ПОЗНАВАТЕЛЬНОЕ Сила воли ведет к действию, а позитивные действия формируют позитивное отношение Как определить диапазон голоса - ваш вокал
Игровые автоматы с быстрым выводом Как цель узнает о ваших желаниях прежде, чем вы начнете действовать. Как компании прогнозируют привычки и манипулируют ими Целительная привычка Как самому избавиться от обидчивости Противоречивые взгляды на качества, присущие мужчинам Тренинг уверенности в себе Вкуснейший "Салат из свеклы с чесноком" Натюрморт и его изобразительные возможности Применение, как принимать мумие? Мумие для волос, лица, при переломах, при кровотечении и т.д. Как научиться брать на себя ответственность Зачем нужны границы в отношениях с детьми? Световозвращающие элементы на детской одежде Как победить свой возраст? Восемь уникальных способов, которые помогут достичь долголетия Как слышать голос Бога Классификация ожирения по ИМТ (ВОЗ) Глава 3. Завет мужчины с женщиной 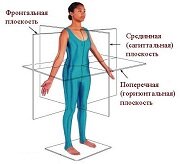
Оси и плоскости тела человека - Тело человека состоит из определенных топографических частей и участков, в которых расположены органы, мышцы, сосуды, нервы и т.д. Отёска стен и прирубка косяков - Когда на доме не достаёт окон и дверей, красивое высокое крыльцо ещё только в воображении, приходится подниматься с улицы в дом по трапу. Дифференциальные уравнения второго порядка (модель рынка с прогнозируемыми ценами) - В простых моделях рынка спрос и предложение обычно полагают зависящими только от текущей цены на товар. | Лабораторна робота 3, 4. ТЕРМІЧНА ОБРОБКА ВУГЛЕЦЕВИХ СТАЛЕЙ. Мета роботи — вивчити вплив термічної обробки на механічні властивості сталей; набути навичок проведення операцій термічної обробки: нормалізації, гартування та відпускання вуглецевих сталей. Завдання:1) ознайомитись з будовою печі і приладом для вимірювання температури; 2) виміряти твердість зразків конструкційної та інструментальної сталей; 3) призначити режими проведення нормалізації, гартування та відпуску; 4) провести гартування, нормалізацію та відпуск різних марок вуглецевої сталі; 5) охарактеризувати структури, які одержані в зразках після кожного виду термічної обробки, вказуючи на діаграмі сплавів залізо — цементит; виміряти твердість після термічної обробки; 6) написати звіт про виконану роботу. Обладнання і матеріали: електропечі для нагрівання; зразки вуглецевої сталі різних марок; прилади для вимірювання твердості твердоміри Брінеля та Роквелла; полірувально - шліфувальна установка; реактиви для травлення і паста „ГОИ"; кліщі. Студент повинен знати: - види термічної обробки сталей; - вплив термічної обробки на властивості сталі; - методику проведення різних видів термічної обробки. Студент повинен уміти: - призначати режими термічної обробки сталей; - проводити термічну обробку вуглецевих сталей. МЕТОДИЧНІ ВКАЗІВКИ Термічна обробка полягає в нагріванні деталі до певних температур, витримці при цій температурі та охолодженні з різними швидкостями. При цьому відбуваються зміни структури, механічних і технологічних властивостей виробу. При нагріванні і охолодженні в залізовуглецевих сплавах відбувається перетворення за певних температур, які називаються критичними точками. При нагріванні їх прийнято умовно позначати А с1, Ас2, Ас3 (рис. 4.1). Перетворення в сталях при нагріванні носять кристалізаційний характер, тобто при цьому відбувається утворення центрів зародків і послідовний їх ріст. Вихідна структура всіх сталей перліт суміш фериту та цементиту. При повільному нагріванні до температури А с1(723°С) ніяких перетворень в сталі не відбувається. При досягненні критичної точки А с1 перліт переходить в аустеніт. При подальшому нагріванні в доевтектоїдних сталях відбувається поступове розчинення фериту в аустеніті. При температурі вищій Ас3 сталі будуть мати однорідну структуру — аустеніт. При повільному охолодженні евтектоїдної сталі аустеніт перетворюється в перліт (суміш фериту і цементиту). Перетворення аустеніту в перліт відбувається дифузійно, вуглець, виділяючись з аустеніту, утворює зародки цементитних включень, кількість яких і послідовний ріст залежать від ступеня переохолодження. Регулюючи ступінь охолодження аустеніту, можна одержати наступні продукти його розпаду: перліт — крупнозернисту суміш фериту і цементиту; тростит — дрібнозернисту (високодисперсну) суміш фериту та цементиту. При великих ступенях переохолодження аустеніту дифузійний перерозподіл вуглецю практично припиняється і утворення цементиту стає неможливим. Утворюється структура мартенсит — перенасичений твердий розчин вуглецю в Feα Найменша швидкість охолодження, при якій аустеніт перетворюється в мартенсит, називається критичною швидкістю гартування. Мартенсит має голчасту будову і високу твердість (500-650НВ). Види термічної обробки сталі: 1) відпал першого роду чи рекристалізація; 2) відпал другого роду; 3) нормалізація; 4) гартування; 5) відпускання. Відпал першого роду (рекристалізаційний відпал) — нагрівання деталей до температури нижче фазових перетворень, витримка при цій температурі і повільне охолодження. Такий вид відпалу застосовують для зняття внутрішніх напруг у деталей, які одержані методом холодної деформації (холодне прокатування, холодне штампування, волочіння і таке інше), а також для зняття нагартування (наклепу) сталі – рекристалізаційний відпал. Температура рекристалізаційного відпалу для різних металів і сплавів неоднакова. Наприклад, для сталі температура рекристалізаційного відпалу на 150 — 200°С вища температури рекристалізації, за звичай 680 - 700°С, прицьму металу повертаються вихідні властивості, тобто знижується твердість, підвищується пластичність. Відпал другого роду (відпал з фазовими перетвореннями) — нагрівання сталі до температури ненабагато вище критичної, витримка при такій температурі і повільне охолодження разом з піччю. Мета відпалу — вирівняти хімічний склад деталі, одержати дрібнозернисту рівноважну структуру, зняти внутрішні напруги, підвищити пластичність, покращити умови оброблюваності різанням. Відпал другого роду поділяється на повний, неповний, ізотермічний, ступеневий, дифузійний. Повний відпал здійснюється шляхом нагрівання сталі на 30-50°С, вище критичної температури Ас3, витримки при цій температурі і повільному охолодженні. Повному відпалу піддають і гарячедеформовані сталі (поковки, штамповки, прокат, а також зливки і фасонні виливки із вуглецевої і легованої сталі). Неповний відпал здійснюють, нагріваючи деталі до температури вище критичної точки Ас1 на 30-50°С, витримки при цій температурі і наступного повільного охолодження. Неповний відпал потрібен для перекристалізації перліту, зняття внутрішніх напруг, покращення оброблюваності різанням. Застосовується для заевтектоїдних сталей. Нормалізація - проміжний процес термічної обробки між відпалом і гартуванням. Залежно від хімічного складу сталі нормалізацію застосовують іноді замість відпалу чи гартування. Нормалізація відрізняється від відпалу підвищеною швидкістю охолодження (на стійкому чи рухомому повітрі). Процес нормалізації полягає в нагріванні сталі вище критичних температур Ас3, Асm на 30-50 °С(рис.4.1,а) витримці при цій температурі і охолодження на повітрі. Температурний інтервал нормалізації визначають за співвідношенням: Тнорм=Ас3(Асcm)+30…50°С, (4.1) Нормалізацією досягають подрібнення зерна та однорідності структури, усунення внутрішніх напруг і знищення сітки вторинного цементиту в заевтектоїдних сталях. Нормалізації піддають фасонні виливки, поковки, штамповки і прокатні матеріали.  а б Рис. 4.1. Оптимальний температурний інтервал: а-нармалізації; б-гартування Гартування — це процес, який полягає в нагріванні вище критичних температур Ас3, Ас1 на 30-50°С (рис. 4.1.,б), витримці при цій температурі і наступному швидкому охолодженні в воді, маслі чи інших охолоджувальних середовищах. Температурний інтервал гартування визначають за співвідношенням: Тгарт=Ас3(Ас1)+30…50°С, (4.2) Основна мета гартування - висока твердість та міцність виробів. Різке підвищення твердості і міцності при гартуванні відбувається за рахунок зміни структури в процесі нагрівання та охолодження, внаслідок утворення не рівноважних твердих структур — мартенситу, трооститу, сорбіту. Температура нагрівання під гартування залежить від хімічного складу сталі. Доевтектоїдну вуглецеву сталь нагрівають вище критичної температури Ас3 на 30-50°С, а заевтектоїдну та евтектоїдну сталі вище Ас1 на 30-50°С. Температура під гартування доевтектоїдної сталі змінюється із зміною в сталі вуглецю, температура нагрівання заевтектоїдних сталей постійна і дорівнює 770-780°С. Нагрівання деталей повинно бути повільним, щоб не виникали внутрішні напруження і тріщини. Тривалість нагрівання залежить від хімічного складу сталі, від форми та розмірів деталі. Витримка повинна бути достатньою, щоб ввесь процес перетворення ферито-цементитної суміші повністю відбувся. Тривалість витримки, за звичай, становить 25% загального часу нагрівання. Швидкість охолодження повинна бути такою, щоб забезпечити одержання потрібної структури—мартенситу, трооститу, cорбіту, тобто забезпечити необхідні механічні властивості деталі, що обробляється. Для успішного проведення термічної обробки правильний вибір охолоджувального середовища має велике значення. Гартування середньовуглецевих сталей здійснюють у воді при температурі 18°С, а більшість інших сталей в маслі. Об'ємне гартування залежно від способу охолодження поділяється на декілька видів. Гартування в одному охолоджувачі вуглецевих сталей(охолодження в воді) і легованих сталей (охолодження сталей в маслі) полягає втому, що нагріту до температури гартування деталей занурюють в гартувальне середовище і тримають її до повного охолодження. Недолік цього способу — виникнення значних термічних напруг із — за різкої різниці температур нагрітого металу і охолоджувального середовища. Ступінчасте гартування здійснюють швидким охолодженням послідовно в двох різних охолоджувальних середовищах. Першим охолоджувальним середовищем служать розплавлені солі чи масло з температурою на 20-30°С вище точки початку мартенситногоперетворення Мн для даної сталі. В гарячому середовищі деталям надають короткочасну витримку, мета витримки — вирівнювання температур за перерізом деталі. Структура металу — аустеніт. Другим охолоджувальним середовищем є повітря; при цьому аустеніт переходить в мартенсит. 2 9 Перевагою такого методу гартування є зменшення термічних напружень, а отже, неможливість появи тріщин, у ведення і жолобкування, а також оптимальне поєднання високої в'язкості з міцністю. Ступінчасте гартування застосовують для дрібних металів з вуглецевої сталі перерізом 8-10мм і для деталей із легованої сталі перерізом до 30 мм. Ізотермічне гартування, так як і ступеневе гартування, здійснюється в двох охолоджувальних середовищах. Температура гарячого середовища (соляні, селітрові і лужні ванни) залежать від хімічного складу сталі. Час витримки повинен бути достатній для повного перетворення аустеніту в голчастий троостит. Завершальне охолодження до кімнатної температури здійснюється на повітрі. Ізотермічне гартування широко застосовують для деталей із високолегованих сталей. Після ізотермічного гартування сталь набуває високих міцносних властивостей. Поверхневе гартування застосовуються для надання відповідальним деталям (валам, зубчастим колесам і таке інше), що працюють на тертя і одночасно піддаються дії ударних навантажень, твердості поверхневого шару, високого опору зносу і в'язкості серцевини, що забезпечує опір удару. Залежно від способу нагрівання деталей поверхневе гартування деталей поділяється на індукційне (струмами високої частоти), контактне, газополуменеве, гартування в електроліті. Індукційне гартування полягає в тому, що електричний струм високої частоти, проходячи по провіднику — індуктора, створює навколо нього електричне поле (електромагнітне). На поверхні деталі, яка поміщена в цьому колі індуціюються вихрові струми, що спричиняють нагрівання деталей до високих температур. Це забезпечує можливість протікання фазових перетворень, тобто перетворення ферито-цементитної структури в аустеніт. Після охолодження поверхня деталі має структуру мартенситу. Відпускання — це завершальна операція термічної обробки, яка формує структуру, а отже, і властивості сталі. Призначення відпуску — зняти внутрішні напруги, що виникли в процесі гартування і одержати необхідну структуру. Процес відпускання полягає в нагріванні сталі до температур нижче точки Ас1 витримці при цій температурі та охолодженні. В залежності від температури нагрівання загартованої сталі розрізняють три види відпускання: низьке, середнє, високе. Низьке відпускання проводиться при температурі 150-250°С з метою зменшення гартувальних напруг при збереженні мартенситної структури. Твердість деталі після низького відпуску майже не змінюється. Низьке відпускання застосовується для вуглецевих сталей, для яких необхідна висока твердість і знoсостійкість. Середнє відпускання проводиться при температурі нагрівання 350-500°С і застосовується для пружинних і ресорних сталей, а також для сталей, що призначенні для виготовлення штампів. Високе відпускання здійснюється при температурах нагрівання 500-600°С і застосовується для конструкційних сталей машинобудівного призначення. Нагрівання зразків сталі для термообробки в лабораторних умовах проводять в муфельних електричних печах (рис. 4.2), які складаються із металевого корпусу 1,всередині якого викладений муфель 2 із чотирьох плит з вмонтованими в них нагрівальними спіралями 3. Робоча камера зачиняється дверцятами 4. Регулювання температури в печі здійснюється за допомогою ручки 5, а для вимірювання температури застосовуються Рис. 4.2. Муфельна електропіч термоелектричні пірометри-термопари, які вставляють в отвори печі задньої стінки. Піч перед початком роботи добре прогрівають, для чого її витримують на протягом трьох годин за температури 700°С. ПОРЯДОК ВИКОНАННЯ РОБОТИ Після ознайомлення з метою роботи, завданням і після уважного вивчення теоретичних основ різних видів термічної обробки та правил техніки безпеки необхідно призначити режим термічної обробки заданих сталей за діаграмою залізо — цементит , зокрема визначити температуру нагрівання для нормалізації, гартування та відпускання, встановити тривалість витримки, підібрати охолоджувальне середовище. Попередньо слід виміряти твердість зразків на твердомірах Брінеля чи Роквелла, корегуючи її за стандартними даними . Провести нагрівання, витримку і охолодження відповідно до призначених режимів для нормалізації, гартування і відпускання. Виміряти твердість зразків після термічної обробки. Всі дані занести до (відповідного) протоколу. Протокол №1 Нормалізація сталі № зразка | Марка сталі | Твердість до обробки НВ, кг/мм2 | Нормалізація | Структура | Механічні властивості | Температура нагрівання Т,ºС | Тривалість витримки t , с | Охолоджу- вальне середовище | Твердість після обробки НВ, кг/мм2 | σмц , МПа | δ, % | 1 | 2 | 3 | 4 | 5 | 6 | 7 | 8 | 9 | 10 | | | | | | | | | | | | | | | | | | | | | | | | | | | | | | | Протокол №2 Гартування і відпускання вуглецевих сталей № зразка | Марка сталі | Твердість до обробки НВ, кг/мм2 | Гартування | Відпускання | Температура нагрівання Т,ºС | Охолоджувальне середовище | Структура | Вид відпускання | Температура нагрівання Т,ºС | Охолоджувальне середовище | Структура | Твердість після обробки НRС | 1 | 2 | 3 | 4 | 5 | 6 | 7 | 8 | 9 | 10 | 11 | | | | | | | | | | | | | | | | | | | | | | | | | | | | | | | | | | . ЗМІСТ ЗВІТУ В звіті потрібно вказати мету роботи, обладнання інструменти і матеріали; описати послідовність призначення режиму термічної обробки заданих сталей і навести відповідні розрахунки та графічні зображення згідно пунктів ходу виконання роботи; навести і заповнити таблиці протоколів; зробити висновки про результати роботи ХІД РОБОТИ 1. Згідно варіанту індивідуального завдання виписати і розшифрувати марки сталей для проведення нормалізації (табл. 4.6). 2. Визначити твердість заданих сталей на приладі Брінеля і відкоригувати за стандартними даними ГОСТ 1050-74. 3. Визначити температурний інтервал нормалізації за співвідношенням (4.1). 3.1.Навести діаграму стану Fе-FезС і вказати на ній температурний інтервал нормалізації. 4. Визначити тривалість витримки сталей при заданій температурі (табл.4.5. ). 4.1. Вказати охолоджувальне середовище при нормалізації. 5. Провести нормалізацію заданих сталей. 5.1. Описати будову і призначення муфельної електричної печі (рис. 4.2). 5.2. Описати структуру заданих сталей після нормалізації. 6. Визначити твердість нормалізованих сталей на приладі Брінеля і відкоригувати за стандартними даними(табл. 4.2). 7. Результати термообробки та розрахунків занести до таблиці протоколу 1. 8. Виписати і розшифрувати марки сталей для проведення гартування і відпускання (табл. 4.6). 9. Визначити твердість заданих сталей на приладі Брінеля і відкоригувати за стандартними даними ГОСТ 1050-74(табл. 4.1, 4.3, ). 10. Визначити температурний інтервал нормалізації за співвідношенням (4.1). 10.1. Навести діаграму стану Fе-FезС і вказати на ній температурний інтервал гартування. 11. Підібрати охолоджувальне середовище для гартування заданих сталей. 12. Провести гартування заданих сталей. 12.1. Описати структуру заданих сталей після гартування. 13. Провести відпускання загартованих сталей. 13.1. Визначити температурний інтервал залежно від виду відпускання. 13.2. Підібрати охолоджувальне середовище для відпускання заданих сталей. 13.3. Описати структуру заданих сталей після відпускання. 13.4. Вказати температурний інтервал відпускання на діаграмі /див. п.10.1/. 14. Визначити твердість сталей після термообробки на приладі Роквелла і відкоригувати за стандартними даними (табл. 4.3, 4.4). 15. Результати термообробки та розрахунків занести до таблиці протоколу 2. 16. Зробити висновок про результати роботи. 17. Дати відповіді на контрольні питання. ДОДАТКИ Таблиця 4.1. Механічні властивості конструкційної вуглецевої якісної гарячекатаної сталі (ГОСТ 1050-74) Марка сталі | Вміст вуглецю С, % | Механічні властивості в нормалізованому стані | Твердість до обробки НВ, кг/мм2 | Ударна в’язкість aн, кГ∙м/см2 | Границя міцності σмц, кг/мм2 | σт, кг/мм2 | δ, % | Ψ, % | Відпаленої сталі | Гарячекатаної сталі | не менше | не більше | 1 | 2 | 3 | 4 | 5 | 6 | 7 | 8 | 9 | сталь 05КП | <0,06 | - | - | - | - | - | | - | сталь 08КП | 0,05-0,11 | | | | | - | | - | сталь 10 | 0,07-0,14 | | | | | - | | - | сталь 15 | 0,12-0,19 | | | | | - | | - | сталь 20 | 0,17-0,24 | | | | | - | | - | сталь 25 | 0,22-0,30 | | | | | - | | | сталь 30 | 0,27-0,35 | | З0 | | | - | | | сталь 35 | 0,32-0,40 | | | | | - | | | сталь 40 | 0,37-0,45 | | | | | | | | сталь 45 | 0,42-0,50 | | | | | | | | сталь 50 | 0,47-0,55 | | | | | | | | сталь 55 | 0,52-0,60 | | | | | | | - | сталь 60 | 0,57-0,65 | | | | | | | - | сталь 65 | 0,62-0,70 | | | | | | | - | сталь 70 | 0,67-0,75 | | | | | | | - | сталь 75 | 0,72-0,80 | | | | | | | - | сталь 80 | 0,77-0,85 | | | | | | | - | сталь 85 | 0,82-0,90 | | | | | | | - | Таблиця 4.2. Властивості вуглецевої сталі в нормалізованому стані Марка сталі | Механічні властивості | Найменування напівфабрикату | σмц, МПа | δ, % | Ψ,,% | Твердість НВ, кг/мм2 | 1 | 2 | 3 | 4 | 5 | 6 | сталь10 | | | - | 76-118 | Прутки, труби, листи | сталь15 | | | - | 84-131 | Прутки, труби, листи | сталь20 | | | - | 93-147 | Труби, листи | сталь25 | | | | 121-170 | Поковки, прутки,труби | сталь30 | | | | 132-178 | Поковки, прутки,труби | сталь35 | | | | 143-187 | Поковки, прутки | сталь40 | | | | 156-208 | Поковки, прутки | сталь45 | | | | 170-229 | Поковки, прутки, труби | сталь50 | | | | 174-255 | Поковки, прутки | сталь55 | | | | 217-269 | Поковки, прутки | Таблиця 4.3. Орієнтовний режим термічної обробки і твердість інструментальної сталі. Марка сталі | Відпал | Гартування | Відпускання | Темпера-тура,0С | Твердість НВ, кг/мм2 | Темпера-тура,0С | Охолоджувальне середовище | Твердість НRС | Темпера-тура,0С | Твердість НRС | 1 | 2 | 3 | 4 | 5 | 6 | 7 | 8 | У7, У7А | 750-760 | 187-234 | 800-820 | Вода, масло | 61-63 | 200-250 | 56-58 | У8, У8А, У8Г, У8ГА | 750-760 | 187-241 | 780-800 | Вода, масло | 62-64 | 200-250 | 57-59 | У9, У9А | 750-760 | 192-263 | 760-780 | Вода, масло | 62-65 | 180-200 | 59-61 | У10 | 760-780 | 197-279 | 760-780 | Вода, масло | 62-66 | 180-200 | 60-62 | У11 | 760-780 | 203-286 | 760-780 | Вода, масло | 63-66 | 180-200 | 61-63 | У12 | 760-780 | 207-294 | 760-780 | Вода, масло | 64-66 | 160-180 | 62-64 | У13 | 760-780 | 217-302 | 760-780 | Вода, масло | 65-67 | 160-180 | 62-65 | | | | | | | | | | | | Таблиця 4.4. Орієнтовний режим термічної обробки і механічні властивості якісної конструкційної вуглецевої сталі Марка сталі | Температура нагрівання для гартування, нормалізації і повного відпалу, 0С | Охолоджу- вальне середовище | Температура відпускання , 0С | Твердість після гартування і відпускання НRС | 1 | 2 | 3 | 4 | 5 | сталь 35 | 840-880 | Вода | 300-400 400-500 500-600 | 50-41 41-31 31-23 | сталь 40 | 820-860 | Вода | 200-300 300-400 400-500 500-600 | 52-48 48-41 41-33 33-22 | сталь 45 | 810-840 | Вода | 200-300 300-400 400-500 500-600 600-700 | 54-50 50-41 41-33 33-24 24-15 | сталь 50 | 800-840 | Вода | 180-200 380-400 500-550 560-620 | 65-50 48-40 33-24 24-20 | сталь 50Г | 800-840 | Масло | 420-500 | 42-38 | сталь 55 | 790-830 | Вода | 560-620 | 28-26 | сталь 55Г | 790-830 | Масло | 420-500 | 44-42 | сталь 60 | 785-820 | Вода-масло | 400-500 550-620 | 40-35 24-18 | сталь60Г | 785-820 | Масло | 400-500 | 46-44 | сталь65 | 775-815 | Вода-масло | 550-620 | 28-22 | Продовження табл. 4.4. 1 | 2 | 3 | 4 | 5 | сталь65Г | 775-815 | Масло | 420-500 | 47-45 | сталь 70 | 770-810 | Вода-масло | 400-500 610-670 | 46-39 27-22 | сталь70Г | 770-810 | Масло | 420-500 | 48-46 | Таблиця 4.5. Норми нагрівання сталі (в хвилинах) при термічній обробці в лабораторних умовах електричними печами Температура нагрівання, 0С | Форма зразків | Температура нагрівання, 0С | Форма зразків | круг | квадрат | пластина | круг | квадрат | пластина | на 1 мм діаметра | на 2 мм товщини | на 1 мм діаметра | на 2 мм товщини | 1 | 2 | 3 | 4 | 1 | 2 | 3 | 4 | | 2,0 | 3,0 | 4,0 | | 1,0 | 1,5 | 2,0 | | 1,75 | 2,6 | 3,5 | | 0,8 | 1,2 | 1,6 | | 1,5 | 2,2 | 3,0 | | 0,6 | 0,8 | 1,2 | | 1,25 | 1,85 | 2,5 | | 0,4 | 0,6 | 0,8 | Таблиця 4.6. Індивідуальні завдання № варіанта | Нормалізація | Гартування і відпускання | Марки зразків гарячекатаних сталей | Форма і розміри зразків, мм | Марки зразків відпалених сталей | 1 | 2 | 3 | 4 | | сталь 10 сталь 20 сталь 30 | Круг 32 | сталь 40 сталь 50Г У9А | | сталь 15 сталь 25 сталь 35 | Квадрат 18×18×24 /довжина × ширина × товщина/ | сталь 65Г сталь 55 У11 | | сталь40 сталь 50 сталь 55 | Пластина30×20×16 /довжина × ширина × товщина/ | У10 сталь 60 сталь 60Г | | сталь25 сталь 45 сталь 55 | Круг 44 | сталь 70Г У12 сталь 50 | | сталь 30 сталь 40 сталь 50 | Пластина28×24×22 /довжина × ширина × товщина/ | сталь 45 сталь 55Г У13 | ПРАВИЛА ТЕХНІКИ БЕЗПЕКИ Кожен студент при роботі з електрообладнанням і хімічними реактивами зобов'язаний виконувати правила техніки безпеки, що встановлені інструкцією з охорони праці при виконанні робіт в кабінеті-лабораторії. Про проходження інструктажу з питань охорони праці та безпеки життє-діяльності слід розписатися у відповідному журналі реєстрації інструктажів. КОНТРОЛЬНІ ЗАПИТАННЯ ТА ЗАВДАННЯ 1. В чому полягає термічна обробка сталі? 2. Дайте визначення нормалізації сталей та вкажіть її призначення. 3. Охарактеризуйте процес повного відпалу та його призначення. 4. Як визначається температура гартування для доевтектоїдних і заевтектоїдних сталей. 5. Визначте температуру нормалізації сталі У8А. 6. Які структури виникають після повного відпалу, нормалізації, гартування в сталях марок сталь 45, У12А? 7. Які структури виникають після низького, середнього, високого відпускання загартованої сталі? 8. Після якого режиму термообробки можна очікувати якнайбільшу зносостійкість сталі? 9. Після якого режиму термообробки можна очікувати якнайбільшу пружність і ударну в’язкість при достатній твердості сталі? 10. Охарактеризуйте процес відпускання загартованих сталей та його призначення. |