Форма отчёта по лабораторной работе №2 ЛАБОРАТОРНАЯ РАБОТА №2 СВАРКА И РЕЗКА МЕТАЛЛОВ (4 часа) Цель работы: Изучение процесса сварки деталей, технологии сварочного производства и оценки качества сварного шва. Для работы необходимы: линейка, карандаш, сварочный трансформатор, образец сварного соединения, мел, приборы для приготовления мелового раствора, керосин. 1 ФИЗИЧЕСКАЯ СУЩНОСТЬ СВАРКИ Сущность технологического процесса сварки металлов состоит в получении неразъемного соединения путем создания условий для межатомного взаимодействия и возникновения прочных металлических связей между атомами поверхностных слоев свариваемых деталей. Для осуществления межатомного взаимодействия необходимо, чтобы атомы свариваемых поверхностей находились в пределах действия межатомных сил, т. е. на расстояниях, соизмеримых с параметрами кристаллических решеток металлов. Необходимое сближение частиц соединяемых поверхностей достигается воздействием на металлы в зоне сварки тепловой или механической энергии. В зависимости от этого сварочные процессы условно делят на способы сварки плавлением и способы сварки давлением. При сварке металлов плавлением кромки соединяемых заготовок и присадочный материал при помощи внешнего источника тепла нагреваются до расплавления и вследствие повышенной подвижности атомов металлов в жидком состоянии образуют общую сварочную ванну. После охлаждения и кристаллизации расплава в зоне сварки остается сварной шов, прочно соединяющий свариваемые поверхности деталей При сварке давлением соединение двух поверхностей свариваемых заготовок происходит при совместной пластической деформации в результате приложения внешних усилий. Сварку высокопластичных металлов осуществляют без нагрева зоны сварки (холодная сварка); в остальных случаях сварку давлением ведут с подогревом металла до пластического состояния или до оплавления. В процессе деформации в месте контакта поверхностные неровности сминаются, окисные пленки разрушаются и выдавливаются из зоны сварки; осуществляется плотный контакт между очищенными поверхностями заготовок. Пограничные зерна измельчаются и частично взаимно перемешиваются, между частицами материала возникает межатомное взаимодействие. Основными методами сварки давлением являются контактная сварка, диффузионная, ультразвуковая, газопрессовая, сварка трением, холодная сварка. На качество сварки существенно влияет степень чистоты свариваемых поверхностей и металла сварочной ванны. Присутствие окисных пленок и других загрязнений затрудняет взаимопроникновение свариваемых металлов и приводит к понижению прочности сварного соединения. Для защиты металла в процессе сварки от окисления и газопоглощения сварку электрической дугой производят под слоем флюса, в среде инертных газов, в водороде и вакууме. При ручной дуговой сварке используют также электроды, покрытые защитными шлакообразующими обмазками. ЭЛЕКТРОДУГОВАЯ СВАРКА В качестве источника тепла при дуговой электросварке используется электрическая дуга, представляющая собой электрический разряд между двумя электродами в газообразной среде, сопровождающийся большим выделением тепла и лучеиспусканием. Для возникновения дугового разряда необходимо ионизировать газовый промежуток между электродами потому, что при обычных условиях газы, в том числе и воздух, не проводят электричества. Для получения электрической дуги один полюс сварочной машины соединяется со свариваемым изделием, а другой с электродом; при соприкосновении электрода с изделием в месте контакта выделяется большое количество тепла, расплавляющего как кромки изделия, так и металлический электрод. Разогретый электрод отводят на 2—3 мм от изделия, расплавленный конец электрода будет излучать электроны, которые, пролетая с большой скоростью сквозь воздушный промежуток, расщепляют атомы окружающего воздуха на положительно и отрицательно заряженные частицы, так называемые ионы; ионизированный воздух обеспечивает устойчивое горение электрической дуги. Отрицательные ионы при ударе анода выделяют на нем большее количество тепла, чем положительные ионы, ударяющиеся о катод. Поэтому и температура анода выше чем на катоде. Электрическая дуга является мощным источником тепла температура дуги — 4000—5000°. Источниками питания для дуговой сварки служат сварочные трансформаторы переменного тока и сварочные генераторы постоянного, тока или выпрямители. При сварке на постоянном токе дуга горит более устойчиво, улучшаются условия сварки в различных пространственных положениях и, кроме того, имеется возможность вести сварку на прямой или на обратной полярности. Переменный ток менее предпочтителен в технологическом отношении, но сварочные трансформаторы (рисунок 9) проще в эксплуатации и имеют более высокий коэффициент полезного действия, чем генераторы постоянного тока.  1-трансформатор, 2-регулятор Рисунок 9 – Схема сварочного трансформатора с отдельным регулятором Электроды для дуговой сварки разделяют на плавящиеся и неплавящиеся. При сварке плавящимися электродами сварной шов образуется в результате оплавления основного металла деталей и металлического электрода в виде стержней или проволоки, химический состав которой выбирают близким составу свариваемого металла. В качестве неплавящихся электродов применяют угольные, графитовые и вольфрамовые стержни. В этом случае для образования сварочной ванны и шва в дугу необходимо подавать присадочную проволоку. АРГОНО-ДУГОВАЯ СВАРКА При аргоно-дуговой сварке электрод, дугу и сварочную ванну изолируют от воздействия атмосферного воздуха непрерывным потоком газообразного аргона. Аргон из баллона через редуктор подают в сварочную горелку. Горелка имеет вмонтированный электрод и кольцевой канал. Поступающий по кольцевому каналу аргон окружает электрод и дугу концентричной струей, создавая в зоне сварки защитную газовую оболочку (рисунок 10). При аргоно-дуговой сварке отпадает необходимость в применении защитных флюсов или электродов с обмазкой. Сварочный шов получается чистый, свободный от шлака. Высокая плотность тока обеспечивает высокую концентрацию тепла, что способствует уменьшению коробления изделия. Сварка может производиться в любых пространственных положениях. В процессе сварки можно наблюдать за открытой дугой. При аргоно-дуговой сварке используют неплавящиеся вольфрамовые электроды диаметром 1,5—6 мм и плавящуюся электродную проволоку диаметром 0,5— 2,0 мм. Расход аргона 2—18 л/мин. Аргоно-дуговую сварку плавящимся электродом ведут главным образом постоянным током при обратной полярности. Катодное распыление металла детали и бомбардировка поверхности сварочной ванны положительными ионами разрушают окисные и нитридные пленки и другие загрязнения свариваемых поверхностей. Это улучшает качество сварки активных металлов и обеспечивает более высокую производительность.  1 — мундштук; 2 — канал для подачи аргона; 3— электрод; 4— дуга; 5 — изделие; 6— присадочная проволока Рисунок 10 – Дуговая сварка в защитной среде Катодное распыление – разрушение поверхности твёрдого тела при бомбардировке его ионами. Аргоно-дуговая сварка плавящимся электродом может быть использована для соединения практически всех сталей и цветных металлов. 4 ДУГОВАЯ РЕЗКА МЕТАЛЛОВ Дуговую резку металлов можно производить угольным и металлическим электродами путем выплавления расплавленного металла дугой в месте реза. Резку угольным электродом производят постоянным током. При резке угольным электродом получаются неровные края, натеки, большая ширина реза и т. д., поэтому она применяется (при отсутствии кислородной резки) при разборке старых металлоконструкций, удалении литников и прибылей в отливках. При помощи металлического электрода можно подвергать резке металл толщиной до 20 мм. Но и этот способ резки нельзя считать экономически выгодным, так как он дает малую производительность и требует большого расхода электродов. Поверхность реза в этом случае получается неудовлетворительного качества, как и при резке угольным электродом. ГАЗОВАЯ СВАРКА Газовой сваркой называется процесс соединения двух, деталей, при которой нагрев и расплавление кромок этих деталей происходит под действием тепла кислородно-газового пламени. Газовая сварка применяется при сварке изделий из стали небольших толщин, цветных металлов и сплавов, при сварке чугуна, при выполнении сложных ремонтных работ. При газовой сварке в качестве горючих применяются в смеси с кислородом ацетилен, водород, природные газы (метан), коксовые и другие газы, а также пары керосина и бензина. Кислород — газ, не имеющий запаха, вкуса и цвета, не относится к числу горючих газов, но активно поддерживает горение. Процесс горения газов заключается в соединении их с кислородом; горение в кислороде характеризуется образованием яркого пламени, обладающего высокой температурой. Кислород вступает в химическое соединение с металлами и их сплавами. При температуре —183° кислород превращается в прозрачную, голубую жидкость. При испарении 1 л жидкого кислорода образуется 790 л газообразного. Это обстоятельство используют для дешевой транспортировки кислорода. Газообразный кислород перевозят в стальных баллонах. Баллон емкостью 40 л содержит 6 м3 газообразного кислорода под давлением 150 ат. Кислородные баллоны окрашивают в синий цвет. Ацетилен. Для газовой сварки широко применяется ацетилен. Он выделяет наибольшее количество тепла и развивает наибольшую температуру при сгорании в кислороде (3100—32000С). Ацетилен (С2Н2) — газ, представляющий собой химическое соединение двух веществ — углерода и водорода; имеет резкий неприятный запах. Ацетилен получается из карбида кальция при действии воды по реакции: СаС2 + 2Н2О = Са (ОН) 2 + С2Н2 + 30,4 ккал/моль. | При этом выделяется большое количество тепла. Карбид кальция получается из извести и угля путем сплавления их в электропечах. При разложении 1 кг карбида кальция получается 250—300 л ацетилена. Ацетилен образуется в специальных аппаратах — ацетиленовых генераторах. Пары бензина и керосина, применяемые в качестве горючих газов при газовой сварке, отличаются вредностью и способностью взрываться в смеси с воздухом. Поэтому при работе с бензином и керосином нужно соблюдать меры предосторожности. Температура бензино-кислородного пламени 2400—25000С, керосино-кислородного — 2200—2300°С. Заменители ацетилена при газовой сварке и резке. Для газовой сварки применяются дешевые горючие газы: коксовый, природный, метан и др. Температура сгорания коксового газа в кислороде 1800-2000°. Стоимость коксового газа значительно ниже стоимости ацетилена. Применение коксового газа ограничивается, как правило, теми заводами, на которых он производится. В связи с большими разработками месторождений природного газа и сооружений магистральных трубопроводов для передачи этого газа в промышленные центры страны, значительное применение для газовой резки находит природный газ. Природный газ состоит в основном из метана (95%) с большой примесью азота (до 3%) и различных углеводород. Метан представляет собой соединение углерода с водородом. Температура пламени при сгорании метана в кислороде 1900— 2000°. «Нефтяные газы»—отходы, получаемые при перегонке нефти. Нефтяной газ при сгорании в кислороде дает пламя с температурой 2300—2400°. Наиболее полноценным заменителем ацетилена при газовой резко является водород, при помощи которого можно производить резку металла больших толщин (до 1000 мм). Водород получается из воды путем электролиза. В качестве горючего при резке могут быть также применены газы; псевдобутилен — отход при производстве синтетического каучука; генераторный газ, получающийся в больших количествах на металлургических заводах, и др. 6 КОНТАКТНАЯ СВАРКА Особенность - контактной сварки в том, что сварка происходит в результате механического давления на металл, нагретый до пластического состояния. Контактная сварка обеспечивает высокое качество сварных соединений, так как окислы и шлаки при сварке выдавливаются наружу. Вторая особенность контактной сварки — быстрота процесса, высокая производительность, требующая применения машин с большой электрической мощностью. Контактная сварка широко применяется в промышленности, в самолетостроении, инструментальном деле и других важнейших отраслях. При контактной сварке нагрев свариваемых изделий производится теплом, выделяемым при прохождении электрического тока по свариваемым изделиям и в контакте между ними. Применяемые при контактной сварке большие силы тока (десятки и сотни тысяч ампер) обеспечивают быстрый напрев изделия в месте сварки, а приложенное давление дает прочное соединение. Длительность сварки — доли секунды. Контактная сварка может производиться переменным током частотой 50 Гц, аккумулированной энергией, накапливаемой в конденсаторах или других устройствах, а также импульсами постоянного тока. Разновидностями контактной сварки являются стыковая, точечная и роликовая сварки. Стыковой сваркой соединяют детали по всей площади соприкосновения (рисунок 11). Различают три метода стыковой сварки: сопротивлением, непрерывным оплавлением и прерывистым оплавлением.  1-первичная цепь трансформатора; 2-вторичная цепь трансформатора Рисунок 11 – Схема стыковой сварки При сварке сопротивлением электрический ток пропускают через предварительно сжатые заготовки. После разогрева их в месте контакта до пластического состояния заготовки дополнительно сжимаются и производится осадка их на необходимую величину. Затем электрический ток выключается. Свариваемые торцы заготовок перед сваркой тщательно очищаются от окисных пленок и обеспечивается плотное их прилегание. Попадание окислов между контактирующими поверхностями снижает качество сварки. Сварка непрерывным оплавлением производится следующим образом. Торцы свариваемых заготовок сближают до соприкосновения при включенном сварочном токе. Неплотный контакт заготовок обусловливавает высокое сопротивление электрическому току. На торцах заготовок возникают искровые разряды и происходит быстрый нагрев и оплавление торцовых поверхностей. После оплавления всего сечения заготовки быстро осаживаются. Расплавленный металл вытесняется из зазора и образуется сварное соединение по всей площади касания заготовок. По сравнению со сваркой сопротивлением сварка непрерывным оплавлением более производительна и позволяет свариваемые торцы заготовок обрабатывать менее тщательно. Недостатком является значительное разбрызгивание и угар металла. При сварке прерывистым оплавлением нагрев до оплавления всего сечения выполняют путем периодического замыкания и размыкания сварочного контура с последующей осадкой заготовок. Размыкание достигается либо периодическим выключением тока, либо механическим разведением свариваемых заготовок на небольшое расстояние. При такой сварке требуется меньшая мощность машин, но увеличивается расход металла вследствие его угара. Стыковую сварку применяют для соединения стали, медных и алюминиевых сплавов, некоторых сплавов титана. Сваривают и разнородные металлы: сталь с медью, латунь с медью и др. Соединение листовых заготовок производят точечной и шовной сваркой. В зависимости от расположения электродов точечная сварка может бить двусторонней или односторонней. При двусторонней сварке (рисунок 12 а) заготовки накладывают друг на друга и зажимают стержневыми металлическими электродами, по которым пропускают сварочный ток. Режим сварки подбирают таким образом, чтобы металл в зоне контакта — в месте наибольшего сопротивления электрической цепи — нагревался до плавления. После осадки и охлаждения в месте контакта образуется литая сварная точка. Односторонняя сварка (рисунок 12 6) осуществляется двумя электродами, расположенными со стороны одной из свариваемых заготовок. Электрический ток, разогревающий металл в точках сварки, замыкается между электродами через вторую (нижнюю) заготовку и нижнюю медную пластину, которая подкладывается для увеличения тока, протекающего через нижнюю заготовку. Операции точечной сварки производятся в определенной последовательности: сдавливание свариваемых заготовок, включение электрического тока, выдержка в течение определенного времени, выключение тока, увеличение и последующее снятие усилия сжатия. При нарушении последовательности операций качество сварки резко снижается. Диаметр сварной точки зависит от диаметра электрода, величины сварочного тока и продолжительности разогрева при сварке. Практически размер точки по ширине составляет 1,0—1,2 диаметра электрода, который обычно выбирается на 3—4 мм больше суммарной толщины свариваемых заготовок. Свариваемые поверхности заготовок должны быть очищены от окислов.  1,2 – заготовки; 3- подкладка Рисунок 12 – Схема двусторонней (а) и односторонней (б) точечной сварки Режим точечной сварки определяется удельным давлением в зоне сварки, плотностью тока и временем одного цикла сварки. Точечной двусторонней сваркой сваривают внахлестку две, три и даже четыре заготовки. Сварные точки располагают друг от друга на расстоянии, примерно равном 2,5 диаметра электрода. Точечную сварку используют для соединения заготовок одинаковой и различной толщины в пределах от 0,001 до 5 мм (рисунок 13). Роликовая (шовная) сварка обеспечивает получение прочноплотного шва в форме сплошного ряда последовательно расположенных сварных точек. Такой шов получается при помощи вращающихся роликов, к которым подведен сварочный ток и приложено усилие сжатия. Как и точечная, роликовая сварка может быть односторонней и двусторонней (рисунок 14).  а –двусторонняя, б – односторонней Рисунок 14 – Схема шовной сварки Роликовую сварку широко используют в тех случаях, когда при изготовлении различных конструкций из листового материала толщиной 0,3—3 мм требуется обеспечить высокую герметичность сварного соединения. На рисунок 15 показаны наиболее характерные типы сварных соединений, выполняемых роликовой сваркой. 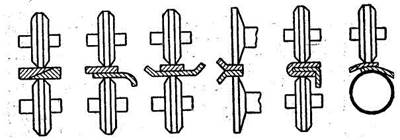 Рисунок 15 – Примеры соединений, выполняемых шовной сваркой ПЛАЗМЕННАЯ СВАРКА В настоящее время целесообразно из дуговой сварки выделить плазменную сварку, которая, наряду с общими признаками, имеет отличия от дуговой сварки. В плазменной сварке основным источником энергии для нагрева материала служит плазма — значительно ионизированный и нагретый газ, в котором концентрации положительных и отрицательных зарядов равны. Плазма представляет собой смесь электрически нейтральных молекул газа и электрически заряженных частиц, электронов и положительных ионов, иногда еще и тяжелых отрицательных ионов. Наличие электрически заряженных частиц делает плазму чувствительной к воздействию электрических полей. Плазма электропроводна, и при действии электрических полей в ней возникают электрические токи. При высоких степенях ионизации электропроводность плазмы может быть очень высокой. Токи в плазме могут отклоняться под действием магнитных полей. Ускорения, сообщаемые заряженным частицам действием электрических и магнитных полей путем соударений, передаются нейтральным частицам газа, и весь объем плазмы может получать направленное движение, образуя струю (или поток) или факел горячего газа. Электрические поля, воздействуя на плазму, передают энергию заряженным частицам, а через них и всей плазме и могут повышать ее температуру примерно до 20 000—30 000° С. Технологически струя плазмы близка к газосварочному пламени, отличаясь более высокой температурой. Плазменной струей или факелом можно осуществлять различные виды обработки: сварку, резку, напыление, пайку, термообработку и т. д., причем можно обрабатывать как металл, так и неметаллические материалы — стекла, керамику и пр. Плазменная сварка сжатой дугой состоит в том, что сечение плазменной струи уменьшается по сравнению со свободной струей под действием магнитных полей, обдуванием потоками газа или распыленной жидкости, пропусканием струи через сопло. Данный способ является наиболее важным и распространенным (рисунок 16). В дуге между неплавящимся электродом 1 и нагреваемым изделием 4 располагается сопло 2, представляющее собой металлическую или графитную пластинку с калиброванным отверстием-каналом, через которое проходит плазменная струя 3, образуемая дуговым разрядом. Дуга может быть прямого действия (замкнут контакт 5, разомкнут 6), косвенного действия (замкнут 6, разомкнут 5) и смешанного действия (замкнуты контакты 5 и 6). При замыкании контакта 6 ток идет через сопротивление 7.  Рисунок 16 – Сварка и резка сжатой дугой Обычно для плазменной сварки используют горелку, часто называемую плазматроном (рисунок 17). В горелку подается одновременно два независимых потока 1 — плазмообразующий и 2 — защитный. В обоих потоках может быть один и тот же газ, например аргон; могут быть и разные газы, например 1 — аргон и 2 — азот + водород. Поток 2 подает газ для образования плазмы; расход и скорость газа небольшие. С увеличением скорости газа усиливается расплавляющее действие плазменной струи и глубина расплавления основного металла. При значительном увеличении скорости газа расплавление металла может стать сквозным, металл выдувается из ванны и процесс сварки может перейти в резку металла. Внешний поток 2 защищает сварочную ванну и зону сварки от воздействия атмосферного воздуха; кроме того, он обжимает плазменную струю за пределами сопла и может придавать ей цилиндрическую или коническую форму. Свободная струя, вышедшая из сопла, постепенно расширяется по мере удаления от среза сопла. Поток 2 в случае дуги косвенного действия может сводить конец факела на острие, что иногда целесообразно технологически, поэтому защитный поток 2 называют также формирующим или фокусирующим.  Рисунок 17 – Плазменная сварочная горелка Плазменная сварка имеет промышленное применение обычно как автоматическая или полуавтоматическая, причем автоматы и полуавтоматы для дуговой сварки легко могут быть приспособлены для плазменной с соответствующей заменой горелки. К преимуществам плазменной сварки можно отнести повышение производительности, уменьшение расхода присадочного металла, расширение возможности стыковой сварки металла без скоса кромок (толщиной до 15 мм) или с уменьшением разделки, малую чувствительность к колебаниям длины дуги, устранение включений вольфрама в наплавленном металле. При значительных толщинах металла возможна многослойная сварка. Сварку можно вести и на вертикальной поверхности. Струя плазмы отличается большой жесткостью и устойчивостью. Плазменная сварка с дугой косвенного действия пригодна не только для металлов, но и для неэлектропроводных материалов (стекла, керамика и т.п.). Для сварки особо малых толщин металла, от десятков микрон до 1 мм, мелких и мельчайших деталей успешно используется разновидность плазменной сварки, известная под названием микроплазменная сварка, или сварка игольчатой дугой, потому, что здесь струя плазмы диаметром 1,5—2 мм, заканчивается острием. Токи применяются 0,1 —10 а, расход газа 10—30 л/ч, диаметр сопла 0,8 мм. Формирующий газ придает плазменной струе форму иглы. ПЛАЗМЕННАЯ РЕЗКА Процессы плазменной сварки и резки отличаются лишь величиной отдельных параметров. Если увеличить ток в плазменной сварочной горелке и поток газа, то плазменная струя будет проплавлять насквозь металл небольшой толщины и процесс сварки перейдет в процесс резки, что иногда используется на практике. Горелка для плазменной резки, или плазменный резак, в настоящее время чаще называется плазмотроном. Плазмотрон для резки отличается от плазменной сварочной горелки размерами, большей электрической мощностью, большим расходом газа, обязательным водяным ох расходом газа, обязательным водяным охлаждением. Наиболее существенные части плазмотрона — электрод и сопло для выхода газа, образующего плазменную струю (рисунок 18). Раньше материалом электрода служил исключительно вольфрам. В отдельных конструкциях плазмотронов были попытки применять электроды угольные (графитные) и водоохлаждаемые медные, но значительного применения они не получили. С 1966 г. началось применение для электродов металла циркония. На рисунке 19 представлена схема стабилизации дуги.  а-концентрическая; б-вихревая 1-защитный газ; 2-рабочий газ Рисунок 19 – Схема стабилизации дуги ВОЗДУШНО-ПЛАЗМЕННАЯ РЕЗКА Основное затруднение при осуществлении плазменной сварки на обычном атмосферном воздухе состояло в создании электрода, стойкого при нагреве в воздухе. Система двойного газа оказывалась слишком сложной и требовала дефицитных газов, хотя и в меньшем количестве. Появление циркониевого электрода в корне изменило вопрос о газах для плазменной резки. Цирконий имеет не очень высокую температуру плавления, около 1900° С и большое химическое сродство к кислороду и азоту, — он активно соединяется с ними, образуя весьма тугоплавкий окисел и нитриды. Нагретый окисел на поверхности электрода проводит ток дуги и в то же время защищает металл от дальнейшего окисления. Появилась реальная возможность использования атмосферного воздуха для плазменной резки. При плазменной резке углеродистых сталей наряду с очень высоким качеством реза обеспечивается и высокая производительность резки. По-видимому, здесь играет роль кислород воздуха, сжигающий металл и ускоряющий резку. Существенное преимущество плазменной резки — практически мгновенный старт, в то время как газокислородная резка требует 5—20 сек, на нагрев металла при начале каждого реза. На рисунках 20–24 представлены примеры плазменной резки и сравнение её с газовой резкой металлов. Рисунок 22 –Примеры плазменной резки  Газовая 13:42 мин Плазменная 4:32 мин Рисуногк 23 – Сравнение плазменной и газовой резки  Рисунок 24 – Скорость резки и область применения в зависимости от толщины металла ПОРЯДОК ПРОВЕДЕНИЯ РАБОТЫ 10.1 Изучить методические материалы по сварке и резке металлов. 10.2 Изучить сварные соединения, полученные разными методами сварки. 10.3 Получить деталь со сварным швом. 10.4 Для проверки качества сварного шва приготовить известковый раствор. Для этого мел измельчить и растворить в воде. Далее приготовленный раствор равномерно нанести на поверхность шва. Дать высохнуть. 10.5 С обратной стороны намочить шов керосином. 10.6 С лицевой стороны проверить шов на наличие пятен на известковом покрытии. 10.7 Оформить отчет. Форма отчёта по лабораторной работе №2 Отчёт по лабораторной работе №2 – Изображение изделия со сварным швом; – Методика проведения испытаний; – Результаты испытаний и выводы по работе. КОНТРОЛЬНЫЕ ВОПРОСЫ 1. Объяснить физическую сущность сварки плавлением 2. Объяснить физическую сущность сварки давлением 3. Перечислить основные методы сварки давлением 4. Факторы, влияющие на качество сварки 5. Приёмы защиты металла в процессе сварки 6. Сущность метода электродуговой сварки 7. Источники питания и их особенности при дуговой сварке 8. Виды электродов при дуговой сварке 9. Сущность метода аргоно-дуговой сварки 10. Сущность метода газовой сварки 11. Газы применяемые при газовой сварке 12. Особенности контактной сварки 13. Стыковая сварка 14. Точечная и роликовая сварки 15. Сущность метода плазменной сварки 16. Плазменная сварка сжатой дугой 17. Плазменная резка и плазмотроны 18. Воздушно-плазменная резка |