значений полей допусков и предельных значений используем таблицы стандарта. Рекомендуемые посадки при номинальных размерах от 1 до 500 мм в системе отверстия 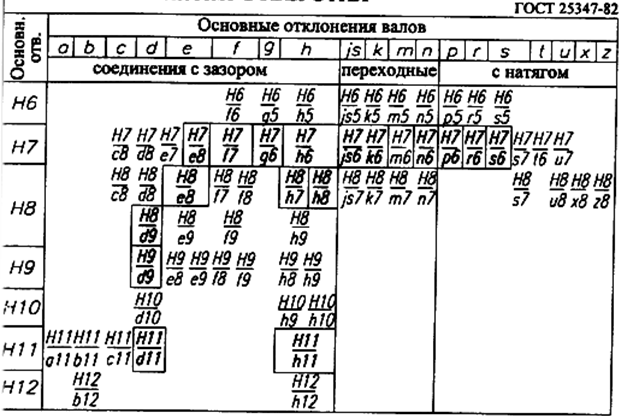 Примечание. Посадки заключенные в рамку являются предпочтительными. Численные значения полей допусков:   Численные значения предельных отклонений валов  Численные значения предельных отклонений отверстий  Посадка ступиц зубчатых колес на валы H7/p6, шейки валов под подшипники выполняем с отклонением m6 или k6 (посадка L0/k6), отверстия в корпусе для колец подшипников – H7 (посадка H7/l0)). Посадки крышек подшипника и шкивов ременных передач – H7/n6. Шейки валов под манжеты выполняются с отклонением вала –d9. В соответствии с ГОСТ 3325-85 назначаем допуски формы посадочных поверхостей подшипников   Назначаем допуски взаимного расположения шеек подшипников и посадочных мест под ступицы зубчатых колес: допуски соосности (для шеек), симметричности (для пазов), параллельности и перпендикулярности различных поверхностей деталей и позиционные допуски (для расположения отверстий) в соответствии с ГОСТ 2308-79. Шероховатости поверхностей назначаем в соответствии с ГОСТ2788-73. Рекомендуемые средние арифметические отклонения Ra профиля в мкм: 12,5 или 20 – неответственные поверхности деталей и заготовок деталей; 6,3 - нерабочие поверхности; 3,2 - торцевые нерабочие поверхности; 1,6 - рабочие поверхности пазов, шлицев и зубьев; 1,25 - торцевые поверхности заплечиков; 0,63 - поверхности валов под подшипники и гладкие посадки ступиц зубчатых колес; 0,32 - поверхности под манжеты и уплотнительные резиновые кольца. Расчет основных элементов корпуса и крышки Как правило корпуса редукторов выполняют из чугуна марки СЧ15 ГОСТ1412-79. Для удобства сборки корпус выполняем разъемным по линии, проходящей через оси валов. Чаще всего, для удобства обработки, плоскость разъема располагают параллельно плоскости прилегания лап редуктора к фундаменту. Отверстия под подшипниковые узлы выполняют совместной обработкой корпуса и крышки, скрепленных и установленных на центрирующих штифтах. Рекомендуемые значения размеров корпуса и крышки: Толщина стенок - δ = ( 0,025·аw+3) мм; Толщина фланцев – b =1,5· δ мм; Толщина фундаментных лап – р = 2,35· δ мм; Диаметр фундаментных болтов – d1=( 0,035… 0,035)·аw+12 , мм; Диаметр болтов в местах установки подшипников – d2 = 0,7· d1, мм; Диаметр болтов скрепляющих корпус и крышку – d3 = (0,5…0,6)· d1, мм; Расстояние между корпусом и подвижными деталями (венцы зубчатых колес) – а = (L)1/3 +3 мм, где L, мм – максимальный габаритный размер; Расстояние между взаимно подвижными, обработанными поверхностями – не менее 5 мм. Ширина фланца – (3…4)·δ, мм Остальные размеры необходимо назначать исходя из опыта конструирования деталей прототипов, конструкции которых приведены в технических справочниках и учебниках. Следует учитывать предполагаемую технологию изготовления деталей ( отливка, поковка, прокат и пр.) Следует учитывать, что часть поверхностей остануться необработанными. Выбор типа смазки Для уменьшения потерь на трение в зацеплениях, предотвращения заедания зубьев, охлаждения зубчатых колес, подшипников и манжет, удаления продуктов износа и предохранения от коррозии, детали редуктора смазывают. Для редукторов общего машиностроения используют жидкие смазки по ГОСТ 20799-75. При окружных скоростях зубчатых колес до 10 м/с допускается окунание трети венца наибольшего зубчатого колеса в масляную ванну. Остальные детали смазываются образованным маслянным туманом и за счет взаимного соприкосновения деталей. Рекомендуемое количество масла (0,6…0,7) литров на 1 кВт. Большие значения для червячных редукторов и редукторов с коническими роликовыми подшипниками. Уровень масла не менее 35 мм от поверхости дна редуктора. Контроль уровня осуществляется при помощи маслоуказателя (контрольное отверстие, окно, щуп). Для замены масла в корпусе выполняют сливное отверстие, расположенное в нижней точке поверхности дна. Заправка редуктора осуществляется либо через специальное отверстие в крышке или при снятой крышке. В редукторе предусматривают элементы сапунирования, для исключения значительного повышения давления внутри корпуса при работе редуктора и нагреве деталей и масла. Допускается смазка подшипников консистентной смазкой (литол, солидол). При этом необходимо установить с внутренней стороны корпуса мазеудерживающие кольца. Такие кольца устанавливают с выступанием за стенку корпуса. Они имеют кольцевую канавку и за счет центробежных сил жидкая смазка удаляется обратно внуть редуктора. За счет этого не допускается вымывание пластичной смазки из подшипникового узла. Для наиболее нагруженных редукторов предпочтительно организовать принудительную систему смазки, путем установки масляного насоса. |