Особливості основних видів термічної обробки Завдання 1. Ознайомитися з окремими структурними складаючими вуглецевих сталей ( фериту, перліту, цементиту) та їх властивостями. 2. Дослідити мікроструктури заданих зразків за допомогою мікроскопу. 3. Намалювати схеми мікроструктур доевтектоїдних, евтектоїдної та заевтектоїдних сталей з різною кількістю вуглецю, позначити назви структур, надати приклади марок сталей та їх використання. Прилади, матеріали і інструмент: - металографічний мікроскоп (МІМ - 7); - зразки мікрошліфів вуглецевих сталей; - альбом фотокарток мікроструктур. Хід роботи Зображення мікроструктури | Позначення мікроструктур | Назва чавуну, його марки, використання | | | | | | | | | | | | | | | | Висновки: Лабораторна робота № 5а Тема:Мікроаналіз чавунів Мета: Вивчити структури сірих, високоміцних, ковких і білих чавунів. Встановити особливості структурної будови різних видів чавунів. Завдання: 1. Ознайомитися з будовою і властивостями структур чавунів (цементиту, перлиту, ледебуриту, фериту та різних форм графіту). 2. Дослідити мікроструктури зразків чавунів за допомогою мікроскопу. 3. Намалювати схеми мікроструктур чавунів; позначити назви структур, надати приклади марок чавунів та їх використання. Обладнання і матеріали: - металографічний мікроскоп (МІМ - 7); - зразки мікрошліфів чавунів; - альбом фотокарток мікроструктур. Хід роботи Зображення мікроструктури | Позначення мікроструктур | Назва сталі, склад вуглецю, марки, використання | | | | | | | | | | | | | | | | Висновки: Лабораторна робота № 7 Тема:Вивчення термічної обробки вуглецевих сталей Мета:Навчитися призначати режими термічної обробки вуглецевих сталей Завдання: 1. Засвоїти технологію проведення основних видів термічної обробки вуглецевих сталей і дослідити вплив термічної обробки на їх структуру властивості. Обладнання і матеріали:Довідкові таблиці режимів термічної обробки, зразки деталей, які підлягають ТО. Методичні рекомендації Термічна обробка – це технологічна операція, яка складається з нагрівання металевого матеріалу до заданої температури, витримки його при цій температурі і наступного охолодження з метою формування в металевому виробі певної структури, яка б забезпечила йому потрібні властивості. Режим термічної обробки найчастіше визначається температурою нагрівання (Тн),часом витримування при цій температурі (τв) і часом (τох) або швидкістю охолодження (Vох). Температурно-часовий режим термічної обробки може бути зображений графічно в координатах “температура – час” (рис. 31). Для визначення режиму термічної обробки вуглецевих сталей користуються лівим нижнім кутом діаграми залізо-цементит, який зветься сталевим кутом (рис. 32). На цьому куті температуру перлітного перетворення (лінія PSK) позначають А1, температуру лінії GS - А3, температуру лінії SE – Аcm. (Фазові перетворення при температурах, відповідних лініям GS і SE, дивись у лабораторній роботі № 3). Температуру А1 позначають Ас1, якщо описують процес нагрівання при термічній обробці, і Аr1, якщо йдеться про процес охолодження. Аналогічно температуру А3 позначають Ас3 і Аr3. Основні види термічної обробки: · відпал · нормалізація · гартування · відпуск Відпал – це термічна обробка, яка складається з нагрівання до визначеної температури, наступної витримки та повільного охолодження (як правило – в печі) з метою отримання рівноважних структур. Розрізняють такі основні види відпалу: · дифузійний (гомогенізуючий) · рекристалізаційний · повний · неповний · ізотермічний  Рисунок 31 Графік повного гартування з наступним середнім відпуском.  Рисунок 32 Сталевий кут діаграми залізо – цементит. Дифузійний відпал застосовують для усунення дендритної ліквації (хімічної неоднорідності), утвореної при кристалізації металу, оскільки така хімічна неоднорідність призводить до неоднорідності властивостей металевого виробу на його дільницях з різним хімічним складом. Цей відпал застосовують для виливків з високолегованих сталей, схильних до ліквації. Його проводять при температурах 1050-12000С з витримкою протягом тривалого часу (10- 20 год), що забезпечує вирівнювання хімічного складу сталі за рахунок дифузії хімічних елементів. Однак при цьому утворюється небажана крупнозерниста структура, що знижує властивості металу. Тому для формування дрібнозернистої структури після дифузійного відпалу звичайно проводять відпал на дрібне зерно (повний відпал, нормалізація тощо). Рекристалізаційний відпал застосовують для відновлення пластичності металевого виробу, втраченої внаслідок його холодної пластичної деформації. Під час пластичної деформації відбувається так званий наклеп металу, який являє собою підвищення міцності та зниження пластичністі за рахунок підвищення кількості дефектів кристалічної будови (дислокацій) у металі. Зерна набувають витягнутої форми. При наступному нагріванні деформованого металу вище так званої температури рекристалізації відбуваються рекристалізаційні процеси. Вони полягають у зародженні в деформованих витягнутих зернах нових зерен округлої форми з меншою кількістю дефектів кристалічної будови, ці нові зерна зростають і замінюють собою старі зерна. Внаслідок рекристалізаційного відпалу знімається наклеп і відновлюється пластичність металу, його можна продовжити деформувати. Дифузійний і рекристалізаційний відпал називають відпалом І-го роду. Фазові перетворення під час відпалу І-го роду не відіграють істотної ролі, як у випадку дифузійного відпалу, або не відбуваються взагалі, як під час рекристалізаційного відпалу. Відпал ІІ-го роду – це відпал з фазовою перекристалізацією, тобто при якому фазові перетворення відіграють провідну роль. До відпалу ІІ роду відносяться повний, ізотермічний та неповний відпал. Повний відпал застосовують для доевтектоїдних сталей з метою подрібнення зерна, усунення внутрішніх напружень, підвищення пластичності. Він складається з нагрівання на 30-500С вище Ас3, витримки при цій температурі до повного перетворення структури на аустенітну і повільного охолодження разом з піччю. При повільному охолодженні, згідно діаграмі залізо-цементит (див. рис. 28), спочатку в інтервалі температур Аr3-Аr1 частина аустеніту перетворюється на ферит, а при температурі Аr1 відбувається перлітне перетворення (перетворення залишків аустеніту на перліт). Таким чином формується дрібнозерниста ферито-перлітна структура (див. рис. 30, а; 25, б, в). Ізотермічний відпал є різновидом повного відпалу. При ізотермічному відпалі виріб нагрівають, як і при повному, на 30-500С вище Ас3, витримують до повного перетворення структури на аустенітну, але потім його швидко охолоджують трохи нижче Аr1 (~6500С) (переносять в іншу піч, або соляну ванну з температурою ~6500С) і витримують при цій температурі до завершення перетворення аустеніту на перліт, після чого продовжують охолодження на повітрі. В результаті скорочується тривалість охолодження порівняно із повним відпалом, а також формується більш однорідна ферито- перлітна структура, оскільки завдяки витримці при ~6500С температура встигає вирівнятися по всьому виробі та перлітне перетворення в усьому об’ємі металу відбувається при однаковому ступені переохолодження. Неповний відпал застосовують переважно для заевтектоїдних інструментальних сталей, його ще називають сфероїдизуючим відпалом. Він полягає в нагріванні сталі на 30-500С вище Ас1, витримці при цій температурі та повільному охолодженні до 620-6800С, а потім на повітрі. Після нагрівання вище Ас1 і витримці при цій температурі в аустениті залишається велика кількість нерозчинених дрібних включень цементиту (від цементитних пластин, які входили до складу перліта, і від сітки вторинного цементиту по границях зерен). На ці включення нашаровується цементит, що утворюється при розпаді аустеніту під час наступного повільного охолодження. Внаслідок такої обробки утворюється структура зернистого перліту (див. рис. 25, д), зникає сітка вторинного цементиту, яка погіршує подальшу обробку виробу. Якщо при одноразовому відпалі не відбувається повна сфероїдизація цементиту, то застосовують відпал за циклічним режимом, а саме кількаразово нагрівають сталь вище Ас1, витримують, охолоджують дещо нижче Аr1 (650-7000С), витримують при цій температурі й знову повторюють цей цикл. Сфероїдизуючий відпал проводять для поліпшення оброблюваності заевтектоїдних інструментальних сталей різанням і отримання досконалішої структури перед наступним гартуванням, оскільки частинки зернистого цементиту гальмують зріст аустенітних зерен при нагріванні під гартування, що забезпечує вищу міцність та в’язкість сталі після неповного гартування, якому звичайно піддають інструментальні сталі. Нормалізація полягає у нагріванні сталей на 30-500С вище температури Ас3 (для доевтектоїдних сталей) і Аcm (для заевтектоїдних сталей), витримуванні при цій температурі та охолодженні на повітрі, тобто з більшою швидкістю, ніж при відпалі. Внаслідок цього утворюється дрібнозерниста структура дісперснішого (ніж після відпалу) перліту, тобто з меншою товщиною пластин фериту і цементиту в ньому. Зменшується кількість фериту в доевтектоїдних сталях і усувається груба сітка вторинного цементиту в заевтектоїдних сталях. Нормалізація є більш економічною операцією, ніж відпал, бо потребує меншого часу перебування металу в термічній печі. Нормалізація і відпал частіше бувають первинними, або проміжними операціями термічної обробки, але можуть бути і завершальними. Гартування сталі поділяється на повне і неповне, залежно від температур, до яких нагрівають сталь під гартування. Повне гартування застосовують для доевтектоїдних сталей, а неповне – для заевтектоїдних. Для доевтектоїдних сталей температура нагрівання має бути на 30-500С вища за Ас3 (повне гартування). Нагрівання і витримка вище Ас3 забезпечує формування перед охолодженням чисто аустенітної структури без включень небажаного м’якого фериту. Заевтектоїдні сталі нагрівають і витримують при температурах на 30-500С вище за Ас1 (неповне гартування), що забезпечує формування аустеніту і зберігання в ньому частинок вторинного цементиту. Оскільки, як було сказано вище, перед гартуванням заевтектоїдні сталі звичайно піддають сфероїдизуючому відпалу, то вторинний цементит перебуває у вигляді сферичних включень і в такому вигляді зберігається при нагріванні та витримці више Ас1 під гартування. Він підвищує твердість загартованої сталі. Після витримки при вказаних температурах сталі швидко охолоджують зі швидкістю, більшою за так звану критичну швидкість гартування Vкр. Таку швидкість охолодження забезпечають такі охолоджувальні середовища як вода (~5000С/с), водні розчини солей (~11000С/с), лугів (~8000С/с), мінеральні оливи (~1000С/с). При цьому аустеніт переохолоджується до таких низьких температур, при яких дуже сповільнюється дифузія атомів вуглецю і заліза, внаслідок чого стає неможливим перетворення аустеніту на перліт, яке є саме дифузійним перетворенням. У той же час при таких низьких температурах відбувається поліморфне перетворення γ-Fe в α-Fe і весь вуглець, який був в аустеніті, в γ-Fe,переходить в α-Fe. Згадаємо, що при кімнатній температурі α-Fe здатне розчинити тільки 0,006 % С, а з аустеніту при гартуванні в нього може перейти до 0,8 % С. Так при гартуванні формується пересичений твердий розчин проникнення вуглецю в α-Fe, цей розчин називають мартенситом. Внаслідок великого вмісту вуглецю в мартенситі кубічна кристалічна решітка α-Fe стає тетрагональною. Окремі кристали мартенситу мають вигляд тонких пластин, які звужуються до кінців, тому на шліфі мартенсит має гольчасту будову (рис. 33, а, б). В разі значного перегрівання сталі під гартуванні (при цьому зерна аустеніту значно збільшуються у розмірах), при наступному охолодженні утворюється крупногольчастий мартенсит (рис. 33, а). Характерними властивостями загартованої сталі з мартенситною структурою є висока твердість (до 65 HRC), міцність, але мала пластичність (δ;ψ); ці сталі мають низьку в’язкість, тобто вони крихкі. Для поліпшення властивостей і зниження внутрішніх напружень всі сталі після гарту піддають відпуску. Відпуск полягає в нагріванні загартованих сталей до температур нижче Ас1, витримуванні при цих температурах для перетворення мартенситу в рівноважні структури та наступному охолодженні, звичайно на повітрі. Рисунок 33 Мікроструктура мартенситу гартування (а)крупногольчастого, (б) дрібногольчастого, (в) сорбіту відпуску | | Оскільки мартенсит є пересиченим твердим розчином вуглецю в α-Fe, то він є нестабільною фазою і при його нагріванні під час відпуску надлишковий вуглець виділяється з α-Fe у вигляді частинок цементиту. Ступінь його виділення залежить від температури нагрівання. Розрізняють три види відпуску: низький, середній і високий. Низький відпуск проводять з нагріванням до 150-2000С. При цій температурі тільки починають утворюватися ділянки з підвищеним вмістом вуглецю в мартенситі, вони є зародками цементиту. Таку структуру називають мартенситом відпуску, візуально вона практично не відрізняється від мартенситу гартування. Низький відпуск дещо знижує внутрішні напруження в сталі, твердість залишається високою (58-62 HRC). Його застосовують для різального і вимірювального інструменту, виробів після поверхневого гартування, цементації; нітроцементації. Середній відпуск проводять при 350-5000С після гартування пружин і ресор. Такий відпуск призводить до повного виділення вуглецю із твердого розчину у вигляді дуже дрібних (дрібнодисперсних) частинок цементиту Fe3C, а твердий розчин, який таким чином звільняється від надлишкового вуглецю, стає феритом. Тобто на цій стадії розпад мартенситу можна записати як Мартенсит → Ф + Ц Така структура називається трооститом відпуску. Сталь із такою структурою має високу пружність, твердість 40-50 HRC. Високий відпуск проводять при 550-6500С. При цих температурах йде коагуляція і сфероїдизація цементитних частинок. Коагуляція – це зріст одних частинок за рахунок розчинення інших, менших за розміром. Отриману після високого відпуску структуру називають сорбітом відпуску (рис. 33, в), вона забезпечує сталі високу ударну в’язкість, задовільну міцність і твердість близько 25-35 HRC. Гартування з наступним високим відпуском (відпуском на сорбіт) називають поліпшенням. Поліпшення застосовують для конструкційних сталей, з яких виготовляють деталі, що працюють в умовах значних динамічних і змінних навантажень. 7.3 Завдання 1 Засвоїти надані теоретичні відомості. 2 До таблиці 3 занести відомості про основні види термічної обробки сталей. Схематично замалювати прогнозовану структуру сталі після термічної обробки. 3 Замалювати сталевий кут діаграми залізо-цементит і для заданої сталі визначити температури певних видів термічної обробки: відпалу, нормалізації, гартування, відпусків (низького, середнього, високого). 4 Для зразка сталі 45 визначити температуру, тривалість нагрівання (приблизно 0,8 хв на 1мм перерізу зразка) і витримування (приблизно 0,2 хв на 1 мм перерізу зразка) у печі для гартування. 5 Провести нагрівання і витримування 4-х зразків у муфельній електропечі за визначеним часом, потім загартувати їх у воді, для чого необхідно кліщами швидко перенести кожний зразок з печі у воду і охолоджувати його, перемішуючи воду коловими рухами зразка. Швидкість охолодження у воді ~5000С/с. 6 Один загартований зразок залишити для досліджень, а для трьох інших провести низький, середній і високий відпуск, попередньо визначивши температури цих відпусків, тривалість нагрівання (приблизно 1 хв на 1 мм перерізу зразка) і тривалість витримування (приблизно 0,25 хв на 1 мм перерізу зразка). Охолодження зразків здійснити у воді. 7 Виготовити ікрошліфи із отриманих зразків сталі 45, дослідити іх мікроструктуру на мікроскопі МЕТАМ-1Р і визначити твердість за Роквелом. Результати занести до Таблиці 4. 8 Побудувати графік впливу температури відпуску сталі 45 на її твердість. Контрольні запитання 1Що таке термічна обробка? 2 Користуючись сталевим кутом діаграми залізо-цементит, поясніть, які фазові перетворення відбуваються у вуглецевих сталях при їх нагріванні чи охолодженні до критичних температур А1, А3 і Аcm. 3 Поясніть сутність кожного з розглянути видів термічної обробки сталей, з якою метою і для яких сталей їх застосовують. 4 Поясніть, чому для доевтектоїдних сталей застосовують повне гартування, а для заевтектоїдних неповне. 5 Що таке мартенсит, з якої фази і за яких умов він утворюється? 6 В чому полягає розпад мартенситу при відпуску, які фази утворюються? Таблиця 3 Особливості основних видів термічної обробки Вид термо-обробки | Темпера-тура нагрі-вання; 0С | Оходжув. середо-вище | Швид-кість охолод-ження | Схема структури | Структ. складові | Застосування | відпал повний | | | | | | | відпал неповний | | | | | | | нормалізація | | | | | | | гартування повне | | | | | | | гартування неповне | | | | | | | відпуск низький | | | | | | | відпуск середній | | | | | | | відпуск високий | | | | | | | Таблиця 4 Структура і твердість сталі 45 після гартування і відпуску Вид термічної обробки | Режим термічної обробки | Твердість, HRC | Схема структури | Структ. складові | Особливості структури | гартування | нагрівання до час нагр. і витр. охолодж. | |  | | Мартенсит має гольчасту будо-ву, сталь тверда і крихка | низький відпуск | нагрівання до час нагр. і витр. охолодж. | |  | | Мартенсит від-пуску, знято вну-трішні напруж. | середній відпуск | нагрівання до час нагр. і витр. охолодж. | | 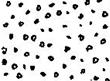 | | Троостит відпус-ку – дисперсні частинки цемен-титу у фериті | високий відпуск | нагрівання до час нагр. і витр. охолодж. | |  | | Сорбіт відпуску – цементитні ча-стинки збільши-лись у розмірі | Лабораторна робота № 7а Тема: Дослідження мікроструктури сталей після термічної обробки. Мета: Виявити вплив термічної обробки на структуру та властивості сталі. Завдання 1 .Ознайомитися а основними видами термічної обробки ( відпалювання, нормалізацією, гартуванням, відпусканням). 2. Розглянути мікро шліфи з різною термічною обробкою. 3. Замалювати схематичне зображення структурних перетворень, які відбуваються при гартуванні доєвтектоїдаих та заевтектоїдних сталей. 4.3амалювати мікроструктури сталі марки Сталь 45 після відпалювання, нормалізації, гартування. 5.Описати вплив термічної обробки на структуру та властивості сталі. Обладнання і матеріали: - металографічний мікроскоп ( МІМ-7 ); - набір мікрошліфів вуглецевих сталей; - альбом фотокарток мікрошліфів; Методичні рекомендації Метою термічної обробки є отримання завданих властивостей сплаву шляхом зміни його структури. При відпалюванністалі нагріваються вище фазових перетворень, витримуються деякий час і повільно охолоджуються ( як правило разом з піччю). Швидкість охолодження при відпалюванні повинна забезпечити перетворення аустеніту в ферито-цементитну суміш ( для легованих сталей -30-100 град / год; для вуглецевих - 150-200 град / год.) Після відпалювання отримують структури які відповідають діаграмі стану "залізо -цементит", так: - для доєвтектоїдаих сталей - перліт і ферит - для евтектоїдної сталі - перліт; - для заевтектоїдних сталей - перліт і цементит вторинний. , При нормалізаціїсталь охолоджується з більшою швидкістю, чим при відпалюванні (на повітрі ). При цьому утворюється дрібніша структура, ніж при відпалюванні, так: - для низьковуглецевих сталей - ферит і перліт - для середаьо-та високовуглецевих - сорбіт; Твердість і міцність при нормалізації вище ніж при відпалюванні. При гартуванністалі нагрівають до температур : - доевтектоїдні - Асз + ( 30 - 50 )°С; - заевтектоїдаі - Асі +'( 30 - 50 )°С. Охолодження відбувається зі швидкістю більше критичної ( 15.0 -200 град /сек ), яка забезпечує перетворення аустеніту в мартенсит. Мета гартування - отримання найбільшої твердості та міцності. При повному гартуванні доевтектоїдної сталі ( див. схему № 1а) вона нагрівається до температури, яка забезпечує отримання однорідного аустеніту. А при швидкому охолодженні - утворення структури мартенситу При неповному гартуванні доевтектоїдної сталі ( нагрів між Асі і Асз) структура сталі буде складатися з аустеніту та фериту ( див. схему № 1). При наступному охолоджені аустеніт перейде в мартенсит, а ферит залишиться без змін. Залишковий ферит знижує твердість сталі Схема № 1 Структурні перетворення в доєвтектоїдаих сталях при гартуванні.  Заевтектоїдаі сталі при гартуванні нагрівають до температури Асі + ( 30-50 )°С. Структура заевтектоїдної сталі після гартування буде складатися з мартенситу, цементиту вторинного та підвищеної кількості залишкового аустеніту. Цементит вторинний у заевтектоїдних сталях після гартування має велику твердість , а тому не зменшує твердість загартованої сталі (схема № 2а). При гартуванні заевтектоїдної сталі з нагрівом вище. Аст в структурі загартованої сталі буде присутній крупногольчатий мартенсит з підвищеною кількістю залишкового аустеніту (схема №2б). Наявність великої кількості залишкового аустеніту приводить до зниження твердості; наявність крупних зерен приводить до зниження ударної в'язкості і до збільшення внутрішніх напружень. Схема № 2.  Структурних перетворень в заевтектоїдних сталях при гартуванні. Лабораторна робота № 8 Тема: Мікроаналіз сплавів кольорових металів Мета: Вивчити структури міді, латуні, бронзи, сплавів алюмінію, магнію, антифрикційних сплавів. Завдання 1. Ознайомитися з окремими структурними складовими кольорових металів та сплавів. 2. Дослідити мікроструктури заданих зразків за допомогою мікроскопу. 3. Намалювати схеми мікроструктур кольорових металів та сплавів. Позначити назви структур, надати приклади марок сплавів та їх використання. Обладнання і матеріали: - металографічний мікроскоп (МІМ - 7); - зразки мікрошліфів кольорових металів та сплавів; альбом фотокарток мікроструктур. Хід роботи Зображення мікроструктури | Позначення мікроструктур | Назва сплаву, марки, використання | | | | | | | | | | | | | | | | Висновки: Лабораторна робота № 9 
Тема:Вимірювання основних кутів ріжучих інструментів. Мета: Навчитися самостійно, проводити вимірювання основних кутів інструменту Завдання 1. Ознайомитися з методичними вказівками. 2. Замалювати ескіз ріжучого інструменту з геометрією основних площин і кутів. 3. Заміряти основні кути інструменту, а ті кути, які не можна заміряти – визначити розрахунком. 4. Записати значення отриманих кутів. 5. Зробити висновки стосовно придатності інструменту. Обладнання і матеріали: - кутомір універсальний; - кутомір оптичний; - токарні різці. Методичні вказівки Вимірювання кутів проводять одновимірними або універсальними інструментами. До одновимірних інструментів відносяться: кутові плитки, кутові ухили, косинці, конічні калібрі – пробки. До універсальних інструментів відносяться кутоміри, конусні лінійки і ін. Ріжучі властивості різця значною мірою залежать від кутів його заточування або, як прийнято говорити, від «геометрії» різця. Головні кути Якщо провести головну січну площину N – N перпендикулярно до проекції головної ріжучої кромки на основну площину, то можливо розглянути наступні кути: ά – головний задній кут, утворюється між площиною різання і головною задньою поверхнею (6 – 150); γ – головний передній кут, утворений площиною, перпендикулярної площини різання і передньою поверхнею (-10 до +200); β – кут загострення, утворюється між передньою і головною задньою поверхнею; δ – кут різання, утворюється площиною різання і передньою поверхнею. Між головними кутами різця можуть бути такі співвідношення: ά + β + γ = 900; ά + β = δ; δ + γ = 900 Допоміжні кути Вони виходять при перетині допоміжною січною площиною N1 – N1 допоміжної ріжучої кромки. ά1 – допоміжний задній кут, утворюється між допоміжною задньою поверхнею та площиною, що проходить через допоміжну ріжучу кромку перпендикулярно основній площині (8 – 100); γ1 – допоміжний передній кут, утворюється між площиною, перпендикулярної площині різання і передньою поверхнею.  Кути в плані Вони вимірюються в основній площині. φ – головний кут в плані (30 – 900); φ1 – допоміжний кут в плані (10 – 150); ε – кут при вершині, ε = 1800 – (φ + φ1).  Рисунок 34 Геометричні параметри різця Головні кути | Допоміжні кути | Кути в плані | ά | γ | β | δ | ά1 | γ1 | φ | φ1 | ε | | | | | | | | | | Висновки: |