ПОЗНАВАТЕЛЬНОЕ Оси и плоскости тела человека - Тело человека состоит из определенных топографических частей и участков, в которых расположены органы, мышцы, сосуды, нервы и т.д. Отёска стен и прирубка косяков - Когда на доме не достаёт окон и дверей, красивое высокое крыльцо ещё только в воображении, приходится подниматься с улицы в дом по трапу. Дифференциальные уравнения второго порядка (модель рынка с прогнозируемыми ценами) - В простых моделях рынка спрос и предложение обычно полагают зависящими только от текущей цены на товар. | на ремонт гидромеханического редуктора переменного наполнения СОДЕРЖАНИЕ ВВЕДЕНИЕ……………………………………………………………………….2 1. Анализ отказов оборудования локомотивов депо Печора ………….4 2. Ремонт гидромеханического редуктора переменного наполнения…8 ЗАКЛЮЧЕНИЕ…………………………………………………………………………………………………...18 Список литературы…………………………………………………………….19 ВВЕДЕНИЕ Локомотивное депо Печора (ТЧЭ-22) является основным депо, включая и оборотное депо Инта (ТД-60), имеющее свой комплекс зданий и сооружений, предназначенный для организации, обслуживания и ремонта локомотивов, подготовке их к эксплуатации в летний так и зимний период. Сюда входят: здания ремонта и пункты технического обслуживания локомотивов, здания эксплуатации, столовая, дом отдыха локомотивных бригад, пункты экипировки, склады хранения топлива и горюче – смазочных материалов, реостат, котельная и подъездные тракционные пути с разворотом в виде треугольника. Являясь основным, локомотивное депо Печора имеет свой приписной парк локомотивов: Пассажирские локомотивы 2ТЭ10Утк – 15 тепловозов, 2ТЭ10Ут – 3 тепловоза. Грузовые локомотивы 3ТЭ10У – 2 тепловоза, 3ТЭ10М – 11 тепловозов, 3ТЭ10Мк – 6 тепловозов, 2ТЭ10У – 33 тепловоза, 2ТЭ10М – 33 тепловоза, 2ТЭ10Мк – 5 тепловоза. Маневровые локомотивы ЧМЭ3 – 2 тепловоза. Всего 110 локомотивов. В депо проводят следующие виды технического обслуживания и ремонта локомотивов: ТО – 1 выполняются локомотивными бригадами, ТО – 2, ТО – 3, ТО – 4, ТО – 5, ТР – 1, ТР – 2 выполняемый ремонтным персонал ТМХ-Сервис. Локомотивные бригады депо Печора производят обслуживания участков плеч следующих направлений, они представлены на рисунке 1. В четном направлении станция Усинск, станция Инта, в нечетном направлении станция Сосногорск. Ст. Усинск 108 км 47 км 133 км Ст. Инта 249 км Ст. Сыня Ст. Печора Ст. Сосногорск Рис.1 Численность локомотивных бригад в локомотивном депо Печора в пассажирском, грузовом, хозяйственном и маневровом виде движения составляет: Машинист тепловоза – 273 человека, помощник машиниста тепловоза – 273 человека. Основной задачей локомотивного депо Печора является своевременно, устойчиво и качественно обеспечивать постоянно растущие перевозки грузов и пассажиров тяговым подвижным составом и локомотивными бригадами, гарантировать безопасность и точное соблюдение графика движения поездов. Выполнение плана по объему выполняемой работы: Наименование показателей | Единица измерения | 12 месяцев | факт 2014 год | 2015 год | результат к плану | результат к факту 2014г. | план | факт | +/- | % | +/- | % | Объем перевозок | млн. ткм брутто | 6 261,9 | 5 959 | 6 098,1 | 139,1 | 102,3 | -163,8 | 97,4 | грузовые перевозки | млн. ткм брутто | 4 789,9 | 4 732 | 4 848,0 | 116,0 | 102,5 | 58,1 | 101,2 | пассажирское движение | млн. ткм брутто | 1 225,4 | 1 034 | 1 078,6 | 44,6 | 104,3 | -146,8 | 88,0 | хозяйственное движение | млн. ткм брутто | 246,6 | | 171,5 | -21,5 | 88,9 | -75,1 | 69,5 | В пассажирском движенииплан выполняется на 104,3% (сверх плана на 44,6 млн. т-км брутто), к уровню прошлого года произошло снижение на 146,8 млн т-км брутто или 88%. Причины: 1. Снижение количества пассажирских поездов дальнего следования на 5,5% к уровню прошлого года (7862 поезда против 8319 поездов в 2014 году); 2. Снижение пассажирооборота на 15,3% по причине конкуренции других видов транспорта (авиация); 3. Снижение сформированных вагонов на 17,4% на Сосногорском регионе. В хозяйственном движении план выполнен на 88,9% (ниже плана на 21,5 млн т-км брутто), к уровню прошлого года снижение на 75,1 млн т-км брутто – 69,5%. Причины: 1. Основное место хозяйственных работ по капремонту пути находится в непосредственной близости от станции погрузки хопер-дозаторных вагонов по станции Кожва. 2. При росте хозяйственных поездов на 10,7% к уровню прошлого года(6840 против 6178 поездов) – снижена выработка часов хозработ в 2015 году на 5,4% - 68,6 тыс.часов против 72,5 тыс. часов в 2014 году. Выполнение задания по качественным показателям использования ТПС: Наименование показателей | Единица измер. | 12 месяцев | факт 2014 год | 2015 год | результат к плану | результат к факту 2014г. | план | факт | +/- | % | +/- | % | Производительность локомотива | тыс.ткм брутто в сутки | 1 321,2 | 1 361,3 | 1 450,5 | 89,2 | 106,6 | 129,3 | 109,8 | Средний вес поезда | тонн | 2 781,0 | 2 750,8 | 2 776,3 | 25,5 | 100,9 | -4,7 | 99,8 | Среднесуточный пробег | км в сутки | 592,3 | 587,6 | 617,9 | 30,3 | 105,2 | 25,6 | 104,3 | Техническая скорость | км/час | 45,4 | 44,6 | 45,6 | 1,0 | 102,2 | 0,2 | 100,4 | Участковая скорость | км/час | 35,1 | 36,1 | 37,6 | 1,5 | 104,2 | 2,5 | 107,1 | 1. Анализ отказов оборудования локомотивов депо Печора За 2015 год в эксплуатационном локомотивном депо Печора допущено 1989 случаев непланового ремонта тепловозов против 3484 случаев непланового ремонта за тот же период 2014 года. В сравнении с прошлым годом количество случаев постановки тепловозов на неплановый ремонт снижено на 1495 сл. Сравнение количества случаев постановок тепловозов, на неплановый ремонт допущенных 2015/2014 г.г. по депо приписки локомотивов на рисунке 1.  Рисунок 1. Из представленного рисунка видно, что за 2015 год допущено снижение количества НПР. Анализ продолжительности простоя тепловозов на неплановом ремонте за 2015/2014 г.г. по ремонтному локомотивному депо Печора приведен в таблице 1. Таблица 1. Депо | 2015 г. | 2014 г. | Кол-во | Общий простой, час | Средний простой, час | Кол-во | Общий простой, час | Средний простой, час | Печора | | | | | | | | | | | | | | Средний простой тепловозов на неплановом ремонте в депо за 2015 г. повысился на 52 часа. В целом по депо Печора, при сравнении причин возникновения неплановых ремонтов по ремонтным локомотивным депо, сервисным депо за 2015/2014 г.г. прослеживаются следующие закономерности: основное количество неплановых ремонтов допущено по причине неудовлетворительного качества ремонта при проведении ТО-2, ТО-3 и ТР-1, ТР-2 в депо. Количество заходов на неплановый ремонт, возникших по вине заводов за 2015 года составило 28 случая. за 2015/2014 г.г. Наименование | 2015г. | 2014г. | Всего случаев: | | | Часов простоя: | | | ПО НЕИСПРАВНОСТЯМ: | | | ДИЗЕЛЬ: | | | В том числе: | | | Коленвал и его подшипники, вертикальная передача | | | Шатунно-поршневая группа | | | Топливная аппаратура | | | Воздухонагнетатели | | | Система охлаждения, в/насосы, выхлопной коллектор | | | ВСПОМОГАТЕЛЬНОЕ ОБОРУДОВАНИЕ: | | | В том числе: | | | Водяные секции | | | Редукторы, валы, муфты | | | Вентиляторы ТЭД | | | ЭЛЕКТРООБОРУДОВАНИЕ: | | | В том числе: | | | Генераторы | | | Тяговые электродвигатели | | | Эл. цепи, аппаратура | | | Вспомогательные машины | | | ТОРМОЗНОЕ ОБОРУДОВАНИЕ: | | | В том числе: | | | Компрессор | | | Автотормозные приборы, воздуховод | | | КОЛЕСНЫЕ ПАРЫ: | | | МОП: | | | ПРОЧЕЕ ОБОРУДОВАНИЕ: | | | По виновности: локомотивные бригады | | | ремонтные бригады | | | Заводской ремонт | | | Прочие | | | Воздухонагнетатели Основными неисправностями по группе воздухонагнетатели явились: - излом вала ротора турбокомпрессора; - разрушение опорно-упорного подшипника; Система охлаждения, водяные насосы Основными неисправностями по группе система охлаждения и водяные насосы явились: - утечка воды по переходникам. - течь воды по постановке выхлопного коллектора. - течь воды по соединениям трубопроводов, дюритам, термосифонной трубке, адаптерам. Холодильное устройство Основными неисправностями по группе холодильное устройство явились: - неисправность секций холодильника, течь, засорение внутренней поверхности трубок. - неисправность гидропривода, автоматики. - неисправность главного вентилятора. Привод силовых механизмов Основными неисправностями по группе привод силовых механизмов явились: - неисправность промежуточных и распределительных редукторов; - разрушение муфт; - обрыв валов, валопроводов; Компрессор Основными неисправностями по группе компрессор явились: - неисправность нагнетательных клапанов; - неисправность предохранительных клапанов; Тяговый электродвигатель Основными неисправностями по группе тяговый электродвигатель явились: - МВЗ обмотки якоря; - МВЗ, обрыв, излом обмотки полюсов; - повреждение выводных кабелей; - понижение сопротивления изоляции якоря; - задир коллектора, излом кронштейна щеткодержателя Высоковольтная и низковольтная цепь, аппараты Основными неисправностями по группе высоковольтные и низковольтные цепи, аппараты явились: - пробой, понижение изоляции низковольтных цепей; - пробой, понижение изоляции высоковольтных цепей; - регулировка мощности; - излом проводов, нарушение изоляции, распайка; - обрыв в цепях управления; - неисправность блоков, приборов; - неисправность контакторов; Сравнение количества случаев неплановых ремонтов тепловозов на 1 млн. км. пробега по группам оборудования допущенных за 2015/2014 г.г. по ремонтному локомотивному депо представлено в таблице 1. Мероприятия для снижения количества неплановых ремонтов в эксплуатационном локомотивном депо Печора. 1.По цилиндро-поршневой группе: -на ТО-3 после одиночной смены поршней или втулок производить замер и при необходимости регулировку камер сжатия дизелей Д100; -на всех ТО-3, ТР на дизелях Д100 производить установку двухрежимных форсунок или форсунок со вставками; -при производстве ТО-3,ТР обязательно выполнять мероприятия на основе спектрального анализа дизельного масла, утверждённых дорогой; -с целью выявления поврежденных вкладышей коленчатых валов производить замеры камер сгорания на каждом ТО-3, при увеличении размера камеры более 0,5 мм производить ревизию шатунно-поршневой группы одноименного цилиндра; -в случае переукладки вкладышей коленчатых валов, приемщикам производить контрольную проверку на «натяг» не менее 2-х вкладышей на каждую переукладку; -не допускать постановку одного и того же локомотива на плановые виды ремонта вне основного депо приписки более одного раза подряд. 2.По воздухонагнетателям: -для предотвращения обрыва трубок подвода масла к подшипникам ТК-34 и его фильтру не допускать выпуск тепловозов из ремонта с отсутствующими или незакрепленными державками и скобами, -установка ТК-34 разных модификаций на один дизель и смена одного ТК-34 запрещается, производить смену обоих ТК-34. -при ремонте ТК-34, устанавливать плиту и подпятник только одного чертежа. 3.По электрическому оборудованию: -добиваться снижения количества неплановых по электрическому оборудованию за счет более высоких требований к системе защиты тепловозов от корпусных замыканий эл.цепей; -локомотивным бригадам перед выездом из депо под поезд производить обязательную сушку обмоток ТЭД током, протекающим по ним по установленной технологии; 4.По цеху ремонта. -повышать качество проведения ТО-2 в пунктах оборота, в части выявления обводнения и замерзания смазки; -повысить качество технической учебы в цехах ремонта и эксплуатации. -повысить спрос с локомотивных бригад в части выполнения ТО-1 и сохранности тепловозного оборудования; - -для увеличения ресурса бандажа заказать фрезы на станок КЖ-20 под профиль с гребнем 33 мм. 5.По холодильному оборудованию. -постоянно контролировать состояние водоподготовки, соответствие воды браковочным показателям; -повысить спрос с локомотивных бригад за соблюдением ими температурного режима при ведении поезда; 6.По цеху эксплуатации: -готовность тепловозов из всех видов ремонта дежурным по депо принимать только от приемщиков локомотивов; -повысить спрос с локомотивных бригад за проведение ими ТО-1. Технологическая карта на ремонт гидромеханического редуктора переменного наполнения № п/п | Наименование операции | Порядок выполнения операции | Технические условия, нормы допусков | Метрологическое обеспечение, оборудование и инструмент | 1. | Наружная помывка. | Произвести наружную промывку гидропривода. | Промывку производить в течение 10 - 15 минут. | Моечная машина ММД-12, кран-балка, чалочное приспособление. | 2. | Разборка гидропривода. | В процессе разборки проверить зазоры между зубьями конических зубчатых колес и прилегание зубьев.Промыть все детали редуктора и корпуса с осветительным керосином и продуть сухим сжатым воздухом. | Зазор между зубьями конических зубчатых колес должен быть в пределах: - при выбранных внутрь корпуса осевых разбегах валов не менее 0,21 мм, - при выбранных наружу корпуса осевых разбегах валов 0,41 - 0,63 мм.Прилегание зубьев должно быть не менее 60% высоты и длины зуба и располагаться в средней части поверхности зуба. | Подставка для разборки гидропривода, приспособление для проверки зазоров в зубьях зубчатых колес, медная выколотка, кран-балка, чалочное приспособление, молоток, гаечные ключи, ванна с керосином. | 3. | Ремонт корпуса гидропривода. | Осмотреть и остучать молотком корпус гидропривода на предмет появления в нем трещин.Корпус гидропривода, имеющий несквозные трещины, длиной не более 50 мм, восстановить сваркой.Осмотреть посадочные места под гнезда подшипников. Овальность, конусность, задиры и риски посадочных мест под гнезда подшипников устранить шабрением. Осмотреть шпильки в корпусе, резьбовые отверстия корпуса. | Ослабление посадки съемных подшипниковых гнезд в постелях корпуса гидропривода, а также при износе гнезд под кольца подшипников до 0,1 мм устранить путем нанесения пленки эластомера ГЭН-150(В) на наружные поверхности гнезд подшипника. При значительных износах разрешается место в корпусе под гнездо расточить и поставить на эластомер ГЭН-150(В) втулку с толщиной стенки не менее 1,5 мм или произвести газовую наплавку с последующей обработкой.Шпильки с ослаблением посадки в корпусе и шпильки, имеющие более 2-х витков сорванной резьбы заменить. | Подставка для гидропривода, молоток, сварочная установка, шабер, микрометр, индикаторный нутромер, кран-балка, чалочное приспособление. | 4. | Ремонт валов (при полной разборке). | Замерить диаметры валов под посадку подшипников. Восстановление посадки подшипников и зубчатых колес на валу при износе вала до 0,1 мм на диаметр производить путем нанесения пленки эластомера ГЭН-150(В) на посадочные места внутренних колец подшипников и диаметров зубчатых колес. Проверить посадку фланцев на конусной шейке вала. Восстановление посадки производить вибродуговой наплавкой, а при отсутствии оборудования для вибродуговой наплавки разрешается ручная наплавка. Наплавляемые поверхности обработать на станке.Осмотреть резьбу в отверстиях и на концах вала. При наличии сорванной или забитой резьбы – резьбу перерезать на следующий размер по ГОСТу. Разрешается срезать на станке дефектную резьбу, дополнительно снять слой металла еще на одну глубину резьбы и восстановить наплавкой место под резьбу.Осмотреть шпонки и шпоночные пазы валов.При износе шпоночного паза вала под шпонку более 1 мм разработанный паз заварить вибродуговым способом электродной проволокой Св – 10Г2 диаметром 1 мм под слоем флюса АН-348АМ мелкой грануляции.Проверить биение валов в центрах станка с помощью индикатора. | Коническую поверхность фланца подогнать по конической поверхности конца вала так, чтобы при проверке по краске прилегание этих поверхностей было не менее 75% общей поверхности конуса вала Восстановление слоя производить автоматической или вибродуговой наплавкой под слоем флюса, ручной электродуговой или газовой наплавкой. После проточки и наплавки, новая резьба должна быть чистой, без каких-либо дефектов в металле. Пригонку шпоночного паза к шпонке и наоборот, можно выполнить одним из следующих способов: а) обработкой пазов спариваемых деталей под ремонтный размер с постановкой шпонки ремонтного размера; б) обработкой паза только у одной детали под ремонтный размер с постановкой ступенчатой шпонки. Допускается увеличивать пазы по ширине более нормального размера: При ширине паза до 10 мм на 0,5 мм, а при ширине более 10 мм на 1 мм; в) электродуговой наплавкой пазов с последующей обработкой под нормальный размер. Новая шпонка должна быть пригнана по пазу вала и фланца с натягом 0,02 - 0,03 мм. Биение валов по посадочным и резьбовым поверхностям допускаются не более 0,05 мм. При большем биении валов произвести их правку с последующей проверкой дефектоскопом. | Шлифовальный станок, микрометр, индикаторный нутромер, сварочная установка, токарный станок, посуда с краской. | 5. | Ремонт зубчатых колес (при разборке вала) | Осмотреть зубчатые колеса. Зубчатые колеса заменить при следующих дефектах: а) изломах или трещинах в зубьях и теле зубчатого колеса; б) повреждении контактной коррозией поверхности зубьев более 25%; в) выкрашивании рабочих поверхностей зубьев; г) отколе зубьев от торца более 15% его длины; д) вмятинах на поверхности каждого зуба конического зубчатого колеса более 30 мм2 с глубиной более 0,4 мм; е) предельном износе зубьев. | Конические зубчатые колеса заменить комплектно и проверкой зацепления на «пятно контакта». | Стеллаж. | 6. | Ремонт колес гидромуфты. | Осмотреть насосное и турбинное колеса. Остучать молотком лопатки и диски колес. Проверить плотность призонных болтов в местах посадки путем остукивания легкими ударами молотка. При ослаблении посадки болтов развернуть отверстия и поставить новые болты. | На поверхности круга циркуляции дефекты не допускаются.При наличии сквозных трещин, отколов или уменьшении их толщины – колеса заменить.Толщина лопаток должна быть не менее 5 мм на турбинных и 4 мм на насосных колесах.Колеса заменить также в следующих случаях: а) насосное колесо с трещинами по перемычкам между разгрузочными окнами в диске; б) турбинное колесо при ослаблении посадки втулки в турбинном колесе. Разрешается заварка трещин в лопатках и дисках колес длиной не более 50% периметра лопатки.Перед разверткой отверстий метки спаренности, поставленные при разборке, должны совпадать.Увеличение диаметра отверстий под болты допускается не более 0,3 мм.Натяг на посадку болтов производить в пределах 0,003 - 0,034 мм. | Развертка, сварочная установка, приспособление для статической балансировки, молоток. | 7. | Ремонт чаши (колокола). | Осмотреть и остучать чашу. Осмотреть шпильки. При замене, шпильки ставить на густотертом сурике или на густотертых цинковых белилах и затягивать их до упора в не нарезанную часть. Осмотреть резьбовые отверстия чаши. | Дребезжащий звук укажет на наличие трещин. При наличии сквозных трещин и отколов чашу заменить. Чашу, имеющую мелкие трещины, заварить газовой, электродуговой или аргонодуговой сваркой. Риски и задиры на привалочной поверхности чаши зачистить.Ослабшие по посадке шпильки и шпильки, имеющие более 2-х витков сорванной резьбы, заменить.При наличии сорванных ниток в резьбовых отверстиях чаши, резьбу перерезать на следующий размер по ГОСТу. | Молоток, приспособление для статической балансировки турбинного колеса в сборе с чашей. | 8. | Ремонт подшипников. | Подшипники осмотреть и определить их пригодность. После разборки гидропривода шариковые и роликовые подшипники промыть в бензине с добавлением 4 ¸ 6% минерального масла или в осветительном керосине. Запрещается промывка подшипников качения в дизельном топливе. Промывку во второй ванне производить с применением жесткой волосяной щетки. Вымытые подшипники продуть сухим сжатым воздухом и осмотреть. Восстановление плотности посадки подшипников на шейках валов при износе вала до 0,1 мм производить путем нанесения эластомера ГЭН-150 (В) на внутреннюю обойму подшипника или на посадочную поверхность вала. Восстановление плотности посадки подшипников в отверстиях гнезд подшипников производить путем нанесения эластомера ГЭН-150 (В) на наружную поверхность кольца подшипника или на посадочную поверхность гнезда подшипника. | Подшипники качения не допускаются к эксплуатации при наличии следующих дефектов и повреждений: а) отколов металла или трещин на поверхности качения (на кольцах, шариках или роликах); б) цветов побежалости и следов заклинивания на поверхности качения деталей вследствие перегрева; в) выбоин и отпечатков удара на беговых дорожках колец от тугой посадки или ударной нагрузки; г) выкрашивания или шелушения металла, мелких раковин, большого числа точек на поверхностях качения деталей; д) раковины коррозийного и некоррозийного характера; е) глубоких рисок, забоин на поверхностях качения деталей; ж) повреждения сепараторов: надлом, трещины, срезы и ослабление заклепок, выработка гнезд до выпадания роликов; з) зазора между стальными штампованными сепараторами и буртом внутреннего кольца шарикоподшипника менее 0,3 мм; и) предельного износа и деформации деталей, т.е. когда осевой или радиальный зазор более допускаемых норм. Допускаются к дальнейшей эксплуатации подшипники качения, имеющие незначительные дефекты и повреждения: а) царапины и риски на посадочных поверхностях колец, появившиеся вследствие ослабления посадки; б) забоины, вмятины, следы коррозии на сепараторе, не препятствующие нормальному движению шариков и роликов; в) темные пятна коррозийного характера на поверхностях качения деталей, устраняемые зачисткой; г) матовую поверхность качения деталей как следствие нормального износаРиски и коррозию на поверхностях качения и в местах посадки деталей подшипников допускается устранять зачисткой вручную мелкой шлифовальной шкуркой. | Ванны с бензином или осветительным керосином, жесткая волосяная щетка, воздушный шланг, посуда с эластомером. | 9. | Ремонт фланцев. | Осмотреть и остучать молотком фланец. Заусенцы на торцовой поверхности фланца устранить зачисткой шабером. Замерить овальность отверстий под болты во фланцах. Остукиванием молотком и по смещению фланца относительно хвостовика вала проверить плотность посадки фланцев на валу. Проверить по краске прилегание фланца и вала. | При наличии трещин в любом месте, фланец заменить. При овальности отверстий под болты во фланцах более 0,3 мм восстановить их электродуговой сваркой электродами ЭЧ2 диаметром 4 - 5 мм с последующей механической обработкой на станке.В случае ослабления посадки фланца, коническую поверхность фланца наплавить.Прилегание по краске должно составлять не менее 75% поверхности. | Молоток, шабер, сварочная установка, токарный станок, штангенциркуль, посуда с краской. | 10. | Ремонт крышек. | Осмотреть и остучать молотком крышки гидропривода. | Дребезжащий звук укажет на наличие трещин. При наличии изломов крышку заменить. Трещины в крышках заварить. Отверстия, имеющие выработку более 0,3 мм, заварить с последующей обработкой на станке. | Молоток, сварочная установка, сверлильный станок. | 11. | Ремонт гнезд подшипников. | Осмотреть и остучать молотком гнездо подшипника. Ослабление посадки гнезда подшипника в корпусе гидропривода устранить путем нанесения эластомера ГЭН-150(В) на наружные поверхности гнезда. При износе гнезда подшипника и места его посадки в корпусе более 0,3 мм, разрешается постановка на эластомер ГЭН-150(В) втулки толщиной не менее 1,5 мм. | При наличии трещин или откола фланца – гнездо заменить. | Молоток. | 12. | Ремонт пружины механизма регулирования гидропривода. | Осмотреть пружину. Проверить упругость пружины.Проверить высоту пружины в свободном состоянии линейкой. Проверить угольником перпендикулярность опорных поверхностей пружины к ее оси. | При наличии каких-либо трещин на витках, пружину заменить.После 3-х кратного сжатия до соприкосновения витков пружина не должна иметь остаточной деформации. Высота пружины в свободном состоянии должна быть 205 - 3 мм.При неперпендикулярности более 2,0 мм опорные поверхности пружины прошлифовать. | Линейка, угольник. | 13. | Ремонт лабиринтного кольца. | Осмотреть и остучать лабиринтное кольцо.Проверить зазор при помощи щупа между лабиринтным кольцом и крышкой.Острые кромки и риски зачистить напильником. | При наличии трещин, откола или ослабления посадки кольца на валу кольцо заменить. Зазор должен быть не более 0,4 мм. | Молоток, щуп, напильник. | 14. | Ремонт зубчатой рейки. | Осмотреть зубчатую рейку. Риски, выработку и вмятины на цилиндрической поверхности и в зубьях рейки устранить шлифованием.При наличии сорванной резьбы на конце хвостовика рейки резьбу перерезать на следующий размер по ГОСТу. | При наличии трещин в теле или отколов в зубьях рейку заменить. Разрешается срезать на станке дефектную резьбу, дополнительно снять слой металла еще на одну глубину резьбы и восстановить наплавкой место под резьбу. | Шлифовальный станок, токарный станок. | 15. | Ремонт черпачковых трубок. | Осмотреть черпачковые трубки.При ослаблении трубки разрешается производить пайку мест соединения трубки с зубчатым колесом латунью Л62. Место пайки зачистить, трубку подогнать по месту с учетом диаметра черпачковых трубок.После осмотра и ремонта черпачковую трубку продуть сжатым воздухом. | При наличии трещин или вмятин на теле трубки, черпачковую трубку заменить. | Оборудование для пайки трубок, воздушный шланг. | 16. | Ремонт пальцев черпачков. | Осмотреть палец черпачка. Риски и выработку на поверхности пальца устранить шлифованием на станке. Замерить зазор между пальцем и посадочной поверхностью зубчатого колеса.Осмотреть резьбу в отверстии пальца. | При наличии трещин палец заменить. При увеличении зазора между пальцем и посадочной поверхностью зубчатого колеса более 0,1 мм палец заменить. При наличии сорванной или забитой резьбы в отверстии пальца - резьбу перерезать на следующий размер по ГОСТу. | Шлифовальный станок, щуп, метчик. | 17. | Ремонт стакана. | Осмотреть стакан. Риски, заусенцы, задиры и следы коррозии на поверхности устранить шабером или шкуркой шлифовальной. | При наличии трещины, откола фланца или сорванных ниток резьбы, стакан заменить. | Шабер, шкурка шлифовальная. | 18. | Разборка, ремонт и сборка лопастного насоса. | Масляный насос гидропривода разобрать. Детали насоса промыть в керосине, продуть сжатым воздухом, вытереть насухо безворсовой салфеткой, тщательно осмотреть и произвести замеры. Осмотреть пружины. Проверить упругость пружины. Проверить угольником перпендикулярность опорных поверхностей пружины к их оси. Осмотреть лопасти. Замерить износ лопастей. Осмотреть ротор.Осмотреть состояние шпилек в крышке. При замене шпильки ставить на густотертом сурике или на густотертых цинковых белилах и затягивать до упора в не нарезанную часть. Осмотреть статор.Проверить зазор «б» между торцом ротора и крышкой или фланцем и ротором. Размер «б» определяется микрометром, как разность между толщиной статора и ротора. Величину этого зазора в допустимых пределах обеспечивать подшлифовкой торцов статора или ротора. После шлифовки торцы статора притереть на плите, а затем к крышке и фланцу с применением наждачного порошка зернистостью 30Н или притирочных паст Г45, М20, М23.Проверить прилегание поверхностей статора к крышке и фланцу по краске.При наличии на внутренней рабочей поверхности статора по диаметру 100А (+0,035) рисок, сколов и выработки глубиной до 0,4 мм рабочую поверхность статора прошлифовать на станке до диаметра 100,3, 1009А (+0,035) мм. При значительном повреждении внутренней рабочей поверхности статора по диаметру 100А (+0,035) мм и выработке ее более 0,4 мм, внутренний диаметр статора расточить до диаметра 102,5 + 0,025 мм, выточить бронзовую втулку по размерам, запрессовать в статор с применением эластомера ГЭН-150(В) и расточить до размера Ø 100А (+0,035) мм.Произвести сборку насоса. При сборке установить размер а = 0.15 - 0,20 мм – наименьший зазор в перемычке между всасывающим и нагнетательным каналами.Собранный насос испытать на стенде дизельным маслом с температурой 60о - 70оС и с числом оборотов 2500 об/мин. | При наличии трещин на витках или протёртости витков, пружину заменить. После трехкратного сжатия пружины до соприкосновения витков, она не должна иметь остаточной деформации. При неперпендикулярности более 0,4 мм опорные поверхности пружины прошлифовать При наличии задиров на рабочих поверхностях лопастей или износе их более 0,12 мм лопасти заменить. При наличии трещин в любой части ротора, задиров и сколов на рабочих поверхностях, ротор заменить. Ослабшие в посадке шпильки или имеющие более 2-х витков сорванной резьбы, заменить. Трещины в корпусе статора не допускаются. Размер «б» измерять в трех точках через 120о в рабочей зоне ротора. Зазор «б» должен быть в пределах 0,075 - 0,16 мм. Прилегание поверхностей статора к крышке и фланцу должно быть не менее 75%. Производительность насоса должна быть не менее 22 л/мин. Течь масла в сопрягаемых местах статора с крышкой и фланцем не допускается. | Ванна с керосином, воздушный шланг, поверочная плита, угольник, микрометр, шлифовальный станок, токарный станок, посуда с краской, стенд для испытания лопастного насоса. | 19. | Сборка узлов гидропривода. | Собрать узел вертикального вала. Нагреть в электрической печи до температуры 180 - 200оС кольцо лабиринта и напрессовать на фланец. Нагреть в электрической печи до температуры 180 - 200оС зубчатое кольцо и напрессовать на цилиндрический хвостовик вала до упора в бурт. Установить в гнездо подшипников роликоподшипник, шарикоподшипник и роликоподшипник. Нагреть в масле до температуры 90 - 100оС гнездо подшипников в сборе с роликоподшипниками и шарикоподшипником и напрессовать на вал. Установить осевой натяг 4 - 7 мм фланца в холодном состоянии по расстоянию между торцами фланца и внутреннего кольца роликоподшипника. Поставить крышку гнезда подшипников и отрегулировать зазор 0,0 - 0,1 мм между торцами крышки и наружного кольца роликоподшипника. Нанести метки спаренности на наружной поверхности гнезда подшипников против винта – заглушки и канала подвода смазки для совмещения масляных каналов гнезда подшипников и корпуса гидропривода. Нагреть в электрической печи до температуры 200оС фланец с кольцом лабиринта и напрессовать на хвостовик вала. Проверить правильность сборки вертикального вала. Собрать узел ведомого вала и углового редуктора. Нагреть в электрической печи до температуры 200оС зубчатое кольцо и напрессовать на вал. После полного остывания зубчатого колеса установить внутреннее кольцо подшипника и зафиксировать его разрезным и пружинным кольцами. Установить шарикоподшипник в гнездо подшипника и зафиксировать его пружинным кольцом. Нагреть в масле до температуры 90 - 100оС гнездо подшипника с шарикоподшипником и напрессовать на вал. Установить гнездо с наружным кольцом роликоподшипника и отрегулировать зазор 0,0 - 0,2 мм между торцами кольца подшипника и крышки Установить ведомой вал в корпус гидропривода, при этом пазы для подвода смазки в гнездах подшипников должны располагаться сверху.Затянуть гайки крепления гнезд подшипников и застопорить их стопорными шайбами.Установить вертикальный вал в сборе с регулировочными прокладками на шпильки в корпус гидропривода. Отрегулировать боковой зазор в конических зубчатых колесах прокладками и прокладками, устанавливаемыми между корпусом гидропривода и фланцем гнезда подшипников. Проверить прилегание зубьев по краске. Установить осевой натяг 4 - 7 мм турбинного колеса в холодном состоянии по расстоянию между торцами турбинного колеса и бурта вала. Установить на конусный хвостовик вала чашу. Нагреть в электрической печи до температуры 200оС турбинное кольцо и напрессовать на вал, предварительно обезжирить сопрягаемые поверхности. Собрать узел ведущего вала с механизмом регулирования черпачковых трубок. Установить на вал насосное колесо и закрепить болтами. Нагреть в масле до температуры 90 - 100оС внутреннее кольцо роликоподшипника и напрессовать оправкой на вал. Зафиксировать кольцо роликоподшипника разрезным и стопорным кольцами. Раскернить в месте стыков разрезное кольцо. В процессе сборки произвести проверки и регулировки: - проверить щупом зазор между разрезным кольцом и кольцом роликоподшипника; - проверить щупом зазор между торцом наружного кольца роликоподшипника и кольцом; - установить длину хода рейки «L» 41 - 43 мм. Установить фланец на конусный хвостовик вала и затянуть гайкой, предварительно обезжирить конусные поверхности хвостовика вала и фланца.Проверить вращение собранного ведущего вала с механизмом регулирования черпачковых трубок. | Перед посадкой обезжирить сопрягаемые поверхности. Перед посадкой сопрягаемые поверхности обезжирить. Напрессовку зубчатого колеса производить на гидропрессе. Натяг при напрессовке зубчатого колеса – 0,045 - 0,165 мм. Наружные обоймы устанавливать в гнездо подшипников с зазором 0,0 - 0,075 мм. Натяг при напрессовке внутренних обойм подшипников на вал должен быть – 0,01 - 0,05 мм. Требуемый натяг обеспечить шлифованием торца фланца или установкой дистанционного кольца. Регулировку зазора производить паронитовыми прокладками. Вал должен вращаться свободно, без заеданий. Перед посадкой зубчатого колеса обезжирить сопрягаемые поверхности. Напрессовку зубчатого колеса производить на гидропрессе. Натяг при напрессовке зубчатого колеса – 0,015 - 0,135 мм. Натяг при напрессовке внутреннего кольца подшипника – 0,01 - 0,05 мм. Наружную обойму шарикоподшипника в гнездо подшипника устанавливать с зазором 0,0 - 0,075 мм. Натяг при напрессовке внутреннего кольца шарикоподшипника – 0,01 - 0,05 мм. Регулировку производить паронитовыми прокладками. Установку производить так, чтобы канал подвода смазки совпал с отверстием К 1/4". Боковой зазор между зубьями конических зубчатых колес должен быть: а) при выбранных внутрь корпуса осевых разбегах вертикального и ведомого валов не менее 0,21 мм; б) при выбранных наружу осевых разбегах валов 0,41- 0,63 мм. «Пятно контакта» должно быть не менее 60% длины и высоты зуба и располагаться в средней части поверхности зуба. Натяг при напрессовке внутреннего кольца роликоподшипников должен быть – 0,01 - 0,04 мм. Зазор должен быть 0,0 - 0,1 мм. Регулировку зазора производить шлифованием разрезного кольца. Зазор должен быть 0,3 мм, регулировку обеспечить шлифованием кольца. Регулировку длины хода рейки производить гайками, при этом зазор между полностью разведенными трубками и внутренней поверхностью чаши должно быть 3+1 мм, а диаметр «Д» при полностью сведенных трубках должен быть Д = 206 ±3 мм. Регулировку зазора «Ч» и диаметра «Д» обеспечить за счет подгонки черпачковых трубок по диаметру. Затяжку гайки производить тарированным ключом. Момент затяжки 45+5 кг.см. Собранный ведущий вал с механизмом регулирования черпачковых трубок должен вращаться плавно, без рывков и заклиниваний. | Электрическая печь, масляная ванна, кран-балка, чалочное приспособление, зубило, гаечные ключи. Электрическая печь, масляная ванна, кран-балка, чалочное приспособление, гаечные ключи, приспособление для проверки бокового зазора между зубьями конических шестерен, посуда с краской. Масляная ванна, щуп, ключ с регулируемым крутящим моментом, гаечные ключи, кран-балка, чалочное приспособление. | 20. | Сборка гидропривода. | Установить прокладки на шпильки корпуса гидропривода и ведущий вал с механизмом регулирования черпачковых трубок в корпус гидропривода и отрегулировать зазор между насосным и турбинным колесами.Проверить сборку гидропривода. | Зазор между насосным и турбинным колесами должен быть 2 +1,0-0,5 мм, регулируется толщиной прокладок.В собранном гидроприводе валы должны вращаться легко, без стуков, рывков и заклиниваний.Механической связи между ведущим и ведомым валами гидромуфты не должно быть. | Кран-балка, чалочное приспособление, штангенциркуль с глубинометром, гаечные и торцовые ключи. | 21. | Испытание гидропривода на тепловозе при реостатных испытаниях. | Проверить и при необходимости отрегулировать давление масла, поступающего в гидромуфту. Проверить и при необходимости отрегулировать давление масла, поступающего на смазку конических зубчатых колес и подшипников гидропривода. | Давление масла, поступающего в гидромуфту, должно быть в пределах 0,7 - 1,2 кгс/см2 при 850 об/мин. Давление масла, поступающего на смазку конических зубчатых колес и подшипников гидропривода, должно быть в пределах 0,4 - 0,7 кгс/см2 при 850 об/мин.При 400 об/мин вала дизеля давление масла, поступающего в гидромуфту и на смазку конических зубчатых колес и подшипников при открытых верхних жалюзи, должно быть не менее 0,1 кгс/см2.При обкатке гидропривода не должно быть ненормального стука и прерывистого шума. Течь масла в местах разъема не допускается. Температура картера возле подшипниковых узлов должна быть не более 85оС. | Установка для проведения реостатных испытаний, гаечные ключи. | 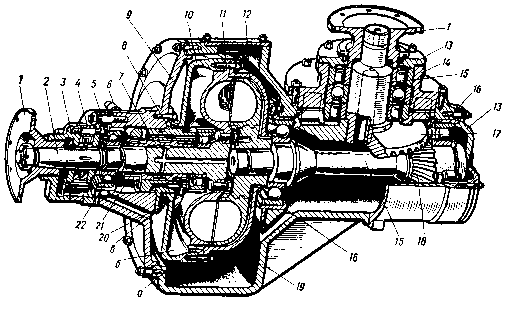 Рис. 1. Гидромуфта переменного наполнения. 1 – фланец; 2 - вал приводной; 3 – крышка лопастного насоса; 4 – насос; 5 – фланец насоса; 6 – зубчатая рейка; 7 – втулка-шестерня; 8 – ступица; 9 – фланец корпуса; 10 – чаши колокола; 11 – насосное колесо; 12 – турбинное колесо; 13 – крышка; 14 – подшипниковый стакан; 15 – валы; 16 – гнездо подшипника; 17,18 – конические шестерни; 19 – корпус; 20 – черпачковая трубка; 21 – шестерня; 22 – шариковый подшипник привода. ЗАКЛЮЧЕНИЕ Прохождение практики считаю весьма полезным мероприятием для выработки профессиональных навыков и для моей будущей работы по специальности. Я считаю, что производственная практика является важной частью подготовки высококвалифицированных специалистов, поскольку в процессе ее ставится задача закрепления и расширения знаний, полученных при обучении студентов. Требуется изучение работы предприятия, учреждения, в которых будущие специалисты проходят практику. В течение же производственной практики работа студентов должна строиться таким образом, чтобы поставленная узкая задача завершалась конкретным результатом. Только в этом случае достигается основная цель практики, как формы приобщения студента к самостоятельной работе. За время прохождения учебной практики в эксплуатационном локомотивном депо ПЕЧОРА структурном подразделении Северной Дирекции тяги - филиала ОАО «РЖД» были получены как теоретические, так и практические знания. Эксплуатация локомотивов - это совокупность мероприятий, связанных с использованием и обслуживанием локомотивов на линии, а также с системой ремонта и подготовки их к поездке. Эксплуатация локомотивов как первичное звено в организации движения поездов осуществляется на участках обращения локомотивов, по которым поезда проводятся эстафетным способом. В системе эксплуатации локомотивов организация работы локомотивных бригад определяет технологию технического обслуживания и ремонта локомотивов в депо, в известной мере - конструктивные решения при проектировании новых локомотивов и играет важнейшую роль в обеспечении установленного режима труда и отдыха машинистов и их помощников. Она оказывает существенное влияние на технологические процессы работы депо и ремонт локомотивов. Список литературы. 1. Документация производственно-технического отдела экплатационного локомотивного депо Печора ТЧЭ-22. 2. К.М. Рудая «Устройство и ремонт тепловозов». Транспорт , 1981 г. 3. А.А. Пойда , Н.М. Хуторянский , В.Е. Кононов «Тепловозы. Механическое оборудование , устройство и ремонт» . Транспорт , 1988 г. |