Технічне обслуговування кривошипно-шатунного і газорозподільного механізмів двигунів При діагностуванні двигуна в цілому перевіряють такі прямі (структурні) діагностичні параметри: ефективну потужність двигунів; тиск масла у головній масляній магістралі; питому витрату палива; вміст оксиду вуглецю у відпрацьованих газах; димність відпрацьованих газів дизелів. У циліндро-поршневій групі перевіряють такі зазори: між поршнем і кільцем по висоті канавки; у стиках поршневих кілець; між циліндром (гільзою циліндра) і поршнем у верхньому поясі. У кривошипно-шатунному механізмі перевіряють такі зазори: між шийками колінчастого вала і корінними підшипниками; між шийками колінчастого вала і шатунними підшипниками; між поршневим пальцем і втулкою верхньої головки шатуна; осьовий у корінних підшипниках колінчастого вала. Оцінюючи технічний стан механізму газорозподілу, перевіряють: фази газорозподілу; зазор між розподільним валом і підшипниками; спрацьовування напрямних втулок-клапанів; зазори між клапаном і сідлом клапана, клапаном і приводом клапана, клапаном і коромислом. Найбільше поширені методи діагностування кривошипно-шатунного і газорозподільного механізмів за шумами й вібраціями, параметрами картерного масла, герметичністю надпоршневого простору циліндрів двигуна (за компресією, прориванням газу в картер двигуна, угаром масла, розрідженням на впуску, витіканням стиснутого повітря, опором проти прокручування колінчастого вала, ступенем димлення). Діагностування за шумами і вібраціями.Шуми в працюючому двигуні виникають унаслідок стукоту корінних і шатунних підшипників, поршневих пальців, поршнів, вібрації клапанів, коливання розподільного вала і кулачків від імпульсів крутильних коливань колінчастого вала, коливання газів по впускному і випускному трубопроводах, детонації в карбюраторному двигуні, співударяння різних деталей, тертя в рухомих з'єднаннях. За характером стукоту або шуму і за місцем його виникнення можна визначити деякі несправності двигуна (збільшення зазорів у підшипниках колінчастого вала, між поршнем і циліндром, клапанами і штовхачами, клапанами і втулками, у підшипниках розподільного вала). Наиперспективнішим методом діагностування технічного стану газорозподільного і кривошипно-шатунного механізмів є віброакустичні методи із застосуванням спеціальної вимірювальної апаратури. Для віброакустичного діагностування використовують коливальні процеси пружного середовища, які виникають при роботі механізмів. Джерелом цих коливань є газодинамічні процеси (згоряння, випуск, впуск), регулярні механічні співударяння у спряженнях за рахунок зазорів і неврівноваженості мас, а також хаотичні коливання, які зумовлені процесами тертя. При роботі двигуна всі ці коливання накладаються одне на одне і, взаємодіючи, утворюють випадкову сукупність коливальних процесів, яку називають спектром. Це ускладнює віброакустичне діагностування потребою заглушувати перешкоди, виділяти корисні сигнали й розшифровувати коливальний спектр. Поширення коливань у пружному середовищі (тверді тіла, рідини, гази) має хвильовий характер. Параметрами коливального процесу є частота (періодичність), рівень (амплітуда) і фаза (положення імпульсу коливального процесу щодо опорної точки циклу роботи механізму). Рівень вимірюють зміщенням, швидкістю або прискоренням частинок пружного середовища, тиском, що виникає в ньому, або ж потужністю коливального процесу. Між параметрами коливального процесу є перевідні масштаби. Повітряні коливання прийнято називати шумами (стукотом), які сприймаються за допомогою мікрофона. Коливання матеріалу, з якого складається механізм, називають вібраціями. Параметри вібрації сприймають за допомогою п'єзоелектричних датчиків, потім підсилюють, вимірюють за масштабом і реєструють. Віброакустична діагностика дає змогу розшифрувати коливальні процеси, оскільки кожна співударяюча пара породжує свої власні коливання, які за своїми параметрами різко відрізняються від коливань газодинамічного походження і коливань, спричинених тертям. Потужність коливань різко змінюється при зміні зазорів. Це пояснюється тим, що зміна зазорів приводить до зміни енергії співударянь. При цьому змінюється також тривалість співударянь. Наявність коливань пар, що співударяються, визначають за фазою відносно опорної точки (верхня мертва точка, посадка клапана та ін.). Є кілька методів віброакустичного діагностування. Найпоширеніша реєстрація рівня коливального процесу у вигляді миттєвого імпульсу в функції часу (або частоти обертання колінчастого вала) за допомогою осцилографа. Рівень і характер спаду коливального процесу порівняно з нормативним дають змогу визначити несправність спряження, що діагностується. Більш універсальним методом віброакустичної діагностики є реєстрація й аналіз усього спектра, тобто всієї сукупності коливальних процесів. Коливальний спектр знімають на вузькій характерній ділянці процесу при відповідних швидкісному й навантажувальному режимах роботи механізму, який діагностують. Аналіз спектра полягає в групуванні за частотами його складових коливальних процесів за допомогою фільтрів (подібно до настроювання радіоприймачів на відповідну хвилю). Дефект виявляють за максимальним або середнім рівнем коливального процесу у смузі частот, зумовленій роботою діагностованого спряження порівняно з нормативами (еталонами). Наближено визначити шуми і стукіт у двигуні можна за допомогою стетоскопа (рис. 2). Двигун допускається до експлуатації при помірному стукоті клапанів, штовхачів і розподільного вала на малих обертах холостого ходу. Якщо виявлено стукіт у шатунних і корінних підшипниках колінчастого вала, то двигун до експлуатації не допускається. Стукіт корінних підшипників глухий сильний низького тону. Стукіт шатунних підшипників середнього тону дзвінкіший, ніж стукіт корінних підшипників. При вимиканні запалювання стукіт у циліндрі підшипника, який перевіряють, зникає. Стукіт корінних підшипників прослуховується в площині розняття картера, а шатунних — на стінках блока циліндрів по лінії руху поршня в місцях, що відповідають верхній і нижній мертвим точкам (рис. 3). Стукіт поршневих пальців різкометалевий, він зникає при вимиканні запалювання. Прослуховується у верхній частині блока циліндрів при різко-змінному режимі роботи прогрітого двигуна. Наявність стукоту свідчить про підвищений зазор між пальцем і втулкою головки шатуна або про збільшений отвір для пальця в бобишці поршня. Стукіт поршнів глухий, клацаючий, він зменшується в міру прогрівання двигуна. Стукіт поршнів прослуховується у верхній частині блока циліндрів з^бку, протилежного розподільному валу, при роботі недостатньо прогрітого двигуна (у разі сильного спрацювання можливий стукіт поршня і на прогрітому двигуні). Наявність стукоту свідчить про значне спрацювання поршнів і циліндрів. Рис. 2. Стетоскоп електронний: 1 — привід; 2 — елементи живлення; З — корпус-ручка; 4 — перетворювач; 5 — стержень; 6 — телефон-навушник Рис. 3. Зони прослуховування двигуна з верхніми (а) і нижніми (б) клапанами: 1 — зона клапанів; 2 — поршнів; 3 — штовхачів; 4 — підшипників; 5 — розподільних шестерень Стукіт клапанів дзвінкий, добре прослуховується на прогрітому двигуні при малих обертах двигуна. Він виникає при збільшенні теплових зазорів між стержнями клапанів і носком коромисла (штовхачем). Точність діагнозу за допомогою стетоскопів значною мірою залежить від досвіду механіка або слюсаря-моториста. Діагностування за параметрами картерного масладає змогу визначити темп спрацьовування деталей двигуна, якість роботи повітряних і масляних Технічне обслуговування і поточний ремонт двигунів фільтрів, герметичність системи охолодження, а також придатність самого масла. В основу діагностування покладено те, що концентрація в маслі двигуна продуктів спрацьовування основних деталей зберігається практично сталою при нормальному технічному стані двигуна і різко зростає перед відмовами. Діагноз ставлять, порівнюючи добуті результати аналізу масла (при справно працюючих масляних і повітряних фільтрах і нормальному стані масла) з граничними показниками і попередніми результатами. Перевищення допустимих норм концентрації в маслі металів свідчить про несправну роботу спряжених деталей, перевищення норми вмісту кремнію, несправність системи охолодження, а знижена в'язкість масла дає змогу дійти висновку про його придатність. Для діагностування двигуна за концентрацією продуктів спрацювання в картерному маслі (кожного металу зокрема) застосовують спектральний аналіз, спалюючи рідку пробу масла у високотемпературному полум'ї вольтової дуги. Спектр реєструють за допомогою високочутливого спектрографа автоматизованої фотоелектричної установки. Пара продуктів спрацювання дає лінійчатий спектр, який піддають кількісному аналізу. При якісному аналізі виявляють спектральні лінії, що свідчать про присутність у картерному маслі металів деталей, які спрацьовуються, а при кількісному визначають інтенсивність почорніння спектральних ліній. Почорніння ліній вимірюють мікрофотометром. Потім добуті результати переводять в абсолютні одиниці концентрації, використовуючи тарувальні графіки. Основні деталі, які обмежують ресурс двигуна, виготовлені з феромагнітних металів (гільзи циліндрів, поршневі кільця та ін.). Тому їхні несправності призводять до збільшення в маслі кількості феромагнітних продуктів спрацьовування, за концентрацією яких можна дійти висновку про технічний стан агрегате. Діагностування двигуна за концентрацією феромагнітних частинок у картерному маслі проводять порівняно швидко і просто, але не дуже точно. Його здійснюють за допомогою електричного приладу, який вимірює концентрацію продуктів спрацьовування за зміною індуктивності масла внаслідок присутності в ньому феромагнітних частинок. Діагностування за герметичністю надпоршневого простору циліндрів двигуна.Ці роботи виконують за компресією, витіканням стиснутого повітря, прориванням газів у картер двигуна, угаром масла та іншим. Діагностування за компресією. Тиск газів у циліндрі наприкінці такту стиснення (компресія) залежить від спрацювання циліндропоршневої групи, в'язкості масла, частоти обертання колінчастого вала, герметичності клапанів та ін. Компресію перевіряють компресометром або компресографом (записуючим манометром). Для перевірки компресії двигун прогрівають до температури охолодної рідини (80...90 °С), потім його зупиняють, повністю відкривають дросельну і повітряну заслінки карбюратора і від'єднують проводи від свічок запалювання. Очистивши і продувши стиснутим повітрям заглиблення біля свічок запалювання, викручують свічки і, уставивши гумовий наконечник 2 (рис. 4) компресометра в отвір для свічки (карбюраторні двигуни) або форсунки (дизельні двигуни) одного з циліндрів, прокручують колін частий вал двигуна стартером на 10... 12 обертів. Тиск відлічують по шкалі манометра 4. Далі натискують пальцем на стержень золотника 6 компресо-метра до встановлення стрілки манометра в нульове положення і перевіряють тиск у решти циліндрів. Перевіряють компресію кілька разів. Різниця показань манометра в окремих циліндрах не повинна перевищувати ОД МПа для карбюраторних двигунів і 0,2 МПа — для дизельних. Мінімально допустиму компресію залежно від ступеня стиску визначають заводи—виготовлювачі двигунів і зазначають у відповідних інструкціях про експлуатацію автомобілів. Основні недоліки цього методу діагностування такі: розрядження акумуляторної батареї при прокручуванні колінчастого вала двигуна; не-порівнюваність показників компресометра при вимірюванні тиску в різних двигунах через неможливість мати однакову частоту обертання; неможливість визначення безпосередньої причини низької компресії. | |  | Рис. 4. Схема перевірки компресії:1 — головка циліндрів; 2 — гумовий наконечник; 3 — шланг; 4 — манометр; 5 — клапан випуску повітря; 6 — золотник Діагностування за виходом стиснутого повітря. Причини спаду компресії можна визначити за виходом стиснутого повітря, яке подається в циліндр двигуна через отвір для свічки: якщо стиснуте повітря виходить через карбюратор або глушитель, то клапани нещільно прилягають до сідел; якщо через сапун, то не справна (спрацьована) циліндропоршнева група; якщо стиснуте повітря потрапляє в сусідній циліндр з охолодженою рідиною, то пошкоджена прокладка головки блока. Витікання стиснутого повітря з циліндра точніше можна визначити за допомогою спеціального переносного приладу, який дає змогу визначити технічний стан циліндрів, поршневих кілець, клапанів і прокладок головок блока циліндрів. За допомогою цього приладу по черзі впускають стиснуте повітря в циліндри через отвори для свічок запалювання або форсунки при непрацюючому двигуні в положенні, коли клапани закриті, і при цьому вимірюють вихід повітря за показаннями манометра приладу. Діагностування за прориванням газів у картер двигуна. Проривання газів у картер двигуна значною мірою залежить від спрацювання та навантаження двигуна і мало залежить від частоти обертання колінчастого вала. Об'єм газів, що прориваються, вимірюють за допомогою газових лічильників або простих і надійних у роботі приладів типу реометрів. Проривання газів у картер нового двигуна досягає 15...20 л/хв, спрацьованого — 80...130 л/хв. Для вимірювання проривання газу заглушують пробками трубки системи вентиляції картера і потім вставляють у горловину маслоналивного патрубка наконечник гумового шланга, другий кінець шланга з'єднують із вхідним патрубком газового лічильника (або реометра), що міститься в кабіні водія у вертикальному положенні. Випробування проводять під час руху на II або III передачах, педаль дросельної заслінки натискують до відмови. Випробування проводять протягом 30 с, після чого різницю показань лічильника між двома вимірюваннями переводять у літри за хвилину (л/хв). У разі значного спрацювання двигуна тиск газів у картері підвищується до 0,008...0,016 МПа. Виміряти його можна за допомогою звичайного водяного п'єзометра. Проривання газів у картер двигуна можна виміряти також газовим витратоміром на стенді тягових якостей під навантаженням, що відповідає максимальному крутному моментові двигуна на прямій передачі. Діагностування за прориванням газів у картер двигуна має обмежене застосування з багатьох причин (велика трудомісткість, низька точність тощо). Діагностування за угаром масла застосовують у тих випадках, коли немає втрат масла через корінні підшипники і нещільності картера. Угар масла залежить від спрацювання кілець, поршнів, циліндрів та від герметичності клапанів. Витрату масла на угар перевіряють при швидкості руху 35...45 км/год. Двигун заправляють маслом до верхньої мітки покажчика рівня, а після пробігу не менш як 50 км доливають масло до цього ж рівня і підраховують фактичну витрату (угар) масла. Одночасно при цьому перевіряють витрату палива. Середня експлуатаційна витрата масла, встановлена для карбюраторних двигунів, 4 % витрати палива, для дизелів — 5 %. Якщо витрата масла тільки на угар досягає цих значень, то двигун треба направити в ремонт. Звичайно угар масла має становити 0,5...1 % витрати палива. Затягання деталей кріплення головки блока.При роботі двигуна кріплення головки блока циліндрів ослаблюються внаслідок деякого сідання прокладки і здовження болтів 1...4 (шпильок). Кріпити головку блока циліндрів треба з середніх гайок (болтів), поступово переходити до крайніх у певній послідовності. Болти (гайки) кріплять у два прийоми: попередньо й остаточно. Величина затягання забезпечується динамометричною рукояткою відповідно до заводських вказівок про обслуговування автомобілів. Гайки (болти) кріплення чавунної головки блока підтягають на підігрітому двигуні, а з алюмінієвих сплавів — на холодному. Це пояснюється тим, що затягування гайок на гарячому двигуні після його остигання виявиться недостатнім унаслідок того, що головка блока з алюмінієвих сплавів стискується більше, ніж стальні шпильки. При затягуванні кріплень головки блока слід мати на увазі, що недостатнє і неправильне затягування призводить до руйнування прокладки головки блока, деформування головки, порушення герметичності камери згоряння.  | Запобігання прогорянню прокладок і головок циліндрів двигуна.Прогоряння прокладок і головок циліндрів двигунів — один із найпоширеніших дефектів, причому це відбувається у двигунах із різними пробігами і термінами експлуатації. Дефект цей буває двох видів: прогоряння прокладок і головок по перемичках між сусідніми камерами згоряння; точкове руйнування нижньої площини головки в зоні біля впускних клапанів і коло циліндра та прогоряння прокладок у цих же місцях. Перший вид трапляється порівняно рідко. Основною причиною детонаційного згорянняу двигуні (при правильно встановленому куті випередження запалювання) є застосування бензину з октановим числом, нижчим від установленого інструкцією заводів-виготов-лювачів. Помилково побутує думка, що при низьких температурах можна користуватись паливом із меншим октановим числом, наприклад, застосовувати замість А-76 для двигуна бензин А-72. Низька температура навколишнього повітря не знімає вимог до застосовуваного палива, оскільки повітря в повітряний фільтр надходить із підкапотного простору з досить високою температурою. Крім того, в зимовий період для підвищення ефективності роботи опалювального приладу і запобігання заморожуванню радіатора водії підтримують підвищену температуру охолодної рідини. При цьому, природно, підвищується температура повітря в підкапотному просторі й посилюється детонація. Детонаційне згоряння може виникнути і при занадто ранньому куті випередження запалювання. Дуже часто в експлуатації треба враховувати вплив на кут випередження запалювання індивідуальних особливостей двигуна та якості палива. У таких випадках треба коректувати кут випередження за детонаційною пробою. її роблять так: прогрівають двигун до температури охолодної рідини (не менш як 85 °С) і рухаються на автомобілі по рівній ділянці дороги на вищій передачі з найменшою швидкістю. Різко натискують до упору педаль акселератора і тримають її в такому положенні 10... 15 с, розганяючи автомобіль і прислухаючись до роботи двигуна. Якщо при розганянні автомобіля детонація прослухувалась, переміщують стрілку октан-коректора в бік знака мінус (-) у положення, при якому детонація не прослухується; якщо детонації немає, послідовно, по одній поділці, переміщують стрілку октан-коректора в бік знака плюс (+) до появи слабо прослухуваної детонації, а потім переміщують стрілку на одну поділку в бік знака мінус (-) і в цьому положенні закріплюють регулювальні гайки октан-коректора. Слід пам'ятати, що при правильному встановленні запалювання слабий детонаційний стукіт може прослухуватись тільки на початку розганяння автомобіля. Коли двигун працює, на рівень його детонації впливають і деякі інші фактори: сорт бензину (при етилованому бензині потрібне деяке зменшення випередження запалювання порівняно з неетилованим того самого сорту); забирання повітря в повітряний фільтр із підкапотного простору в теплу пору року; перевантаження автомобіля; неправильне використання передач у коробці передач (робота на прямій передачі при малій частоті обертання і рушання з місця на другій передачі). Підгорянню прокладок і головок циліндрів двигуна можна запобігти такими заходами: регулярним підтяганням болтів кріплення головок до блока циліндрів; експлуатацією двигунів без перегрівання; застосуванням палива відповідно до інструкції заводу-виготовлювача; правильним установленням кута випередження запалювання і коректуванням його за детонаційною пробою; підведенням зовнішнього повітря в теплу пору року до повітряного фільтра карбюратора; правильним використанням передач у коробці передач; завантажуванням автомобіля за його вантажопідйомністю; відновленням об'єму камер згоряння при ремонті головок. Регулювання теплових зазорів клапанів.Теплові зазори збільшуються внаслідок спрацювання кулачків і штовхачів, клапанів і коромисел. Збільшення зазору призводить до збільшення шуму в клапанному механізмі, втрати потужності, а зменшення — до обгоряння сідел і клапанів, «чхання» в карбюраторі, «пострілів» у глушителі, зменшення потужності, збільшення спрацювання циліндрів. Регулювання зазорів (рис. 5) — трудомістка операція, оскільки на багатьох автомобілях треба виконувати додатково демонтажі. Тепловий зазор вимірюють щупом. Розмір зазорів зазначають в інструкціях автомобільних заводів. Теплові зазори регулюють при повністю закритих клапанах, починаючи з першого циліндра, а потім у послідовності, що відповідає порядку роботи двигуна. Зазор змінюють до потрібної величини, обертаючи регулювальний болт штовхача або гвинта коромисла.  Рис. 5. Регулювання теплових зазорів клапанів у двигунах з верхнім розміщенням клапанів Очистка нагару в циліндрах двигуна.Нагар призводить до залягання поршневих кілець, зависання клапанів, перегрівання двигуна, посилення спрацьовування, підвищення витрати палива, зниження потужності двигуна та ін. В умовах експлуатації нагар можна видалити при знятій головці блока ібез зняття її. При знятій головці блока нагар видаляють металевими скребками, волосяними щітками й обтиральними кінцями. Перед видаленням нагар розм'якшують гасом. Без зняття головки блока нагар видаляють так. У кожен циліндр підігрітого двигуна заливають 150...200 см3 суміші, що становить 80 % гасу і 20 % масла для двигунів. Потім заміняють свічки старими, прокручують кілька разів колінчастий вал, через 10...12 год заводять двигун на 20...30 хв (за цей час розм'якшений нагар вигоряє). Після видалення нагару треба змінити масло в картері двигуна і перед пуском у кожен циліндр залити по 20...ЗО см3 свіжого масла. Є й інші способи очистки нагару без зняття головки блока (із застосуванням денатурованого спирту, ацетону та ін.), але вони мають обмежене застосування. Поточний ремонт двигунів У процесі експлуатації двигунів зношуються тертьові деталі. У результаті цього виникають несправності, які усувають при поточному ремонті. При проведенні поточного ремонту автомобілів і агрегатів додержуються таких правил: 1. Агрегати розбирають не повністю, а до меж, що дають можливість усунути відмову і перевірити стан деталей. 2. Знімають агрегат з автомобіля тільки тоді, коли трудомісткість його заміни менша трудомісткості обсягу робіт без зняття або коли ремонт без зняття з автомобіля не можливий. 3. Агрегати, що надійшли на пости, попередньо очищають від бруду і промивають. 4. Для проведення розбірно-складальних робіт застосовують необхідне технологічне устаткування й інструмент. Основні несправності двигуна, їхні ознаки і причини.Зниження потужності: двигун не розвиває нормальні обороти під навантаженням, сильно димить і глохне, не має прийомистості. Причинами цієї несправності можуть бути: утворення нагару на свічах, голівках поршнів, у камері згоряння, на клапанах і поршневих кільцях, відкладеннях у впускній системі і системі охолодження; неправильне регулювання клапанів; нещільна посадка клапанів у гніздах; несправність системи запалювання; ушкодження прокладки головки блока циліндрів; руйнація або втрата пружності пружин клапанів. Підвищену витрату масла можуть викликати такі причини: витікання масла через сальники колінчастого вала, нещільність у з'єднаннях картера кришок клапанної коробки, кришок і розподільних шестерень, трубопроводів масляного радіатора; знос або поломка поршневих кілець; знос по висоті кільцевих канавок у поршні; закоксування прорізів у маслозйомних поршневих кільцях; знос циліндрів, утворення задирів або подряпин на їх поверхні та інше. Сильний стукіт під час роботи виникає за таких причин: неправильні зазори між клапанами і штовхачами; неправильна установка запалювання: знос, підплавлення вкладишів корінних і шатунних підшипників; знос поршневих пальців і поршнів; знос розподільних шестерень; знос розподільного вала і його підшипників; знос штовхачів, клапанів і сідел клапанів та інше. Перевитрата палива відбувається через: знос поршнів, кілець і робочої поверхні циліндрів; роботу двигуна на бідній або багатій суміші і т. д. Низький тиск масла може бути викликаний такими причинами: знижений рівень масла в картері; знос корінних і шатунних підшипників; несправність масляного насоса; порушення регулювання редукційного клапана масляного насоса або засмічення його; перегрівання двигуна. Наявність води в циліндрах можна визначити за перебоями у роботі двигуна при справних системах живлення і запалювання. Відбувається це за таких причин: ослаблення затягування гайок шпильок кріплення в головці блока циліндрів; несправність прокладки головки; тріщина в блоці або головці блока. Заміна шатунно-поршневої групи двигуна. Якщо циліндри двигуна дуже зношені і форма їх порушена, двигун знімають з автомобіля і направляють у поточний ремонт для заміни поршнів, поршневих кілець, а в окремих випадках і гільз, поршневих пальців і вкладишів. Двигун розбирають на спеціальному стенді, що дозволяє повертати його на 360° щодо осі колінчастого вала. Всі зняті деталі промивають і перевіряють. При ремонті двигуна не допускається знос робочої поверхні гільз циліндрів більш ніж на 0,2 мм, шатунних шийок — більш ніж на 0,05 мм, корінних шийок — більш ніж на 0,07 мм; виключаються тріщини будь-якого характеру і розташування на блоці і головці. Зношені гільзи циліндрів випресовують за допомогою зйомника для демонтажу гільз. Якщо в нижній частині блока місця установок кілець ущільнення сильно уражені корозією, особливо крапковою, і є глибокі раковини, припостановці нової гільзи може спостерігатися погане ущільнення і підтікання охолодної рідини. Щоб уникнути цього, необхідно заповнити місця, вражені корозією, епоксидною смолою ЗД-6 і зачистити. Краї верхньої частини блока, що першими стикаються з гумовими кільцями ущільнення при запресовці гільзи, округляють і зачищають наждачним полотном або папером для запобігання пошкоджень кілець в процесі цієї запресовки. Перед запресовкою гільзи підбирають по блоку так, щоб бурт гільзи виступав над площиною блока циліндрів на 0,02... 0,165 мм (залежно від марки двигуна). Різниця в розмірі виступу бурту в різних точках однієї гільзи не повинна перевищувати 0,01мм. Гільзи в блок циліндрів запресовують, користуючися спеціальними пристосуваннями. При запресуванні гільзи необхідно стежити, щоб не зрізалися виступаючі частини кілець ущільнення об крайки отвору блока циліндрів. Перед запресовкою у блок гільзи сортують по групах за розмірами. Добір поршнів за розмірами циліндрів.При ремонті двигуна сполучені деталі підбирають двома способами: штучним і груповим (селективним). Штучний добір полягає в тому, що до однієї деталі даного сполучення добирають другу деталь, виходячи з розміру, зазору або натягу, що припускається при їхньому складанні. Наприклад, поршні і гільзи двигуна обробляються з широким полем допусків, унаслідок чого будь-який поршень не може бути поставлений у будь-яку гільзу. За технічними умовами на складання треба встановлювати нормальний зазор між гільзою і поршнем. Гільза і поршень добираються за розміром зазору за допомогою двох щупів. Товщина одного дорівнює мінімально припустимому зазору, іншого — максимально припустимому. Якщо поршень з тонким щупом проходить по всій довжині гільзи вільно, а з щупом, товщина якого відповідає максимальному зазору, не проходить, такі поршень і гільзу вважають скомплектованими. Щуп закладають на всю довжину юбки поршня в площині, перпендикулярній до осі отворів бобишок. Для точності добору рекомендується пропускати поршень із щупом у трьох-чотирьох положеннях по окружності гільзи. Гільзу і поршень можна підбирати і без щупів попереднім виміром сполучених деталей. Для цього заміряють внутрішній діаметр гільзи, тобто знаходять її дійсний розмір. Виходячи з припустимого нормального зазору, визначають необхідний діаметр спідниці поршня: 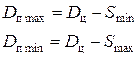 де и — максимальний і мінімальний діаметри поршня; — діаметр циліндра; Smax и Smin — допустимі максимальний і мінімальний зазори. При штучному доборі деталей не завжди забезпечується необхідна якість складання сполучення і, крім того, витрачається багато часу на добір деталей. Незважаючи на недоліки, штучний добір широко застосовується на АТП, тому що він не потребує попередньої технологічної підготовки. Груповий (селективний) добір характеризується таким: деталі сполучаються після їхньої обробки і контролю; попередньо сортують за розмірами на визначені групи. Відсортовані деталі помічають цифрами, буквами або кольоровими фарбами. При складанні визначеного сполучення використовуються деталі однієї групи. Наприклад, якщо діаметр циліндра двигуна належить до групи А, в цей циліндр має бути підібраний поршень групи А. У двигунах позначення розмірної групи поршня вибивають на днищі поршня. Заміна поршневих кілець. Після того, як прийняте рішення про необхідність заміни поршневих кілець, двигун треба розібрати, не знімаючи його з автомобіля, у такій послідовності: злити рідину із системи охолодження двигуна; від'єднати від головки циліндрів усі трубопроводи, захистити їхні внутрішні порожнини від попадання пилюки і бруду; зняти кришку головки циліндрів; зняти коромисла разом з осями і вийняти штанги; послабити гайки кріплення головки циліндрів, дотримуючи ту ж послідовність, що і при затягуванні, потім вивернути їх; зняти головку циліндрів з двигуна; зняти обережно прокладку головки циліндрів; зняти піддон картера; вивернути болти і зняти кришки нижніх головок шатунів; вийняти поршень у зборі з шатуном із гільзи. При заміні поршневих кілець необхідно перевірити стан дзеркала гільзи і ступінь її спрацювання. Переконавшись, що поверхня кожної гільзи не має задирок, що потребують її заміни, проміряють гільзи за діаметром, з'ясовуючи відхилення в розмірах. Максимально допустимі відхилення від правильної геометричної форми, при яких заміна кілець може забезпечити нормальну витрату масла і задану потужність, становлять 0,13 мм. Потім очищають канавки і днище поршня від нагару і перевіряють ступінь спрацювання канавок заміром зазору між кільцями і стінкою канавок. При цьому кільце повинне цілком увійти в канавку. Особливо інтенсивно зношується верхня канавка. Якщо зазор у канавці верхнього кільця перевищує 0,25 мм, доцільно замінити поршень. Поршневі кільця до гільз циліндрів і поршнів підбирають відповідно до розмірів гільз циліндрів і поршнів. При цьому зазор у замку кілець повинен знаходитися у визначених межах. Такий зазор у стику поршневих кілець забезпечується підпилюванням стиків кілець (стежачи за тим, щоб стики кілець були паралельними). Підбираючи кільця до поршневих канавок, необхідно звертати увагу на те, щоб кільця вільно оберталися в канавці поршня. Зазор перевіряють за допомогою щупа товщиною 0,05—0,08 мм. За потреби кільця протирають дрібнозернистим бруском або наждачною шкуркою. Компресійні кільця встановлюють на поршні фаскою догори. Поршневі кільця розташовують так, щоб між стиками двох сусідніх кілець був однаковий кут. Перед установкою в циліндр поршень і поршневі кільця змащують маслом для двигунів. Заміна шатунних і корінних вкладишів двигуна.Якщо стукають підшипники, а тиск у масляній магістралі нижче 0,5 кгс/см2 на холостому ходу при справно працюючому масляному насосі і редукційних клапанах, необхідно замінити вкладиші. Для цього з картера двигуна зливають масло, знімають бризковики двигуна, викручують болти кріплення масляного картера і знімають картер з прокладками. Потім викручують болти кріплення фланця мас-лоприймача і знімають маслоприймач із прокладкою, обережно відділяючи її викруткою від площини блока циліндрів. Після цього розшплінтовують і відпускають гайки шатунних болтів, знімають шатунні кришки з вкладишами попарно (1—5, 2—6, 3—7, 4—8), повертаючи при цьому колінчастий вал за допомогою пускової ручки. Перед зняттям кришки необхідно позначити. Поверхню постелі нижньої голівки шатуна, шатунні шийки і кришки промивають і протирають, потім перевіряють поверхню шатунних шийок, на яких не повинно бути задирок і рисок. Знос шийок не повинен перевищувати 0,05 мм. При наявності задирок, рисок, зносі поверхні шийок вище допустимого розміру заміняти вкладиші недоцільно. У цьому випадку двигун варто зняти з автомобіля і направити в капітальний ремонт. Після перевірки стану шатунних шийок колінчастого вала промивають і протирають нові вкладиші того ж розміру і встановлюють їх у постелі кришок і нижніх голівок шатуна, попередньо змастивши поверхню вкладиша і шийки маслом для двигуна. При установці необхідно стежити за тим, щоб вкладиші з отворами для масла були вставлені в постіль шатуна і фіксуючі виступи, які є на одному із стиків кожного вкладиша, правильно заходили впризначені для них пази в постелях.Глава 7 Заміна колінчастого вала.Для заміни колінчастого вала двигун знімають з автомобіля і розбирають на спеціальних стендах. Заміна колінчастого вала є дуже трудомісткою відповідальною операцією і проводиться в крайніх випадках. Якщо при заміні колінчастого вала проводять ряд супутніх ремонтів (ремонт блока і головки циліндрів і т. ін.), тоді двигун направляють у капітальний ремонт. Для заміни колінчастого вала необхідно виконати роботи в такій послідовності: зняти піддон картера; зняти масляний насос; зняти маховик і картер маховика; зняти шків і кришку шестерень розподілу; зняти кришки шатуна і проштовхнути поршні до головки циліндрів; вивернути болти кріплення кришок корінних підшипників і зняти кришки, перевіривши при цьому відповідність клейма на кришці клейму на блоці циліндрів; зняти колінчастий вал. Якщо в процесі ремонту виникає необхідність заміни шестерень колінчастого вала, то знімають шків, кришку шестерень розподілу і передню кришку корінного підшипника, а потім спресовують знімачем шестерню. Заміна втулки верхньої головки шатуна.Зношені втулки верхньої головки шатуна заміняють. Для випресовки і запресовки чопів застосовують оправки. Перед запресовкою втулки добирають за отвором верхньої головки шатуна з забезпеченням натягу не менше 0,05 мм. Втулка має бути запресована на рівні з торцевими поверхнями верхньої головки шатуна. Запресовану втулку розточують на горизонтально-розточувальних верстатах або обробляють розгорткою. Внутрішня поверхня розточеної втулки має бути чистою, без рисок, чистота поверхні не нижче 8-го класу. Знос не повинен перевищувати 0,004 мм. Шатуни по внутрішньому діаметру отвору у втулці сортують на розмірні групи. Кожну групу шатунів маркують маслостійкою фарбою визначеного кольору. Заміна переднього і заднього сальників колінчастого вала.Заміну переднього і заднього сальників колінчастого вала здійснюють при підтіканні в них масла. Проте підтікання масла може бути викликано не тільки спрацюванням сальників, а й підвищеним тиском масла в картері двигуна в результаті підвищеного пропускання газів поршневими кільцями, або несправності вентиляції картера. Тому перед заміною сальників перевіряють стан системи вентиляції картера і тиск газів у картері двигуна. Сальник заміняють новим у випадку втрати еластичності манжети або її зносу, при повертанні манжети або переміщенні її в обоймі, а також при послабленні пружини сальника, щоб не було підтікання масла через місце посадки сальника, гніздо в кришці розподільних шестерень змащують тонким шаром герметику. Щоб герметик не встиг висохнути, гніздо змащують безпосередньо перед запресовкою сальника (поверхні кришки і сальника, які сполучаються, повинні бути чистими). Перед запресовкою сальника в кришку робочу поверхню манжети змащують тонким шаром солідолу, щоб виключити можливість її ушкодження під час монтажу кришки на колінчастому валу. Перед установкою на кришці поверхню прокладки кришки розподільних шестерень також змащують герметиком. Після запресовки в кришку розподільних шестерень сальник центрують щодо осі колінчастого вала за допомогою спеціальної оправки. Кришку 1 розподільних шестерень встановлюють на місце і закріплюють болтами так, щоб вона вільно переміщалася в будь-якому напрямку в межах зазорів між болтами й отворами під болти в кришці. Потім надівають на передній кінець колінчастого вала конічну оправку 2, що центрує, і, вкручуючи храповик 3, переміщають її настільки, щоб оправка ввійшла конічною поверхнею в сальник і сцентрувала його щодо осі колінчастого вала. Лише після цього рівномірно затягують усі болти і гайки, що кріплять кришку до блока, відвертають храповик і знімають оправку. Сальник працює надійно в сполученні з чисто відполірованою зовнішньою поверхнею ступиці. Манжета сальника за наявності на ній спрацьованих канавок або інших пошкоджень не забезпечує герметичності з'єднання.  Центрування переднього сальника колінчастого вала:1 — кришка розподільних шестерень з сальником; 2 — конічна оправка; 3 — храповик колінчастого вала Ступицю на передній кінець колінчастого вала напресовують до упора в масловідбійник за допомогою оправки. Після цього на ступицю встановлюють і закріплюють шківи колінчастого вала. На диску кожного шківа вибита мітка, яка при установці повинна знаходитися над шпоночною канавкою в ступиці. Храповик і ремінь вентилятора встановлюють у послідовності, зворотній процесу зняття. ПОСЛІДОВНІСТЬ ВИКОНАННЯ РОБОТИ: Визначення величини компресії в циліндрах двигуна 1. Вивчити будову та підготовити до роботи прилад компресометр. 2. Запустити двигун і прогріти його до робочої температури. 3. Зупинити двигун. 4. В карбюраторному двигуні викрутити всі свічки. В дизельному двигуні зняти форсунку циліндра, що перевіряється. 5. Вставити наконечник компресометра в отвір для свічки чи форсунки. 6. Карбюраторний двигун прокрутити стартером на протязі 3-5 с. Дизельний двигун запустити на мінімальних обертах холостого ходу. 7. По шкалі компресометра зафіксувати максимальний тиск в циліндрі. 8. Випустити повітря з компресометра через зворотній клапан. 9. Виконати операції 5 – 8 для кожного циліндра двигуна. 10. Визначити різницю максимального і мінімального значення компресії в різних циліндрах двигуна. 11. Одержані значення порвняти з нормативними. |