III. КРЕПЛЕНИЕ ЦИЛИНДРА ТУРБИНЫ И КОРПУСА ПОДШИПНИКА Методические указания Следует обратить внимание на следующие основные вопросы: 1) конструкция корпусов паровых турбин; 2) фланцевое соединение корпуса турбины, обеспечение необходимого натяга шпильки и его контроль; 3) крепление цилиндра турбины и корпуса подшипника к фундаментальной раме, обеспечение тепловых расширений статора; 4) конструкция паровых и сопловых коробок; 5) конструкция сопловых сегментов; 6) конструкция диафрагмы; 7) установка диафрагм в цилиндре или обойме; 8) материалы, применяемые для изготовления: а) корпусов; б) сопловых и паровых коробок; в) диафрагм; г) сопловых элементов; 9) порядок сборки и разборки узлов статора турбины. К статору паровой турбины относятся: 1) корпус турбины: а) цилиндр высокого давления (ЦВД); б) цилиндр среднего давления (ЦСД); в) цилиндр низкого давления (ЦНД); 2) паровые коробки; 3) сопловые аппараты; 4) диафрагмы; 5) фланцы горизонтальных и вертикальных разъёмов. I. КОРПУС ТУРБИНЫ Корпус турбины (цилиндр) служит для крепления всех деталей статора и обеспечивает прохождение пара по заданному пути. При работе корпус паровых турбин подвержен действию следующих сил: 1) усилий от разности давлений пара внутри цилиндра и атмосферным; корпус ц.н.д. может быть нагружен внешним давление атмосферы; 2) усилий, приложенных со стороны диафрагм и направляющих аппаратов; 3) усилий от ротора, который может стать источником вибрационной нагрузки; 4) усилий, приложенных со стороны пароподводящих труб; 5) усилий от температурных напряжений, вызываемых разной температурой стенки корпуса по длине и толщине, разной температурой стенки по окружности в одном и том же сечении. Главными напряжениями являются термические напряжения и напряжения, возникающие от действия внутреннего давления пара. Значительные размеры корпуса и высокая температура обуславливает заметные температруные деформации (фиг.1). Для изготовления корпусов применяют стальное и чугунное литьё, а также сварные конструкции. В настоящее время всё шире применяются сварные и сварно-литые корпуса турбин. Эти конструкции позволяют существенно снизить вес, исключить применение сложных отливок. Корпуса, которые принято называть сварными, включают более или менее крупные литые части и в сущности являются сварно-литыми. Фиг.1. Деформация ц.в.д. турбины при пуске: а) в случае превышения температур внутри корпуса; б) в случае превышения температур снаружи фланцев. Однако, сварно-литыми, обычно, называются конструкции в которых сварка играет подсобную роль, а не главную. Наибольшее применение сварно-литые корпуса нашли в ц.в.д. и ц.с.д. Этому способствовали прогресс сварки и хорошая свариваемость углеродистой и углеродисто–малибденовой сталей, из которых, обычно, отливаются эти корпуса. В турбинах малой и средней мощности с начальным давлением пара 12-16 ата и температурой до 250ºС корпуса изготавливают из чугунного литья. Корпус обычно имеет горизонтальный разъём (фиг.2), необходимый для сборки и разборки, а также замера осевых и радиальных зазоров между деталями ротора и статора, и один или два вертикальных разъёма. Наличие вертикальных разъёмов позволяет унифицировать отдельные части цилиндров для турбин различной мощности и типов (в основном для серий с одинаковыми начальными параметрами пара), а также изготовить ц.н.д., ц.с.д. и ц.в.д. из различных материалов. Фиг.2. Горизонтальный разъем нижней передней части корпуса турбины К-4-35 (АК-4-4) КТЗ. Это позволяет сэкономить дорогостоящие стали, необходимые для изготовления деталей, работающих при высоких давлениях и температурах. Место встречи вертикального и горизонтального разъёмов называют «крестовым стыком». Фланцы горизонтального разъёма в турбинах высокого давления являются одной из наиболее напряжённых частей корпуса и в эксплуатации причиняют немало затруднений в связи с трудностью их уплотнения. В расточках турбины устанавливаются диафрагмы, сопловые сегменты, обоймы паровых уплотнений (переднего и заднего), в корпусе находятся каналы, подводящие и распределяющие пар, патрубки промежуточных отборов и выпускной патрубок. Всё это представляет собой довольно сложную конструкцию. Поэтому корпусу стараются придать по возможности простую форму. Размеры корпуса определяются размерами проточной части турбины. Иногда диаметр корпуса, следуя за диаметром проточной части, изменяется несколькими резко выраженными ступенями. Корпус заднего подшипника чаще всего выполняется литым заодно с ц.н.д. . Корпус же переднего подшипника, где температура пара высока, выполняется литым отдельно от корпуса турбины, во избежание возможно больших температурных напряжений и перемещений. При пуске и остановке турбины возможно кратковременное накопление значительных масс воды в любой ступени. Для удаления этой влаги существуют специальные карманы или колодцы в корпусах турбин и другие устройства, из которых влага отводится в систему продувания. На фиг.3а показаны различные устройства для сбора и отвода влаги.  Фиг.3. Устройства для отвода влаги из последних ступеней: а, б – активных Диафрагмы устанавливаются с осевым зазором 1, через который влага выбрасывается в окружной канал 2, по желобкам 3. На другой конструкции (фиг.3б) окружные каналы 4 для сбора и стока влаги образуются фасонными накладками 5. Влага отводится наружу через канал 6 в корпусе турбины; для уменьшения их числа делают по одному каналу на группу ступеней. Аналогичные устройства в реактивных ступенях (фиг.3в,г) несколько проще: влага отводится либо из каждой ступени через отдельные радиальные отверстия 8 в корпусе, либо из группы ступеней. Отверстия 9 служат для перетекания воды. Щитки 10 предохраняют корпус от эрозии. Фиг.3. Устройства для отвода влаги из последних ступеней: в, г – реактивных. В связи с переходом паровых турбин на критические и сверхкритические начальные параметры пара широко применяются двустенные корпуса. Общая идея двустенной конструкции состоит в следующем. Проточная часть турбины заключается во внутренний корпус (обойму), который схватывается наружным корпусом. Пространство между наружным и внутренним корпусом заполнено паром среднего давления. Поэтому толщина стенок корпусов и размеры фланцев получаются значительно меньше, чем в обычных (одностенных). Значительно облегчаются температурные условия работы корпусов и резьбовых соединений. Примером отечественной конструкции турбины сверхвысокого давления является изображенная на фиг.4 предвключенная турбина Л.М.З. типа СВР-50-3. Параметры этой турбины: Nе = 50МВт; n = 3000 об/мин.; Pо = 200 ата; tо = 550÷570ºС; P2 = 34 ата. Корпус турбины отлит из стали 20хМЛ. Внутренний корпус (обойма) состоит из двух половин; крепление их друг с другом и подвеска к корпусу показаны на фиг.4 (узел 2). Обе половины стянуты шпильками 5. Центровка внутренней обоймы осуществляется шпонками 4. Их конструкция показана на фиг.4 (узел 1). К обойме присоединены сопловые сегменты первой ступени. Центровка их в вертикальной плоскости осуществляется шпонками 6. В такой конструкции нагрузка внутреннего цилиндра уменьшается благодаря тому, что он омывается снаружи паром сравнительно высокого давления. Конструкция с внутренним корпусом снижает также разность температур по обе стороны стенок как внутреннего, так и наружного цилиндра. В настоящее время перспективной является конструкция корпуса с вертикальным разъёмом [2]. Такая конструкция заменит сильно нагруженные фланцевые соединения горизонтального разъёма сравнительно слабонагруженным соединением вертикального типа. 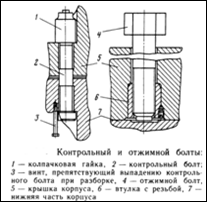 II. ФЛАНЦЕВЫЕ СОЕДИНЕНИЯ Для соединения частей корпуса применяются фланцевые соединения. Фланцевые соединения испытывают значительную нагрузку, имеют толщину до 300 мм и более. Стенки корпуса сопрягают с фланцем скруглением большого радиуса или коническим переходом. Для уменьшения нагрузки на болты и изгиба фланцев, болты располагают возможно ближе к стенки корпуса. В наиболее нагруженных соединениях: для податливости и уменьшения термических напряжений применяют колпачковые гайки (фиг.5) или дистанционные втулки.  Герметичность вертикального и горизонтального разъёмов достигается холодной или горячей затяжкой болтов и шпилек, при которой в них создаются необходимые упругие напряжения ( до 30-40 кг/мм² ). В настоящее время для резьбовых соединений более М52 применяют горячую затяжку, т.е. необходимую упругую деформацию обеспечивают нагревом. Во фланцах, кроме резьбовых соединений под болты или шпильки, имеются отверстия под отжимные болты и штифты. Перед сборкой турбины фланцы горизонтального разъёма тщательно очищают, подшабривают и покрывают мастикой, состоящей из графита на варёном льняном масле. Иногда в состав мастики вводят сурик и др. составляющие. Особенно важно обеспечить плотность и надёжность соединения фланцев при металлическом контакте. Применение прокладок не допускается. На некоторых заводах, после чистовой обработки болты проверяют по краске. Производится лишь небольшая шабровка. Наружный край фланца примерно на половину его ширины опиливают. Удаляемый металл имеет форму клина толщиной от 0 до 0,04-0,045 мм на наружном крае. После соединения обеих половин корпуса (до затяжки) по наружному краю входит щуп толщиной 0,08-0,09 мм. При затяжке болтов создаётся повышенное удельное давление на внутренней части фланцевого контура. Этот способ позволяет избежать трудоёмкой шабровки. Обычный способ затяжки при помощи ключа и удлинённой трубы не обеспечивает равномерного обжима болтов. Значительно более совершенной является окончательная затяжка фланцев при помощи нагрева болтов; охлаждаясь, болт стягивает соединение. У турбин высокого давления затяжка болтов должна быть сильной во избежание просачивания пара. Поэтому болты или шпильки фланцев таких турбин выполняют их хромомолибденовой стали, хорошо переносящей действия высоких температур и располагают их близко друг к другу. В настоящее время для прогрева применяют 3 способа: 1) автогенной горелкой с длинным нережущим пламенем, которое вводится в отверстие, просверленное в болте; 2) электрическим нагревательным аппаратом (электронным или угольным электродом), вставленным в отверстие болта; 3) паром или горячим воздухом, струя которого направляется в отверстие болта (фиг.5). В остывших болтах (шпильках) замеряется вытяжка (фиг.5), величина которой устанавливается окончательно заводом–изготовителем экспериментально. В таблице №1 приведены данные по затяжке шпилек фланцев горизонтального разъёма ц.в.д. турбины К-150-130 ХТГЗ. Перед отворачиванием гаек болты (шпильки) нагревают до образования зазора между торцом гайки и фланцем. Время нагрева зависит от способа нагрева и диаметра болта. Очень большая длина фланца горизонтального разъема турбины высокого давления по сравнению со стенками корпуса вызывает трудности при пуске из холодного состояния или остановке турбины, вследствие неодинаковой скорости нагрева и охлаждения фланцев и болтов, возможно и неодинаковое их расширение или сжатие. Температура головок болтов может быть ниже температуры фланцев примерно на 50°С, а следовательно, возможно опасное перенапряжение болтов с переходом за пределы текучести. Таблица №1 Корпус ц.в.д. | Шпилька | Длина шпильки | Угол поворота гайки после нагрева шпильки (°С) | Зазор между торцом гайки и плоскостью фланца после нагрева шпильки (мм) | Удлине-ние шпильки (мм) | Наружный | 1М140 | 1265; 1280 | | 2,5 | 1,3÷1,4 | 1М140 | 1025; 985 | | 1,1 | 0,7÷0,75 | 1М85 | 970; 982 | | 1,9 | 1,0÷1,1 | 1М64 | | | 0,8 | не замеря-ется | Наряду с этим более массивные фланцы интенсивнее излучают тепло, чем стенки корпуса турбины, поэтому при быстром пуске нагрев фланцев может значительно отставать от нагрева стенки корпуса. Температура фланцев обычно на 40÷100°С ниже температуры корпуса. В этой связи целесообразно производить паровой обогрев болтов и фланцев. Один из способов обогрева фланцев паром, пропускаемым через короба 1 и 2 из листовой стали, приваренные вдоль фланцев (фиг.6). Фиг.6. Устройство для обогрева паром фланцев и шпилек корпуса турбины высокого давления. Для обогрева соединительных болтов или шпилек пар раздельно пропускается через отверстие в них, что позволяет регулировать относительную скорость прогрева фланцев и шпилек. Причем это сокращает время пуска турбины. III. КРЕПЛЕНИЕ ЦИЛИНДРА ТУРБИНЫ И КОРПУСА ПОДШИПНИКА Обеспечение тепловых расширений статора турбины В настоящее время найден достаточно простой и надёжный способ крепления цилиндров с корпусами подшипников и на фундаментных рамах. Он является типичным для турбин различного типа: конденсационных противодавленческих и с различным числом цилиндров. При креплении должны быть обеспечены: 1) свобода теплового расширения цилиндров и корпусов подшипником в осевом и радиальном направлениях; 2) сохранение постоянства взаимного положения расточки цилиндров турбины и корпусов подшипников, т.е. без нарушения соосности последних, которые часто выполняются как отдельные детали. Величины теплового расширения турбины и её деталей различны и находятся в зависимости от температуры рабочего пара и линейных размеров турбины. Тепловое расширение цилиндров каждой турбины изменяется как по величине, так и по знаку (расширение и сжатие) при пуске, нагружении, изменении режимов работы и при остановке турбины. Корпуса небольших турбин, а также ц.в.д. многоступенчатых турбин обычно подвешиваются к корпусам переднего и заднего подшипника (фиг.8) при помощи лап или полуфланцевых соединений, укреплённых на фундаментной плите (фиг.7,9,10). Непосредственно с фундаментной плитой корпус турбины не соединяется, что позволяет ему свободно расширяться в любом радиальном направлении при помощи шпонок 3, 4, 1 (фиг.9). Удлинение в осевом направлении возможно, т.к. корпус подшипника может перемещаться по фундаментной плите, скользя по направляющим шпонкам 5, 2 (фиг.9). 
Соединение корпуса турбины с корпусом подшипника должно взаимно центрировать обе эти детали, при помощи лап (фиг.8 а,б,в,г,д). Лапы представляют собой продолжение фланца нижней половины корпуса, последние опираются на корпус подшипника. В небольших турбинах среднего и низкого давления применяются также полуфланцевые соединения 8 нижней половины корпуса с корпусом переднего подшипника. Радиальное расположение шпонок позволяет цилиндру свободно расширяться по радиусу. Иногда для соединения подшипника и фундаментной рамы применена гибкая опора 7 (фиг.9 б,г). При монтаже гибкая опора отклоняется на половину величины теплового расширения в сторону, противоположную расширению. При расширении гибкая опора проходит вертикальное положение и изгибается в обратную сторону (фиг.9,б) предварительного натяга. Гибкая опора может быть применена в турбинах, имеющих величину осевого теплового расширения до 18 мм. Болты и шпильки, которыми подшипники крепятся к фундаментной раме, не должны быть затянутыми, т.к. это препятствовало бы продольному перемещению подшипника по шпонке. Они должны создавать подвижные болтовые соединения 6 (фиг.9). На фиг.7 показаны конструкции крепления корпусов подшипников (болтовые соединения подвижные). Зазоры, указанные на фиг.7, достигаются заплечиком на шпильке (фиг.7а), в который упирается гайка, в конструкции фиг.7б – дистанционной втулкой; в конструкции фиг.7в – угольниками. Зазор Х (фиг.7), позволяющий подшипнику смещаться в осевом направлении, зависит от величины температурой деформации цилиндра турбины и может составлять 10-20 мм. На фиг.9а,в показаны схемы крепления одноцилиндровых конденсационных турбин с корпусами подшипников и на фундаментных рамах. Здесь корпус заднего подшипника выполнен заодно с корпусом турбины, т.к. выхлопная часть ц.н.д. имеет почти ту же температуру, что и подшипник. Как видно из фиг.9а, ц.н.д. опирается боковыми лапами 9 на поперечную фундаментную раму. Фиксирующие точки Ф (фикспунт) турбины определяются осями поперечной 1 и продольной (осевой) 2 шпонок (фиг.9), установленных на задней опоре выпускного патрубка. Тепловое расширение происходит в сторону ц.в.д.. Крепление корпусов ц.в.д. со стойками подшипников видно из фиг.9 и описано выше. В турбинах с противодавлением (фиг.9в,г), где разница в температурах большая, подшипник изготовляется отдельно от корпуса и схемы крепления аналогичны переднему подшипнику. Двухцилиндровые (фиг.10) и трехцилиндровые турбины можно рассматривать как состоящие из противодавленческих и конденсационных турбин. Поэтому, всё сказанное выше – о креплении цилиндров к корпусам подшипников и на фундаментных рамах – в равной мере относится и к многоцилиндровым турбинам. В двухцилиндровых двухпоточных турбинах (фиг.10,б) фиксирующая точка расположена приблизительно посередине ц.н.д.. Поверхности скольжения корпуса подшипника и фундаментной рамы при монтаже протираются серебристым графитом. IV. СОПЛОВЫЕ КОРОБКИ В некоторых конструкциях турбин впуск свежего пара происходит непосредственно в корпус турбины, в предсопловые камеры, где устанавливается сопловой аппарат. Это усложняет отливку корпуса, а при высоких начальных параметрах пара необходимо изготовлять ц.в.д. из высококачественной стали. Поэтому в современных турбинах широко применяются вставные сопловые коробки (фиг.11,12,13), в которых устраиваются сопловые камеры (числом от 1 до 5). Вставные сопловые коробки крепятся к корпусу турбины болтами или сваркой. Обычно сопловые коробки устанавливаются перед регулирующей ступенью ц.в.д.. У турбин с двустенным корпусом, работающих при сверхкритических параметрах, сопловая коробка небольших размеров вставляется во внутренний корпус перед первой ступенью (фиг.13). Сопловая коробка по конструктивному оформлению напоминает внутренний корпус двустенной конструкции, но укороченный до размеров паровпускного пояса. Кроме того, сопловая коробка занимает иногда лишь часть дуги окружности. Крепление сопловых коробок в корпусе допускает свободное их расширение в радиальных направлениях. Конструкции сопловых коробок разнообразны. Различают коробки с небольшой (менее 0,5) (фиг.11) и большой (0,5–1) степенью впуска (фиг.12,13). К первым относятся сопловые коробки вспомогательных турбин, а также главных турбин небольшой мощности, ко вторым – коробки главных турбин большой мощности. У вспомогательных турбин, в ряде случаев, сопловая коробка бывает объединена с корпусом регулирующего клапана (фиг.11а,в). На фиг.11 показаны сопловые коробки (вставные) ц.в.д. умеренной мощности.  Коробка вместе с сопловым сегментом заводится в крышку корпуса сверху в радиальном направлении и крепится к крышке турбины плоским фланцем 1 при помощи болтов (фиг.11,а) или сваркой (фиг.11,б,в). Сопловые коробки (фиг.11а) удобны тем, что их можно вынуть, не снимая крышки корпуса турбины. Они просты по конструкции, удобно монтируются и имеют возможность беспрепятственно расширяться. Для фланцевого соединения сопловых коробок на корпусе предусматриваются приливы или патрубки. В последние годы широко практикуется приварка сопловых коробок к корпусу. При этом на корпусе нет фланцев, приливов, патрубков (фиг.11,12) и тому подобных местных скоплений металла. Стенки корпуса сохраняют примерно одинаковую толщину по всей окружности паровпускного пояса. В стационарной турбине ЛМЗ (фиг.12) имеются 4 вставные небольшие коробки; они литые приварные. Помимо сварного шва имеются направляющие выступы А-А, которыми каждая коробка опирается на корпус и скользит относительно его. К сопловым коробкам приварен корпусов клапанов. Как видно, рациональное размещение и крепление сваркой нескольких небольших сопловых коробок позволяет обеспечить симметричное температурное поле в паровпускном поясе турбины и избежать местных скоплений металла. Такое размещение и крепление сопловых коробок ценно для турбин, рассчитанных на быстрый пуск без прогрева или с кратковременным прогревом. На фиг.13 показан поперечный разрез турбины К-150-170 (СВК-150) ЛМЗ с двустенным корпусом по регулирующим клапанам и сопловым сегментам. К обойме внутреннего корпуса присоединены литые сопловые коробки с помощью сварки. Центровка их в вертикальной плоскости осуществляется шпонками 1. Патрубки, подводящие пар от сопловых клапанов, свободно входят в приёмные втулки сопловых коробок, уплотняясь поршневыми кольцами. V. СОПЛОВЫЕ АППАРАТЫ  Сопловой аппарат служит для преобразования потенциальной энергии пара в кинетическую, и направления потока пара на рабочие лопатки. Сопловой аппарат, обычно, состоит из нескольких сегментов сопел, к каждому из которых пар поступает из отдельного клапана. Сегменты могут быть сборные и цельные. Сборные сегменты могут набираться из отдельных индивидуальных сопел или из двух обойм и набора цельнофрезерных сопловых перегородок. Примеры конструкций сборных сегментов из отдельных индивидуальных сопел представлены на фиг.14.  Такие сопла делают из прямоугольных брусков небольшой длины. Сопла 3 заводятся выступом 2 в канавку корпуса 1 и закрепляются накладкой 4, которая крепится к корпусу винтами 6. Последние стопорятся шайбами 5. Для плотности зажатия сопел накладка 4 опирается на выступ 7, который обеспечивает плотность зажатия всех сопел. Между отдельными сопловыми сегментами вставляются проставки. При сборных сопловых сегментах и наборных индивидуальных соплах, независимо от их конструкции, невозможно избежать просачивания пара через неплотности между отдельными деталями. В связи с этим более совершенными являются цельные сопловые сегменты, где лопатки составляют одно целое с обоймами или, по крайней мере, с одной из них. К этим конструкциям относятся: литые, кованные, сварные, паянные или комбинированные: сварнокованные и сварнолитые сегменты. Литые сегменты в настоящее время встречаются редко, т.к. внутренние поверхности каналов, обрабатываемые только вручную, получаются шероховатыми. В силу большой шероховатости стенок и искажения формы каналов потери в соплах больше, чем в индивидуально обработанных соплах. На фиг.15 показан сварнокованнный сегмент. Сегмент состоит из лопаточного аппарата 1 (в котором лопатки фрезерованы заодно с корпусом сегмента) и вставок 2 между лопатками. Деталь 1 показана в развёртке А-А. На кромках лопаток сняты фаски. Эти фаски необходимы для приварки вставок 2, как показано на фиг.15а. После приварки вставок каналы полностью перекрыты и на получившийся бандаж приваривают обод (фиг.15,б). Ограничивают сегмент приваренные проставки 3 и 5. По верхнему диаметру сегмента приварен козырёк 6. Сваренный сегмент подвергается термообработке (отпуску), после чего обрабатываются его наружные поверхности, показанные линиями на фиг.15,б в сечении Б-Б.  VI. ДИАФРАГМЫ Основное назначение диафрагмы – отделять одну ступень давления от другой. Диафрагмы несут на себе направляющий лопаточный аппарат. Лопаточные каналы диафрагм должны быть правильно рассчитаны и точно выполнены, т.к. от этого зависит направление струи пара, поступающего на рабочие лопатки, и величина потерь энергии в струе пара. Диафрагмы должны обеспечить непроницаемое разделение внутренней полости турбины, т.к. при перетекании пара из одной ступени в другую через неплотности, минуя лопатки, энергия пара на данной ступени не используется. Каждая диафрагма находится под действием разности давлений; величина статического парового усилия весьма значительна (фиг.17). Так, диафрагма с наружным диаметром 1000 мм и диаметром центрального отверстия 250 мм при разности давления в 1 кг/см² испытывает суммарную осевую нагрузку около 7,5 т. Кроме того, диафрагмы интенсивно омываются паром и, следовательно, расширяются быстрее корпуса (при пуске), а сжимаются медленнее (при остановке). Любая диафрагма (фиг.17), независимо от её конструкции, состоит из полотна 4, представляющего собой остов диафрагмы, сопловых лопаток 2, обода 1 и уплотнения 5, устанавливаемого в месте перехода вала через центральное отверстие диафрагмы. Диафрагма состоит из двух половин. Одна половина закрепляется в нижней, вторая в верхней половине корпуса. Диафрагмы вставляются непосредственно в расточки корпуса (фиг.17) или в специальные обоймы, закрепляемые в корпусе. В современных турбинах применяют диафрагмы: 1) литые, чугунные или стальные; 2) кованные; 3) сварные. Литые диафрагмы могут быть чугунными или стальными; кованные или сварные диафрагмы – только стальными. Литые диафрагмы, применяемые в основном в последних ступенях, где большие проходные сечения и шероховатость каналов не играет существенной роли, они менее прочны, чем остальные – ввиду склонности чугуна к росту при температуре 250-300°С. В настоящее время применяют чугунные диафрагмы с залитыми в них стальными лопатками. Применение стальных диафрагм диктуется в одних случаях прямой необходимостью (высокие температуры пара – свыше 300°С), в других – стремлением к облегчению диафрагм. 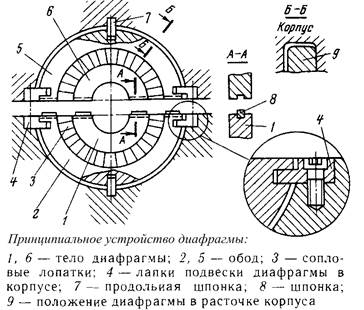 Из-за трудности отливки стальных диафрагм с залитыми перегородками, литые стальные диафрагмы обычно снабжаются сопловым аппаратом наборной конструкции. Наборные обработанные сопла, имеющие незначительную высоту лопаток, обеспечивают наиболее точную форму сопловых каналов. Крупный их недостаток – утечки в стыках сопел и большая трудоёмкость изготовления. Поэтому, в настоящее время, диафрагмы первых ступеней высокого давления изготавливают кованными с приваренными к ним сопловыми лопатками с широкими и узкими профилями (фиг.18). Такая конструкция диафрагм позволяет: 1) сохранить в процессе изготовления диафрагмы свойства металла лопаток и их поверхность; 2) выполнить сопловые каналы с гладкими стенками; 3) применять лопатки с заострёнными выходными кромками, что способствует более высокому КПД облопачивания; 4) обеспечить герметичность каждого соплового канала; 5) удешевить производство стальных диафрагм. В ц.н.д. турбины также могут применяться сварные диафрагмы. Однако в ряде случаев более дешёвыми оказываются чугунные диафрагмы с залитыми в них лопатками. На фиг.18а показана сварная диафрагма с узкими лопатками. С широкими лопатками – на фиг.18,б. В сварной диафрагме (фиг.18,б) лопатка 5 проходит через профильные отверстия, пробитые в бандажах 4 и 6, и приварена к последним. Затем лопаточный венец приваривается к телу 8 и ободу 3 диафрагмы. Козырёк 10 служит для радиального ограничения зазора рабочих лопаток и является элементом лабиринтового уплотнения. 

Диафрагма на рис.18а отличается от описанной выше конструкции тем, что сопловые лопатки сделаны небольшой ширины, что благоприятно сказывается на КПД решётки. Поэтому здесь тело диафрагмы изготовлено заодно с ободом, соединяясь профилированными стойками 7. |